Use the 5S System and Keep Your Facility Clean, Safe, and Efficient
So you’ve taken a long, hard look at your facility and determined it’s time to clean things up. Time to disinfect and declutter. Time to organize and streamline. Time to take care of the mess before it becomes a source of injury, illness, or regulatory fines. Ready to roll your sleeves up and get to work? Here’s how to practice good housekeeping as swiftly and efficiently as possible with the 5 S Principles (also known as the 5S System, or simply 5S)—a lean business methodology for workplace organization.
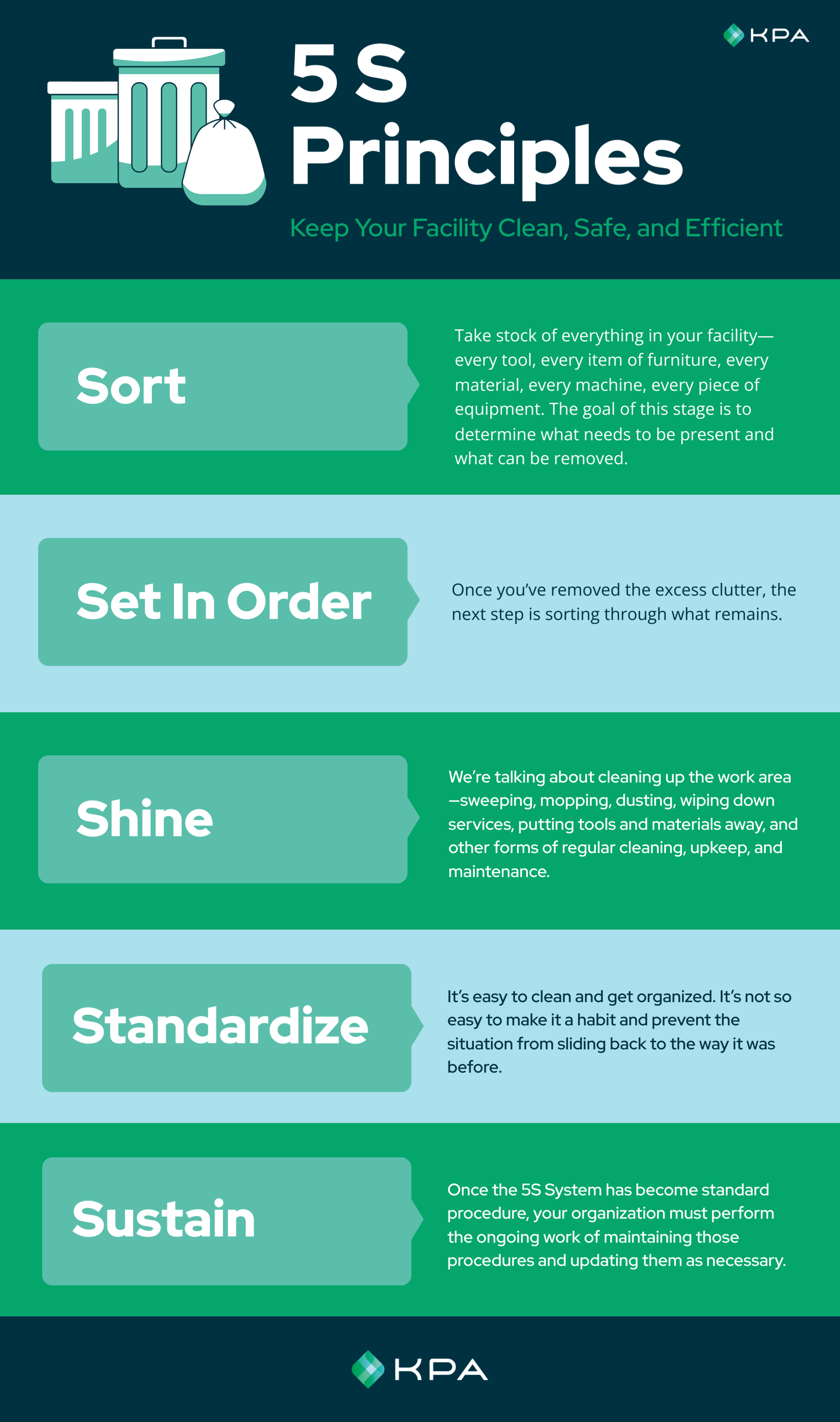
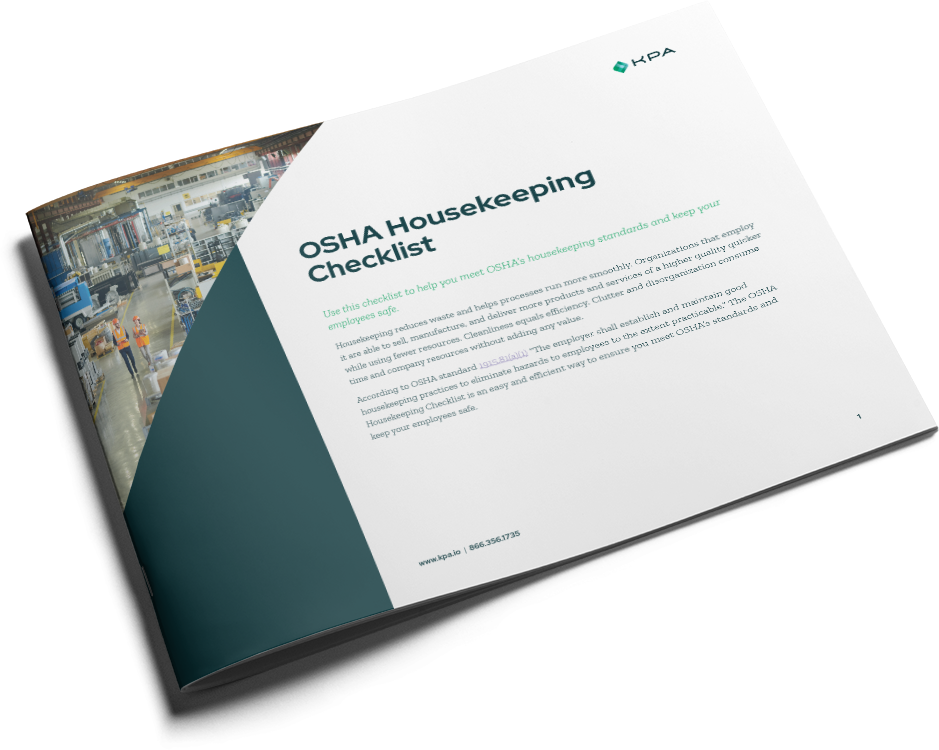
OSHA Housekeeping Checklist
Download KPA's OSHA Housekeeping Checklist to help you identify areas in need of some good housekeeping.
An Overview of The 5S System
Phase 1: Sort
Take stock of everything in your facility—every tool, every item of furniture, every material, every machine, every piece of equipment. If possible, bring everything into a common area, so you can go through it all at once.
The goal of this stage is to determine what needs to be present and what can be removed. Channel your inner Marie Kondo—only instead of considering whether something sparks joy, ask the following questions:
- What is the purpose of this item?
- When was this item last used?
- How frequently is it used?
- Who uses it?
- Does it really need to be here?
You may find out that certain items are obsolete, either because you have an upgraded version of the same item available, or because the item is seldom or never used. In other cases, you might discover that you have multiples of the same item when you only need one.
These questions help determine the value of each item. A workplace might be better off without unnecessary items, as these things can get in the way, take up space, and ultimately become hazards.
Be sure to involve your team in these determinations. The best people to assess the items in a space are the people who work in that space. They’re the ones who can most accurately answer the questions above.
When you’ve determined that an item isn’t necessary, you have a few options:
- give it to a different department
- put it in storage
- recycle it or throw it away
- sell it!
Yes, you can make money from items you don’t need. Even scrap metal can fetch a couple hundred dollars.
Tip: Use the red tag method. Keep in mind that sometimes an item’s value may be uncertain—for example if it hasn’t been used recently, but might be needed in the future. In these cases, use the red tag method. Red tags are typically cardboard labels or stickers that can be attached to the item or items in question. These tags can contain a wealth of information about each item—such as the item’s location, its description, the name of the person applying the tag, the date of the application, and so on. Red-tagged items should be placed in a designated area, and if the items haven’t been used after a specific amount of time (e.g. 1–2 months), it’s time to get rid of them.
Phase 2: Set in Order
Once you’ve removed the excess clutter, the next step is sorting through what remains. There’s no universal standard for organizing and arranging workplace tools, equipment, and materials. You’ll need to develop a system that works best for your organization.
Here are a few questions to help you along:
- Which people (or workstations) use which items?
- When are the items used?
- Which items are used most frequently?
- Should items be grouped by type?
- Where would it be most logical to place items?
- Are more storage containers necessary to keep things organized?
This is the perfect opportunity to drive organizational efficiency. The way you place items can improve ergonomics and cut down on unnecessary motion. Think logically, in terms of process. You’ll need to consider what tasks are involved in your business processes, the frequency of those tasks, the paths people take through the space, and so forth.
At this point, you may want to pause and think about the relationship between your housekeeping and other lean organizational efforts. What arrangement will cause the least amount of waste—the fewest wasted materials and the fewest wasted minutes for workers. Every extra motion translates to lost time. Every 30 seconds spent moving across a facility adds up, particularly if we’re talking about something 100 employees do every day of the year.
Tip: Waste takes many forms. Maybe it’s walking back and forth between areas to do a job because interrelated materials aren’t kept in a shared location. Perhaps it’s excess inventory taking up space. Or maybe it’s unutilized or under-utilized talents—your people aren’t contributing to the fullest of their abilities.
Phase 3: Shine
This is the fun part.
Not really. Shining is the hard labor of housekeeping. We’re talking about cleaning up the work area—sweeping, mopping, dusting, wiping down services, putting tools and materials away, and other forms of regular cleaning, upkeep, and maintenance.
This is perhaps the most frequently overlooked phase—especially when work gets busy. But it’s important to continually make time for it, for a number of reasons:
1. It keeps people safe. A slippery or dusty surface can cause trips and falls—the most common form of workplace injury, and the #1 OSHA violation. Clean up spills and you’ll save thousands on fines, medical bills, workers’ compensation costs, and lost productivity.
2. It helps your bottom line. Maintenance ensures your equipment stays operational. Keep things clean and humming and you’ll minimize the chances of a work stoppage and ensuing profit loss.
3. It improves workplace morale. Shining is everyone’s job—not just the janitorial staff. In the 5S system, every worker takes responsibility for cleaning up their workspace, ideally on a daily basis—e.g. at the end of the shift. Doing so helps people take pride in their spaces, which in the long run means they’ll be better invested in their work and in the business.
Tip: Not everyone knows how to clean properly. Shining may seem obvious, but it’s a skill that many people need to learn. Show your employees—especially new employees—which cleaners to use, where cleaners are stored, how to clean equipment, and so on. Some shine jobs may be more challenging or delicate than others (e.g. computer equipment), so make sure you’re giving the right people responsibility.
Phase 4: Standardize
Once you’ve completed the first 3 steps of the 5S System, you’ll undoubtedly notice a difference. All that extra stuff is gone, everything’s organized, spaces are cleaned, and equipment is in good working order.
The problem is keeping everything that way. It’s easy to clean and get organized. It’s not so easy to make it a habit and prevent the situation from sliding back to the way it was before.
The Standardize phase is what makes the 5S System different from the typical spring cleaning project. It’s how you systematize everything that just happened, turning one-time efforts into habits.
You’ll need to assign regular tasks, create schedules, and post instructions. Standardizing makes it clear to employees what’s needed and expected, along with how to do it. More importantly, it lets people know who is responsible for what.
Depending on the workplace, a daily 5S checklist or chart might be useful. In many organizations, this takes the form of a posted schedule indicating how frequently certain cleaning tasks must occur, and who is responsible for them.
But checklists and instructions only go so far. Initially, your people will probably need reminders. Just like anything else, you’ll need to assign tasks, check in, and offer help and guidance when necessary. Eventually, housekeeping activities will become routine—part of the organization’s standard operating procedures—but your team will need nudging to get there.
Tip: Use visual cues. Signs, labels, posters, floor marking tape, tool organizers—these visual cues play an important role in 5S. They’re reminders that housekeeping work needs to be done. They can also provide clear instructions—without words—for keeping items in place.
Phase 5: Sustain
Finally, once the 5S System has become standard procedure, your organization must perform the ongoing work of maintaining those procedures and updating them as necessary.
The Sustain phase is about making 5S a long term program, not just an advanced short-term project. It’s how you turn this into a part of your organization’s culture. And if you do it right, you’ll start to notice continuous positive results.
To create a sustainable housekeeping program, you need to involve everyone—all managers and employees on the manufacturing floor, in the warehouse, in the office, and elsewhere. All workers should be aware of the initiative and their role in keeping the workplace clean and organized.
Successful 5S organizations know how to keep things interesting. Look for areas that can be improved and ways to make cleaning fun and rewarding. Pay attention to what other organizations are doing—new ideas and advances in the 5S System come along often.
Remember: housekeeping is an ongoing practice. I’d say it’s a marathon, not a sprint, but marathons end—the work of housekeeping is never over. This is why it can be so challenging for organizations to move past Phases 1–3 of the 5S System.
When you launch your housekeeping initiative, you might grab people’s attention—you might get them on board right away. But it’s that period between when it’s new and when it becomes a routine that you’re most likely to lose people. After they’ve done it once, they won’t want to keep doing it. Their passion will fade. They’ll become burnt out. That’s why managers need to get creative with how they keep people motivated—a topic we’ll explore in our next article.
Don’t wait until then to start cleaning and improve your organization’s housekeeping. KPA’s workforce safety and compliance team can help—contact us.
Related Content
Explore more comprehensive articles, specialized guides, and insightful interviews selected, offering fresh insights, data-driven analysis, and expert perspectives.
Notice: Undefined index: post_type in /nas/content/live/kpaioprod/wp-content/themes/total-child-theme/kpa_cards_shortcode.php on line 10
Notice: Undefined index: post_type in /nas/content/live/kpaioprod/wp-content/themes/total-child-theme/kpa_cards_shortcode.php on line 15
Notice: Undefined index: taxonomy in /nas/content/live/kpaioprod/wp-content/themes/total-child-theme/kpa_cards_shortcode.php on line 16
Notice: Undefined index: tag in /nas/content/live/kpaioprod/wp-content/themes/total-child-theme/kpa_cards_shortcode.php on line 17