Safety Horizons – Regulations and Compliance in 2024: an Interview with KPA’s Zach Pucillo
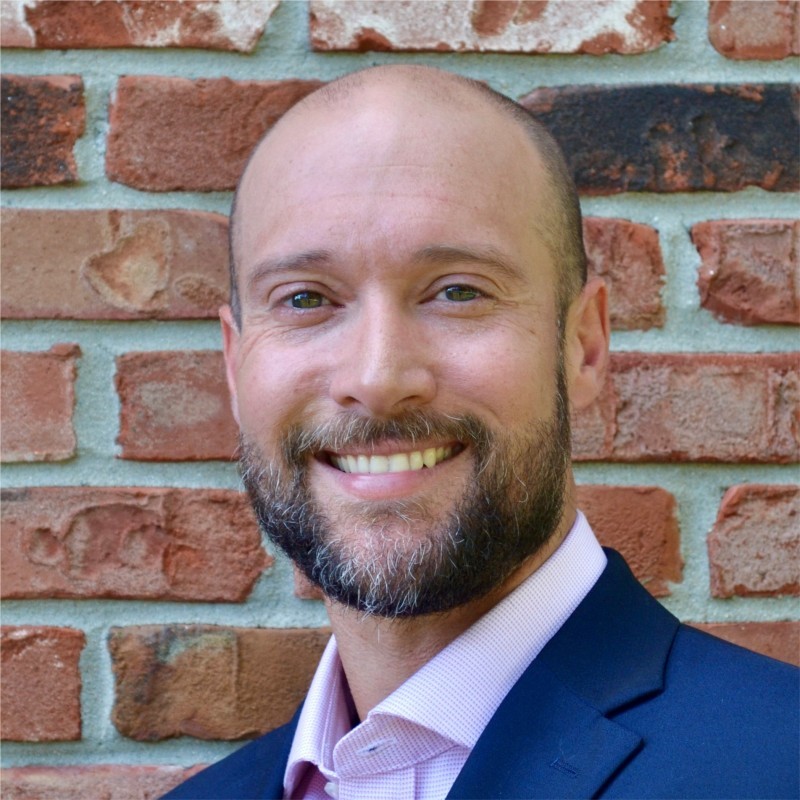
[00:00:43]
So as we dive into 2024, what do you think will change in the rulebook for workplace safety? Any hunches about where things are headed on the regulatory front?
Yes, actually, so OSHA released a fall agenda, and they do this every spring and fall of every year that is out there. And looking at the most previous updates that they had, they had several regulations in the pre-rule phase, which is why we’re still gathering information. Maybe we will actually try to make this a standard, but we need to really evaluate all aspects of it first.
Then there’s also the proposed rule phase, and that is where, okay, we’ve gathered our information, and now we’re actually going to propose some specifics to the rule.
And then finally is the final rule stage, and that is where we have to actually take a vote on getting this passed into the code of federal regulations.
So when I took a look at the most recent update, there were five regulations in the pre-rule phase, and there were two areas that I saw that were highlights. One would be the Heat Illness Prevention Standard, and so OSHA is looking at putting a Heat Illness Prevention Standard in place federally across all states. Several states currently have heat rules in effect for those hot summer days, and ensure that policies go into effect in the workplace, such as providing additional shade, additional breaks, and then a schedule for how to acclimatize yourself back to hot working conditions. So looking at it from an indoor standard and also an outdoor standard.
Then the other highlight that I saw was workplace violence in healthcare. So with that, they’re trying to actually put into place and gather information on what to do for employers that need to respond to workplace violence incidents in the medical industry, the healthcare areas. So the reason I find that one a highlight, is I can see that almost being a precursor that might be coming down the road as far as the rest of industries go, general industry, as well as construction.
Then there are 12 rules in the proposed stage. Some of the highlights there were emergency response, and why that’s there is OSHA has not taken a look at the emergency response standards, probably in the last 30 years. And so there’s been a lot of technology updates. There have been a lot of just generalizations that the industry has made to enhance emergency response and a lot better ways to protect people who need to respond to emergency events. So we’re not just talking about EMS. We’re also talking about standards that could affect your employees if they happen to be on an emergency response team at your organization.
The Lockout/Tagout Standard, once again, we’re taking a look at something that was written several years ago, and there have been technology updates since then. So a lot of different machinery out there is now operated by computer key switches. So if I hit the enter button, it might start up a machinery out there. And so how do we actually adapt the Lockout/Tagout Standard to how technology has really risen in industrial spaces?
Tree care, the reason I wanted to highlight that one is because, yes, there’s an industry for that. However, a lot of places have maintenance teams that go to handle the groundskeeping and maintenance on the property. And so those industries, or those companies, that will actually have maintenance teams that take care of trimming trees on the property, they actually have to keep up with that standard to understand what they need to put in place for their maintenance teams.
Personal protective equipment and construction is just about to that final rule actually, and that is making it so that personal protective equipment is provided to employees of all shapes and sizes that are out there, ensuring that a construction company is just not issuing large safety gloves, vests, and just one particular type of safety glasses. No, it’s got to be something that employees have options to pick from. And so to make sure that those options do fit the employee as well too.0.
And then powered industrial trucks, and anytime they make a change to powered industrial trucks, and the most common truck we’re talking about is forklifts, then we have to take a look at the whole standard because it might require additional training for all forklift users that are out there.
And finally, in the final rule section, there are about seven different rules out there. The two highlights that I took away from the final rules, are that, hey, they’re in place at this point. We’ve got to actually start taking action items to improve our safety standards to get them up to the federal standards. And the first one is revolving around the Hazard Communication Standard. So hazard communication, we got on board with the globally harmonized system when it first came out, and that was about 2011, 2012. And so that is an evolving standard, the global harmonization system. They continually update that. And so we’re just updating to the current level of that globally harmonized system, and it’s going to evolve a little bit when it comes to labeling of chemicals that are really small bottles. I mean, how do you put all that information on a tiny little 10 milliliter bottle? You can’t. Then also a little bit about aerosols and making sure there are different classifications.
Then the last one I wanted to highlight here before we move on is the electronic submission of injury illnesses. So there’s the record-keeping rules, which I’m just breaking it down. It’s the OSHA 300 forms, the OSHA 300, the 300A, and the 301. That’s where we log all injuries that have happened throughout the calendar year, and organizations have to record those on logs. However, as of a few years ago, electronic submission of that data was now required. You had to actually submit that data to an OSHA website.
And so there’s been a little bit of change to that that’s going into effect in 2024, and that is going to be, so if you’re less than 20 employees, you do not have to report anything electronically. If you have over 20 employees, and your North American Industrial Classification System code, your NAICS code, the four-digit code that every industry gets assigned, if your number shows up on Appendix A in the regulation, you have to submit the information from your 300A electronically. If you have over a hundred employees, and your code shows up on Appendix B, then you have to submit the information from your 301 forms, your 300, and your 300A. And then finally, if you have over 250 employees, you have to submit the 300A information. And those are all due by March 2nd of each calendar year.
So lots of activity going on, lots of things getting to the final rules as we kind of move throughout the different years.
[00:07:16]
That is some great insight on what’s coming up for sure. And I know that understanding these regulatory changes and knowing when these deadlines are coming up is important. And you kind of tackled this a little bit in the question you’ve already answered, but do you have any insider scoop on what OSHA might have up their sleeves, specifically this year? Are they eyeing any industries in particular, or are there any safety issues that they’re looking to tackle?
Yeah, so they have emphasis programs out there that they’ve actually put into place, and that gives us an insight into what industries are really trying to tackle. And so fall protection is one of the emphasis programs that is still going on. And fall protection, let’s face it, we haven’t gotten that right, unfortunately. It’s the number one most cited regulation out there, and it occurs it’s number one every year for the past 10, to 15 years. We’ve got construction activities, roofing activities, even in general industry where we have people going up on roofs that are at elevations of four feet or higher and six feet or higher, and that’s where we have significant injuries happen.
And so as we take a look at that, OSHA is also taking a look at that, and they want to try to get more in control of that, so they created an emphasis program on that. And so if I am a compliance officer, I’m driving down the road, maybe going to lunch, and I see construction activities where there’s a person up on a roof, no harness, working right next to a leading edge where they could fall, then I’m going to probably pull over and conduct an investigation at that point. They have the power to do so.
Another industry, really, is the warehousing industry. I don’t know about you, but electronic shopping is a great thing. You’ve got your different online retailers, Amazon, and Walmart, and it’s very convenient for the consumer. However, there has to be somewhere behind the scenes where all that product sits, and it has to be moved out in a very timely fashion to try to make these consumers happy. What does that mean? Warehousing and distribution. Those warehouses are popping up all over the place.
I live in the Midwest, and I think in the past few years, we’ve had probably about 20 to 30 large warehouses pop up around where I live. And of course, those can become chaotic places because they operate on a 24/7 type of operation. They have constantly people moving around, order pickers, and machinery going around. We’ve got forklifts powering around those facilities. And so they are very much primed for injuries to happen to employees, and therefore, these warehouses, these different companies have to make sure that they are keeping up on their toes because OSHA created an emphasis program around inspecting warehouse distribution centers. So they’re really targeting those two areas.
And then one thing that’s coming down the pipeline that I think, from an OSHA standpoint, I haven’t heard any rumblings on a federal level yet except for in the healthcare industry, but there’s a particular state in California that just passed a new law that is requiring workplace violence standards for all businesses. And so in California, if you have over 10 employees, you really need to pay attention to, I believe it’s Senate Bill 553, and that is the workplace violence standard. It’s going to require their employers to develop a written program, conduct annual training, and then log any incidents that surround workplace violence.
And they’ve come up with a few definitions in there. There are four different types of workplace violence that are out there. Honestly, I’m thinking to myself as I’m reading this, wow, there’s a lot here, but man, this is probably long overdue for workplaces because we’re seeing an escalation and spike when it comes to workplace violence incidents. And that could be anything from just more of your on-site violence between two employees or customers getting angry and acting out all the way up to the active shooter situations, which is very unfortunate. But it’s on the workplaces, I think, to really put together some plans to try to be preventative in those situations and de-escalate those situations. So I see OSHA probably taking a look at what California’s doing with that and maybe keeping a close eye. And it wouldn’t surprise me if we see something proposed down the road as far as a federal workplace violence safety standard.
[00:11:34]
Got it. Yeah, those definitely make sense. They’re not ones that I had heard of, but with the climate that we’re in, I think they are definitely going to be high on the list of priorities for OSHA.
I know OSHA is a big facet of regulation for our listeners, but there have been other regulatory bodies that have been coming up and getting more into fines and checking out these businesses. So besides OSHA, are there any other sheriffs in town that our listeners should be keeping an eye on or any fresh rules that might be popping up? Anything else they might need to watch out for this year?
Yes, so you’ve got the Environmental Protection Agency. Usually, when it comes to environmental health and safety, we’re talking mostly about safety, but we can’t forget about the environmental side. We have that EPA out there that makes regulations. And one thing that’s on their agenda, actually, is trying to control the release of hazardous substances a little bit more.
So there’s the Clean Water Act, and it was probably about 20 years ago, they had an amendment to the Clean Water Act where we don’t want petroleum-based products getting into the water. And so they created what we would refer to as the SPCC rules, and that’s Spill Prevention Control and Countermeasures. And if you were to store so much oil on your property, you would have to develop a plan that would basically be like, what are we going to do in case there’s a spill? How are we going to respond to that spill? What do we need to do for cleanup efforts as well?
So that was all petroleum-based product, but on the new agenda that they’ve had, now they’re taking a look at really going at all hazardous substances. So we don’t know any threshold amounts yet. They’re still in this proposed rules phase, so they’re still gathering information, but I believe they’ll probably make a threshold limit out there. And if you store so many hazardous materials on your property in a liquid form, you’re going to have to have a prevention plan showing this is how we maintain our chemicals to make sure that they don’t get released. If they do happen to be released, this is how we go about containing them and cleaning them up so they don’t reach waterways. So we’re keeping an eye on that one, very early in that phase.
Something that’s a little bit more down the road is what I refer to as PFAS, I’m going to do my best here, and that is per- and polyfluoroalkyl substances.
So these are what we’re calling forever chemicals, and they’re making regulations right now to really eliminate or reduce the amount of these forever chemicals that are produced. And these are the type of chemicals you would put on that makes things water-resistant, so different waxes, food packaging, different containers to make sure that the food doesn’t stick to the actual wrapper, wetsuit type of material to make sure that people are going surfing or something like that. It’s water-repellent, more than anything else.
So the chemicals are usually used for those types of products. And the problem with them is that they don’t break down. They don’t go away. That’s why we’re calling them forever chemicals. I should rephrase. They do break down, but they break down into microbial amounts. And so those go out into the environment, and we can’t see them, we can’t smell them, and they’re landing in different areas out there in the environment, the grass, the water. Well, what happens when it goes into the water? And the same with the grass. Well, we have animals that eat that, and then we, in turn, eat the animals, some of us do, and it’s bioaccumulation at that point.
And so we’re starting to see these PFAS, or forever chemicals, actually accumulate more in human bodies, and it’s actually now leading to different types of cancers becoming a little bit more predominant out there. And so we want to avoid that as much as possible, and we want to eliminate that. So if you happen to be a manufacturer of those forever chemicals or use them, you might want to pay attention to what the EPA is trying to regulate when it comes to those.
And then one final thing that’s not the EPA, it’s actually a different one. It’s the FAA or the Federal Airline Administration. And the reason I bring this up is because, with technology that’s being updated out there, I’m seeing more and more use of drones in the workplace. I’m seeing them just in chemical manufacturing plants where maybe they’re trying to get a read on emissions, or they’re trying to get an overview map of the whole plant operations. I’m seeing it in the roofing industry. And so if you are using a drone, you have to make sure that it is registered with the FAA.
There are exemptions. If you only use it recreationally, and it’s less than, I believe it’s half a pound, then there’s an exemption from that rule. But if you use a drone for any type of work practice, and it’s over half of a pound, you do have to register that with the FAA. So that was something they came out within the past year, and I thought it was interesting. I just want to make sure people are aware of that.
[00:16:21]
Yeah, that is interesting. And it seems like the EPA and FAA have been coming up a lot more in safety news in the past year or so. And clearly, speaking of drones, it has something to do with technology and the way that technology is sort of changing the space. So with tech doing its fast and furious thing, how do you think that’s going to impact workplace safety, especially with all these potential new rules to follow?
Well, it’s good, actually, tech is making our lives so much easier in so many different ways. My thing is we just have to be careful about certain ways that tech is getting used. And what do I mean by that? It’s probably about artificial intelligence that’s out there. We have to be careful about how that’s actually being used in the workplace. A lot of people are going to use that. In the safety world, I’ve even seen applications where artificial intelligence is starting to catch people on camera for not wearing personal protective equipment, and all of a sudden it sends a screenshot to a manager. And at that point, that manager can make their decision on what they want to do there.
But at what point are we going over the line with being too cautious as well with artificial intelligence? Are we using artificial intelligence to write our safety programs? We shouldn’t be doing that because these should all be site-specific, and we should actually know the information in our programs ourselves. A lot of people would use them to write workplace policies as well. Once again, should not be using that approach because you need to have site-specific information in there. You should know how your policy operates, and you should be able to easily communicate those items to your employees. We shouldn’t be just putting things together that we’re going to sit on a shelf. These things should actually be used.
But there are also great things out there as well. Apps, mobile applications, safety world is getting more and more of those that are out there. There’s a great one, I believe it’s Fall Protection Hero. It’s actually a game. And so if you’re in the construction industry, I would probably have all of my employees download that and use it if they’re going to be doing any type of elevated platform work. And that is, it’s a little stick figure, and you design a fall protection system for them. And then at the end, if you push them off the ledge by flicking your finger on the person, and if you designed it right, you saved their life. If you designed it wrong, well, you could probably think what happens there.
But there are also virtual learning environments I’m also seeing in the safety world. And so we learn so much by seeing. We only learn so much by hearing how to perform the operation. You learn the best from actually doing it, hands-on experience. And so for our younger generation that’s joining the workforce, I mean, they went through a pandemic. They are addicted to technology with phones, applications, and video games. Why not use that to your advantage? Make a virtual learning experience for them. There are lots of different companies out there that can help out with that, and they can actually use some of the virtual learning environments that have already been out there. And so you can actually kind of scale your work environment and give them a task to do, and they can perform that task in the virtual environment, and hopefully, they’re doing it safely. And if they’re not, then you can have definitely a coaching experience right there with them at that moment where nobody got hurt.
[00:19:25]
It truly amazes me what we can accomplish these days in the safety sphere.
Oh yeah, for sure. I mean, there are other things that are coming out there. In fact, with KPA, microtraining is something that we’re taking a look at as well. We’re trying to cater to shorter attention spans. We’re in a high-production world out there, but if we can get great content over to the user in the span of a training course that’s maybe just a couple of minutes long, then why not take that approach, and why not push that out there to our clientele?
We have mobile applications as well too that we’re actually empowering our clients with. We have platforms that can make our client experience so flexible out there like, “Hey, you want it to do this? Yes, it can do that.” Don’t just try to think of safety as a platform where you get harnessed into, we want it to do this. No, it can’t do that. I’m sorry. No, it can’t do that. We have KPA Flex, which is very flexible, and more often times than not, when we get asked a certain thing like, “Hey, can your software do this?” Yes, you just have to set it up that way, which is great.
[00:20:23]
Incredible. And I know that because tech is growing in ubiquity, it’s always going to have some influence on what’s happening in safety worldwide. And being an expert and working in this field must give you a lot of good insight into how these things can affect a company’s day-to-day safety. So can you share any recent success stories in safety compliance, adoption, or perhaps a cautionary tale that highlights the importance of staying updated with these regulations?
I’ll do two. So I’ve got one on one side of the spectrum and one that kind of teeters on both. So when it comes to a success story, we were working with a client actually, and I’m not going to share the client’s name or anything like that, but we actually came on site with KPA services with them. They were in dire need of help because, with their insurance company, they were spending a lot of money due to a couple of accidents that they had in the past. And so we came in, we set up a good inspection routine, gave them the tools that they needed to help them develop their programs, but not necessarily the programs or processes is what we really took a look at. We were looking at processes that were very dangerous because they weren’t well thought out. We had people who were making travel distances with products that were absolutely not necessary where they were actually carrying it by hand when we should have been using forklift amounts at that point. We had cases where we were using electrical wiring that was supposed to be for temporary use where it was like, no, we need to actually put in hardwired amounts here so that we’re not exposing the employees to trip hazards all over the place, but also electrical hazards at the same time.
So I mean we could go down that list, but for the sake of time, I’ll say that after about three years of working with the client, they took their experience modification rating, which is a rating that is given by their insurance company, and we went from a 1.03 down to a 0.95, which is excellent because what that experience modification rating is, one is usually that standard. Anybody above a one was paying higher on their premiums. Anybody below a one was paying less premiums than some of their competitors were. So by going in and helping them look at their processes, conducting inspections, and training their employees, we were actually able to help the company save money with their insurance program. And plus they threw in a discount once they learned about the services that we were offering as well too, which is excellent. It actually was the cherry on top for us.
And then a different story was, so this is a personal one from in the field, and it shows kind of the success of safety. But wait a minute, as we take a look at it, the root cause here was an ultimate problem that we have to figure out. So I was working at a facility. We were on a plant floor and there was an area where maintenance was going on, and they were working on basically an engine, if you will. And what they were doing was they were torching to try to get some nuts and bolts loose that had been seized on the actual engine.
And so as I walked by the area, things seemed to be looking okay. I moved up to the front of the facility, and I was talking with a different manager, and all of a sudden, that employee that was doing the welding came running by as fast as possible, yelling fire, running back with the fire extinguisher. I, of course, run out there. I see him using the extinguisher. He is putting out some flames.
Well, what had happened was that while he was welding, a rogue spark flew away and got into a drain, and apparently there was something flammable in that drain because a wall of fire shot up through the drain. The employee, of course, shocked, dropped what he was doing, ran to the front, grabbed a fire extinguisher, and ran back to put out the fire.
Now sounds great, right? Success story. We got the fire put out, with little damage. However, as we took a look at and investigated it, the employee went and grabbed a fire extinguisher from up by where we were standing at that he knew that fire extinguisher was there, but he didn’t realize there was a fire extinguisher that was about five feet away from him that he could have grabbed much quicker and put that fire out much faster.
Also, somebody had apparently the spill that had a flammable liquid go into the drain at some point. And so that flammable liquid being in the drain, nobody reported it. And now, we have contamination that was actually in the drain that led to a fire. So not only do we have a fire, we have now a hazardous waste that we have to manage that we typically don’t manage because it’s usually just water that’s in that area.
So even though the employee did the right thing, oh, also while he was welding, he didn’t have the right curtain set up as well, which is what caused the spark to go flying off and going into the drain. So even though he put the fire out, we still had three different cases there where we could have probably prevented it or something has gone worse here, and we need to actually take a look at it.
So I guess the moral of the story is, yes, celebrate the successes that you have when responding to an incident, but that incident happened for a reason. And so you really got to investigate what was the root cause of why we had a fire or somebody got hurt. Did we leave a pile of rags sitting out that should have been in a bucket? Was the person not trained well enough? Did we not have the right type of equipment on hand? Let’s not blame the employee. That’s on us for putting the employee in that situation and not monitoring their efforts. So you have to think about safety incidences from all areas, step back, take a look at it as a crime scene and really go into an investigation.
[00:25:45]
Thanks for sharing those anecdotes. I mean, it definitely makes sense that while things went well, there are always ways that we can improve until we’re hopefully avoiding these things to 100%. It’s a little bit of a pie-in-the-sky sort of aspiration, but I think what we’re all hoping for is that we can get to a place where everybody who’s working somewhere knows exactly what to do in these scenarios to prevent these things from happening in the first place. So as we continue through this new year, what are some smart moves that companies can make right now to keep workplaces safe, considering what all these new rules might be?
Make this your safety year. Be proactive, not reactive. So many companies are reactive, just like this situation I just described. We had to react to a situation that could have been prevented in the first place. And so what I say is be proactive. Actually, sit down and take a look at your whole safety program as a management team. What can you do to improve upon that? Do you have programs that are just binders of paper sitting on a shelf? Is your training just somebody reading through a manual? No, that’s not a safety program at all then.
So take a look at what you can do to be proactive. Maybe you need a little bit more help. Take a look at a company like KPA. We come in. We help out by providing processes, programs that are customized to your facility, all the resources and tools that a company needs to be safe. We have the right platform for you. We help you out with your training, and we customize that training to specifically what the employees are doing in the workplace. We work with the management team by walking through the shops and taking a look for any type of hazards that are out there as well.
And then going along with that, get other eyes on your operation, have some kind of consultant walk in, somebody that’s been experienced with safety in the past, safety and environmental regulations. You walk by, probably, the same things every day in your home, and at your workplace, and probably think nothing of them, just like the guy who probably walked by that fire extinguisher that was five feet away from him every day and never realized it was there. We never realized some of these hazards are there because we walk by them every day, and they just camouflage themselves away from us. There might be something like an extension cord lying out across the floor. A third set of eyes is going to probably pick up on that very quickly, whereas you may have a story behind why that needs to be there, but ultimately, does it really need to be there? Probably not.
And then I would also say, as you’re looking at regulations, a lot of companies will try to look at loopholes as well too. Hey, what can we do to not have to comply with this? Let’s just say that we have this number of employees so that we’re exempt from this, or no, we’re going to classify ourselves as this industry to be exempt from this type of regulation. If you’re doing that, stop doing that. There’s a motto, I think, that’s in the automotive industry that is called fix it right the first time. You don’t want customers coming back to you complaining about how the repair wasn’t done the proper way. Same thing with safety. Only you’re going to have hurt employees coming back along with their attorneys coming back and saying, “You didn’t do this right the first time. That’s why this employee got hurt.” And now not only are you going to suffer from it morally and consciously with an employee being hurt, but also financially potentially. So don’t look for the loopholes. Look at the intention of the regulation. Try to make sure that you’re following what that intention is.
[00:29:02]
I think those are also some really great insights to continue with this new year on the right foot. So before we close out, is there anything else you’d like to share with the listeners?
Just make this year your year about safety. Don’t pass it off to somebody else. Come together as a team. Take a look at your entire program and look for ways to improve. Everybody can always improve in one area or another, so try to sit down as a team and to identify that. Make it your year to try to make a safe workplace with zero losses.
[00:29:33]
Fantastic. Well, it was a great time to talk about the start of the new year, what to look out for, regulatory bodies on the horizon, and what new rules might be on the horizon. And I think you’ve done a great job of summing everything up that our listeners should be looking into to keep their workplaces as safe as possible in 2024. So Zach, thank you so much for joining us today. We really appreciate it.
Thank you very much for having me. It’s always a pleasure doing these podcasts with you.