In the post, “Tips to Reduce Fire and Storage Hazards in Your Dealership,” we identified the steps a dealership can take to reduce the risks associated with electric vehicle (EV) fires and battery storage. Some of those solutions may not be feasible for every electric vehicle and every dealership. That means you need a way to determine which batteries pose more risk than others so that you can classify them as critical risk, high risk, or average risk.
Assessing high-voltage lithium-ion EV batteries isn’t the easiest task, but we’ll break it down for you. Let’s start first with understanding how EV batteries are constructed.
EV Battery Components
For the purposes of this discussion, the most important parts of the battery are the cells, modules, cooling system, casing, and battery management system.
Cells
An EV’s energy is stored in the battery cells. Each cell consists of two electrodes that collect current: an anode, which is positively charged, and a cathode, which is negatively charged. A solution called electrolyte separates the anode and cathode and transports positively charged ions between the cathode and anode terminals. When the battery is charging, lithium ions move from the anode to the cathode and store energy. When the battery is in use, lithium ions move from the cathode to the anode and discharge energy. The flow of ions is called electricity, which powers the motor.
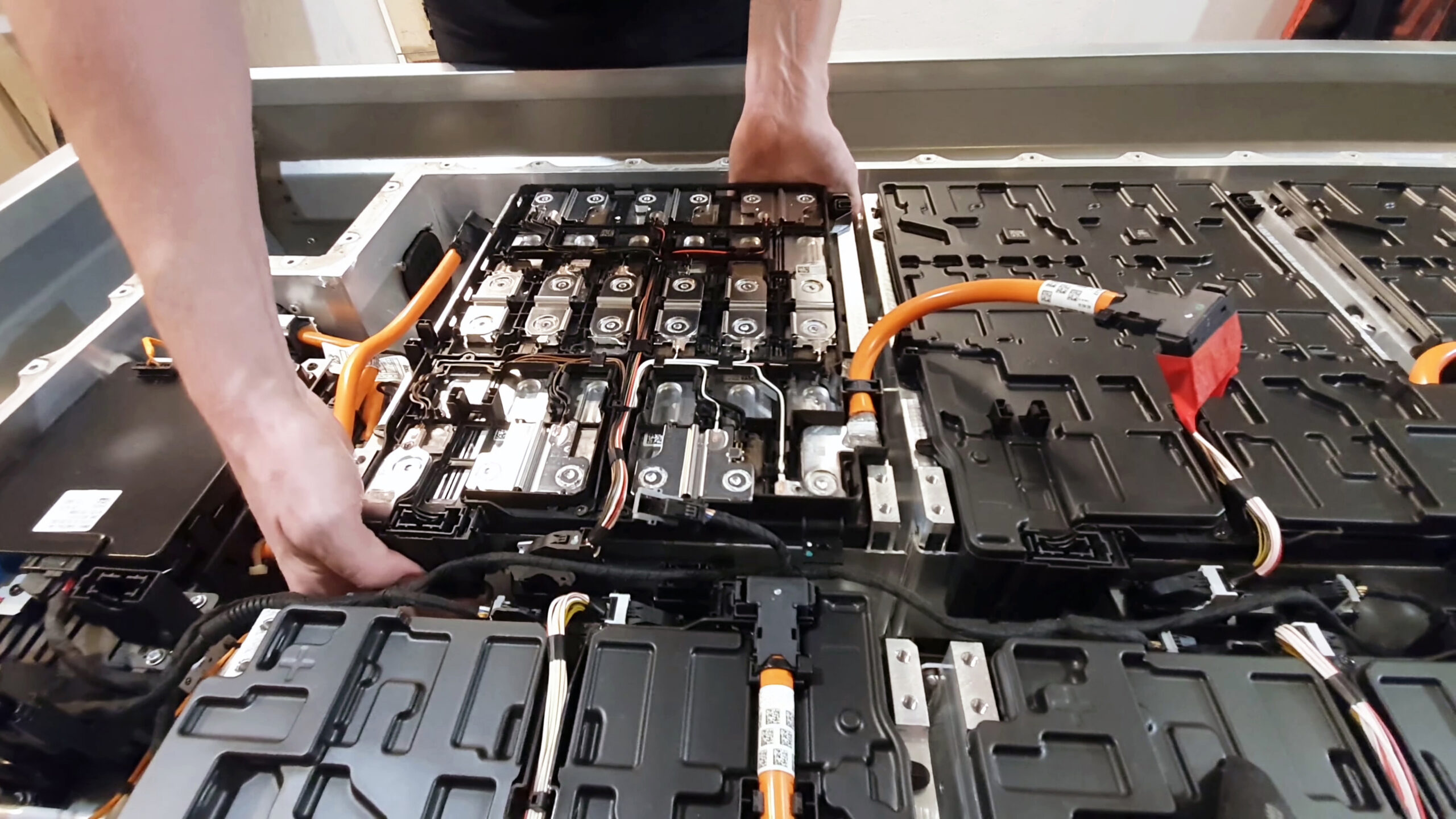
Modules
The battery manufacturer stores groups of cells in compact containers called modules, packs, or jars. These containers can look very different, depending on the battery manufacturer. From here forward, we refer to them simply as “modules.”
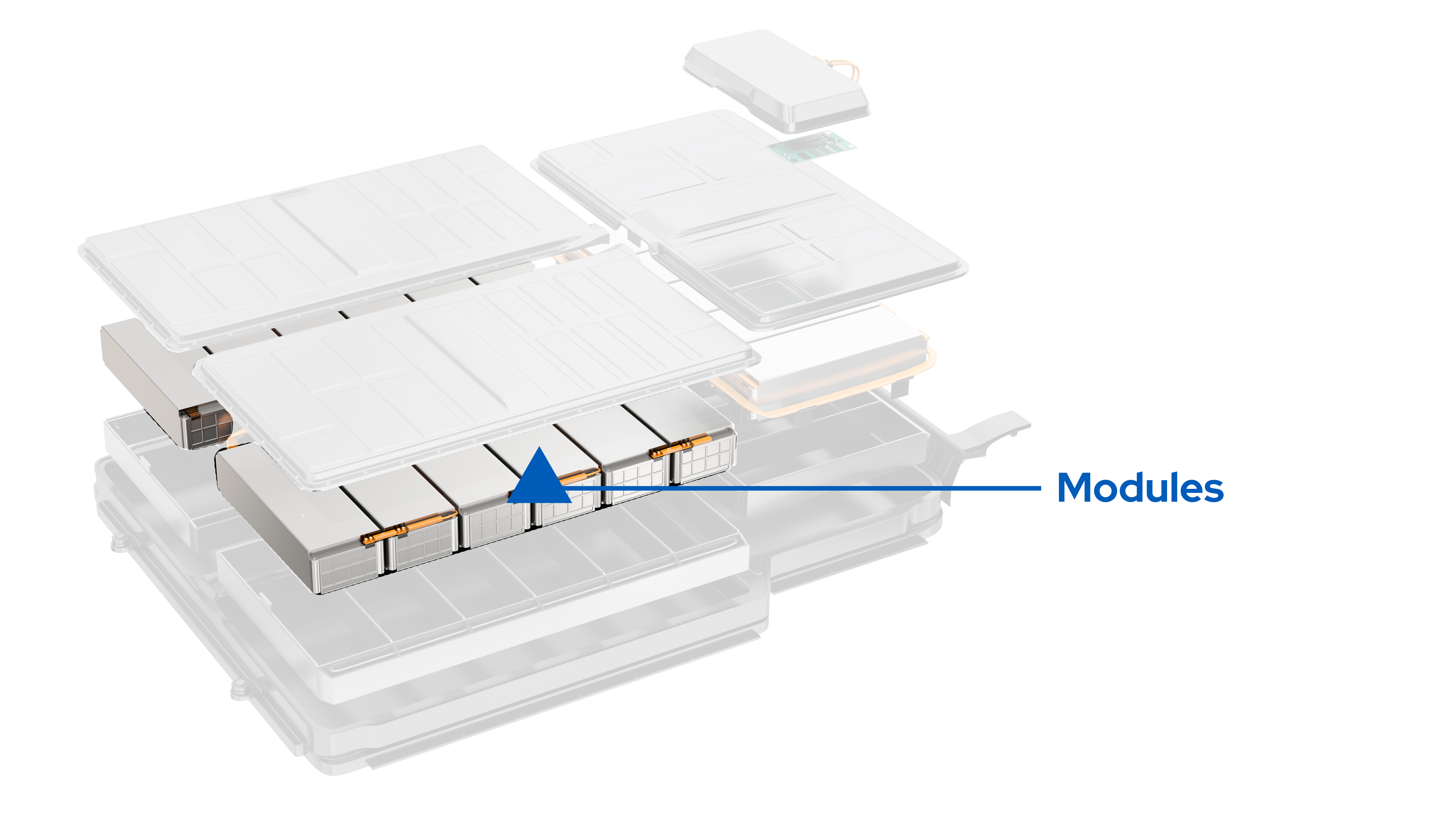
Cooling System
Energy discharge from lithium-ion batteries creates a great deal of heat. Electric vehicles are equipped with cooling systems that transfer heat away from the modules, similar to the traditional antifreeze/coolant systems in internal combustion engine vehicles.
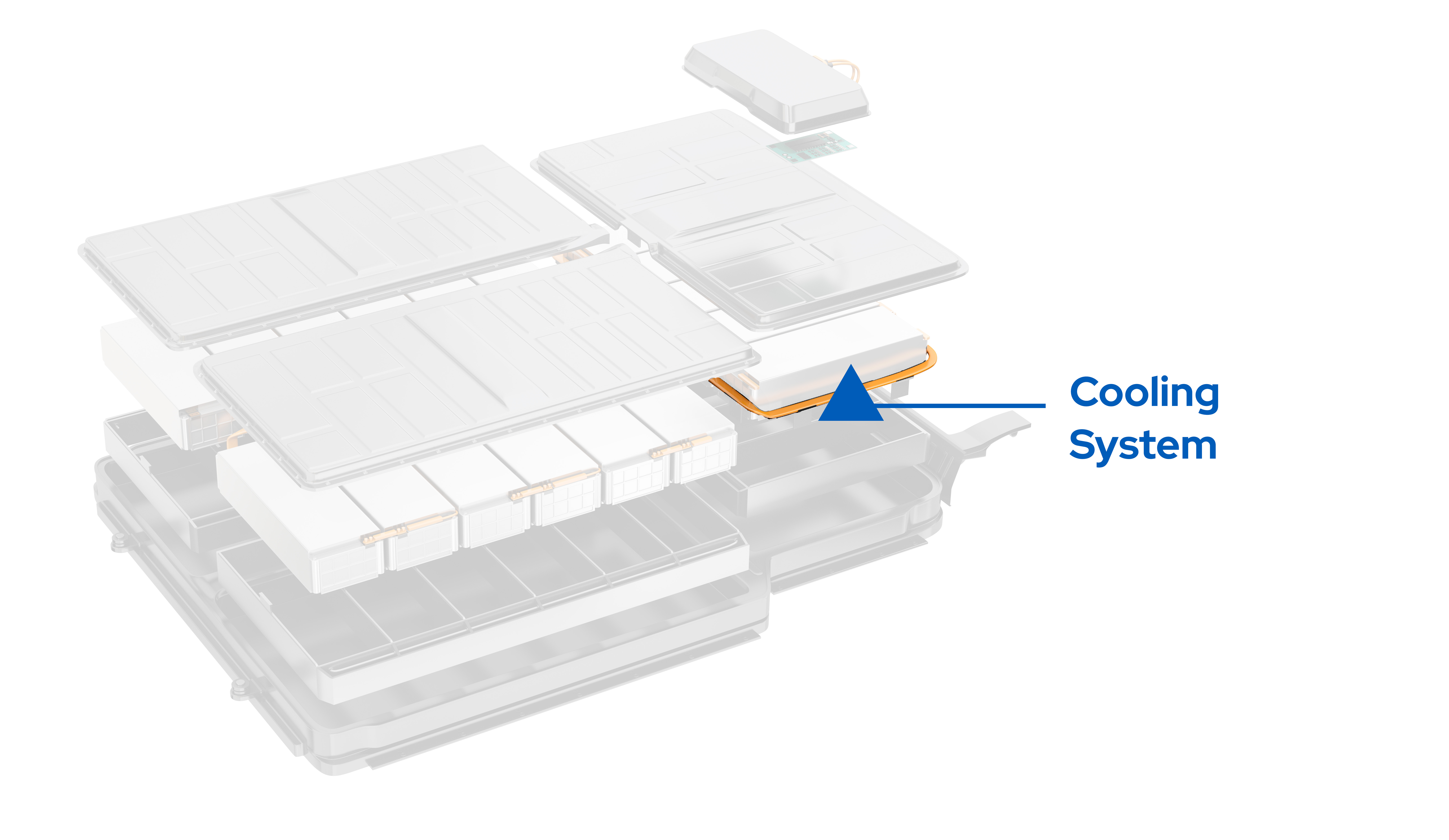
Casing
Cells, modules, and the cooling system are enclosed in a protective casing. This casing is designed to protect the modules from impact, chemicals, vehicle heat, environmental heat, and structural damage.
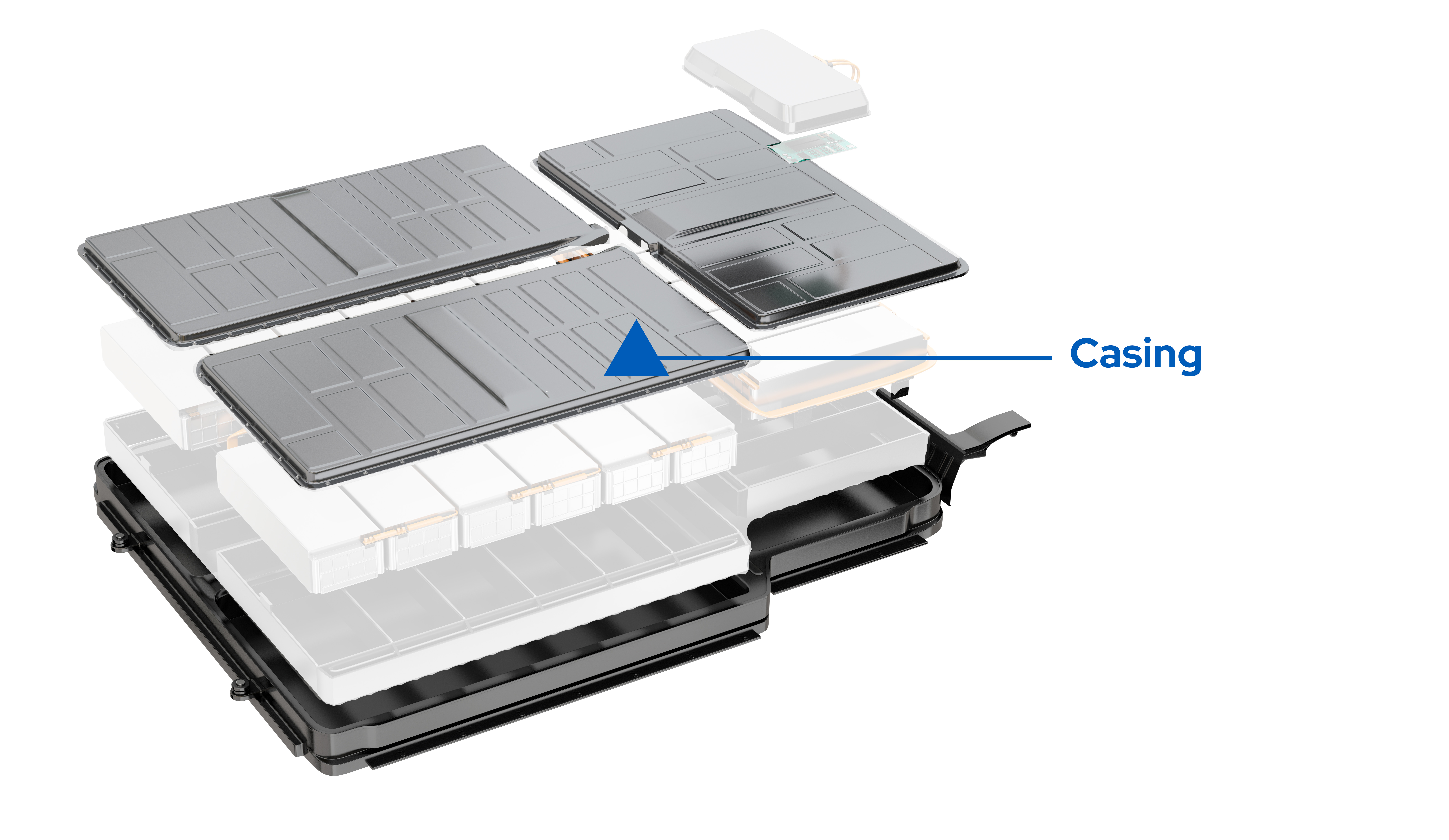
Battery Management System
A battery management system (BMS) is the “onboard computer.” Its sensors communicate with the vehicle to ensure proper operation of the battery, the components powered by the battery, and the battery’s interface with its energy supplies. Without a BMS, the battery system will not function as intended.
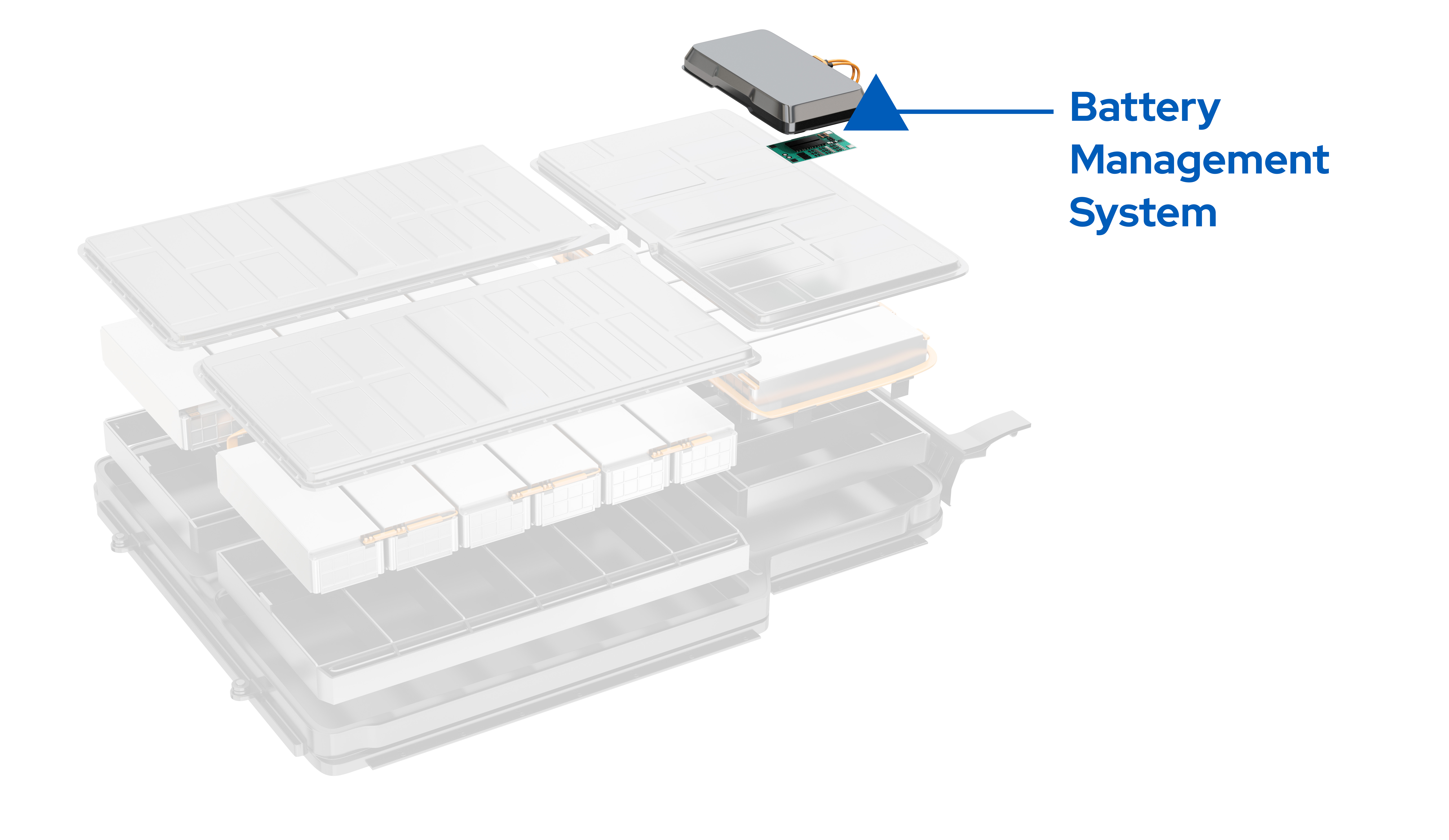
Now that you know the basic components of an EV battery, we’ll teach you the steps you need to take when inspecting and assessing:
- A battery that’s inside a vehicle;
- A battery that’s ready to be installed; and
- A battery that needs to be packaged and shipped offsite.
If you haven’t already, subscribe to the blog, and we’ll send these articles right to your inbox.
Stay on top of EV requirements with KPA, the nation’s leader in automotive compliance solutions.
KPA has an EV compliance solution designed to help you prepare your facility, educate your staff, and document/maintain OSHA compliance.
In addition to addressing general awareness about EVs, KPA is developing a monthly series of self-directed training programs for supervisors to train their staff. Topics will range from EV battery hazards, including fire risks and proper storage, electrical hazards, personal protective equipment, de-energization, stranded energy, and more. These tools, along with on-site consulting and additional EV compliance content, will comprise KPA’s comprehensive EV Compliance Solution, available this fall.