Mid-Year Regulations Review – an Interview with Zach Pucillo
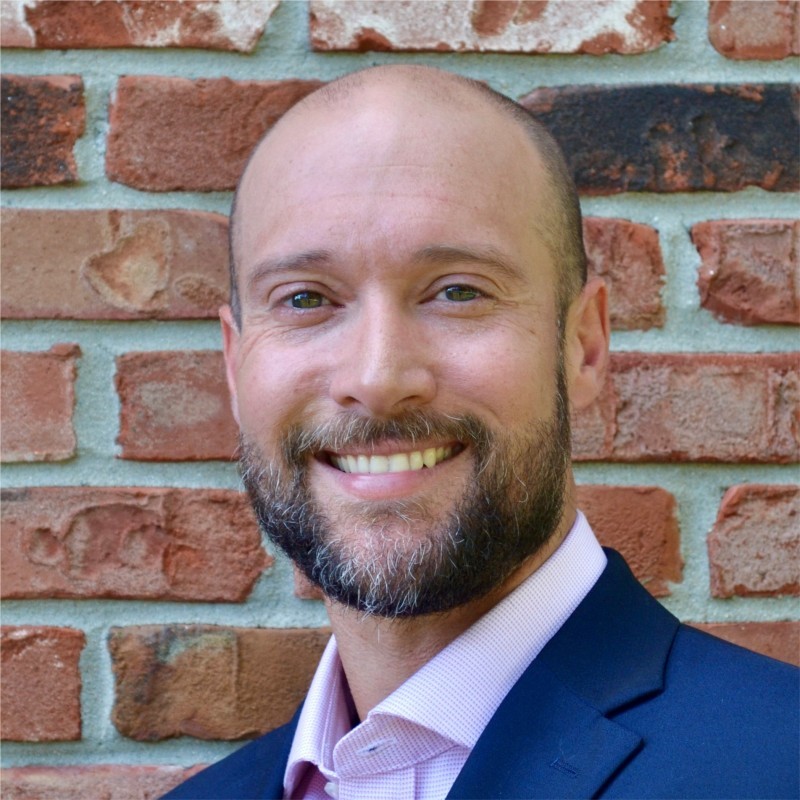
Today, we’re speaking with Zach Pucillo, KPA’s own EHS regulatory compliance manager. A certified safety professional and certified hazardous materials manager, recognized in 2022 by the Alliance of Hazardous Materials Professionals as Hazardous Materials Professional of the Year and accepted into the 2022 Class of Rising Stars by the National Safety Council. Thanks for being with us today, Zach.
Thank you very much for having me, Kat. It’s always a pleasure to be on here.
[00:45:08]
Absolutely. So, I know we had you at the beginning of the year, and we’re jumping in for a mid-year update. So, we want to get a temperature on things that have been going on and your expertise in that area. So, to jump into the first question, what are some notable updates or revisions that have occurred within the regulatory landscape around EHS since the beginning of the year, and how are businesses adapting to these changes?
Sure. There have been a few different releases from some of the regulatory agencies, and some other items have been moving along that whole proposal into the rulemaking path as well. So, there are a couple of key updates when it comes to the environment.
So, the Environmental Protection Agency did make an update to the Clean Water Act. And so, what the requiring is that, if you’re a facility that has hazardous substances that you store on-site and you have certain quantities of those hazardous substances, now you have to make what’s called a facility response plan and put that into place and it’s basically making sure that, if you have any type of release of that substance, it doesn’t get to what they deem as a navigable water of the United States which they’re still trying to define that, that’s an ongoing ever-ending thing in the courts. But I have always interpreted it that if you can put a canoe in that body of water and paddle one inch, it’s a navigable water of the United States.
So, if the facility has what they have deemed as hazardous substances and so what’s a hazardous substance? If you go to the Clean Water Act, they have a list, they have these reportable quantities on there, if you store over those reportable quantities, then you have to come up with one of these response plans. And so, you’re basically indicating here’s what we have on-site, here’s how we’re going to make sure that these things don’t get released and into the water and, if we do have an accidental spill, here’s how we’re going to respond to it. So, it’s very similar to the SPCC rules that came out about 15 years ago, but now we’re talking about not just petroleum-based products, that’s what the SPCC rules we’re talking about, but now we’re talking about any type of hazardous substance that’s on that list of lists in the Clean Water Act.
So, if you’re a facility, you have to take a look at this regulation, take a look at the list of lists, and see if you store anything on-site that could have potential that could end up getting into a waterway that could be nearby. The EPA has also banned a few chemicals that were used in production in the United States for a long time, one of them being asbestos, and that’s a term that most of us are familiar with. So, asbestos is a material that was commonly used about 40 or 50 years ago in a lot of different products out there because it is very heat-resistant. And so, you could put it on different coatings for, in vehicles, you have a hot engine that’s going so you would need a gasket around certain parts, you would use asbestos. The same thing with brake pads and different products that are out there, mainly on gaskets though where asbestos was used.
And so, the EPA has now banned all commercial use of asbestos and, therefore, that’s a great thing for employees in the work environment because, if they’re manufacturing those products and they’re being surrounded by asbestos or maybe they’re just using those products, once that stuff becomes airborne, so if they’re grinding on any type of asbestos-related products or anything like that, these fibers become airborne, they get into employee’s lungs and they cause long-term diseases out there. Lung cancer, mesothelioma is another common disease that’s out there that can be linked back to asbestos, so it’s a great thing that they’re banning that.
For a facility, you just have to take a look at whether we are using any asbestos-containing products, are our employees exposed to any of that. For instance, it’s pretty much phased out by now, but in an automotive dealership, in the repair shop, because asbestos was in the brake pads, technicians were cleaning those rotors and, if they weren’t careful, if they were making that dust get airborne, that can get into their lungs. They’ve pretty much phased out that from the brake pads at this point, but still older vehicles may still have that on there so it’s a good thing that it’s being phased out completely.
And then one last thing the EPA has done recently, they’re banning a chemical called methylene chloride. And so, methylene chloride and also perchloroethylene are two chlorinated solvents. The chlorinated solvents were used for a lot of different commercial properties to do cleaning because they would be great at cleaning and it wouldn’t leave a watery mess behind. Chlorinated solvents would actually evaporate into the environment so you could do some good cleaning and then not have that watery mess but when that stuff evaporates, it’s very bad for the central nervous system. And so, what they’re doing is, perchloroethylene was used in dry cleaning, methylene chloride was used to clean different machine parts that are out there, it’s a great degreasing agent but, once again, very bad for the employee’s health. So, that’s being completely phased out of US manufacturing out there.
So, those are some of the main updates I’ve seen from the EPA, they’ve also had out there about PFAS or polyfluorinated alkalinal substances, I refer to them as forever chemicals. They’ve actually set some limits on forever chemicals and how much can actually be exposed to the environment from the manufacturing industry. So, forever chemicals, we’re talking about waxes and little bitty bits of microscopic plastics, these things never break down. They get out in the environment, they never break down. They get into a pond, they get into the soil, and then we have animals that can ingest that, bioaccumulation, we ingest the animals, and then we ingest that stuff as well, and it’s been linked to causing diseases. So, the EPA has set limits on how much of that can actually be produced in the United States as well.
From the safety standpoint, OSHA just released a rule update, it’s the designated employee representative rule update. So, in the past, when there was an OSHA inspection going on, you would have a compliance safety and health officer come out on-site to investigate the findings of the complaint or whatever triggered the inspection. And so, in the past, the employer had the ability to designate a representative to come in and accompany that inspection. Maybe it was an attorney, who could have been a safety professional who really knew the industry that could help with the inspection to make sure that it was actually going right. Well, now, the new update is that the employee who submitted the complaint or who is going to participate in the inspection can actually designate their own representative as well.
So, you can have an employer representative, you can have an employee representative, and the employee representative does not have to be an employee of the actual company that’s being inspected. So, they could go out and get their own attorney, their own safety and health representative, or what’s getting out there in the news today is they could actually get a union representative to come into their shop and accompany that inspection even if that shop is not unionized.
So, why would they seek out a union representative? Because a union representative knows the rights, they know the industry, and they know what the safety implications are for that industry so they may want to choose a union representative that has much more knowledge about that industry to help the compliance safety and health officer, but that health officer has the complete say-so in authorizing representatives or not allowing a representative to accompany them. So, it’s really all up to that compliance, safety, and health officer when they’re on site.
OSHA also has presented a draft of their heat illness prevention standard that’s going to be a federal standard to an advisory construction safety committee. And that committee actually took a look at the proposed rule, and they said, “We urge you to get this into the notice of proposed rulemaking.” They want to get this out as fast as possible, this has been in the works for some years now, and so, to see OSHA actually get this into a notice of proposed rulemaking, meaning it is actually getting some traction going along.
So, this could be pretty substantial because it would be a federal rulemaking across all 50 states to all employers to make sure that, once certain temperature thresholds are reached in the summertime, heat illness prevention policies will kick into place for that employer. Meaning it’s probably going to be shade breaks, it’s going to mean additional water, it’s going to mean making sure that employees are trained on recognizing heat illnesses as well. So, this will have a sweeping requirement call to action for all employers if it ever gets put into a final rule. There will be some lobbying back and forth, so we don’t know what those thresholds will be but it is actually moving that regulation down the road.
So, keeping advised of that and, also, there is a national emphasis program going on right now. If a compliance officer is doing an inspection, they can actually add a heat illness-related inspection in as well where they’re going to check in to see if employees are being exposed to the heat and if they are being properly protected as well. And then, finally, from the OSHA standpoint, a little bit of news here is that OSHA is restructuring some of their regions for their regional offices that are out there. So, they will still have 10 regions, but on the West Coast, now everything will be known as the San Francisco region, and so they’ll have an office in San Francisco, and that will be the only office out there for pretty much the entire West Coast.
And then, in the southeast, they’re going to add a regional office in Birmingham, Alabama. And so, they’re actually going to restructure some of that regional area down there, such as the Panhandle of Florida will report to the Birmingham location. Why is that important? It’s just we have to understand that if you have any type of reporting needs, such as reporting a fatality, or an amputation, or a loss of an eye, then you would have to make sure you’re reporting to the right regional office. So, making sure you understand which one you would report to, and which area or region you fall into is going to be key going forward as well. So, that’s all the different updates that I’ve seen come across from the beginning of the year up until now.
Our Better Workforce Blog is your Ultimate Guide!
Stay informed with weekly industry updates, expert insights, best practices, and actionable tips to enhance workplace safety and compliance.
[00:11:01]
Sounds like these regulatory bodies have been really busy making all these updates.
But you and I, being part of this industry, know that new rules are really nothing without the enforcement of these rules. So, can you tell us a little bit about how these bodies, like OSHA, the EPA, and DOT, are continuing to enforce existing regulations along with these new rules and maybe what trends are emerging in terms of compliance and enforcement strategies among these bodies?
Yeah. Let’s just take OSHA, for example. When it comes to enforcement, how they’re stepping it up, well, they just asked for a budget increase as well too from the White House administration and it has been granted. They didn’t get exactly what they wanted, but they got a 3% budget increase pretty much and so they’re going to be able to staff more enforcement officers is the plan to use that budget for. So, inspections are one thing, of course, that they do, and that’s based on whistleblower protections, they have targeted programs as well,t, they have these national emphasis programs, the main one right now is related to heat and fall protection.
Also, they’re taking injury and illness data that they’re receiving annually as well. Every year, organizations have to report the OSHA 300 information electronically. Not everybody but some of them do. And so, they’re receiving that data, and now they’re starting to analyze it and determine what are the high-hazard industries out there, what industries are having more accidents than the other industries. And so, once they take a look at that, they’ll be able to target their enforcement and their national emphasis programs a little bit closer to home to some of those different industries that have those higher rates of injuries that are going on out there.
So, the rates of the regulatory agencies fall in line with that is really trying to analyze data that they’re collecting to see, okay, where should we put our enforcement strategies at when it comes to the different industries that are out there. And then some of the trends that you were asking about, they’re looking at using more digital tools. For instance, OSHA is looking at worker health issues as well, which they haven’t looked at as much in the past. They want to make sure that employees are retaining information as well. They understand that management is probably going to understand what they need to do for OSHA compliance, such as, if I’m a compliance officer, “Hey, do you have SDSs?” “Yeah, yeah, we have a whole book of them, or we have them online.”
But OSHA’s taking a step forward, and they’re having more and more informal interviews with employees and asking them on the fly, “By the way, do you know if you have a safety data sheets?” And if that employee has no idea, well, the employer is not doing their job to pass that information along and so we’ve got training issues that are going on. OSHA won’t state it, but the head administration is very pro-collective bargaining agreement, and they want to see your workers’ rights protected without having to step into the situation, so they want to see as much proactiveness as possible.
A large focus as well too has been on warehouse and distribution centers as well. Online shopping. I bought something from Amazon yesterday, and it showed up today. And so, that time that I bought something from when it showed up today, meaning an order had to go into that distribution center, and employees had to pick it, pack it, get it on a truck, get it to the warehouse, then they had to get it onto a different delivery truck, and that delivery driver had to get it to my house and that all happened within a 24-hour span. So, are we really being as safe as possible throughout that 24-hour span?
I love convenience, I love getting things as fast as possible, but if I were a consumer and I knew that, hey, getting this tomorrow meant that somebody’s at risk of cutting off a finger, getting into a severe accident because we’re cutting corners on trying to get that package delivered, that’s a trend that OSHA is looking into. We all love convenience, and we all love efficiency, but we have to make sure that we’re doing it safely as well. So, the top trends, proactiveness, really enhancing your training as well too of your employees, making sure they understand all the implications, the consequences of cutting corners and then, also, just public awareness as well.
So, when something goes wrong, if we find in a distribution warehouse center that there are so many OSHA violations that are happening, that information is quickly getting out to the public via social media campaigns, via news outlet centers. And so, everybody, I’m sure, subscribes to some news outlet center, and it comes right across our phones at this point. This company was cited X amount of dollars because of 14 safety violations or a fatality happened here. So, that public scrutiny is also a trend that OSHA is trying to, and all these agencies are trying to use to make sure that companies and organizations are stepping into compliance.
[00:16:02]
Absolutely. Another reason I really appreciate being in this position is understanding all of these things and being able to see how these bodies are changing things and making sure that we’re keeping people safe. So, in that same vein, I know that these regulatory bodies are sometimes seen as a hitch in the armor for these businesses or something that they have to deal with. But I know that there are ways that these regulatory bodies are trying to collaborate with these businesses in order to address these issues and to make sure that they’re keeping people safe. And in that, I know that there are some environmental changes, things that we’re seeing when it comes to extreme weather, pollution, things like that.
Can you tell me about some of the initiatives being undertaken to promote sustainability and environmental stewardship? I think you touched on it a little bit in the first question, but I’d appreciate it if you could delve deeper into that.
Yeah, there are a few initiatives out there just off of reference. They happen to make sure that we’re trying to control global warming as much as possible, climate change, just like you mentioned. So, for instance, the EPA regulatory wise they have, and this is more enforcement than it is collaboration. There’s some collaboration as well too, I’ll get to in a moment. But enforcement wise would be like there’s what they call the AIM Act.
And so, the AIM Act is about trying to control the refrigerants that are used in a lot of our different products because those refrigerants contain a chemical called hydrofluorocarbons, and they get into the atmosphere, and they can deplete, pretty much, the ozone layer and then cause, at that point, global warming to happen a little bit more and more and more. So, the AIM Act is set by the EPA, they’re trying to phase down those hydrofluorocarbons from being emitted into the environment by about 85%, and they have a goal year of trying to get that accomplished by 2036.
So, they’re really hitting the refrigerant, different manufacturers, industries out there trying to look at different chemicals to substitute. Let’s think about it, it’s been getting hotter, so how do we cool ourselves off? Well, we use refrigerants. Well, that’s actually causing some of the global warming that’s going on out there. So, if we can control the refrigerants, then, hopefully, it’s not going to be as hot in the future and, therefore, we don’t need to rely on refrigerants as much.
But hey, let’s face it: those hot summers, we’re going to want our air conditioning in our vehicles and homes, we want to keep our food from spoiling and all that. Refrigerants are here to stay, but can we substitute different chemicals that can be a little bit safer and not as harmful to the environment when it comes to that?
Another thing is that the EPA also, I call it the EV rule. So, basically, by, I think, 2028, they want most of the production of vehicles out there to be electric vehicles. So, we’re seeing a lot more lithium-ion batteries being used out there, we’re seeing the switch over in the manufacturing side to more EV-type use, and, therefore, that’s going to control some of the carbon emissions that are being put out there from electric vehicles.
So, those are more enforcement strategies, but there are different ways for companies to also partner. EPA’s got this Green Power Partnership as well. It’s a voluntary program and it encourages organizations to use green power as a way to reduce those impacts on the environment. So, trying to get away from as much electricity use, trying to cut down as much of that anymore, that’s why you’re seeing some of these vegetation roofs that are out there, seeing more solar panel usage out there to try to cut down on the carbon footprint but also how much energy is being consumed by these businesses.
Department of Energy has Better Buildings initiatives and so there’s money out there in some of these partnerships to go out and collect if you were willing to put in some of these different technologies to help with the systems of trying to be less energy consuming. Motion detectors on lights, LED lights for your parking lots as well too or for your whole lighting structure that is in there, all these different things. Solar panel energy, as I just mentioned, very much coming up, and trying to partner with these different companies and give incentives in the form of tax credits for the use of these items, just like the Energy Star program that we use for our household consumers. If you buy an Energy Star-rated appliance, then you’ll get a tax credit for that because it doesn’t have as much of an impact on the environment.
Environmental, Social, Governance as well, ESG, is a big popular term that’s been out there over the past year, and that is just really the due diligence of these companies to promote what they’re doing to have less of an impact on the environment. They want to make sure that they’re promoting what they’re doing so the consumer sees that and, “Hey, I want to buy from that company because they are actually trying to make sure that the environment is being protected.” So, you’ll see a lot of this environmental social governance terminology out there and it’s really to try to lower those carbon footprints, lower that energy usage and preserve the environment and be a good company in doing so. So, lots of different partnership collaborations that are going on.
[00:21:12]
Those sound awesome and like a great way for companies to offset what they may perceive as an unexpected cost in trying to do these things or meet these regulations. So, thanks for sharing that. I think those are some really good tips for our listeners. I know environmental is one side, but there are a lot of other aspects when it comes to regulations. Especially around transportation, I feel like we’ve been seeing a lot about the DOT recently.
So, can you tell us a little bit about how companies are addressing transportation and logistics challenges in light of these DOT regulations, particularly concerning safety standards and compliance with transportation laws? Have any innovations been adopted to enhance efficiency here?
So, you mean the how’s my driving phone number, bumper sticker is not working anymore? No, it’s been time for technology updates. I mentioned it earlier, with the warehouse and distribution centers that are going on, we have so many different fleets of trucks that are now going all through in and out of our neighborhoods at this point. We have fleets of trucks that are trying to transport all these customer goods across the country and get them there in such a timely fashion that you can have access to them within 24 hours of actually ordering them. So, are we being safe over the road?
Well, the DOT is experimenting with a lot of different items out there. They’ve got a technology that uses what they call interoperable wireless communications, and they actually tested this out in Wyoming on a stretch of Interstate 80 which goes pretty much across the entire state. And you think of Wyoming, okay, probably think of Wyoming, maybe not a whole lot of populated metro areas or anything like that, but it could be a harsh winter environment. I-80, you’re not thinking of too much lighting as it gets into the evening and nighttime hours and so that could be very susceptible to a lot of different roadside hazards that are out there.
So, what they did was they equipped about 300 or so trucks in a fleet with these onboard systems, it’s like a tablet that they would put in there, and that tablet would automatically collect data and then relay data to the other 300 trucks that were within that fleet. And so, it would get weather updates, it would get construction updates, it would give any type of roadside accident updates. In the wintertime, we’ve seen some of the videos, and I’ve seen them as well too, when the roads get iced over, or we have a whiteout condition, all of a sudden, it turns into a 50-car pileup. If you’re a truck driver and you have one of those onboard types of tablets and it tells you whiteout conditions, massive roadside accident up ahead, all lanes are closed down, at that point, you’re going to probably pull off and take the next exit and not contribute on to that type of a hazard.
So, these little interoperable communication systems are pretty cool, actually, and I’m hoping that we’ll see more fleets actually put those into place. There are electronic logging devices so that truckers can track hours as well too for road safety, and lots of different fleet management systems so you can do monitoring of your driver locations, they’re driving behavior, and their vehicle health. Me as a personal consumer who has to buy car insurance, and I’ve got a brand new driver on the road, actually, my daughter just turned 16, and got her license, and I’m praying every day. But with the insurance, we’re looking for discounts, and so we have this drive trend type of application that just monitors our driving habits, and then it just lets us know, hey, you sped over 10 miles per hour over the speed limit this many times over the past week.
If we have that type of system within our fleets as well, as safety managers, we can monitor that data and then curb our training and policies to try to correct those bad behaviors. So, the DOT is really trying to promote a lot of that out there. Instead of just trying to put out enforcement, they’re trying to promote a lot of these different technology strategies to make us safer on the road.
[00:25:20]
That sounds like there’s a lot going on to make sure that people are safer and using technology to make sure that things are on the up and up and we take care of our people and reduce these risks, so that’s great to hear. And I know that we talked about a lot of different areas today so I want to wrap it all up together in one. Can we talk about some key issues or trends that are influencing the entire regulatory environment, including anything to do with EHS, the OSHA, the EPA, and DOT? How can businesses stay informed and be proactive in navigating these complexities?
Okay. So, first part of your question, I’ll just run through the three regulatory agencies we’ve already talked about. So, for the EPA, a lot of the influence, the trends that we’re seeing, with the EPA, everything is affected with them by impact on the land, the water, the air. And it seems like, with the recent regulations, the most impact that we’re seeing is on air enforcement. So, take a look at what you’re emitting out there, take a look at your carbon footprint as well, take a look at everything that you are generating as well too waste water-wise and you can look at it with the naked eye without even having any regulation knowledge. Are we doing the right things here? That’s part of that environmental social governance that’s out there. Make sure you’re doing anything you can to reduce climate change that you’re affecting with your own business.
For OSHA, focuses on heat illness prevention, especially when we get into the mid-summer months, that’s going to be a major focus for them. They’re also taking a look at mental health as much as possible. Are workers being exposed to too much pressure on the job, and are we realizing when there are mental health issues going on with employees and we actually being … Are we empathizing with that, or are we just ignoring that and then that employee is at a higher risk for an injury?
I hate to bring back up the pandemic, but it’s something that’s still, it’s still out there, and so taking a look at infectious diseases, that one caught us a little bit by surprise, of course. However, that threat’s always been out there so how can we be better prepared for something like that in the future? And then workplace violence, that’s another key issue that they’re trying to focus on a little bit more. In fact, we’ve seen some state enforcement going on with that regulation change.
And for the DOT, their main impact or trend is focusing on that distribution warehouse safety. We’ve got so many different 18-wheelers that are out on the roads, a lot of these different box trucks that are delivering packages as well too, and also, now we’re starting to see the influx of autonomous vehicles, ones that are pretty much self-driving. And so, there’s going to have to be some different regulatory enforcement surrounding those because I don’t think we have a whole lot of regulations surrounding robotics and artificial intelligence, and that seems to be an influx into our industry today. We’re going to start to see some more concern over that because now we’re mixing in a robot driver versus a human driver, and how can one really prepare for what the other one is going to do at all times?
So, the key thing is to stay informed. And I think you asked in the second part how can you stay informed. Subscribe to this podcast, of course, if you haven’t already done so. But subscribe to informative newsletters surrounding your particular industry, there’s lots of different publications that are out there, of course. Go to the regulatory agencies, they have newsrooms you can subscribe to there, and feedback as well. Connect with industry leaders on social media platforms like LinkedIn. I think LinkedIn is a great source. You have to be careful about who you’re getting information from, but it’s a business professional community and, therefore, a lot of people are posting different regulations that are coming out from these different regulatory agencies, so we want to make sure that they’re actually getting collected as well.
So, yeah, follow some people on LinkedIn and follow me out there. I post regularly. I post updates constantly on my LinkedIn page about different regulatory updates. So, stay informed as much as you can, and if you have questions, you can always contact KPA or me, and I can get you whatever regulatory information I need to.
[00:29:45]
Thanks, Zach. I think those are all really great tips for how to stay informed and how to be proactive in making sure that you are staying on top of these regulations. I know it can be tough for businesses out there to see all these different bodies, knowing that they’re all coming up with different rules, getting bigger budgets, and going harder on these regulations, but those are some great tips on how to stay up to date. And as we’re wrapping up, we’re getting towards the end of the show here, one thing I always love is the fact that you have a really unique perspective because you are in the field, you’re able to see on a day-to-day basis what these businesses are dealing with. And I think, as much as we can look at safety as something that’s really life-saving, because it is, there are oftentimes when there are lighthearted situations that you run into.
So, I would love to wrap this up with if you could tell us a story about an inspection where you uncovered something funny or something silly happened to do with the inspection just to have a little lighthearted touch at the end. So, give us something, what do you have from an inspection where something went a little bit differently than you expected?
Oh, the funny story question. Gosh, I’ve got funny stories. Might be running out of funny stories, I got to get myself out and back into the field. But I guess, speaking of technology, how we’ve talked about technology throughout all of this, with KPA, as a consultant, I would use technology to complete audits of facilities when I was in the field, and so it would be real-time results. So, as I would complete an inspection, I would identify a hazard, I would take a picture of it, I would log it, and it would sync automatically into our platform.
And so, there was one time I was doing an inspection, and I kept seeing, after I would write something up and walk away, I kept seeing somebody run out there and immediately fix whatever it was, and I just assumed like, “Okay, they see me taking a picture of it, they know that there’s something going on.” But then it started happening with documentation and paperwork as well too which really got a little bit odd at that point. So, I walk into the manager’s office to review the findings of the audit, and his reply back to me was, “Everything’s 100%, you don’t have to worry about anything.” I was like, “What are you talking about?” I was like, “I saw somebody following me and fixing things while they were on their phone. What was that all about?”
And he’s like, “Well, you know how your inspection results come in real-time? I was actually logged in and watching everything that you put on the website, and I immediately had my guy fix it as soon as you were done with it, so I didn’t have to worry about it again.” So, I was like, “You know I still have to talk to you about these things because there was a problem in the first place, but I appreciate you taking care of them immediately, that was always a nice thing.” So, one of the funny things I’ll share, we just had the Stand Down for Safety week, where the whole industry recognizes fall prevention, and trying to mitigate those hazards is still the number one ranked citation out there, most violations out there happen to be with fall protection. So, there were two instances.
One facility I was at, had a landing where they were storing a bunch of extra parts, extra just material that was up there. And so, I was taking a look at it, and I was like, “Well, apparently, employees do get up there from time to time,” and there was no guardrail or anything like that, so I told the manager, I was like, “See that landing up there? That’s definitely over four feet, we’re an industrial setting, you have to have fall protection up there, you got to put a guardrail or something like that.” So, of course, the manager was like, “Are you kidding me? We hardly ever get up there,” and I said, “Nope, nope, you have to do that. If anybody gets up there at any time, you pretty much have to have fall protection for that employee.”
The next time I went in, they had addressed it, but they had a fence up there that they had made. It was all green. Then they had boxes that they had painted and put together to look like cows in a pasture. Then they had a big sign up there that said Zach’s safety pasture. So, because I required them to have fall protection, they had to poke a little fun at me by making their little fun safety pasture up there.
And then, one time around Christmas, I was doing an inspection, and there was an area that I walked by, and I noticed there was a ceiling tile missing, and there were legs sticking out of it, and somebody had taken a Santa Claus decoration and had the Santa legs sticking out of the roof almost like it was coming down the chimney in the facility. So, I ended up writing up the facility for not having Santa have fall protection in the area which everybody got a little bit of a chuckle out of that, but just trying to make sure that everybody’s aware of fall protection, I guess. So, they poke fun at me, I’ll poke fun right back at them.
[00:34:23]
Hey, that’s an important one. We always look at the OSHA Top 10 every year, and fall protection is always in the top five.
Thanks again, Zach. It’s always great to have you on the show and always great to have a mid-year check-in to see how things are going, what to look out for, what regulatory bodies have brewing on the horizon, and what new rules might be coming up, and what that enforcement is going to look like. You’ve done a great job of summarizing everything for our listeners that they should be looking for to keep their workplaces as safe as possible for the rest of 2024 and into 2025. So, Zach, thanks again for joining us today, we really appreciate you.
It’s always a pleasure to be here, Kat. Thank you for having me. And for everybody, stay safe out there and stay well-informed.