Strategies for Finishing Your Year Strong: An Interview with KPA’s Amanda Rawls
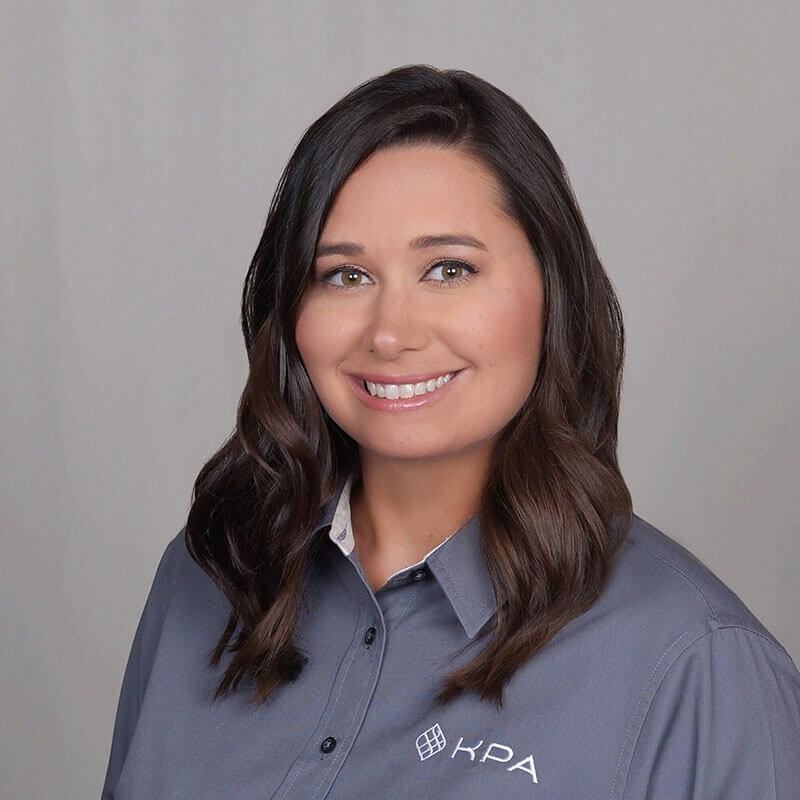
[00:00:17]
Today we’re joined by KPA’s District Manager for the South Central District, Amanda Rawls, to talk about ways safety professionals can ensure a strong finish for their year. Thanks so much for joining us, Amanda. We really appreciate you taking the time to talk with us today.
Yeah, happy to be here.
[00:00:36]
So let’s dive in. It’s a little hard to believe, but we’re getting down to the end of the year. What should safety professionals have in mind to make sure that they have a strong finish to the year?
Well, it’s fall. We’ve made it past the summer months, so this time of year can be pivotal for a successful safety program. I feel like once October starts, you just get the feeling that the year is already over. Holidays are coming up. A lot of PTO can be taken by employees and managers. Schedules change. You kind of feel like you’re just finishing out the year, and there’s no time for new projects. Everyone’s just trying to finish what they’ve already started, so it’s a challenge to come up with a big initiative towards the end of the year. Which does make fall a great time of year to start looking back and also looking forward.
So, what really worked for your facility this year? What was successful, and kind of more importantly, what wasn’t successful? If you’re wondering if your program or initiatives were successful, there are a couple of ways to do that. I think first you have to be honest with your answer. Your self-assessment probably isn’t all that off if you are gauging if something was a win or a loss. But if you aren’t sure, just ask someone. You can do this with a more casual conversation or by creating an anonymous safety survey to gather more feedback.
Another way to look back at the year is by reviewing any regulatory enforcement and how you’ve handled that situation. So was OSHA on site? The EPA? A state inspector? If they were, how did it go for you? Were you able to gather the requested documents easily? Could you answer their questions in a reasonable amount of time? Did you feel prepared? And did any citations result from an inspection?
So, that’s more of like a look back for 2023, and I think to finish the year strong, it’s important for safety professionals to have a few things on their to-do list before the end of the year. The first one is to take a look back at accident trends for the year so far. You should have a list of injuries that have happened this year already, so you can use this data to focus your time and your safety goals. These accident trends also make great content for your upcoming safety committee meetings.
When looking at your injuries for the year, what are you seeing? Are there trends and patterns? Are injuries from the same department? How severe were the injuries? You’ll also want to evaluate the cost of the injury versus the frequency and severity of what happened. One accident that led to surgery and time away from work can also impact your X-modification rate with your workers’ compensation carrier.
The other thing you want to make sure that you’re doing is updating your OSHA 300 log. For most industries, severe injuries must be recorded on that OSHA 300 log throughout the year. So, at the start of 2024, you’ll need to complete that OSHA 300A form, which will require the log data from 2023. So it’s a good idea to ensure that your OSHA 300 log is up to date throughout 2023, but definitely before the end of the year.
Another calendar item is to assess your training completion. So training. It’s so easy and it’s so hard. It’s easy to complete if you do it one topic at a time, but it can be hard to manage for just a handful of employees. So take a look and see if your employees are managing this well. This is important because if OSHA is on site, they always ask for training. Always. And it’s a black-and-white thing. You either have the training done or you don’t. There’s really just not any in-between. So have your employees completed it? And if not, what has the challenge been in getting this done?
Lastly, I think fall is just the time of year to look at next year’s budget and how you can make a case for any necessary requests. It’s important for you to find out when these budget meetings are happening so you can prepare. You’ve had enough time this year to gather some good data points. Hopefully, you’ve had some year-to-year statistics to help back up your requests. So how much is safety costing you? It’s important in these budget meetings to reinforce that these aren’t just dollars spent but it’s an investment in your people and your safety culture. Easy budget requests could be replacing broken emergency equipment, rethinking how to restock your first aid kits, or replacing some personal protective equipment for employees.
But there will be some larger budget requests that should be considered. And that could be an investment in technology. Too many safety professionals still rely on spreadsheets and emails to manage data and spread a safety message. Wouldn’t it be easier if there was software to help you do that? Even better if it’s software with an app that employees can use, too. Paper-based systems are just not an ideal way to manage your safety programs in this day and age. EHS software can provide tools to manage your chemical inventory, track your audits, Track your injuries, and even merge the data you’ve gathered into required OSHA forms.
The best kind of technology will help you manage your employee training at a glance. You’ll know exactly what’s lacking and what needs to be targeted, and also supply some real-time reports that can be shared with other managers. So wouldn’t it be nice if your job wasn’t just to gather all the data points but just look at them and react with decisions? If your facility does not have any safety software, then I would strongly recommend that you investigate what your options are and what would work best for your team. At this point, everyone has a cell phone, and most people have access to a computer, so access to software is there, it’s just utilizing it the best way you can for your team.
[00:05:59]
So, the quick recap for Q4 is to review any accident or incident trends, check on your training completion, and consider safety needs as you’re working on next year’s budget. It seems like looking at the technology component is key because it could probably help with all of those other suggestions.
Definitely. It’s just in this day and age, there are so many people who aren’t using technology the best way that they can, and they forget that this also applies to the safety world in our industry as well. There are lots of cool tools and resources, so I just encourage everyone to explore what’s out there.
[00:06:34]
So you have years of experience helping organizations, large and small, create safe workplaces. What are some common things safety professionals tend to overlook or that fall off their radar?
The first one is housekeeping. It sounds so generic, but it really is the foundation of a great safety program. Are people paying attention to hazards within their immediate workspace? If they aren’t, housekeeping issues are going to build up. And when things aren’t tidy, it can create slip and trip hazards. It also isn’t a good look. Both good housekeeping and poor housekeeping spread. If it gets out of control, it’s hard to wrangle it back in. Nobody likes working in a dirty place, and no one wants to waste their time searching for equipment they can’t find because nothing has a home. Having an organized shop is really important to the morale of your employees and the first step in taking some responsibility and pride in where people work.
Another one that people can forget is paperwork. So just stay on top of it as best you can. If paperwork lives in a box or it’s just a digital file and nobody ever looks at it, then we’re going to forget about it. A good example could be waste receipts. Are those receipts actually getting filed on-site? How often is your waste getting picked up? And do you have a receipt to match each of those pickups? And if that waste is hazardous waste, are your manifests matched? Paperwork is just really easy to lose track of if we don’t have a process to manage it.
Another item that tends to get overlooked is the frequent inspections that need to happen on-site. If you have a forklift, Daily inspections are required. If you have an SPCC plan, then tank inspections are going to be needed. If you store hazardous waste on-site, then weekly inspections for waste containers are required. There are just so many inspections for different things and different places, so I know it can get lost in your daily grind. But you’ll need to stay on top of them because this is part of the paperwork that regulators will be asking about.
My last nugget for what can get overlooked is training. I’m just going to mention it again because it’s just that important. It’s ongoing. Sometimes we tend to just have a big emphasis on a particular topic with our employees and after you’ve talked about it for so long, we’re tired of talking about it. Then training can only be addressed in cycles. Regulators will ask about training, so just don’t let this one get away from you and how you manage this process.
[00:09:01]
So housekeeping, paperwork, frequent inspections, and training. All things to keep an eye on.
They’re going to happen throughout the year, even as we inch towards 2024.
[00:09:11]
Knowing there are all of these things to pay attention to, do you have any suggestions for how safety professionals can keep these on their radar?
Yeah, I’ve got a few of them. I think for inspections, just creating a recurring task in your Outlook or Google Calendar is just an easy thing to do. You can set this up for yourself or other managers. You can add a task to inspect emergency equipment like your fire extinguishers. Then all you gotta do is just set that reoccurrence to monthly and then share that calendar invite with other people if they’re also in charge of the inspections. Just having reminders built into your calendar is an easy way not to forget to complete the task.
And I’ll say it again, but I just think EHS software is an easy solution to help safety professionals manage the required training for employees. Most software training content can be available in multiple languages, which is helpful for people to understand what they’re learning. That software can provide reports to you at a glance and also send notifications out for expired training to both employees and their managers.
And as for housekeeping, I know it was the first one that I mentioned, but there’s just not a really easy solution for this. You just gotta stay on top of it. And I feel like this is where a positive safety program can really have an effect. Rewarding employees for clean and tidy spaces may change how others are going to organize their space and hopefully follow suit. I also have shops that close business early about once a month, that way, they can just do a shop cleanout. So this gives employees some paid time to get rid of just unneeded items. You really don’t need 50 cans of the same product. So, managers really do need to make cleaning out people’s spaces an easy thing to do.
[00:10:55]
Love it. Really practical tips, thanks for those. Now, shifting gears a bit, do you have any notable anecdotes or safety stories to share?
I do… it is one that happened recently that does address a few of the things that we talked about today. So, I have one, of an employee who used a hand power tool incorrectly. So, this one happened pretty recently with one of my clients. An employee was working at a car dealership and brought his own power hand tool, a die grinder. He used the original grinder wheel while working on site, and eventually, that one’s gonna get used up. So, he needed a new wheel at that point. So what he did was just walk into his employer’s tool room and grab a new grinder wheel.
The problem was, is that he didn’t check the spindle speed for the new grinder wheel against the tool that he brought in from home, and since he brought in his grinder from home, it just didn’t have the necessary safety guarding that was installed with it as well. Yeah, I know. You can see where this is going. So the employee was using the die grinder and he’s cutting and grinding, and guess what? The wheel comes apart. And when that happens, it starts to shoot back those pieces of the wheel toward the technician because the safety guard wasn’t in place.
Those pieces hit him in the face and chest, causing some bruising, and it knocked out a few teeth as well. So, it wasn’t pretty. The technician wasn’t wearing a face shield, which is part of why the injury was so severe.
On this day, the tech brought a tool from home into the shop. He didn’t think it’d be a big deal, but it was. Because he was hospitalized, OSHA was notified of the severe injury and they came on site to investigate. They asked for the PPE hazard assessment, which is some of the paperwork that we talked about. They asked for training records regarding PPE, something else that I mentioned already as well. This location was cited for a few OSHA standards, including no guarding on the tool, not wearing appropriate PPE, no training, and for the hazard assessment being inaccurate.
So just some of the items that we talked about today did lead to citations for the facility, and that’s exactly what we’re trying to avoid.
[00:13:05]
Well, that’s certainly a cautionary tale that pretty much brings us full circle on why all of these things matter. Before we close, do you have any final thoughts you’d like to share with our listeners?
Yeah, it’s okay to be honest with an assessment of your safety program. You know, we all have great goals at the start of the year. Maybe you’ve had a chance to accomplish most of them. Maybe you know that there’s room for improvement.
I feel like we can realize those little things about how we’re doing, and this is the time of year when we can really make a difference for next year. So, I just don’t want anyone feeling less motivated that it didn’t get done or that it can’t get done because there’s still time to do it. There’s still time to finish out some of the goals and initiatives from this year, and we’re still well ahead of the game for 2024.
So, I think paying attention to what’s happened this year, making changes where you can. If you get to be a part of those budget conversations, that really can make a huge leap in where your safety program can go in the future.
[00:14:04]
That’s a perfect positive note to close things out. Thanks so much for joining us today, Amanda, and sharing all of this with our listeners.
My pleasure.