Where Should You Focus to Improve Your Safety Program? Here are Two Tips
Having a safety program in place is a great first step. But a lot goes into making that safety program an ongoing success. Where should you invest your time and resources to continually improve your safety program? Where should you start? We’ve got some suggestions.
Tip #1:
Dive into your leading and lagging indicators
A good launching point is to look at your leading indicators and lagging indicators.
What is a Leading Indicator?
Leading indicators are forward-looking indicators where the focus is on proactively identifying and discussing ways to create a safe workplace with the goal of getting to zero loss.
Common leading indicators include:
- Risk assessments
- Hazard assessments
- Supervisor training
- Employee training
- Safety committee meeting attendance
- Walk-through audits and inspections
- Employee suggestions
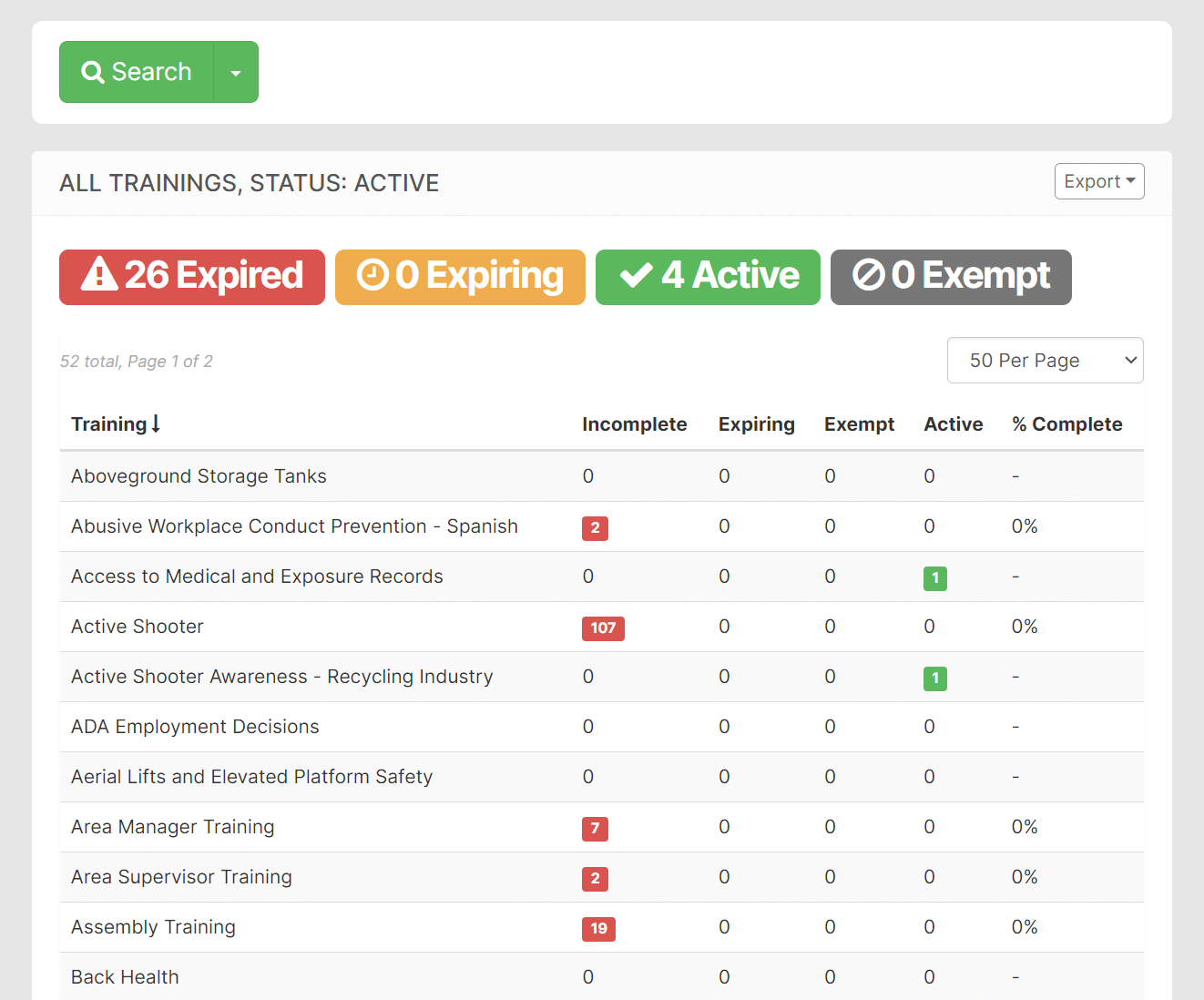
Monitoring your employee training is an example of a leading indicator.
What is a Lagging Indicator?
Lagging indicators take into account what’s already happened. For instance, they focus on things like:
- Recordable injuries
- Citations
- Incident rates and days away, restricted or transferred (DART)
- Worker’s compensation claims
- Experience modification rating (EMR)
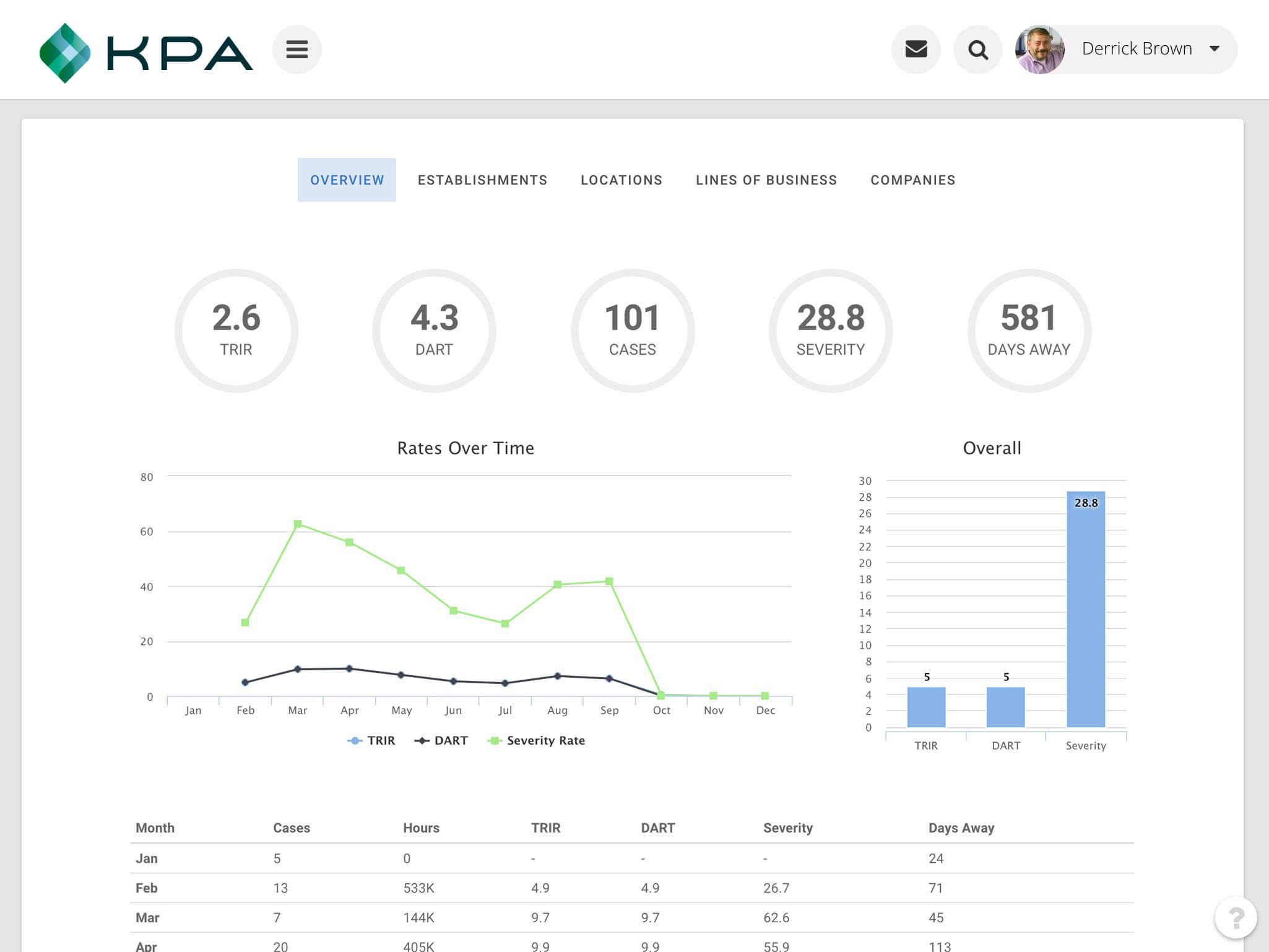
DART and TRIR are examples of lagging indicators
Let’s say your shop had 15 eye injuries last year. That’s a lagging indicator signaling that everyone should be wearing safety glasses and that the company should have an eye injury prevention policy in place to avoid future incidents.
A leading indicator would be something like “only 25% of our workers in Indianapolis have completed their PPE training.”
You’ve gathered your data. You’ve evaluated your leading and lagging indicators to identify where to invest your time. Now, let’s look at how to approach these indicators.
Tip #2:
Use PDCA to develop your approach to closing potential safety gaps
PDCA is a continuous improvement process used across many different fields, from engineering to customer service. And it’s a great tool to use for workplace safety as well.
The acronym PDCA stands for:
- Plan
- Do
- Check
- Act
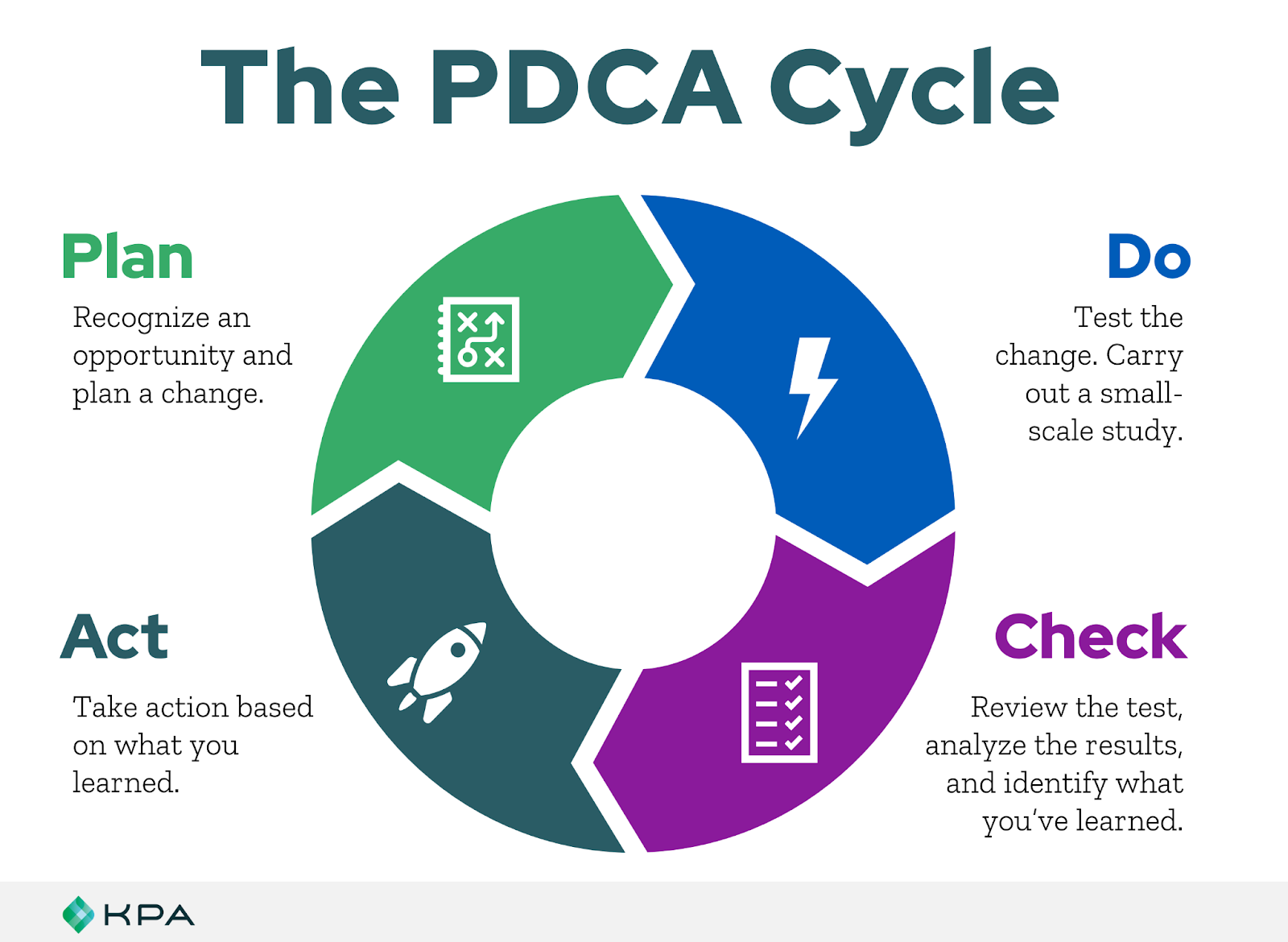
Plan
Identify the strategy for improvement by asking questions such as:
- What’s our vision of how we can improve things?
- What’s the business need for doing this?
- What strategy will we use to achieve the vision?
- What are the tactical and operational goals that will help us achieve the underlying goal?
Do
Focus in on the data. Specifically, the goal is to first:
- Define what will be measured
Then to:
- Gather the data by identifying the who, how, and when, listing the criteria for evaluating the integrity of the data, outline operational goals, and service measurement
Check
The focus here is on the information and processing the data. This is done by looking at the:
- Frequency
- Format
- Tools and systems
- Accuracy of the information
Act
Apply the knowledge gleaned from previous steps to first:
- Analyze the information and the data (look to see if you can spot any trends, targets, and necessary improvements)
Then:
- Present and use the information, which means drafting an assessment summary and action plans.
Plan again
Implement improvement measures.
At each step, it’s important to apply the SMART goal framework. What’s that, you ask? SMART goals are Specific, Measurable, Accountable, Reasonable, and Timely. We’re going to take a look at this process as it relates to improving safety programs in our next post – so stay tuned.
Did you notice how critical data and reporting are to the success of these initiatives?
The analysis you need to make a truly sustainable safety program relies on lots of data…at your fingertips…at your team’s fingertips. That’s where EHS Software truly shines. Analyze your findings and take corrective and preventative actions. Schedule daily/weekly/monthly email reports to be sent to you and your team, including recent reports, pending follow-ups, training status, inspection status, and more.
Let us show you how to use data to build a successful safety program >>