While it may be tempting to jump straight into training when developing your Environmental Health and Safety (EHS) program, proper groundwork is essential. You need to establish your safety team, conduct initial assessments, develop written programs and policies, and complete a chemical inventory first. However, once that foundation is in place, training becomes the most critical component of your entire safety and environmental program.
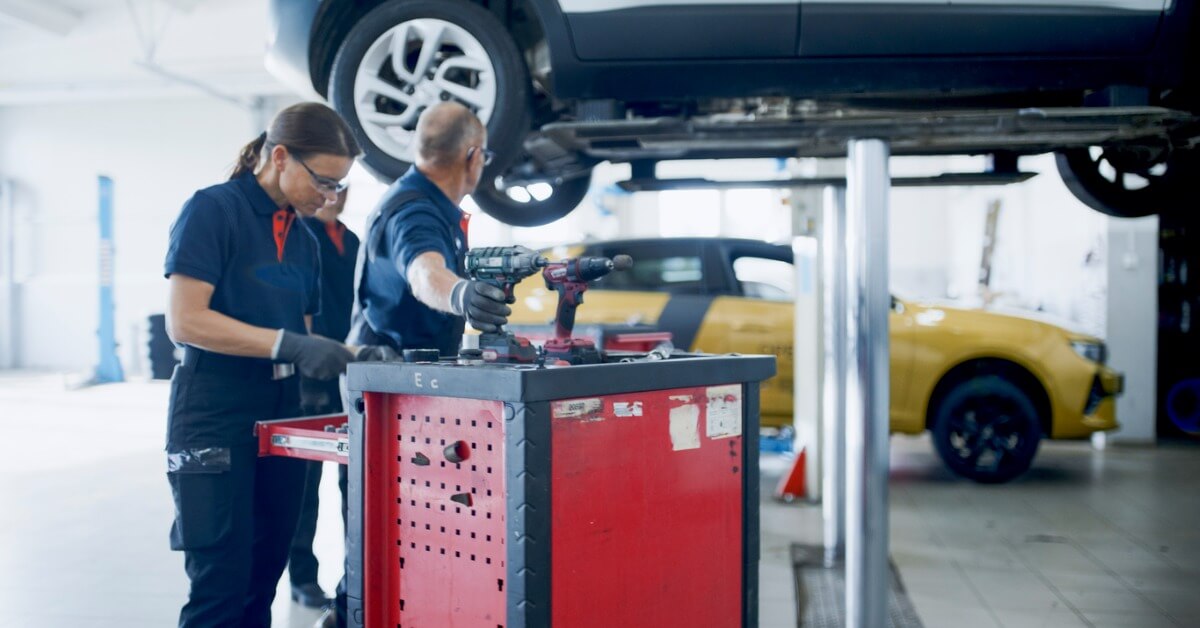
Why Training Can’t Be an Afterthought
Many organizations make the dangerous assumption that employees inherently know how to handle workplace safety situations through common sense. This couldn’t be further from the truth. Your employees need to thoroughly understand your program’s policies and procedures – and this only happens through comprehensive training.
This is especially crucial given today’s workforce demographics. In the dealership world, we’re seeing many young technicians entering the field who may think they know everything but demonstrate daily that there are significant gaps in their safety knowledge. Without proper training, these knowledge gaps create serious risks.
Real-World Examples Show Why Assumptions Are Dangerous
Let’s look at some common examples that demonstrate why we can’t assume employee knowledge:
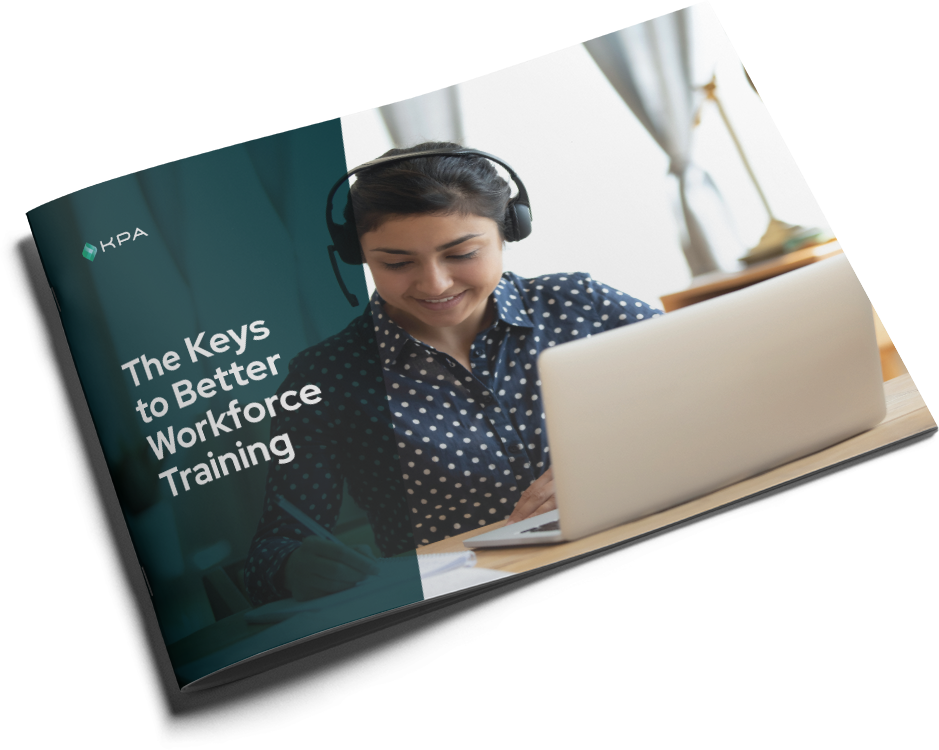
In this ebook, you’ll find the keys to effective training—the best practices for creating and delivering engaging educational content. Including ways to make training relevant, how to tailor content to different roles, and methods to reinforce that training without repetition.
New Hire Training: Start Safe from Day One
For new employees, timing is everything. All safety training should be completed before they step foot in potentially hazardous work environments. This isn’t just a best practice – it’s often a regulatory requirement. Waiting until after they’ve started working to provide safety training puts both the employee and the organization at risk.
Training Management: Why Documentation Matters
The old saying “if it’s not documented, it didn’t happen” is especially true for safety training. Yet many organizations still try to manage their training programs through spreadsheets, creating a nightmare of manual tracking and reporting. Consider what happens when you’re trying to:
- Determine who has taken which courses
- Track whose certifications have expired
- Identify who’s due for renewal
- Send notifications about upcoming requirements
A proper learning management system eliminates these headaches by:
- Automatically tracking completion status
- Generating reports of incomplete training
- Alerting when certifications are expiring
- Maintaining documentation of all training activities
The Bottom Line
Training isn’t just about checking boxes for compliance. It’s about ensuring every employee goes home safely at the end of each day. By investing in comprehensive training programs and proper training management systems, organizations can build a culture of safety that protects their most valuable asset – their people.
Complete Dealership Compliance from KPA
Keep your dealership safe from environmental factors that impact your workers’ and customers’ safety. KPA helps auto dealers maintain cultures of safety, streamline operations, and manage risk through a robust set of tools that includes a combination of consulting, training, and regulatory content.
Next Week, Let’s Look at Accident & Injury Tracking
Join us as we break down the essential steps every dealership must take to build and maintain a successful safety program. If you haven’t already, subscribe to our blog for weekly installments of the 10 steps to complete compliance.
Follow a 10-step journey to compliance.
Move your mouse over each step to learn more about each step.
Related Content
Explore more comprehensive articles, specialized guides, and insightful interviews selected, offering fresh insights, data-driven analysis, and expert perspectives.