As an EHS professional, I’ve seen firsthand how regular safety meetings can transform an organization’s safety culture. But let me be clear – I’m not talking about just having your safety team meet occasionally. A truly effective safety meeting program goes far beyond that.
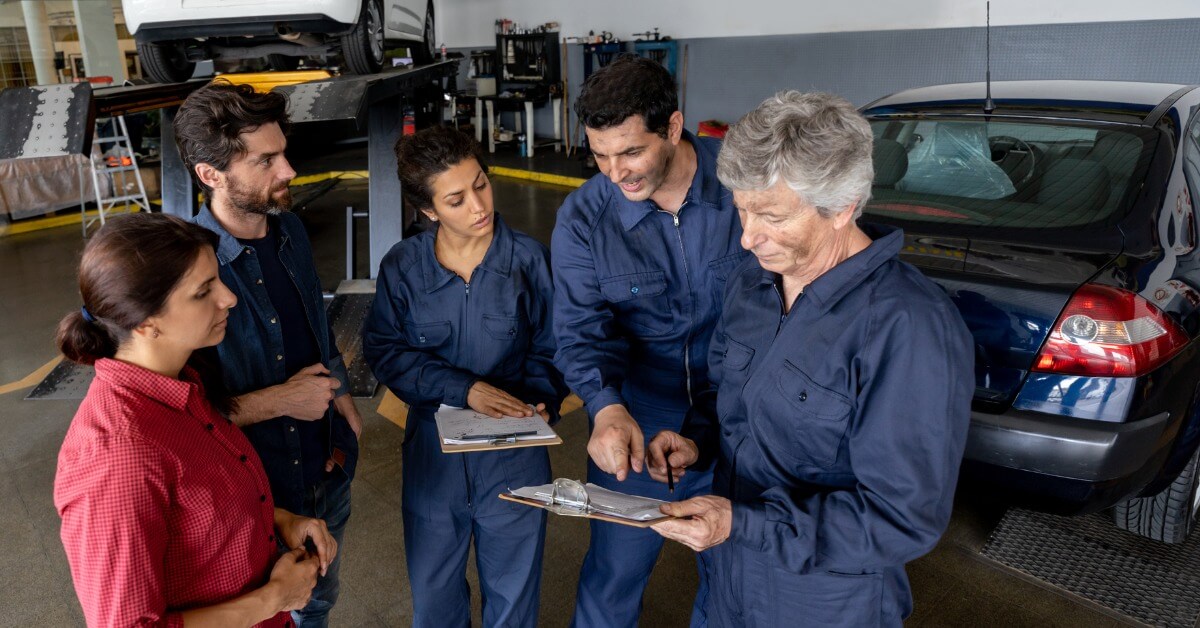
Building the Right Team
The foundation of successful safety meetings is having the right people at the table. You need representation from all shifts, all departments, all levels of management, and your line employees.
Why such a diverse group?
Each person brings a unique perspective on safety challenges. For example, someone working the day shift might identify completely different hazards than someone working the night shift due to different environmental factors and operational conditions. These varied viewpoints are crucial for comprehensive safety management.
Why Quarterly is the Minimum
I’ve seen many organizations try to get by with bi-annual or annual safety meetings, and it almost always falls apart.
Here’s what typically happens:
You meet today and create a task list. But with 180 days until your next meeting, those tasks quickly get pushed to the backburner as daily operations take precedence. There’s no sense of urgency, no accountability.
That’s why I recommend quarterly meetings at minimum, though monthly is even better. This regular cadence creates accountability – people know they’ll need to report back on their progress relatively soon. It keeps safety initiatives front and center rather than letting them fade into the background.
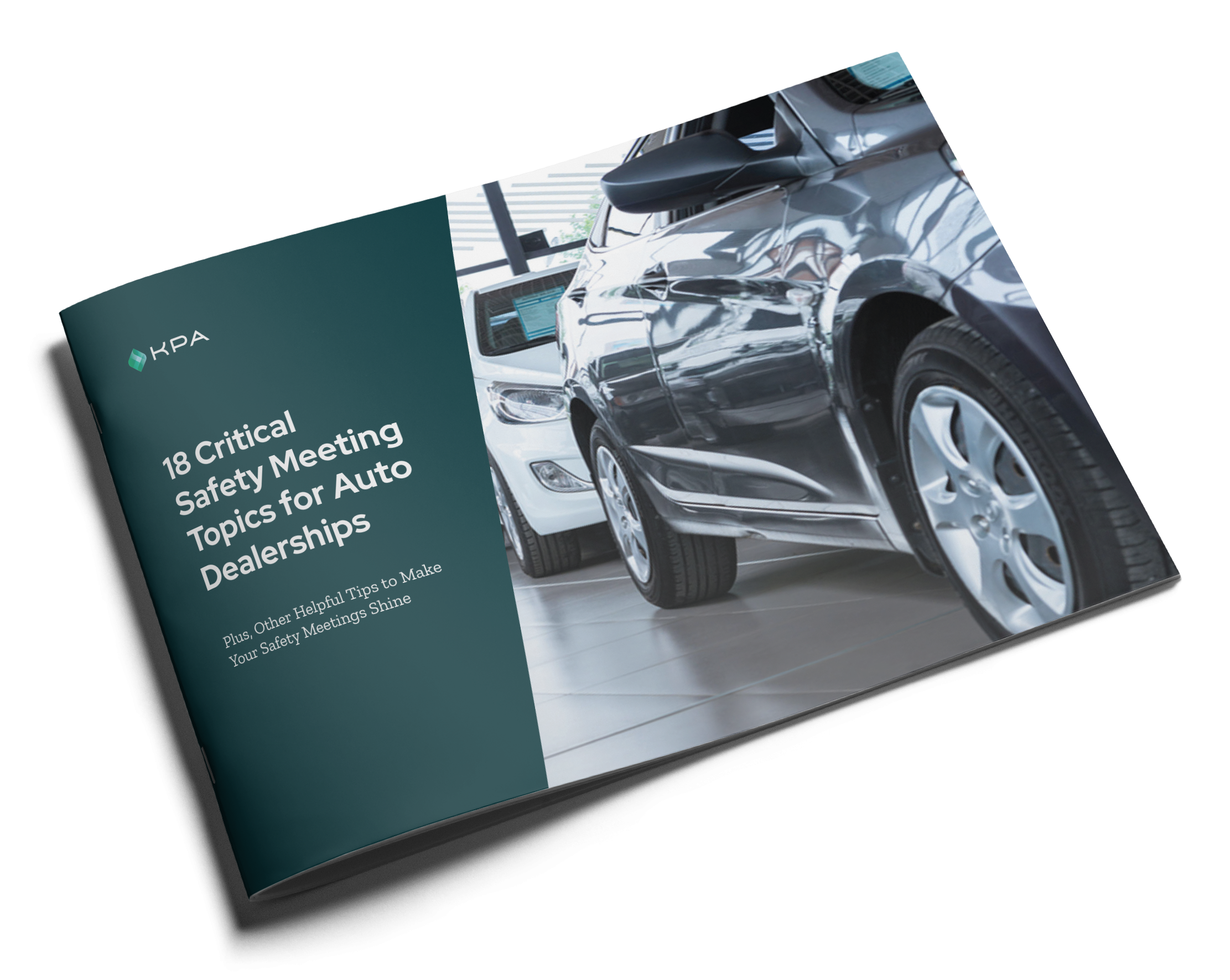
Ready to add safety meetings to your EHS arsenal? Our team is committed to helping you create a culture of safety within your organization.
Turn Safety Meetings into Lasting Success
Regular safety meetings are more than just another calendar item – they’re the engine that drives continuous safety improvement. Whether you start with quarterly meetings or jump right to monthly ones, the key is maintaining that consistent cadence, ensuring diverse representation, making data-driven decisions, and following through on action items.
The results speak for themselves: fewer incidents, better safety outcomes, and a stronger bottom line. But most importantly, you’re protecting your people and creating a workplace where safety is truly valued. Commit to regular safety meetings – your employees and your business will be better for it.
Complete Dealership Compliance from KPA
Keep your dealership safe from environmental factors that impact your workers’ and customers’ safety. KPA helps auto dealers maintain cultures of safety, streamline operations, and manage risk through a robust set of tools that includes a combination of consulting, training, and regulatory content.
Next Week, Let’s Look at Annual Reporting
Join us as we break down the essential steps every dealership must take to build and maintain a successful safety program. If you haven’t already, subscribe to our blog for weekly installments of the 10 steps to complete compliance.
Follow a 10-step journey to compliance.
Move your mouse over each step to learn more about each step.
Related Content
Explore more comprehensive articles, specialized guides, and insightful interviews selected, offering fresh insights, data-driven analysis, and expert perspectives.