To protect employees and reduce the occurrence of illnesses and injuries, employers need information about the dangers of the chemicals they use and recommended protective measures. Workers have both a right and a need to know this information so they can take steps to protect themselves when necessary.
Perhaps it’s no surprise that hazard communication tops the list of most-cited OSHA violations. And that’s tough on businesses. Sliding out of OHSA’s good graces costs companies millions annually, between fines, legal fees, and internal time and effort.
OSHA’s Hazard Communication standard (29 CFR 1910.1200) details the chemical hazard information that employers need to share with employees. It covers all industries where employees are potentially exposed to hazardous chemicals and outlines a common and coherent approach to classifying chemicals and communicating hazard information.
Container labeling is a critical part of complying with the Hazard Communication Standard, and one that trips up a lot of safety teams. To keep you on the right side of the regulations and keep your team safe from chemical exposures, we’ve pulled together some best practices on container labeling for you.
What OSHA Looks for:
- Designation of person(s) responsible for ensuring compliant labeling of containers
- Description of written alternatives to the labeling of stationary process containers (if used)
- Appropriate labels on all workplace containers, including those received from a supplier, secondary containers, and stationary process containers
- A description and explanation of labels on both shipped and workplace containers are included in the employee training program
- Procedures to review and update workplace label information when necessary
Tip: Don’t Remove Labels on Shipping Containers
Paragraph (f) of the hazard communication standard states that a label must be on the immediate container of every hazardous chemical in the workplace. The label provides a snapshot of the hazards and protective information related to the chemical and a summary of the detailed information available on the SDS.
When you purchase a chemical from a supplier, the container will be labeled with the information required under the HCS. Employers can rely on the information provided by their suppliers.
The labels on a properly labeled container will have the following information, located together (other information may also appear on the label):
- Product Identifier: The common (or trade) name
- Signal Word: Either “danger,” for more severe hazards, or “warning,” for less severe hazards
- Hazard Statement(s): The hazard class and category that describes the nature of the hazard(s) of a chemical, including, where appropriate, the degree of risk. Example: Fatal if swallowed.
- Pictograms: One of eight symbols designated for application to a hazard category. Under the HCS, pictograms are black symbols, on a white background, with a red diamond border.
- Precautionary statement(s): A phrase that describes recommended measures to minimize or prevent adverse effects resulting from exposure to a hazardous chemical or improper storage or handling. Example: Do not eat, drink, or smoke when using this product. There are four types of statements: Prevention, Response, Storage, and Disposal. These have been assigned to hazard classes and categories.
- Name, address, and phone number of the manufacturer, importer, or other responsible parties
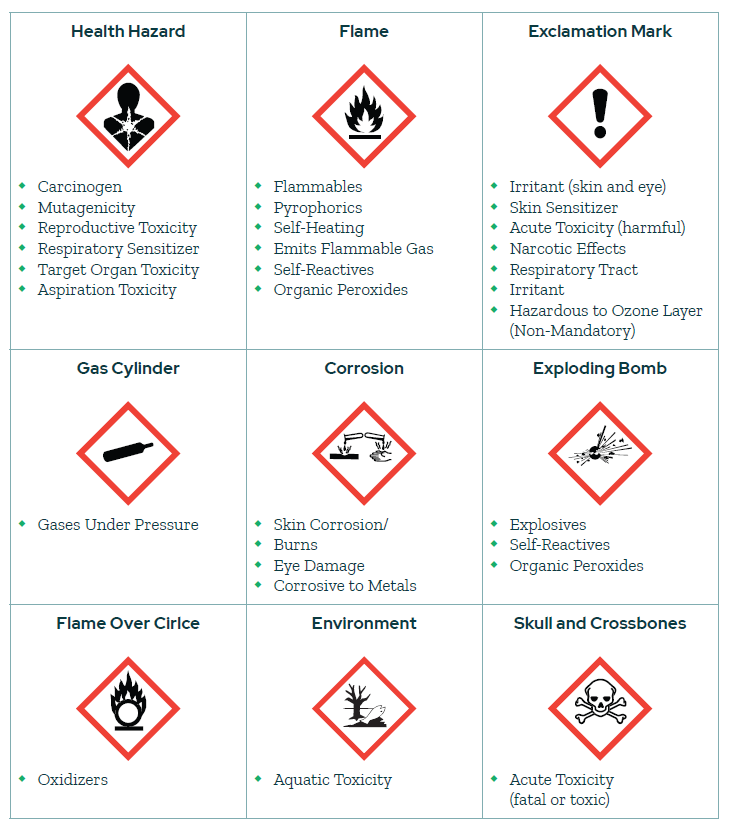
Tip: Label Secondary Containers
Employers may use signs, placards, process sheets, batch tickets, operating procedures, or other written material instead of affixing labels to individual stationary process containers. However, the alternative method must identify which containers it applies to and convey at least general information regarding the hazards of the chemicals.
Make sure that labels in the workplace are legible and prominently displayed. While the label information must be in English, employers are free to add warnings in other languages if workers would find that helpful.
Create a safer workplace with easy access to your Safety Data Sheets. KPA can help.
With SDS Manager:
- Safety Managers import SDSs from a database of over 70 Million SDSs to create a customized library.
- Employees access SDSs within seconds – even when offline or in the field.
- Print pre-populated secondary container labels for GHS compliance.
- Comply with OSHA’s Right to Know and Hazcom requirements.