Employees have the right to know what chemicals they could potentially be exposed to and what hazards those could bring to them from a physical standpoint, from a health standpoint, from an environmental standpoint. That’s the premise behind OSHA’s Hazard Communication Standard, and one of the reasons Safety Data Sheets are top of mind for safety professionals.
What is a Safety Data Sheet?
Safety Data Sheets (or SDS for short) are the source of detailed information on hazardous chemicals. This includes information for many different audiences: employers, employees, safety and health professionals, emergency responders, government agencies, and consumers. The information of immediate use to exposed workers and emergency responders is at the beginning of the SDS, while the more technical information is located in the later sections.
Employers must maintain an SDS for each hazardous chemical they use. Employers must also ensure that these SDSs are readily accessible to employees.
Employers Must Maintain a Safety Data Sheet for Each Hazardous Chemical
Employers must maintain the current version of the SDS for each hazardous chemical in that workplace, make sure that they’re readily available for all employees. , and of course and constantly maintain the most current and up-to-date version.
If you receive a hazardous chemical from a supplier or manufacturer without an SDS, request one as soon as possible. If you receive a new SDS, you must maintain it and make it available to employees.
Why is Maintaining SDSs Important?
Here’s a hypothetical situation for you:
Let’s say you have an employee who was exposed to Clorox Bleach. But the information the triage team’s working with is from of an SDS from when they first added it to the company’s chemical inventory in 2016.
The risk is that you might be working with old information. Clorox might have tweaked their formula since then, or there might be something new that needs to happen, especially from a first aid response situation. And working off of old information, that could be very dangerous for the employee when you’re trying to provide care.
Keep SDSs Readily Available for Employees
Some employers keep the SDSs in a binder in a central location, while others provide access electronically. No matter what system you use, employers must ensure that employees and medical personnel can immediately obtain the required information in an emergency.
What OSHA Looks for:
- Availability of an SDS for each hazardous chemical in the workplace
- Designation of the person(s) responsible for obtaining and maintaining the SDSs
- How SDSs are maintained in the workplace (e.g., in binders or electronically), and how employees can access them in their work areas
- Procedures to follow when you don’t receive an SDS at the time of the first shipment
- Training of employees that includes a review of SDS format and use
Why a Digital SDS Library Beats the Old 3-Ring Binder
You might’ve seen these in facilities in the past…an SDS book sitting in a three-ring binder stuck to the wall of your facility.
Keeping these binders up to date is a very manual process.
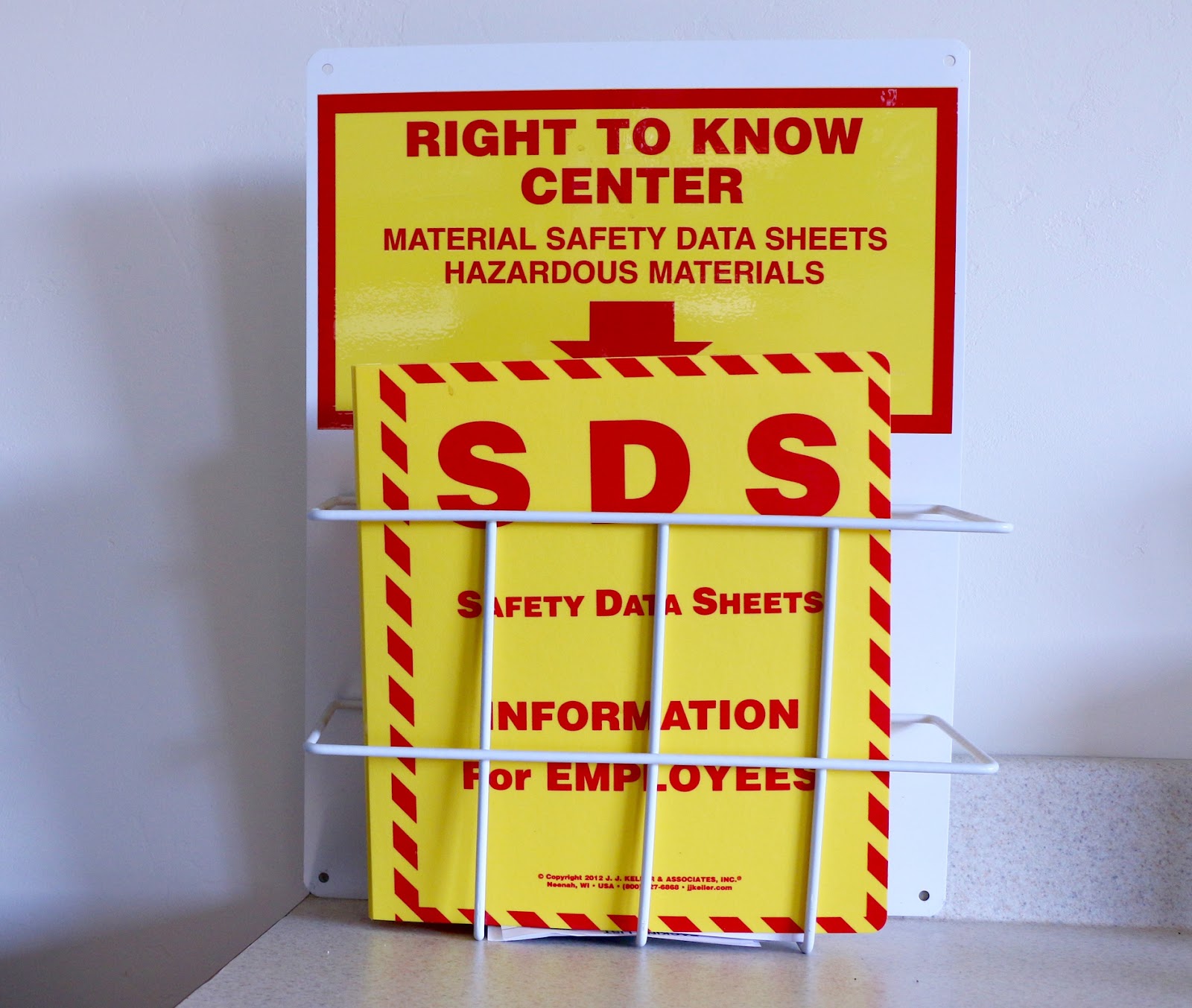
Does your process for keeping your SDS up-to-date look like this?
“We had this annual process in place where once a year, we’d go back through and review, not only the SDSs that we had in place right now to make sure that the ones that we have were still current and up-to-date. And if they weren’t that we were going out and searching, just Googling or go to the manufacturer’s website or things like that to find current versions of those.
We were literally printing off SDSs on paper and trying to keep them organized in alphabetical order. But also too, adding in new ones for something new that we might be using that we didn’t have in there right now.
And the challenge became, that did our annual review in January across all 20+ of our locations around the country. But then a chemical that we use on a regular basis comes out with a new version of their SDS in March. Well, we’re not going to catch that again until the following January. So now we’re working for 10 months on old information. Not only is that dangerous but it’s incredibly time consuming.”
One of the benefits of a digital SDS library is the ability to build your library from a full database of SDSs (KPA’s contains over 70 million). Google begone. And, when an SDS is updated, the system automatically distributes the new version to your library.
One more challenge for SDS binders – a distributed workforce.
OSHA specifies that we make SDSs available to all employees at all times, right? Well, that three-ring binder that’s stuck on the wall can’t travel in 10 different trucks all around the state as your employees are going about their work day. One more reason a digital SDS library makes your company safer and more efficient.
Create a safer workplace with easy access to your Safety Data Sheets. KPA can help.
With SDS Manager:
- Safety Managers import SDSs from a database of over 70 Million SDSs to
- create a customized library.
- Employees access SDSs within seconds – even when offline or in the field.
- Print pre-populated secondary container labels for GHS compliance.
- Comply with OSHA’s Right to Know and Hazcom requirements.
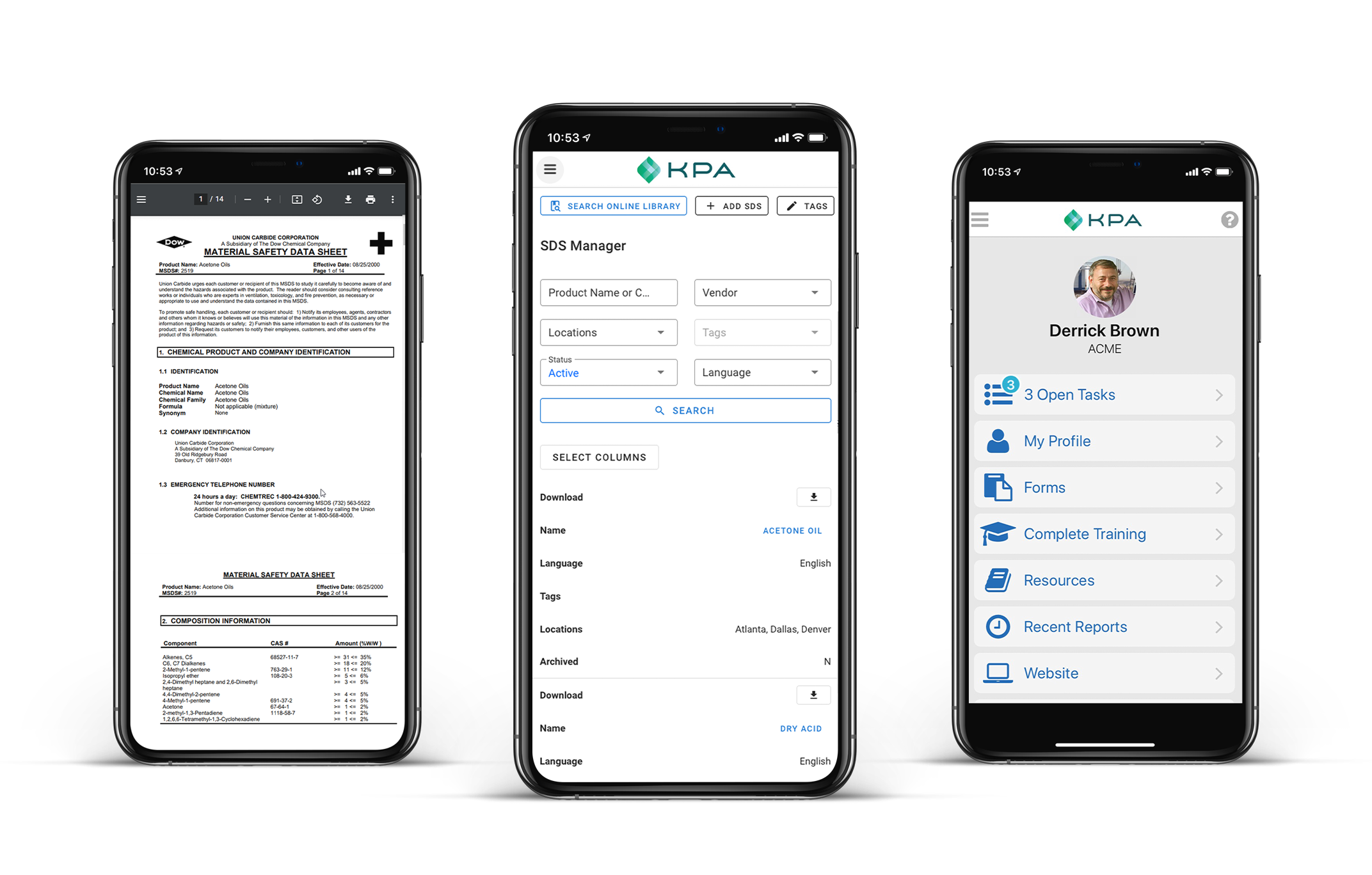