Unpacking the Top 10 OSHA Violations for 2023: An Interview with KPA’s Zach Pucillo
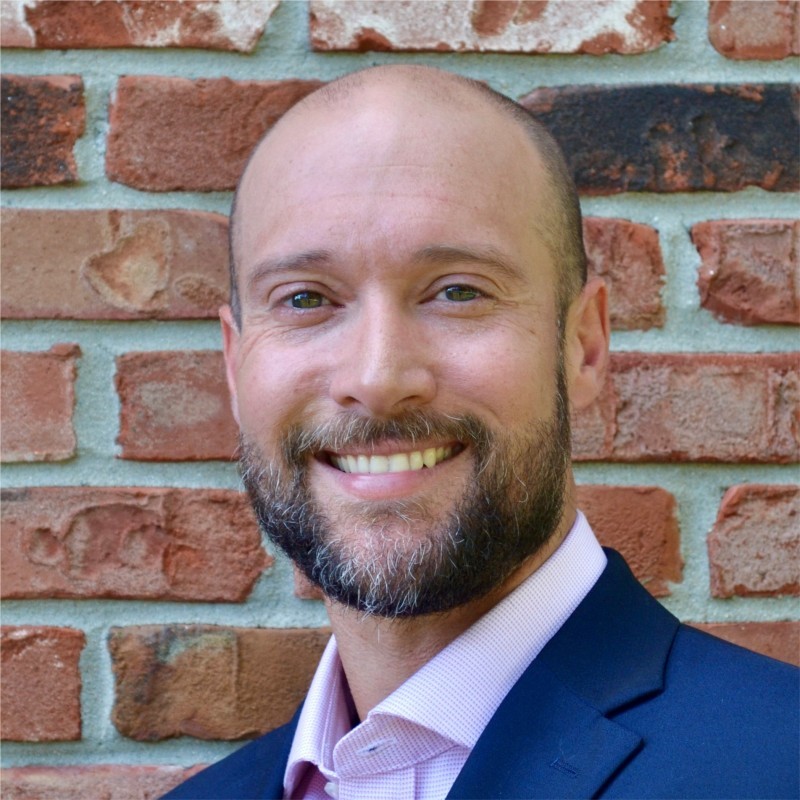
Today, we’re back with KPA’s EHS Regulatory Compliance Manager, Zach Pucillo, to talk about OSHA’s most frequently cited standards. OSHA just announced its top 10 list for 2023. Zach, to get started, can you tell us what those top 10 are?
Yeah, thank you very much. So, I was actually live in person at the National Safety Council’s Congress a few weeks ago in New Orleans and got to see this live as OSHA was going over this top 10 list for the fiscal year of 2023.
So we’ll go from 10 up to 1 here. We don’t need a drum roll, but in the number 10 spot, we have Machine Guarding with 1,644 total violations.
Number 9 was Personal Protective and Lifesaving Equipment for Eye and Face Protection, with 2,074 citations.
Number 8, Fall Protection – Training Requirements, 2,112 citations.
Number 7, Respiratory Protection, with 2,481 citations.
Number 6, Lockout/Tagout Standard or Hazardous Energy Control, with 2,554 citations.
Number 5, Powered Industrial Trucks, with 2,561 citations.
Scaffolding comes in at number 4 with 2,859 citations.
Ladders, with 2,978 citations, comes in at number 3.
And then number 2, Hazard Communication, with 3,213 citations.
And number 1, no surprise here, Fall Protection – General Requirements with 7,721 total citations for the year.
[00:02:02]
That’s quite a list. And you were in the room for that announcement. Was there anything that stood out to you in particular?
So, as far as which regulations made the list, I’ll be honest and say no. That list does not really change year over year, unfortunately. You would hope that some of those may fall off the list. We’re trying to be educated more on other standards, but unfortunately, these 10 continue to make the list year after year. But the order was a little bit different for a few of them.
For instance, Respiratory Protection fell down the list. It was number five, I believe, last year, and then the year before that, it was up around number two. It has fallen down to number seven on this list. I think that’s because the pandemic a few years ago really caused respiratory protection to jump up as a majority of the workforce was wearing masks, and some of them were wearing actual respirators.
And when an employee is wearing a respirator in the workplace, even if they’re wearing it voluntarily, there still have to be some items followed out of the standard. It’s a voluntary use form they call the Appendix D of the Respiratory Standard. With not as much of a focus on the pandemic anymore and employees not wearing masks or respirators, I can see how that one probably did fall down on the list a bit more.
Fall protection continues to be number one, and it’s number one by a huge margin. Unfortunately, we are not getting control of that. OSHA has put forth several different efforts, such as Stand-Down for Safety Month, with a huge emphasis on fall protection. In fact, earlier this year, they put in a national emphasis program on fall protection for certain industries, mainly on the construction side, because that’s where we see a majority of those citations occur.
And I’ll go ahead and throw out a particular industry, and that’s residential roofing. It’s really unfortunate because anytime you’re going over 6 feet, the fall protection standard does apply, so we have to protect those workers. And in the residential roofing area, they are constantly moving around on a roof.
I don’t know if you’ve had a roof done recently, but I had one. I live in suburbia United States, and we’ve had hailstorms, so we’ve had to have roofs replaced before. The company will come out, and they will try to get it all completed in about a 1 to 2-day span. Unfortunately, when I looked up there at the employees who were working on my roof at the time, not one of them was wearing fall protection. I had a conversation with the company owner about that, and he was like, “Time and efficiency, time and efficiency.”
Another thing that did stand out was – Hazard Communication at number two is not really standing out, it’s usually been up there. However, the industry that was most frequently cited was hotels and hospitality. Typically, in the past, we were talking about manufacturing or maybe some of the other different general industries, but hotels and hospitality was one that kind of surprised everybody in the room. There were actually some questions about that. What is the cause of hotels and hospitality jumping up there?
And really, it’s the cleaning chemicals that the employees are using to clean the rooms and do all the laundering of the different bed sheets and towels. So when you think about that, those hotel owners need to make sure that they have a hazard communication program in place. And unfortunately, they’re very unaware of that, and employees are being subjected to chemical exposure without having the proper safety protocols in place from that standard.
I will say that automotive and automotive repair, which jumped up to number three as the most frequently cited industry, opened my eyes a bit. I’ve worked with a lot of automotive repair companies in the past, and typically, they try to be on top of things, but the labeling of the chemicals usually ends up getting them in the long run.
[00:05:55]
Thanks for sharing your insights, Zach. As you mentioned, this list hasn’t changed a lot. This is the 13th year in a row that fall protection has led the list. Why do you think some of these are so intractable?
Yeah. It’s one that we’re all trying to figure out. Even OSHA is still trying to figure it out. Unfortunately, like I said, it’s the time and efficiency thing. Residential roofing, obviously, is the number one cause of that. Anytime you go over four feet in general industry, the fall protection regulations kick in.
And construction, which is where residential roofing falls into place, it’s anything over six feet. And so, once you go on a roof at that point, you have to have fall protection put on, especially working on those slopes of those roofs. In fact, when we’re recording this, we’re not far from the holiday season, and actually, holiday lighting is another different industry that was mentioned in the actual session as an industry that was climbing up to the top of the list for fall protection as most frequently cited.
I don’t know about you, I would love it if a company came out and hung all my Christmas lights up for me. Prevents me from having to climb up there and do that, but when they do that, are they actually putting on the fall protection they’re supposed to be? No, they’re not, and they’re cutting corners. They’re getting it done because when you have to put on a 5-point harness, you have to anchor point somewhere on a residential roof, which means anchoring, and unfortunately, you have to almost install an anchor point that would be attached to the roof structure somehow.
And now we’re getting into the issue of damaging a customer’s roof for your own safety. So, do you literally want to battle that? And so that’s probably causing there to be more people that are not putting on the proper fall protection. They do make different anchor point systems out there that will actually not damage a residential roof. However, it means spending money on that type of equipment, which becomes very costly for a company.
Also, hazard communication. It’s such a meticulous standard. There are so many things that can easily go wrong with being in non-compliance. If you think about it, do you have cleaning chemicals in your home? I assume you do.
[00:08:09]
Yes, absolutely.
So, if you look at your cleaning cabinet, you probably have, what, maybe 20 of them? Maybe a little less than that. But at that point, you’ve been gathering all these chemicals over the years, and so you’re constantly using them for different types of cleaning. But if you’re an industry, you have to make sure that you’re training all of your employees about each one of those chemicals. You have to make sure you have a safety data sheet on hand. You have to keep an inventory of what you have.
[00:08:40]
Ensure everything’s labeled properly.
Yeah, think about putting those cleaning chemicals in the spray bottles, and then if you have children, now you’re handing those over to the children and saying like, “Oh, by the way, can you label those for me?” That’s pretty much what a workplace is like. We provide all these chemicals. Now, here are some spray bottles. Put your chemicals in there and go label them the right way.
And unfortunately, without proper training, they’re not doing that. And so, these compliance officers, it’s easy for them to call out these standards that are on the top 10 list. It’s one of those things where you know it’s wrong when you see it. So, it’s very easy to identify these things. If I drive by and see a guy on a roof without fall protection, I can easily pull over and start issuing a citation for that.
[00:09:24]
Sounds like some folks might be playing the odds there, thinking about time and expense when it comes to compliance. Are there some technology approaches that companies can take to keep themselves on the right side of OSHA regulations?
Oh yeah, and that’s where it’s at, honestly. It’s becoming so much easier to get the information that the employee needs into the palm of their hand and start requiring them to go through different checks and different audits before they go into a job.
It used to be if you were getting ready to do a particular job, you had to analyze the hazards of that job. You had to make sure, “Okay, do we have the proper personal protective equipment in place? What training do we need to do?” And then it’s canned generic training as well. So, like with hazard communication. There are a lot of different software companies out there that have hazard communication training that meets the requirements of OSHA, but it’s not specific to the site.
Now, there is software out there that has customizable training. For instance, KPA has a product called Flex. And in that software, you can actually build a customized training where you can use videos and images and pictures from your own operation, which I think is really cool.
That’s really going to get the message home to the employees. If I have to watch a video or training of somebody else’s facility saying, “Here’s how you work a trash compactor,” when somebody can actually record a video of a person I recognize working that trash compactor safely and saying, “Here’s the pitfalls of this particular trash compactor, which you will see later on today as you’re out there on the actual work floor.” That is such great training, and it’s engaging
[00:11:09]
It’s really a game-changer.
Yeah, it is, because then you know all the ins and outs of that particular piece of equipment, and it’s not that canned training that somebody has to watch. I’m sure you’ve been through several different training courses out there, just clicking through.
[00:11:24]
Yeah, when it feels like the training is generic, it’s easier just to click through and check the boxes.
Oh yeah, you put it on, and then you get your phone out, and you just start swiping away. Doing the doom scrolling is what I call it. And then when it comes to a box, like, “Oh, yeah, I’ve got to check the box that says go to the next slide.” You hit that, and all of a sudden, you’ve got a certificate that you passed your training course.
There are also other technologies out there. Form building, for example. If I could build a customized form and make it digital for any type of safety operation initiative that I wanted to do out there, that’d be so cool. For instance, lockout/tagout. Imagine, there’s a way to de-energize a piece of equipment. Such as, go to the breaker, locate it at this spot, shut this power switch off at breaker switch number 25, put this particular lock on there, and there’s an image next to it. If I can scan a QR code with my phone, and it goes right to a step-by-step process that I’ve built into a form of how to de-energize a piece of equipment — now, I’m getting feedback that, “Okay, I’m doing things the right way because it’s allowing me to continue through the form and it’s not stopping me along the way saying I’m doing things incorrectly.”
I saw an interview earlier today. I don’t remember who they were interviewing, but it was about why kids who have ADHD are more successful with playing video games as opposed to doing homework. Why? Because when you solve a math problem on a piece of paper, it doesn’t do anything. It doesn’t say, “Great job, move on to the next step.” It doesn’t say, oh, you got this incorrect, now you need to go back and retake this. Whereas in a video game, it’s like doing that homework, but it’s rewarding them or making them go back and fix what they didn’t do to beat this level, or you’re rewarded by going on to the next level.
Or, no, you didn’t actually do all the tasks here, so now you need to go back and complete those. We can actually set up training to be that way as well. We can set up forms to actually complete tasks in that way, where we reward people once they are completed by moving them on to the next level, or we take them back and re-educate them the proper way as needed.
I think there are all kinds of benefits to technology out there for the safety world. They’re going to continue to use technology, and when we use that reward where they’ve actually done the right thing, great. When they’ve done the wrong thing, we use that kind of negative reinforcement and go back and re-educate them. It’s like that game format. Why not put that to use since that’s what works?
[00:14:17]
Absolutely, and getting immediate feedback is always helpful when you’re trying to learn something.
Of course, of course.
[00:14:24]
So we talked about technology. What are some processes or people approaches companies can take to protect themselves from OSHA violations?
Knowing the regulations, of course. If people don’t have access to the 1926, the 1910 standards or know what those are. We’ve got to get somebody in the know in the workplace. So, basically, you need a leader that needs to know what they’re actually talking about when it comes to regulations. Those are people who can interpret the regulations, apply them specifically to that business model, and actually go on and prioritize what needs to be done first and then set up safety systems that follow. And if you don’t know, that’s when I would recommend, of course, hiring a consulting firm.
KPA has had consultants for years upon years upon years. And that’s the biggest benefit that the consulting experience has, is that we’re educating people who have no idea what the actual regulations are. But we’re not just saying, “Oh, you have to do this because 1910.134 says so under the respiratory protection standard.” No, we’re breaking it down and making it apply to their business model.
Like, “This applies, and here’s the respirator we should be selecting for this. It is the best option. We need to make sure that because we’re going to select this respirator, we have to go through and make sure that these guys get medically evaluated, that we’re fit testing them for that respirator, that we’re training them on the consequences of not wearing that respirator so that they make a good, educated decision to wear it going forward.”
The days of the hands-over-eyes, mouth, ears, hear no evil, see no evil, all that, those are gone. And based on this top 10 list, we’re starting to see that OSHA is back. With the pandemic going on, people were not in the field, people were not actually at the work sites. However, I believe there were around 22,000 citations last year. This year, I think we’re up around 34,000 total citations for the year. So, these numbers are growing. OSHA is back in the field, and they’re not going to take it when it comes to the attitude of, “Well, just turn our eyes. Go out there and just get the job done, and oh yeah, be safe.” Tagging on that, “Oh yeah, be safe”, is not a safety program.
If you’re still on the edge, you’ve got to understand that Millennials and Gen Z in the workplace know their rights, and they’re going to start contesting unsafe working conditions. There’s that whole defiant type of atmosphere that is out there, and it’s catering to who the actual workforce is going to be. They know technology; they are the most educated and well-informed generation coming into the workplace because they’ve had all the information in the palm of their hands. And when they feel something is not right, they’re going to blow that whistle.
And so that’s when we have regulatory agencies come in, and once again, we can’t just be like, Oh, I didn’t know. No, there was enough information out there. You should have known. And now is the time to make sure that you are in the know going forward.
[00:17:38]
Absolutely. Getting an OSHA citation is certainly one consequence of not following safety regulations, but there are others that are arguably worse. What would you say is the scariest safety issue you see with regularity?
There are all kinds of different consequences that are out there. The things that lead to consequences – cutting corners and complacency. Those are probably the two biggest battles we fight every day. Usually, the employees in the know, they’ve been through training; they know they weren’t supposed to do that, but they did it anyway. And that’s a very scary attitude that can grow and manifest into a really bad culture for your organization. You have to make sure that you’re getting in control of that.
I mean, cutting corners so that we can just get the job done faster, at what expense though? What if cutting corners turns into cutting the tip off of a finger? Now, when you thought you were getting an extra 10 minutes to go home a little bit earlier, has turned into probably another 10 hours of medical care and paperwork. All of a sudden, we’re asking, can this employee continue to work? Do we have to backfill their position? So, cutting corners is not the right way to go.
Complacency, once again, is not the right way to go. That’s just turning a blind eye and being like, “Well, we haven’t been cited in the past, so why continue to do this?” No. That’s not the right way to go about it because it is going to catch up with you eventually. And then the ultimate consequences are employee injuries, deaths, severe injuries, and fatalities – SIFs are what they’re called out there now.
I’ve noticed a group of employees that we’ve seen a bit recently more when it comes to citations and also severe injuries and fatalities. And those are maintenance teams. So, we’re training the individual line employee on how to do their job safely and those specific job tasks. However, our organizations typically have some kind of maintenance team. It might be a maintenance team that goes around and fixes equipment. It could be for lawn maintenance, or it could be landscaping out there to take care of the facility on the outside. And these teams, just trying to keep the building up to date, are exposed to so many hazards that you may not be prepared for.
For instance, you may not have any reason to really have a lockout/tagout program, but if you have a maintenance team and they’re gonna go up and replace light bulbs in the ballast or maybe switch from incandescent bulb fixtures to LEDs like a lot of companies are doing, now there’s a chance you have to worry about lockout/tagout, and potentially fall protection
Unfortunately, not very long ago, in a dealership setting, there was an employee who was changing out some ballasts, and they did not shut the power off for some reason, and they didn’t lock it out. And so they received a shock and fell out of a lift and ended up falling to their death, unfortunately. And it’s like, if we had a lockout/tagout program and we’re training these maintenance teams on this, maybe that could have been prevented.
Another situation, 3Ms in the news right now. They are a massive company for labels and adhesive products, and they had an employee get caught in rollers. So, you know, no machine guarding; there were lockout/tagout issues as well. There shouldn’t ever have been a case where they could have gotten their hands that close.
Another maintenance team issue happened, I think it was in Tennessee years ago. A maintenance person was going up to the roof to put some extra waterproofing around a skylight. And OSHA has fall protection regulations specifically about skylights. If you have skylights, you have to make sure that you have fall protection about six feet around those skylights or you’re wearing a harness and lanyard. And this individual wasn’t. And so put their hand on the actual glass, and they’re applying the caulk around the glass fixture, and the glass ended up falling through, and the employee fell through as well. And there was definitely a tragic outcome when it came to that.
So, just understanding that with these maintenance teams, there are a lot of other regulations that can’t apply to them based on the jobs that they’re doing out there. They’re putting out pesticides, they might be sharpening blades, changing out light fixtures, fixing roof leaks, and then we’re talking fall protection, pesticide regulations; we’re talking lockout/tagout, machine guarding. All these things can apply to people where you might have thought, “Well, we don’t have to educate them anymore. They know what they’re doing because of industry experience.” It’s not the case.
[00:22:24]
Everyone needs reminders.
Of course. Even me, as I’m probably going to go hang up my holiday lights this weekend.
[00:22:34]
Right, right. Before we close out, is there anything else that you’d like to share with our listeners?
I would just say, especially as we’re coming into a winter season, depending on when you’re listening to this, just make sure that you’re also focused on seasonal changes when it comes to safety out there. Depending on where you’re at in the country, you’ll have different weather hit from time to time. So, have a winter preparedness plan. If you are hanging holiday lighting, make sure that you’re using fall protection when you can, and apply these things to your home as well.
We focus so much on our organizations and keeping our employees safe. But also, I will say the other day, I had a household meeting right after dinner with my children. And I showed them where the three fire extinguishers we have in our house were. I also showed them how to operate those fire extinguishers. We have a two-story home. I showed them where the roll-out safety ladder was and how to use that. And none of them knew. And I have age ranges from 16 all the way down to 11 years old. None of them knew how to use any of that equipment and weren’t even sure where it was located. So, I would say, with these top 10 items, take a look at your home as well too. Does anything apply there? And just make sure you keep a safe home as well.
[00:23:55]
I appreciate how you always bring everything back around to something relatable, Zach. And just thank you for joining us here today. We really appreciate having you.
It’s always a pleasure. Anytime I can preach safety and continue to try to get the message out there, I’ll take every chance I can get at that.