“What is EHS software?”
If you’re asking this question, you’re about to transform your business. Understanding EHS software, knowing the differences between providers, and choosing the best solution can save your organization upwards of 5, 6, or 7 figures every year.
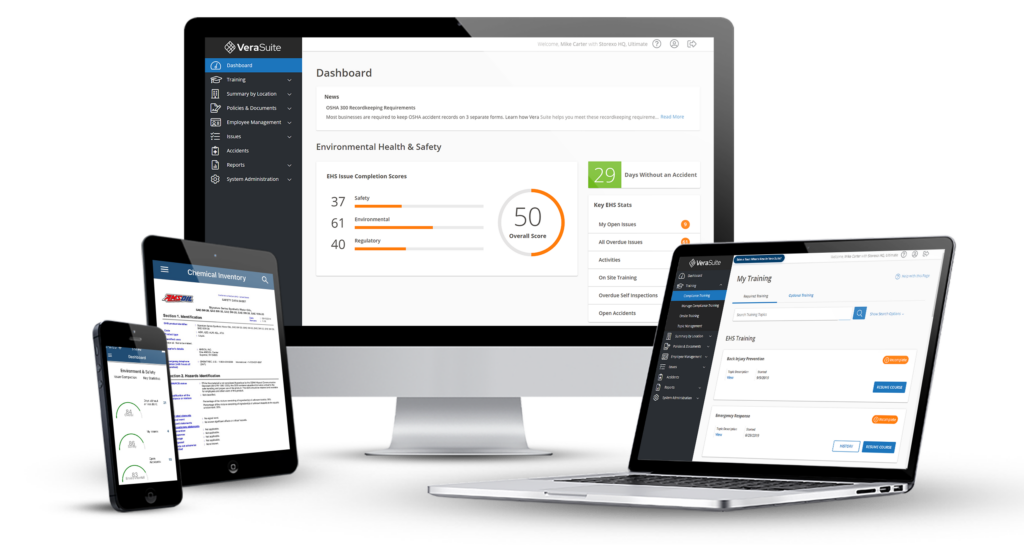
More importantly, it can save lives. EHS management software is how today’s leading organizations protect their workforces from falls, chemical spills, disease outbreaks, collisions, eye and face injuries, and other common but avoidable workplace incidents. When you use environmental health, and safety software, you not only respond to incidents as quickly and effectively as possible but also reduce the chances of incidents happening in the first place. That all adds up to serious savings, happier and healthier workers, and peace of mind for your managers and executives.
Here’s everything you need to know about EHS software—what it is, how it works, why you need it, how to choose the right provider, and more.
What Is EHS, Anyway? What Does EHS Stand For?
EHS stands for environment, health, and safety. (Some people make the E into an adjective—“environmental health and safety”—but both terms refer to the same thing.) EHS is everything an organization does to preserve the health and safety of its workers, as well as the environment—the natural world in which we live.
EHS is often used interchangeably with terms such as OHS (occupational health and safety), HSE (health, safety, and environment), and SHEQ (safety, health, environment, and quality). It’s frequently referred to as “workplace safety” or just “safety.” Basically, we’re talking about keeping people out of harm’s way while on the job.
Why Is EHS Important?
If keeping people alive and uninjured matters to you, environmental health and safety EHS should matter to you. If you neglect EHS, you’re neglecting human lives—the lives of your employees, customers, contractors, vendors, neighbors, and community members.
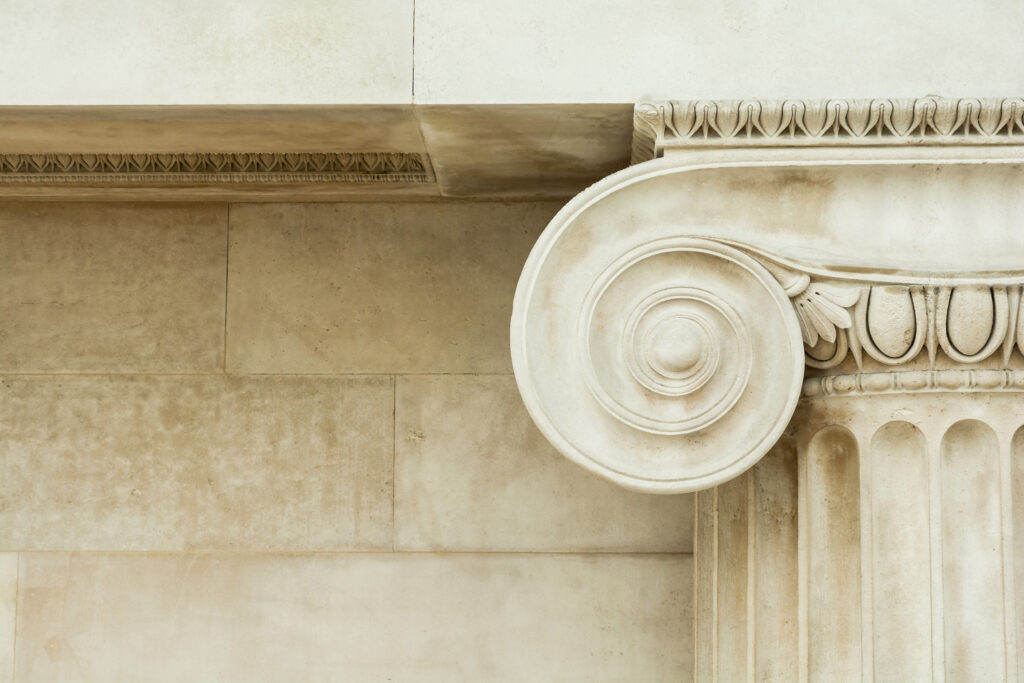
Of course, it’s not like you have a choice. Government authorities such as the Occupational Health and Safety Administration (OSHA), the Environmental Protection Agency (EPA), the Department of Justice (DOJ), and state agencies require your company to follow certain workforce safety and the environmental regulations and standards. You’ll face major bills and legal actions if you don’t. For instance, the cost of a single OSHA violation can exceed $13,000. Some incidents can result in criminal charges and even jail time. To stay on the right side of the law, you need to prove you’re playing by the rules—this is what’s known as compliance.
But beyond the fact that it’s the right and lawful thing to do, there’s a business case for leadership teams to invest in environment, health, and safety. Another way to think about environmental health and safety EHS is as risk management or loss management. Maybe the risk is a fall from a ladder, a forklift accident, a fire, a pandemic, or something else. Maybe the loss is loss of life or loss of business. In any case, the goal of EHS is to eliminate the risk and prevent the loss—or, if that’s not possible, to resolve the situation quickly, completely, and cost-effectively.
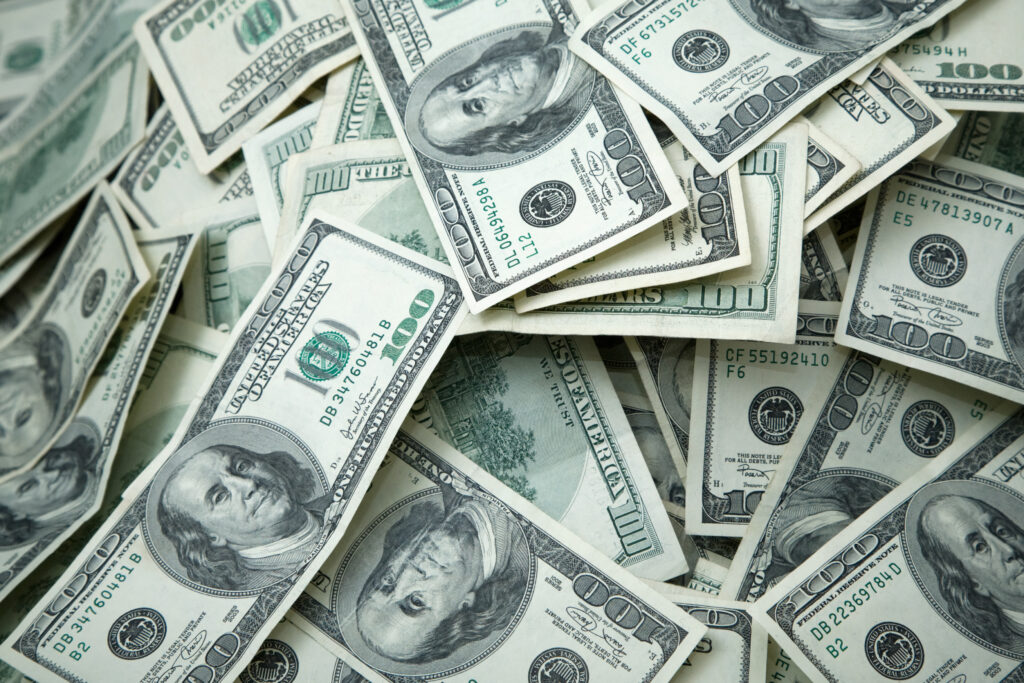
Keep in mind that every EHS risk is also a financial risk. An injury, disease, death, form of pollution or other unwanted activity in a workplace is ultimately the employer’s responsibility. And such an incident can lead to massive expenses, including…
- workers’ compensation claims
- employee absenteeism and turnover
- lost productivity
- lawsuits
- regulatory fines and penalties
- loss of equipment
- loss of materials
- negative publicity and reputational damage
- loss of customer/client trust
(Want to quantify the ROI of safety? We’ve created an ROI calculator you can use to find out, as well as a free white paper on the subject.)
If you want to avoid any of the above, you need to prioritize EHS—and you need to invest in EHS risk management software.
Why Does Software Matter?
For years, organizations had no choice but to manage EHS manually. Every time a worker was injured or got sick, every time a business polluted the environment, someone had to carefully inspect the situation, assess the damage, cross-reference company policies and regulatory materials, and document the incident by hand. Paper records were stored in spreadsheets and filing cabinets. Key information had to be dug up from binders, assuming it was even documented anywhere at all; often, the only source of information was a person’s brain.
This made it virtually impossible for organizations to ensure EHS visibility and consistency across time, departments, and locations. There were few reliable ways to track risk and compliance, let alone improve performance. Different people and groups might be following different versions of rules and policies. Not everyone underwent the same training. Tasks may go uncompleted for long periods of time. Bottlenecks were everywhere. Too often, if a safety manager left the company or was absent, other employees had to step in and figure things out, leading to potentially life-threatening delays and errors in responding to and reporting incidents.
Some companies still do things the manual way, either because they think it’s their only option or because they assume EHS compliance software is too expensive and not worth the cost. Unfortunately, these companies are putting their workers and their bottom lines at risk.
In 2020, EHS is more complicated than ever. And it’s growing in complexity every day thanks to a constant stream of new technologies, regulations, guidelines, and realities of doing business.
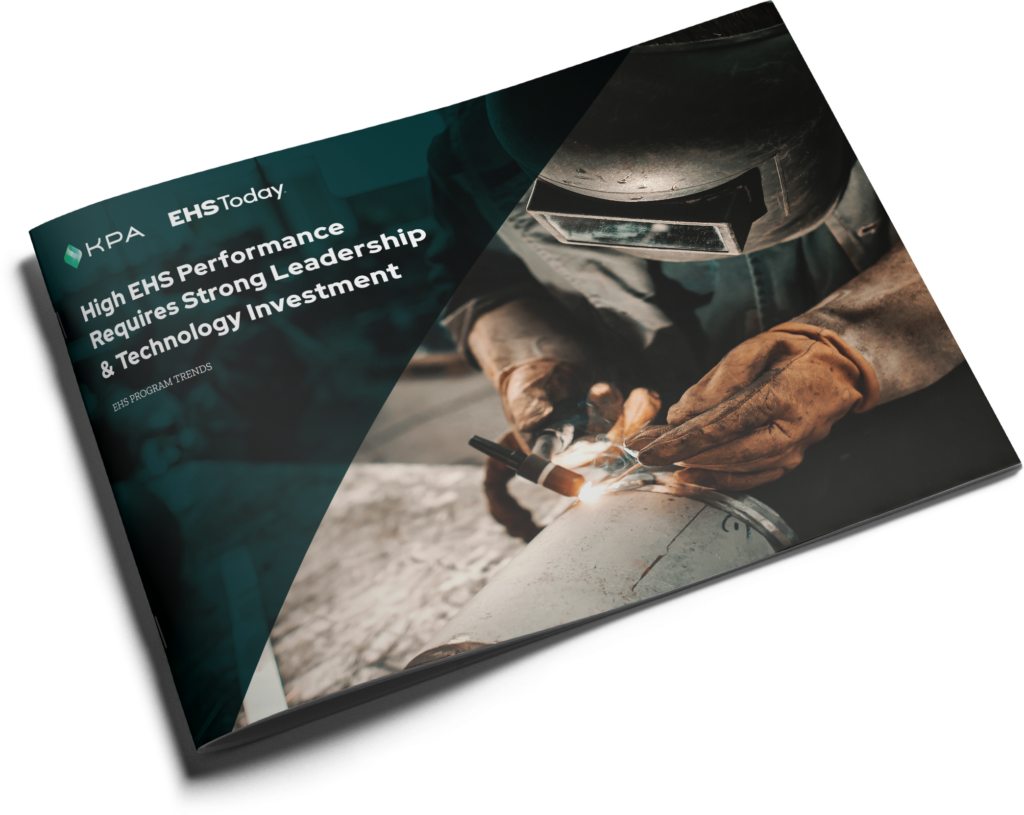
Organizations that do things manually also tend to underperform their competitors. KPA and EHS Today’s 2019 State of the Industry: EHS Program Trends report found that the companies with higher-than-average injury and incident rates are the ones that don’t prioritize their EHS programs. Poor performers frequently rely on manual EHS processes, and any efforts to improve their programs receive little support or buy-in from executives. As a result, their workforces experience unacceptably high numbers of injuries and illnesses, with the situation remaining as bad or getting worse as the years go by.
EHS management software makes it possible—even easy—to stay on top of everything.
What Does It Do? How Does It Work?
EHS software standardizes, simplifies, and automates environment, health, and safety activities. It brings all your EHS program data and activities into a single, comprehensive location, so you can see how things are going, reference regulatory information and policies, and take action in just a few clicks. This reduces gaps and errors, as well as busywork and guesswork. You don’t need to spend time hunting down forms, run around checking on things constantly, or lose sleep worrying whether employees are following the rules and staying safe.
software-based EHS systems make processes such as the following as easy and accurate as possible:
- incident management
- assigning corrective and preventive actions
- recordkeeping while reducing data entry
- safety data sheet (SDS) management
- workforce training
- reporting
- incident and trend analysis
- audits and inspections
Beyond its time- and error-saving capabilities, EHS systems empower better decision-making. You can use it to keep track of what you’re spending and where along with what groups and processes are falling short: Are there specific risk, compliance, and safety practices that employees are struggling with? Are certain departments or teams lagging behind?
20 Things You Can Do Easily With Health & Safety Software
1. Perform facility audits.
2. Record all work-related injuries, illnesses, and accidents.
3. Use data to conduct root-cause analyses and prevent future incidents.
4. Reference results of regular safety observations.
5. Document safety committee meetings.
6. Assign workers to fix malfunctioning equipment.
7. See all open EHS issues in real-time.
8. Follow up on assigned tasks.
9. Receive alerts when tasks are completed or overdue to ensure compliance.
10. Manage workers’ compensation claims.
11. Train new hires.
12. Run annual refresher training.
13. Check training records.
14. Receive updates about new regulations and rule changes.
15. Educate workers on regulatory updates.
16. Fill out OSHA 300, 300A, and 301 Forms.
17. View your chemical inventory.
18. Find and address missing SDS information.
19. Assess the status of personal protective equipment (PPE).
20. Generate compliance reports.
Why Use EHS Software?
There are countless reasons, here are just a few:
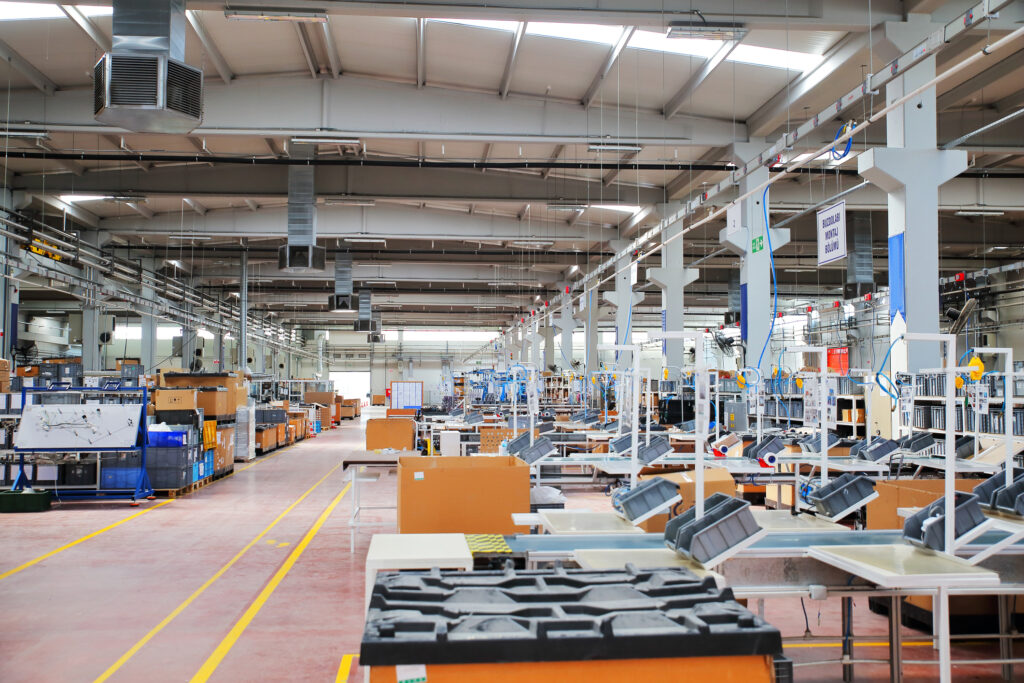
You’ll have fewer workplace injuries and illnesses. This is the big one. You need a reliable, easy way to track and address EHS issues—ideally before they become incidents.
You’ll save money. Lower workers’ compensation costs, fewer penalties, fewer legal fees, less employee turnover—by reducing incidents, EHS compliance software also reduces the expenses associated with incidents.
You’ll improve productivity and efficiency. For one, fewer injuries mean fewer disruptions, fewer lost hours, and fewer days away from work. Moreover, this software eliminates unnecessary tasks, so safety and compliance professionals have more time to focus on what matters.
You’ll make smarter decisions. With comprehensive, up-to-the-minute data at your fingertips, you can zero in on existing issues and correct them before they develop into larger problems. You can also track what programs work and apply elements of those programs to areas that need improvement.
You’ll avoid compliance headaches. Activities such as audits and OSHA reporting can be a pain, both in terms of time and money spent. EHS based software makes it easy to keep investigators and regulators happy—without needless hours spent working on spreadsheets.
You’ll gain a competitive edge. Better hiring, retention, reputation, and morale are all-natural consequences of a good EHS management system. Plus, the money you save by avoiding incidents and automating compliance can be used to improve products, services, or business processes—or passed along to your customers or clients as upfront savings.
Who Uses EHS Software?
Companies of all sizes and industries rely on EHS management software to manage their key safety and compliance processes. Generally speaking, the bigger and more heavily-regulated the organization, the more important it is to use safety compliance software.
Here are a few examples of organizations that put industrial hygiene first and frequently make use of ehs software:
- manufacturing
- food and beverages
- trucking and transportation
- warehousing and distribution
- construction
- automotive
- oil and gas
- utilities
- technology
- engineering
- forestry and agriculture
- medical
- aviation and aerospace
- mining
- retail
How Much Does EHS Software Cost?
EHS software solutions range considerably in cost and cost structure. On the low end are systems priced at a few thousand dollars; on the high end, organizations can expect to pay millions.
Solutions are usually offered through the software-as-a-service (SaaS) model, where users pay a monthly or annual subscription fee to access the software.
Some solutions are white-label, meaning they’re packaged and sold by parties other than the actual technology provider. For instance, Environment health, and safety software company might sell its solution to a commercial insurance broker, who brands the technology and offers it to their clients as part of their insurance package or as an add-on product.
But regardless of the cost or pricing model, people new to web-based safety software usually share the same core question: Is the cost of EHS software worth it? As you might imagine, the answer here depends largely on the solution itself, which brings us to our next question…
How Do EHS Software Solutions Differ?
There are plenty of EHS solutions out there. Some are certainly better—more flexible, intuitive, and feature-rich—than others, but to answer the question above: they’re almost always worth it. Any EHS software solution is better than nothing.
That said, it’s important to find the solution that’s scaled for your organization and built for your needs.
Some organizations develop their own systems. Others buy pre-made software. Unless you run an enterprise technology company or have relatively few EHS needs, the latter is usually a better idea.
Most EHS software solutions offer the same basic features: a dashboard, a document library, corrective actions, and reports. Other elements can vary significantly.
Here are a few variables to pay attention to when looking at competing solutions:
- cost
- mobile access
- ease of use
- quality of training
- customizability
- level of support
Many EHS management system providers will work closely with you to configure the solution and get it up and running at your organization. A good number of these companies (including KPA) pair their technology with consulting services, tailoring everything to the client’s needs. This is the nature of the business If a software provider expects you to use their solution off the shelf with little support, consider that a red flag.
Nonetheless, even in close partnerships between providers and users, failures do happen. A company buys a software solution and little changes. Incidents continue to occur, workers don’t get trained consistently, and so on. This is almost always a problem of implementation rather than a problem with the technology itself. Organizational leadership jumps in too quickly, sets unrealistic goals, or assumes the new system should “just work” with little configuration and human involvement.
How to Evaluate an EHS Software Solution:
4 Questions to Ask
Ultimately, the best EHS software is employee-centric. It generates better safety outcomes because it’s easy to use and people have an incentive to use it. In other words, a system needs to be built for your workforce. If it’s too complicated, unwieldy, or unintuitive—if it doesn’t align with their existing workflows—they won’t use it.
To determine if a solution is the right fit for your people, ask the following questions:

1. Are self-guided forms available? EHS reporting should take minimal time and effort on the employee’s part.
2. Can every user access forms and an information library? If the system creates silos, it’s hardly better than a spreadsheets-and-binders approach.
3. Is the solution mobile-ready? Business today happens on phones. Any employee should be able to quickly pull out their mobile device and enter information at a moment’s notice.
4. Are data dashboards included? Any software you purchase should have strong reporting and dashboard capabilities. Again, ease of use is critical. Keep in mind that EHS might not be a user’s only job. When someone’s busy, they should be able to log in and find the exact data information they need, when they need it.
How to Get Started With EHS Software
Here’s how to implement EHS technology to maximize adoption and minimize frustration:
1. Gather all the EHS information you currently have. If you don’t know where you’re starting from, you can’t chart where you’re going. Before you can say goodbye to the binders and spreadsheets, you’ll need to collect their data. Think of it as a treasure hunt—a mission to seek and out and find all that deep-buried EHS information. Keep in mind that some of this information may not exist in readily available files. Sometimes it’s kept in a single employee’s desk drawer, or locked inside your organization’s institutional memory.
2. Develop a reasonable implementation timeline and scope. In general, projects fail for two reasons: they’re either too grandiose or too ambiguous. You can’t transform your organization’s EHS processes in the span of a day or week. A 90-day timeline is more realistic—but your organization may need more time than that depending on your current situation.
3. Have a good project plan. Once you’ve analyzed and scoped the project, break it down into manageable, measurable goals. Team members will need to agree on these goals and hold themselves and others accountable for achieving them. People should know what they’re responsible for doing and when, as well as the task’s order in the overall project timeline. Project owners are usually necessary. For instance, you may assign one person to collect the various checklists, another person to manage user registration, a third person to train the workforce on the usage of the system, and a fourth to translate paper materials into online tools for audits and incident management. Procedures, schedules, and roles vary from organization to organization—one size doesn’t fit all. But whatever shape it takes, the plan needs to align with the organization’s larger objectives and resources.
4. Ensure buy-in from leadership. Executive sponsorship of the new EHS management system is a must. It’s perhaps the most critical factor in the success or failure of implementation. A statement from the CEO or EVP isn’t enough. A leader must be willing to show up to the meetings, remove bottlenecks, and demonstrate ownership of the system.
To ensure end-users actually use the new system, it’s important to look outside of the EHS department. Executive sponsorship is most powerful when it comes from someone without “safety” in their job title. When a company president or operations VP communicates that the new system is a key initiative, other people listen.
Cross-functional teams and sponsorship can help break down the barriers for other departments to understand why the change is happening. It’s about communicating that safety is important and easy to accomplish.
Industry-Leading EHS Software from KPA
KPA is the leading provider of EHS and workforce compliance software and services for mid-sized companies. KPA combines innovative cloud software, online training, and on-site audit and loss control services to help over 10,000 client locations achieve regulatory compliance, control risk, protect assets, and retain top talent. With our solutions, you can hire, onboard, educate, and inform your employees from one place to ensure full participation in your safety and compliance culture.
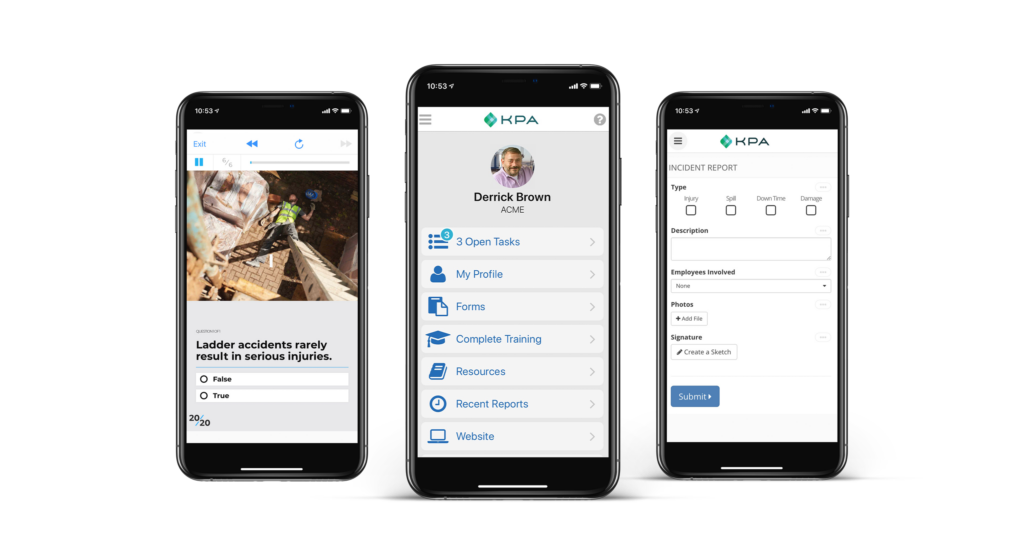
KPA EHS: The Backbone of Your Compliance Program
With KPA EHS, you can…
- Automate manual processes. With KPA’s EHS and workforce compliance software platform, you’ll spend less time on paperwork, spreadsheets, and reporting and have more time to spend in the field with your team: conducting inspections, audits, safety meetings, and training employees.
- Reduce the total cost of risk. Workplace accidents and injuries, worker’s comp costs, and insurance premiums all contribute to your total cost of risk. KPA helps you control those costs by keeping your workforce in compliance with OSHA, EPA, Department of Labor, Department of Transportation, and other regulatory standards, in addition to reducing risk for your workforce.
- Manage safety in one comprehensive platform In Vera EHS, employees log in to a user-friendly interface and complete safety training, access Safety Data Sheets, read and understand policies, and report incidents and accidents. Managers can track inspection results, employee training records, accidents, and overall compliance status. Safety managers can complete audits and corrective actions and then view a roll-up of these activities that can be compared across departments or facilities.
Check out our Compliance Training Library
With these insights, program managers have a complete view of safety trends and areas where they can improve. And they have the peace of mind that nothing falls through the cracks.
Key Features
Get Started with KPA
Want to learn more about KPA EHS? Curious about how KPA’s EHS technology can transform your organization? Give us a call at 866-356-1735, or send us an email at info@kpa.io.
Ready to see our solution for yourself? Click here to see a demo.