What’s the Link Between Safety and Good Housekeeping?
There are plenty of reasons to practice good organizational housekeeping. It ensures business runs smoothly, boosts morale, and creates a positive impression for visitors, just to name a few.
But the primary reason to clean things up—the reason we’re here—is safety. Housekeeping is a crucial part of any environment, health, and safety program. It’s perhaps the most powerful strategy for eliminating the #1 form of workplace accidents: slips, trips, and falls. It also minimizes the spread of illnesses and the possibility of chemical exposure.
You don’t have to take our word for it. Here’s what the Occupational Health and Safety Administration has to say:
“Uncluttered working conditions are essential to the safety of all workers and should be maintained at all times in both work and office areas. Proper housekeeping management provides for an orderly arrangement of operations, tools, equipment, storage facilities, supplies, and waste material. Good housekeeping is evidenced by floors free from grease and oil spillage; properly identified passageways; unobstructed accesses and exits; neat and orderly machinery and equipment; well-nested hoses and cords; properly stored materials; removal of excess waste material or debris from the working area; walkways free from ice and snow; surfaces, including elevated locations, free from accumulated dust; and adequate lighting. Maintaining these conditions contributes significantly to lower incident rates.”
This isn’t just OSHA offering friendly advice. If a state or federal inspector visits your facility and sees a cluttered or dirty working environment, your organization could face serious penalties.
How serious? Recent regulatory actions offer a glimpse. In 2023, Dollar Tree agreed to a 1.35 MILLION DOLLAR settlement after inspectors discovered issues such as blocked emergency exits and improper stacking of merchandise—issues directly related to poor housekeeping.
Safety: the 6th “S”
If you’ve read along with this series so far, you’re familiar with the 5S system—an agile methodology for organizational housekeeping:
1. Sort
2. Set in Order
3. Shine
4. Standardize
5. Sustain
Many companies go a step further and follow a 6S system, with safety as the 6th “S.” The idea behind 6S is to not only prioritize safety as an outcome of the program, but to embed safe practices within housekeeping. In other words, the goal is to create a safer environment and stay safe while doing it.
Here are a few examples of 6S in practice:
Setting up workstations to improve ergonomics so workers aren’t using the same muscles all day and potentially suffering repetitive motion injuries.
Marking intersections to ensure forklift operators won’t collide with each other or pedestrians.
Using signs to label storage cabinets containing cleaning chemicals so that workers are aware of the presence of hazardous substances.
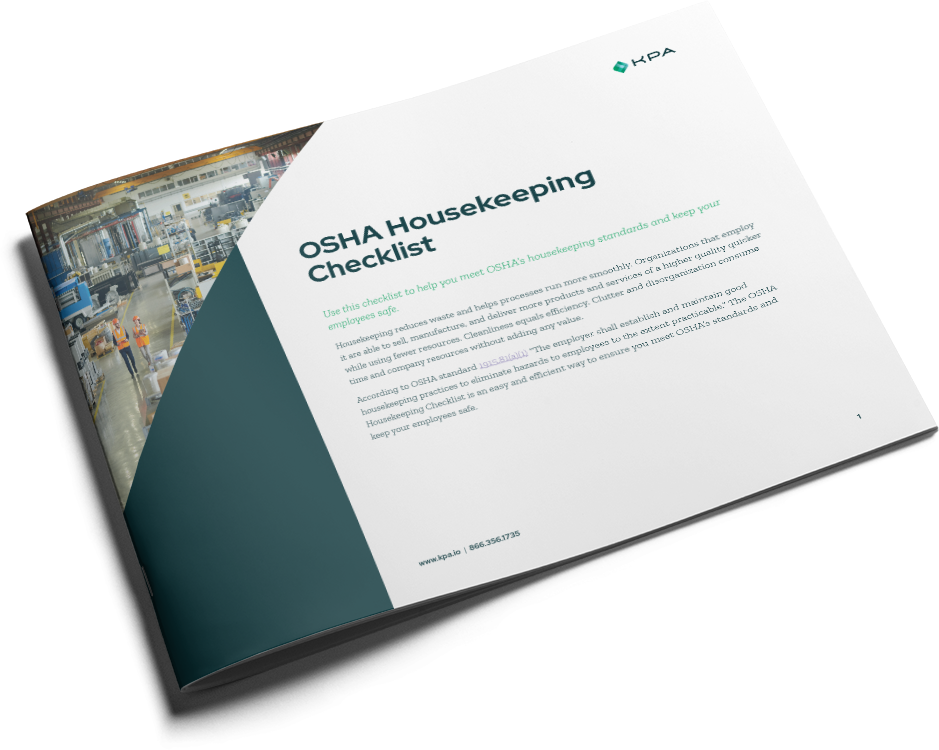
OSHA Housekeeping Checklist
Download KPA's OSHA Housekeeping Checklist to help you identify areas in need of some good housekeeping.
How Poor Housekeeping Affects Safety:
Common Issues to Watch Out For
Start cleaning and improve your organization’s housekeeping. KPA’s workforce safety and compliance team can help—contact us.
Related Content
Explore more comprehensive articles, specialized guides, and insightful interviews selected, offering fresh insights, data-driven analysis, and expert perspectives.