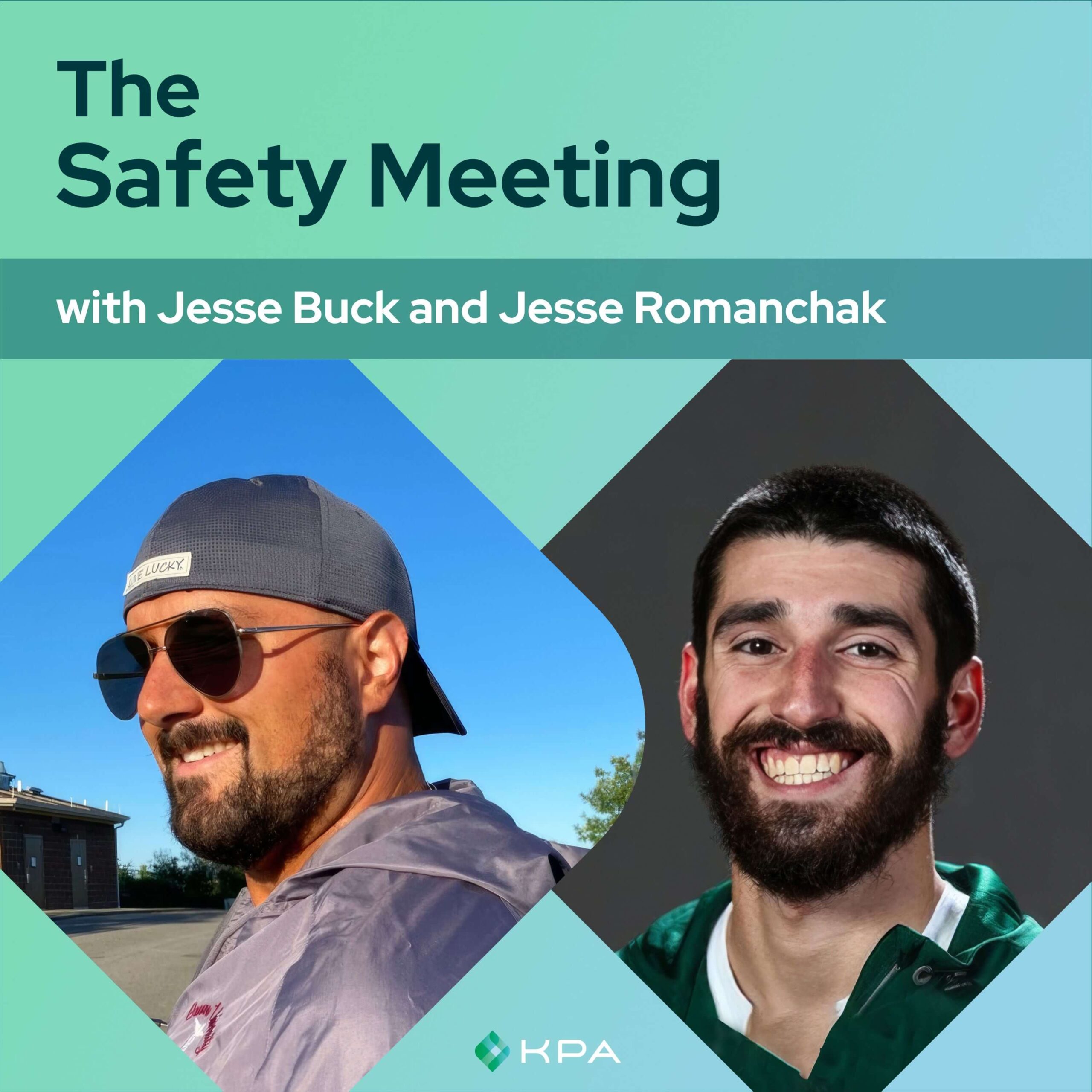
Today we’re speaking with two superstars on the training team, Jesse Romanchack and Jesse Buck. Jesse R, ASP is the industry segment manager on our training team, bringing over five years of experience in the training industry. His expertise and commitment to developing impactful content make him an essential part of the KPA team.
Jesse B, CSP is the industry safety specialist on our training team. With 11 years of combined safety experience, he has developed training for numerous hazardous industries, including steel, oil and gas, metals, recycling, plastics, production, construction, and the automotive sectors. Both these Jesses’ work has been invaluable to KPA, and they’re excited to discuss safety culture with everyone today.
Welcome to the Jesse episode of the Safety Meeting. Thanks for being with us, guys.
Jesse Romanchak: Yeah. Thanks for having us.
[00:01:06]
Absolutely. Alright, let’s jump into the questions. So when you think of companies with strong safety cultures, what stands out to you the most? What do they do differently from the start?
Jesse Buck: When I see companies with strong safety cultures, the biggest thing that sticks out to me is that they make safety personal.
Now, what does that mean? Well, what I’ve noticed is that they don’t really make safety about numbers and metrics. Obviously, those goals are important to set, but they’re not as vocal about that portion of the safety field. Instead, they tend to lean more towards a family environment where everybody’s in it together.
They make it about looking out for your teammates. They’re vocal about that and safety meetings and other environments. To piggyback on that, they try to promote having a reason to work safely. A great example of this would be “family boards” or “Why We Work Safe” boards. These are boards that have employees’ pictures on them, families and friends, and loved ones, and they’re placed in a high-traffic area where a lot of people are able to see them.
And it just serves as a constant reminder that you should take your time and work safely, whenever you walk past and see it.
Jesse Romanchak: And to add on what Jesse B has just said there, the things that stand out the most to me, companies with a strong safety culture, they really practice what they preach on the top down the buy-in from ownership and the management that trickles down to their employees.
You can tell that safety just isn’t a priority for the week because priorities can change, but it’s a value that they live by. So, it’s the companies that are transparent about safety and would rather sacrifice productivity for the sake of safety and the well-being of their employees. That really sticks out to me.
[00:02:46]
Yeah, that makes sense. I can see how the draw to be more productive is there, but it’s great to see that there really are companies out there that do make that sacrifice to ensure that people are coming home safe. And you know, I’m sure across different industries, there are different reasons for the productivity differences.
The training team has a deep background across these industries, as we mentioned in the intros. So, can you guys talk about some unique challenges or best practices around safety culture that you’ve seen in industries like construction, steel, plastics, and others?
Jesse Buck: So usually, you can gauge the safety culture of a company by looking at the work environment. Housekeeping. You see some good and some bad. It’s kind of an eternal struggle depending on the industry that you’re in.
Two of our plastics clients have some of the cleanest work environments that I’ve ever had the pleasure of working in. Everybody I’ve worked with at those locations has always been a class act when it comes to safety.
Another thing you noticed is that time is always at a premium in the work environment. There’s only so much time in the day for production and training, and sometimes it can be hard to balance that and keep everybody up to speed.
[00:03:54]
Absolutely. It makes a lot of sense that managing that time and keeping everyone on top of things can be tough to balance, but I know that there are some insights into these industries that can help shape the training that KPA develops.
So, are there any specific elements that you’ve built into the training to address these unique challenges?
Jesse Romanchak: I can answer the follow-up there. KPA is always striving to make a better training product. By being hands-on in these plants and facilities, our team is able to see what specialized training would be the most helpful. We also take the time to talk with employees and get their professional insight because they’re living this life every day.
So by speaking with them, we’re constantly updating our interactive scenarios and incident recreations to make our training content even more relevant to their industry.
Our Better Workforce Blog is your Ultimate Guide!
Stay informed with weekly industry updates, expert insights, best practices, and actionable tips to enhance workplace safety and compliance.
[00:04:41]
It sounds like you guys are taking feedback in real-time to impact the way that your training content is being developed. How has your experience on the team been impacted by taking in that information to develop those trainings?
Jesse Buck: It has a pretty significant effect on our content. A big part of our job is to observe and analyze the work environment that we’re in. I just want to see if there’s an opportunity to develop new styles of training and new types of training.
Our Blind Spot Training video, which we have produced in the past, is a great example of this. While working with mill service clients, they have large pieces of equipment that are constantly in motion. Anything from frontend loaders to slide pod haulers and massive trucks used to haul product. While a lot of the large equipment these days has backup cameras and different proximity cameras, all these pieces of equipment still present other blind spot hazards that really can’t be addressed. So, we worked with a client to create a video, not just for them but for clients across the board.
We’re always looking for different topics that would add value while out on location and are always willing to collaborate to get it done.
Jesse Romanchak: And just to add on that, by constantly visiting new facilities and also new industries, with our boots-on-the-ground approach, we’re able to have conversations with these managers who are working and striving to keep their employees safe each and every day. And in these conversations, we’re able to hear firsthand what prime hazards are of the most concern in these environments.
By relaying that information back to the team at KPA, we can identify how to update our training and make it even more impactful in addressing those industry-specific hazards instead of creating a cookie-cutter and generic training experience.
[00:06:26]
Yeah. I think we’ve touched on this a couple of times, but it sounds like being in these scenarios and living through this day-to-day with some of the people who are using our content can really shape how we design training. Are there any specific modules or approaches that you guys have implemented because of the insights and observations you’ve made on-site?
Jesse Romanchak: Yeah, sure. As a result of engaging with these managers, again, at these facilities, we’re constantly identifying opportunities for new training series, and as a direct result of speaking with one particular manager in one specific industry, we actually developed our Line of Fire series. That was, at the time, just for one industry, but we were able to make it available across multiple platforms, and it has since helped a few industries change their safety.
It’s just cool to see how inspiration can come from one particular aspect and then spread across the board.
Jesse Buck: And just to add to that, regarding how we approach it, we try to make the training more interactive and as engaging as possible, whether that’s through a powerful employee interview, recreating an incident that happened in the real world, developing interactive scenarios within the training that really force you to stop and analyze a safety scene.
Our main goal is to have the training stand out and be different from other offerings. That’s one thing that’s in constant motion. We’re always looking for ways to make training as interactive as possible while still providing great information.
[00:07:54]
Absolutely. And the couple of other times we’ve had people from the training team on the podcast, we’ve always mentioned the way that recreating those real-world incidents can have a huge impact on people who are taking that training. I think seeing the real-world impact makes a lasting impression.
I know that there are lots of pieces that go into having that tenacity, training, and sticktoitiveness so that people keep it at the top of their minds. From what I’ve heard in other conversations, it seems like management buy-in is a really big part of that, too.
Can we talk a little bit about the role of management buy-in in building a positive safety culture? And how do you see this trickle-down effect impacting the team overall?
Jesse Buck: In my opinion, management buy-in might be the most critical part of creating a positive safety culture.
If there’s no buy-in from the top down, you’re usually not going to see a company with a very good safety culture.
Those working at the floor or site level look at management for guidance on how their work is conducted and how to do it safely. If employees get the sense that management just isn’t looking out for them, they’re less likely to make the changes that management might want to implement.
A good way to show that management cares is just to be seen.
This can be done by conducting safety walks throughout the work area or even having management involved in performing job hazard analysis for specific tasks. It’s just a very basic way for management to know the work area and the employees who work in those specific areas. It’s a great opportunity for management to see the work being performed and identify any areas that have safety deficiencies.
It allows employees to see management working at the floor level. During this process, it’s good to talk to employees as well.
Ask questions, do they have any concerns? Maybe even get to know them on a more personal level, and it can really go a long way towards showing employees they’re cared for and that safety is important to the company.
[00:09:50]
To me, management buy-in is a key component of ensuring that safety culture is ubiquitous throughout the team. Can you guys talk a little bit about how KPA’s training or tools can support managers in leading by example when it comes to safety? Are there features that specifically encourage this kind of trickle-down effect in teams?
Jesse Romanchak: Sure. Maybe not specifically features, but in the past, KPAs training always made an effort to utilize management to showcase the safe work practices that are in our videos. Showing these employees that their managers are committed enough to be on the floor and demonstrating how to do things the right way instead of just sitting back in their office and letting them figure it out on their own really supports a culture that’s committed to keeping its employees safe by practicing what they preach.
Additionally, we try to make it as apparent as possible that employees can always reach out to their supervisor or manager if, at any point, they misunderstand any elements of our training content. KPA highly encourages and really wants to emphasize leaning on your management team to foster a safer working environment.
[00:10:53]
That makes a lot of sense, and it sounds like being connected and really cultivating that sense of community means a lot and can make a big impact when it comes to making sure that everyone is staying safe and doing what they can to stay safe. So, are there any creative or unique ways that companies can foster that sort of village or team atmosphere around safety?
Jesse Buck: Yeah, absolutely. I mentioned the family boards and “Why We Work Safe” boards above. But another program that I’m a huge fan of is Stop Work Authority.
Having a robust Stop Work Authority program can be a nice addition to your safety program. It gives the employees the authority and responsibility to speak up whenever they observe a dangerous situation occurring or see someone else performing unsafe behavior.
Some companies even have software cards that employees can carry around and pull out whenever a stop-work situation occurs. It just gives it that little bit of extra oomph to help it hit home more.
The critical part of the program though, is not just telling someone to stop, and then scolding them and saying that they’re wrong. It’s all about how you communicate the issue. If you’re initiating the Stop Work process, talk about the situation calmly, letting the affected person know that they care about their safety and why they initiated the stop work in the first place. For instance, if I were to observe someone performing an unsafe act, I might say, “Hey, so and so, I noticed you were working from an extension ladder that wasn’t properly tied off. This made me worry that you might fall off the ladder. I really don’t want to see that happen to you. I’m initiating my stop work so we can work together, find a solution, and keep both of us safe.”
Jesse Romanchak: Yeah. And then just to add to that, Jesse Buck and myself, on numerous visits, you know, we walk into plants and facilities and see all the pictures of family and friends that are on those poster boards in the hallways or around the locker room right before you go out onto the floor.
It just kind of serves as a reminder of what’s at stake here. You know, the goal of a safe work environment is that you want to return home to your loved ones in the same condition you came to work in. And you know, that reminder of family is something that helps each and every employee stay grounded and keep each coworker accountable. As Jesse Buck mentioned, reaching out and saying, “Hey, maybe you should think about doing it a different way because you’re not only staying safe for yourself but for the family back at home too.”
[00:13:14]
Yeah, absolutely. We talk a lot about how the objective of everything that KPA does is to send people home to their families safely, so it makes sense to bring that up in the workplace.
And I think the example you gave Jesse B about how you would word it, “Hey, I noticed, I’m worried. Let’s work together.” I can see how that would really encourage people to want to make it safer rather than, as you said, being scolded and having them feel bad about what they quote-unquote did wrong.
That leads me to another question: How can a strong safety culture impact the team outside of these safety outcomes? What are some ripple effects that you guys have seen?
Jesse Buck: The biggest thing I see is the attitudes of the employees. When we walk around these facilities, we’re usually with the local safety professional. Watching the interactions between the workers and that safety pro is always a good indicator of the safety culture and where it’s at.
You notice more of a good comradery type of atmosphere between all the workers whenever they’re having positive interactions with the safety professional and amongst themselves, and the good attitudes are just a big telltale sign. And you can just tell it creates a more positive environment for everybody to work in.
[00:14:29]
Yeah, and that sounds like it makes work better overall. So, as we talked about, aside from keeping teams physically safe, let’s talk a little bit more about how fostering that positive safety culture can continue to impact the workplace. Are there ways that training can support these broader cultural goals to get people in more of a comradery sort of environment?
Jesse Romanchak: Yeah, absolutely. One thing that I’ve noticed in safety cultures that are actually thriving is that it really seems to boost morale. The employees don’t seem to feel extra stress or pressure to rush and complete a task and skip those critical safety steps that would put them at risk of an injury because safety comes before productivity.
In these types of workplaces, employees are more inclined to keep one another safe as a family would, as we mentioned previously. The last thing they want to see is their coworker get injured on their shift, you know? So, KPA works to include personal stories from employees who may have suffered life-changing or altering injuries as a result of a poor safety culture or actions.
By including stories from real people and how their lives have been affected, we feel that it really hits home on a personal level why a positive safety culture is of the utmost importance.
[00:15:41]
That makes a lot of sense, and I’m sure when you come onto a job site, and you start learning about the safety of what you need to do, it sometimes can feel abstract until you maybe see those real-world experiences or have your own aha moment in safety.
So, can you guys share a time when you immediately felt that a team safety culture was good or not so great? You know, maybe these people haven’t had their aha moment yet.
Jesse Buck: Yeah, I definitely have had that aha moment.
It was a long time ago. I was still pretty young in the field and I was working on a construction site with one of the managers on the project. They decided to bypass a guardrail to get a better look at some work that was happening below, or finished work, something to that nature. And he just stepped over the guardrail to get a better look right in front of me. Despite me telling him, you know, “Hey, what are you doing? Get back here.”
He kind of took that attitude, saying it’s okay and nothing will happen. I’ve been doing this for a long time, and it was a pretty interesting situation for me, to say the least.
Jesse Romanchak: And then a similar situation, but not quite as dire. I was out on a visit for KPA during my first year with the company, and on this visit we were there to develop some Lockout Tagout Tryout training.
When we were there, they didn’t have a lockout board, color-coordinated locks, or tags. That was a bit of a surprise to me and an eye-opener that some companies aren’t really doing their due diligence to set their employees up for success in a safe working environment. These employees at this company weren’t aware they were even working under unsafe conditions because of the lack of management education and buy-in.
So they were working at a disadvantage without knowing it. Thankfully due to our training it’s been improved, and since going back they have a proper lockout board and the employees are aware. But it just goes to show that without that buy-in, some employees are set up to suffer.
[00:17:41]
Yeah, it’s got to be hard to see and realize that maybe the company you’re coming to help doesn’t have a great backbone when it comes to protecting its employees. And it’s got to be tough to see that and go, “Oh geez, how can we help?”
So in moments where you’ve noticed that there’s a weaker safety culture, what aspects of that culture stand out the most? Do you find that effective training can encourage or discourage these behaviors in a way that affects the safety culture?
Jesse Buck: Well, the experience that I had was kind of a rude awakening for me regarding safety and culture going hand in hand.
I think in a lot of situations, very experienced people feel like they’re bulletproof when it comes to their work environment. If they’ve been at it for a long time, you know, they’re good at their jobs, and that’s a very, very dangerous mindset to have.
In our training, we try to reiterate that accidents can happen to anybody, no matter how experienced they may be. Safety is a constant, and it should always be at the forefront of each daily task that you perform.
Jesse Romanchak: Yeah, and to follow up on that as well, you know, an aspect that always stands out to me again is that management buy-in. When we walk around a facility with a manager who prioritizes safety, you can just tell by how the employees are performing the work and how they offer to participate in our training.
That culture is being positively affected all the way from the top to the bottom through good management. So I feel that KPA’s training does a great job of showcasing how everyone can have an impact on safety and that no action is too small. And that working to keep yourself and your coworkers safe, whether that be just maintaining proper housekeeping or going through the proper procedures of lockout tagout tryout, our training is always trying to drive the point home that any unsafe act is simply not worth the risk.
[00:19:27]
Absolutely, and that makes a lot of sense that that’s what we’re going for.
When it comes to starting from the bottom, I want to investigate companies that are struggling more with safety culture. Are there any telltale signs that they’re struggling that you can see from the jump?
Jesse Buck: Well, personally, whenever we visit a client, it’s very easy for me to tell what the culture’s like there, safety-wise. I gauge it by how much or how often we’re approached while on location. We’re seen walking around with the safety pro, we usually have some equipment, whether that be a camera, a GoPro, or a drone, and you either get people looking at you suspiciously or just approaching and say, “Hey, what’s up?” and being curious about what’s going on that day. We’re always looking for participants in the work that we do.
When people approach and want to volunteer willingly, that really, really says a lot. It makes you feel like the safety culture is working well. So when you notice people being a little more standoffish in our presence or with the safety pro, you can tell that they might be lacking in the safety culture department.
Jesse Romanchak: Yeah. And to build on that, as Jesse Buck mentioned, when you go into a facility, you can kind of tell when a safety culture is struggling or lacking when the employees appear unhappy or irritated or agitated that you’re around trying to build training content that they’re going to use.
But yeah, when you’re working in an unsafe environment, you definitely can notice. The employees are a little more stressed out, so they don’t want to be as helpful.
When we go to develop our training, sometimes we have to ask these employees, “Hey, do you know where we can find, for example, a no-touch tool or certain PPE so we can film this recreation here?”
Sometimes, they struggle to find the right tool or PPE right away, and it’s kind of an eye-opener. You’re like, huh, you don’t know where this essential tool or equipment is going to keep you safe? If you can’t find that right away, that just tells us that maybe the culture is lacking because they don’t understand why they would need those tools or equipment or why it’s important.
The difference between a life-altering injury and a non-life-altering injury can be that sometimes it’s something as simple as using the proper non-contact tool or having that PPE on. So, those are always big indicators of a culture that’s struggling with its safety.
[00:21:46]
Yeah, and I can see how walking onto a site and getting that feel for them struggling with safety can be a big task. I’m sure it can be a big task to try to promote safety in an environment like that. So, what are some small, consistent actions that teams can take to start building a safety-first mindset on the team?
Jesse Buck: A great way to do that would be to present safety information and training in more small bite-sized pieces.
When you use the right approach for the right topics, it can help employees engage more with what’s being talked about. This is in contrast to longer, drawn-out trainings, where you might have a few people zone out. Longer trainings can be tough.
Weekly Safety Alerts are also a great tool. It doesn’t have to be a major topic, just something that’s going on that week or that day in the plant. They basically make employees aware of what’s going on in a short duration of time, as opposed to sitting through a long training session.
Vocal reinforcement is also a great way to maintain a safety mindset. If you notice someone working safely and performing the proper steps in a job task, let them know about it. Let them know they’re doing a great job. Supervisor, teammate, it doesn’t really matter who it comes from; it just reinforces that behavior and makes it more likely that it will continue in other areas, too.
Jesse Romanchak: Yeah. And to expand on that, as Jesse Buck mentioned before, by having that positive reinforcement over time. Because building a strong safety culture is more of a marathon than a sprint. So, encouraging safe work practices every day and trying to avoid that negative connotation of reacting so harshly or trying to catch your employees in the act of working unsafely and kind of being like a safety cop. That’s going to foster a work environment of employees trying to hide rather than come to you for advice or trying to figure out how to work the safe way because they might feel like they might get reprimanded.
So that’s not really very helpful. You know, employees will be more inclined to work safely knowing that they can come to you for help. So, by giving that positive reinforcement and acknowledgment when employees are working safely, I feel that they’re more motivated to continue working in the right way.
[00:23:55]
Yeah, absolutely. That makes sense. I think you guys did a great job summarizing some of the small actions that helped to build a safety-first mindset. Are there elements in KPAs training that you guys work on that focus on these daily habits or encourage teams to adopt these consistent practices?
Jesse Buck: Yeah, we have to piggyback the small bite-sized pieces comment that I made earlier. We started to release more microcontent trainings.
These are short trainings, usually no more than four minutes in length. In fact, four minutes is kind of pushing it, being too long. It just focuses on one topic as opposed to one of our monthly videos or online training or whatever. It’s just a much shorter topic. It’s been well received so far, and we’re excited to develop more in the future.
Jesse Romanchak: Yeah, and to follow up on that, KPA always tries to be as educational and informative as possible, making sure the viewer is aware of all the risks associated with each training topic.
This ensures that the message to work safely is loud and clear because the consequences of not working safely are clearly outlined and are simply not worth the shortcut. So, we are always harping on that and, again, most notably shown throughout our incident recreations, where the point is really driven home that even these small shortcuts can lead to big incidents.
We should always show how to avoid these incidents by doing things the right way and hammer on those corrective actions as well so that these employees know that if I follow this outline, things will probably be okay.
[00:25:26]
Absolutely. Well, I think you guys have done a really great job of summarizing the ways that you can improve safety culture, how you can spot bad safety culture, and what to do to start taking steps to put people on the right track to building a strong safety culture. We have talked a lot about how training and reinforcing that training can help build up that culture throughout the team.
So is there anything else that you guys want to say to wrap up before we sign off?
Jesse Buck: I’d just like to say safety is everybody’s job. It doesn’t matter if it’s management, supervisor level, floor level, everybody has a part to play in safety.
And I would be remiss to not mention our team as well, the training and content team, editing creative services, we couldn’t produce the training that we have without them. So in that sense, everybody is responsible for safety in any environment.
[00:26:19]
Absolutely. Well, thank you guys so much for sharing your expertise with us today. I know that episodes like this are invaluable to our listeners and people that are in the field. So we really appreciate you both taking some time out of your busy days to talk to everyone who listens to this podcast.
Jesse Romanchak: Yeah, of course. Thanks for having us and helping to make a positive impact.
Jesse Buck: Yeah, thank you very much.
Related Content
Explore more comprehensive articles, specialized guides, and insightful interviews selected, offering fresh insights, data-driven analysis, and expert perspectives.