4 Actionable Steps to Make Your Dealership’s Safety Culture Thrive
Safety culture, safety culture, safety culture. It’s a well-covered topic. We all know it’s important to our dealerships. But how do we take concrete steps to make sure our dealership safety culture thrives?
I’ll be honest here. It’s not like you can wave a wand, think good thoughts, and your magical safety culture will flourish in your service bays. Building a strong culture of safety in your dealership takes dedication. While it may not be magical, it’s not impossible. And we’ve got some actionable steps you can take to get your dealership’s to take root.
1. Build Your Team
Build a team comprised of employees in varied roles to help bring your safety culture to life. As a best practice, build that team out of those who volunteer to help. If you’ve got a team of “volun-tolds” they might not necessarily be motivated to stay committed to the cause. Consider, too, that if an employee taken off a particular job to be on the safety culture team, be sure you’re paying them for that extra time.
When building your team, find out if any workers have specialized experience or experience that could benefit the team as you set out to hone your safety program success. For example, if you have a technician who used to work as a forklift operator, they could be a great resource explaining generally what your forklift training program should focus on. Or, let’s say someone was previously a firefighter. They might have some really good general knowledge to share on workplace CPR and first aid.
2. Establish Priorities
Once you’ve assembled your team, it’s all about establishing priorities, identifying hazards, and discussing risk mitigation strategies.
Start by assessing the probability and severity of those hazards. Once you have a sense of how likely something is to happen, you can start to prioritize as a team.
For example, let’s say we’ve identified a car falling off a lift as a risk. The probability of it happening may be low, but the severity could be catastrophic, so this may very well become the number one priority.
Another priority may be reducing the number of slips and falls on the shop floor. Also, perhaps you had a forklift accident occur once and a bunch of hand-tool errors.
Now that you’ve got a running list of hazards it’s time to assign them each with a grade. We call this a Risk Assessment.
A risk assessment is an examination and evaluation of hazards present in a workplace. It’s the process of cataloging and classifying the various machines, equipment, operational procedures, employee behaviors and habits, working conditions, and other potential factors that could cause people harm. Dive into how to conduct one here >>
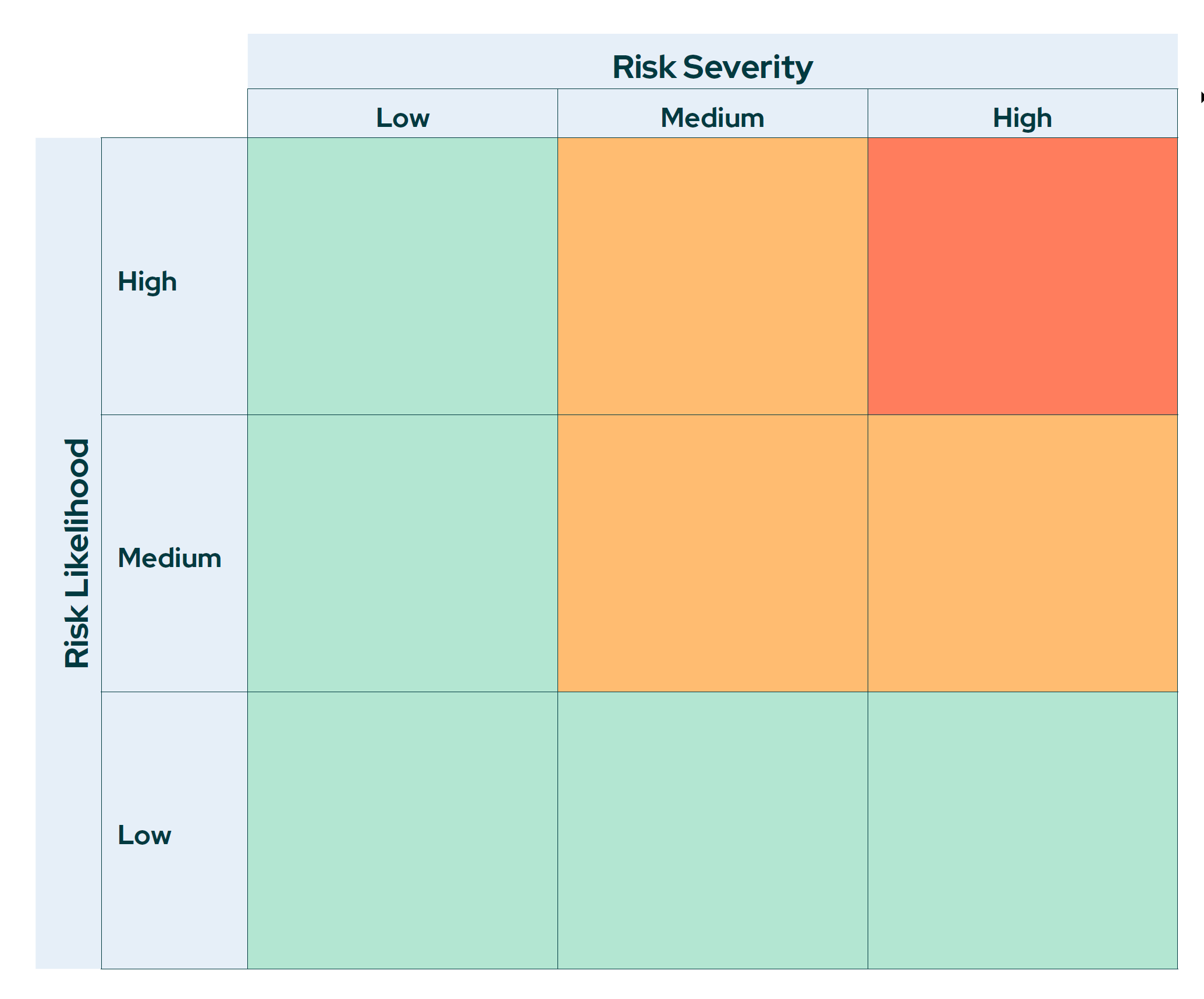
3. Build Your Strategy
Ok, you’ve assessed your risks and figured out which ones you want to tackle first. Next, it’s time to focus on pre- and post-mitigation strategies.
Both pre- and post-risk mitigation focus on risk severity (acceptable, tolerable, undesirable, intolerable), risk likelihood (improbable, possible, probable), and risk level (low, medium, high, extreme).
Between pre- and post-mitigation lies an important step: Identifying the department(s) involved and mitigations, warnings, and remedies.
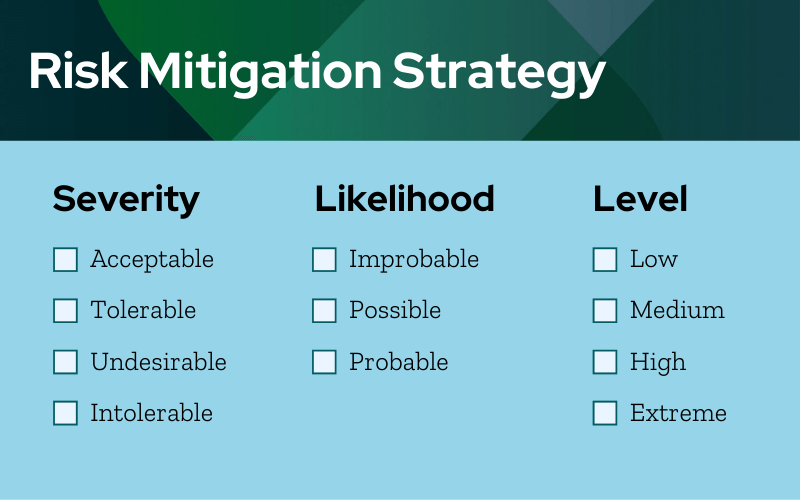
Let’s talk slips and falls as an example.
The pre-mitigation risk severity is tolerable. The risk likelihood is probable. And the risk level is medium to the service department.
To decrease the risk, perhaps you’ll want to increase floor inspections to three times a day. By doing so, the post-mitigation risk severity is still tolerable, but the likelihood has moved from probably to possible, and the risk level remains medium.
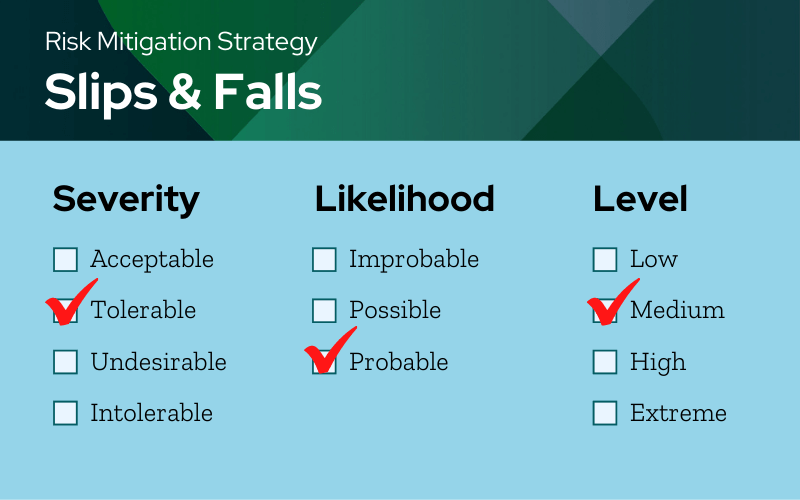
Now, let’s use a car lift accident as an example.
The pre-mitigation risk severity is intolerable, the risk likelihood is possible, and the risk level is high.
But, by instituting mandatory automotive training and contract lift inspection service, the risk likelihood drops to improbable once employees are trained and the lifts are deemed to be in good shape. Therefore, the risk level also drops from high to medium.
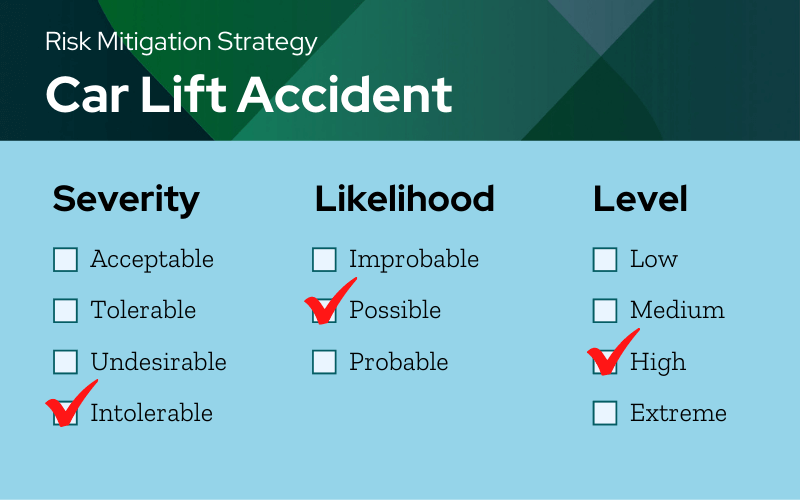
For safety issues like forklift training hand tool errors, practices such as instituting a forklift safety program and holding shop safety talks could be examples to risk severity, likelihood, and levels.
The bottom line: This can be a labor-intensive process for the team, but by doing this, you’ll be in a better position to manage safety risks and your safety program as a whole.
4. Walk the Walk
If you show up to the shop floor without safety glasses on, that sends a message that perhaps those safety glasses aren’t all that necessary on the shop floor. The next thing you know, the mechanics aren’t wearing eye protection, and an accident results in an eye injury. So, always “practice what you preach.”
Give employees responsibility and provide them with active ways to be involved in your safety program.
Responsibility leads to accountability, and this is a critical point to focus on when it comes to safety engagement. Here are a few suggestions to get you started:
- Track the number of workers involved in developing safety procedures, and participating in tool-box talks, and injury investigations
- Ask employees for feedback on reasonable safety goals ahead of safety meetings
- Look to see how many employees participate in safety-perception surveys
- Ask for their input in developing task-specific job safety analyses/job hazard analyses on how to perform routine tasks safely
- Have them participate on accident investigation teams and help to identify/implement corrective actions to eliminate hazards
These are also all examples of measurable leading indicators that can help make a safety program successful.
Use incentive programs based on leading indicators.
Need some ideas?
- Institute a “See Something Say Something” initiative.
- Reward those who participate in a job safety analysis who identify the risks their specific tasks pose.
- Start an anonymous safety glasses spot check. Team mates who are following the rules get a reward, such as lunch with the company president.
Whew! This is a lot of information to digest.
But worth it for a strong dealership safety culture.
But, we’re confident that if you invest in addressing these issues, you’ll improve and sustain a successful safety program.
KPA has everything you need to create a safety program that works and a dealership safety culture that sticks. Organizations of all kinds rely on our tools, training, and consulting expertise to minimize risk and maximize business performance. Let us show you how we can help.