What leading indicators are you tracking? Here’s what KPA customers said.
In May, OSHA issued a letter asking for comments from organizations about the effectiveness of leading indicators on impacting health and safety programs. The agency is looking to create a new Leading Indicators Resource tool and is looking for best practices. This is a great excuse for us to take another look and ask our customers how they use leading indicators to improve their EHS programs.
Let’s take a quick review of how to develop leading indicators and take a look at the different ways to identify leading indicators.
6 Steps for Using Leading Indicators
- Plan by choosing the leading indicator.
- Set a goal for the indicator.
- Communicate with your crews and teams about the indicator, goal, and how you’ll track it. Explain why you’ve chosen this particular leading indicator.
- Start using your leading indicators by collecting data, measuring progress towards your goal, creating an action plan if you need to meet it, and then communicating your progress with your crews.
- Assess or reassess your goal and indicator. Sometimes indicators and goals can take a while to collect enough data, so be sure to review things regularly.
- Respond to your key learnings, share them with the relevant teams, and change things based on what you learn.
Looking for more guidance or information? We leaned heavily on this OSHA document; you might like it too.
What leading indicators are you tracking? Here’s what KPA customers mentioned.
We put the question out to our KPA Connect community members. And as always, they had some great advice.
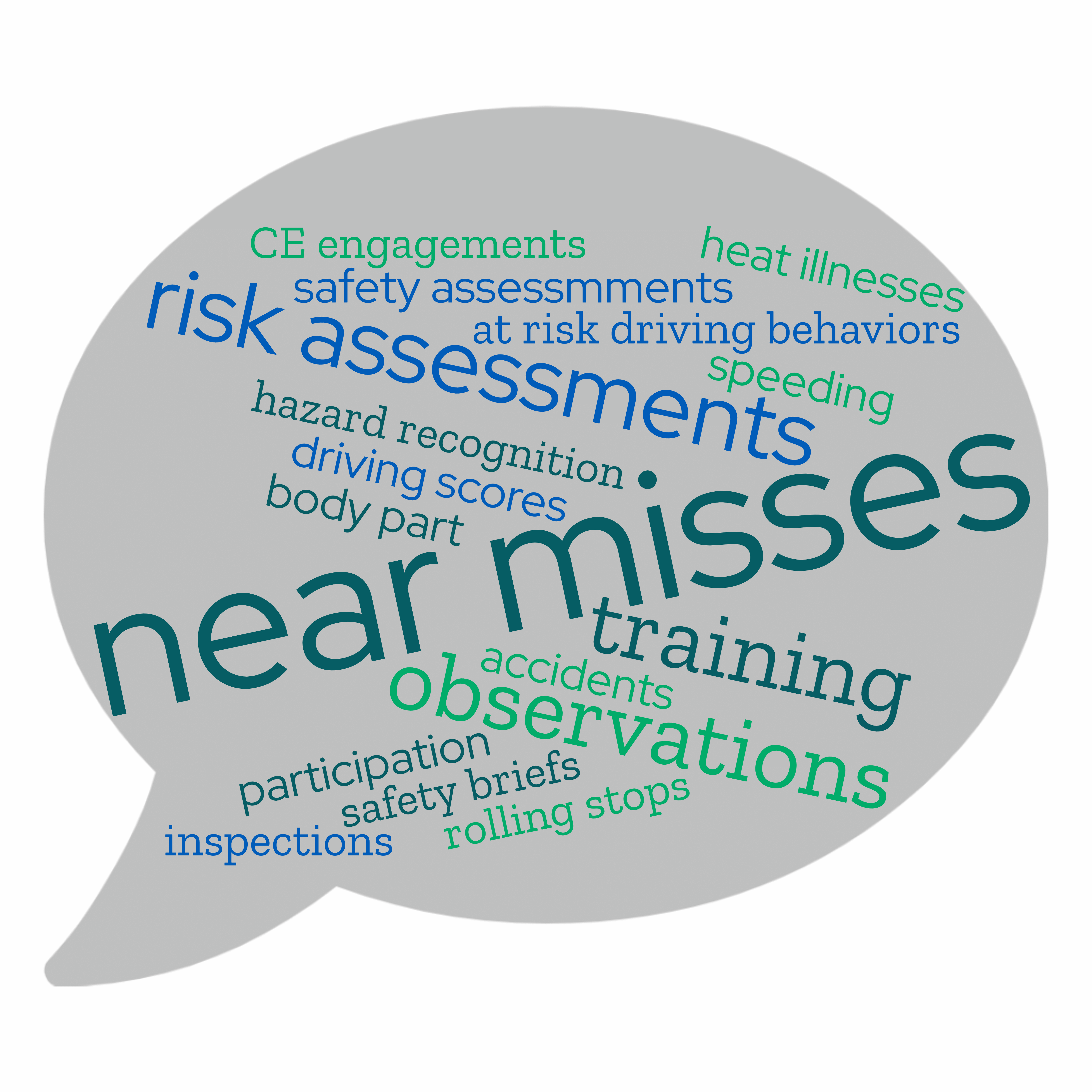
What are some of the leading indicators that you’re tracking?
At-risk driving behaviors such as speeding and rolling stops.
How do you determine their effectiveness?
We use artificial intelligence built into our dash cam system.
Bill Woods
Director of Safety, Quality, and Regulatory Compliance
American Welding and Gas
(Read the Case Study)
What are some of the leading indicators that you’re tracking?
Number of safety assessments, Number of CE Engagements, Number of Hazard Recognition Cards
How do you determine their effectiveness?
High numbers normally correlate to increased safety culture on the job site and fewer safety-related issues
Safety Specialist, Construction Company
What are some of the leading indicators that you’re tracking?
Good catches, training compliance, equipment maintenance
How do you determine their effectiveness?
Mostly by our incident rates and severity. Being a smaller org, we like these to be at zero as a single incident wrecks our numbers.
Timothy Shaw
Information Success Coordinator
McCumber Well Service
Tracking leading indicators is easier with solid EHS software in your safety team’s hands.
KPA simplifies data visualization and reporting, giving users easy access to actionable insights into their EHS program performance. Your data is presented in real-time, so no delay or extra steps are required to access the information. The dashboards are configured based on features tailored to your business’s unique requirements, giving you the power to make informed decisions that impact workplace safety.
Let KPA show you how to take a data-driven approach to safety.