Digital Safety as a Resource Multiplier: An Interview with KPA’s Jade Brainard
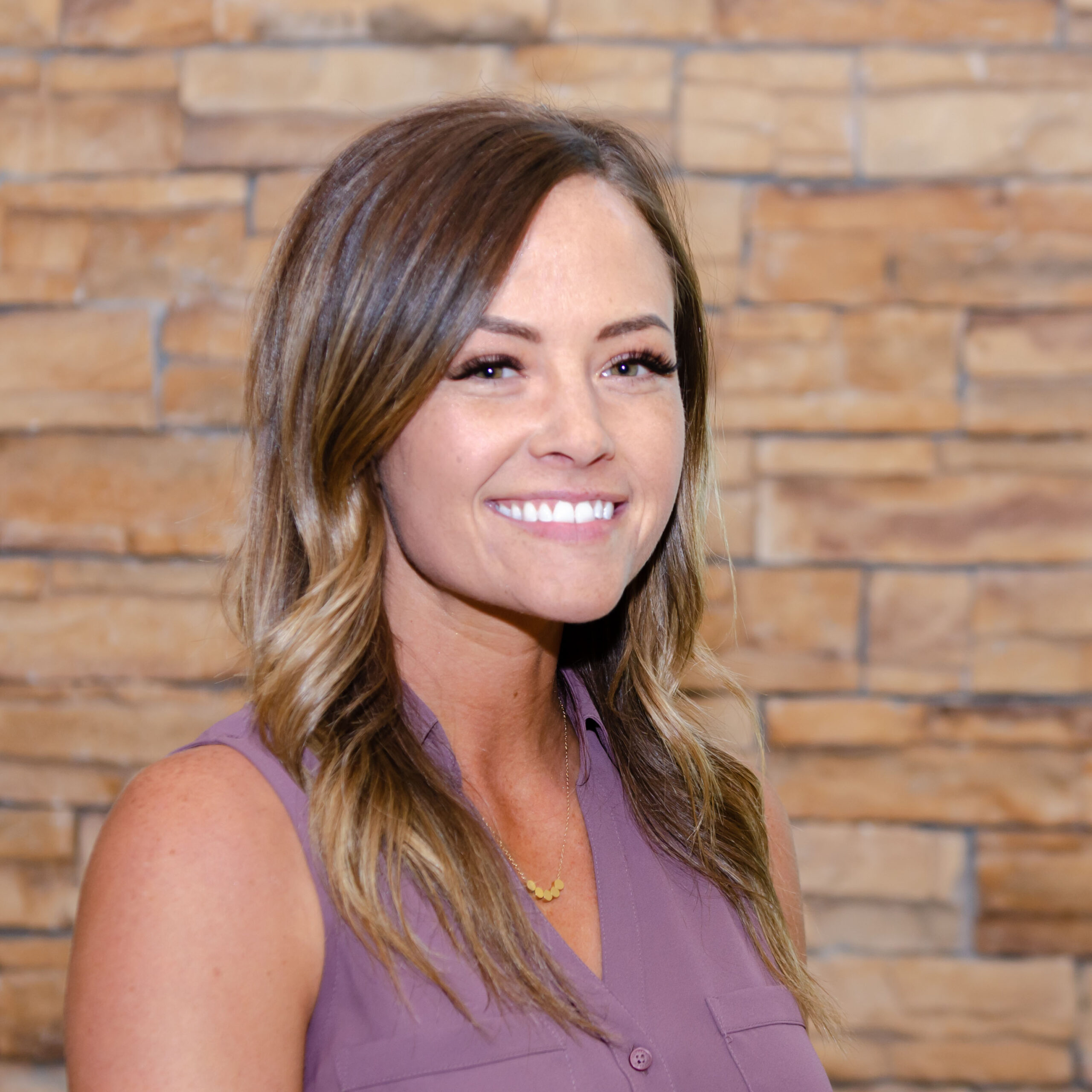
[00:00]
Today, we’ve brought back KPA’s product director, Jade Brainard, to discuss how digital safety positively impacts productivity. Thanks so much for joining us, Jade. We really appreciate you taking the time to talk with us today.
Thank you, it’s great to be here.
[00:35]
Let’s dive in. Health and safety programs are often perceived as something that slows down processes. It can be viewed as a disruptor to production. How can we flip that perception and demonstrate that safety can actually speed things up?
I think that is definitely a perception that still exists, surprisingly. We all know that time is money, and I think that’s the biggest impact digitizing your safety processes can have on productivity. And there are a lot of individual ways that we can measure that, from reducing paperwork to providing real-time data and reporting, supporting our remote workforce, and overall streamlining our compliance process. So having an EHS software system really automates some of that compliance tracking and reporting, ensuring that organizations can adhere to those local, state, and federal regulations and really reduces the time and effort spent on manual compliance tasks.
So we’ll drill into reduced paperwork. For any EHS professional who has introduced a digitized process, the first ROI they recognize is eliminating manual processes and paper-based recordkeeping with digital solutions. Think about audits and inspections. Rather than trying to go and find a clipboard and the right documents to fill out, writing things down by hand, or putting it into an Excel spreadsheet, now we have a systemized process and standardized reporting across workforces. Not only are we not tracking down paper files, but we have a digitized review of the collection effort and then summarizing standardized information at a higher level within the business, so just reducing that paper pushing. And a lot of times those hard copy documents don’t make it to the right hands, and then we can’t identify what data we’re missing, or we can’t standardize the process, so really reducing that paperwork and, that manual process is one of the biggest impacts on introducing a digitized process.
But that real-time data and reporting is where I think productivity is impacted because it allows organizations to not spend weeks trying to summarize manual reports, but they can immediately get access and insights into what’s going on in the business to allow them to make data-driven decisions quickly and identify trends and take those corrective actions.
I certainly need to mention that remote work support, so having a digitized process or an EHS software solution available, allows employees and teams that are working in remote areas or at different locations to quickly and easily access any safety data they need and perform necessary tasks.
So that might be looking up a safety data sheet or reporting a workplace incident, or maybe I need to find a standard policy or program or job hazard analysis. I have all of that information at my fingertips rather than in dispersed areas within the workplace, trying to track down certain binders or documents or get into a corporate SharePoint.
Now everything is in one place, not to mention training, so training allows us to educate and ensure that we’re meeting those training compliance requirements and make sure our workforce is properly trained at all times. Rather than stopping production so we can do in-person training, we can deliver training quickly, effectively, and more often.
So there are a lot of different ways that we can measure productivity improvement, but I think it comes down to having the right information available to our workforce at the right times. And having a software tool and everything in one place really allows for that to happen.
[04:52]
So we’ve talked about the overall productivity savings from having digital health and safety measures in place. Can you talk a bit about how safety technology can actually become a resource multiplier?
So, if you don’t have a system in place, then you’re really relying on those individuals. And those individuals need to be in person. A lot of times, an organization might have one safety professional, and he or she might be managing multiple job sites or multiple locations, and they just can’t be everywhere at all times.
So having a technology tool allows them to duplicate their efforts and reach those workforces simultaneously. So, I’ll go back to the point earlier about safety training. If you don’t have a system in place, then it’s your safety officer’s role to be on-site to offer that training, and if they’re doing that in person, they’re stopping production.
They may have missed employees who weren’t there that day, and then the safety person’s going to have to come back. But if we had a tool in place that allows that safety person to make customizations to training, to deliver that to the workforce remotely, maybe not stop production, maybe have individuals take their safety training one at a time so work can continue and safety training is still getting done.
So I think that’s one great example. But there are a lot of them, from doing audits and inspections to getting more of the workforce involved in the safety program rather than making it the sole role of the safety officer. So that they can spend more time recognizing trends, identifying issues, and really taking proactive approaches to reducing workplace incidents and hazards versus paper-pushing and doing repetitive actions.
[06:51]
That makes a ton of sense. It’s always helpful to learn from what other companies have found successful. Do you have any specific examples of how companies are using safety to speed things up instead of slowing them down?
So many of our customers at KPA have communicated the ROI of their programs and how they’ve recognized success and improvements in productivity, and a lot of that comes down to time savings, but also cost savings that were attributed by digitizing these safety processes. There’s one customer that comes to mind, they’re actually a well-completion company that serves the oil and gas industry.
They shared their story of having to prepare a business case to present to executive leadership to continually get buy-in for the investment required to maintain software year-over-year. So they broke down their ROI calculator into categories such as man-hours spent organizing safety reports, doing data entry, analyzing the data, and facilitating training, as we mentioned before, but also utilizing a system to support their maintenance and repair process.
So they found that not only did digitizing their safety process do what would require an additional two to three full-time employees to do, but also, since they use the software for operational processes, such as being able to submit work orders for maintenance and repairs or ordering parts, it dramatically improved production efficiency.
So they are able to make sure that all teams have the tools and the equipment they need when they need it. They’re not stopping production because they’re missing what’s needed on the job site or missing what’s needed on the manufacturing floor. They can use technology to proactively communicate those things quickly, in a real-time manner, so work can continue.
[08:51]
Your last example covered this a little bit, but to dive further in, are there other ways that companies can show that their safety measures are having a positive impact on the bottom line, knowing that reporting back to other stakeholders in the business is always key?
For sure. It all comes down to measuring the key performance indicators that matter. It’s difficult to demonstrate how time savings can lead to an impact on the bottom line, but EHS software systems make more data available in real time. And that real-time data allows safety teams to quickly recognize areas of risk and exposure before something happens.
And it allows them to take some proactive measures that will lead to incident reduction. And reducing workplace incidents is where we see an impact on bottom-line results. A lot of our KPA customers, and I’m sure many organizations out there, track KPIs such as your TRIR, which is your total recordable incident rate, as well as workers comp claims.
And recognizing year-over-year improvements in cost savings, in reducing your total incident rate, or reducing your workers’ comp claims, that’s where you recognize the cost savings, and that’s where it directly impacts the bottom line. So, even if having the right tools at your fingertips helps your organization avoid just one workplace incident per year, it’s going to pay for itself.
So that’s really where the bottom-line impact happens. Are you seeing a downward trend? Are you seeing a reduction in workplace incidents and workers comp claims? That’s where the time savings lead to dollar savings and a positive impact on production and business results that leadership will recognize.
[10:48]
Jade, thank you again for joining us today and sharing all of this with our listeners.
No problem. Thank you for having me.