During their dealership inspections, KPA consultants routinely observe and document activities that could be considered unsafe.
Some of the most problematic employee behaviors stem from complacency, particularly among technicians who often perform repetitive tasks.
Unfortunately, this can have dire consequences when one of the most dangerous pieces of equipment a technician works with is the one lifted above their head many times a day.
KPA consultants catch lift safety infractions entirely too often when walking the shop floor.
They find things like:
- Techs NOT completing a “shake test” prior to fully lifting a vehicle
- Hearing the safety locks click, but the technician does NOT lower the vehicle on a lock when finished
- Bungee cords or screwdrivers disabling safety locks altogether
- Missing cotter pins
Even ONE or ONE TIME is too many. Unfortunately, this scenario can become a reality, as seen in a recent tragic incident.
A technician had been killed in a lift accident. The tech had been guiding a truck with transmission issues onto a runway lift, and, when the transmission caught, the truck lurched forward towards him and the wall behind him.
Our hearts go out to the technician’s family and friends. It is unfortunate that anyone should not be able to return home safely from their workplace on a daily basis.
This is an important story to share – not to scare employees or sensationalize someone’s pain. It’s a sober reminder that there are risks associated with working with vehicle lifts if certain rules and precautions are not taken.
What can you do to keep your shop safe when it comes to lift safety?
Below are three areas you will want to make sure are covered.
Annual Auto Lift Inspections and Maintenance
When were your lifts last inspected, and where is the documentation?
OSHA does not have a particular set of regulations dealing with automotive lifts, so the regulatory agency defers to another set of rules; the ANSI Standards.
The ANSI Standards mandate that a “qualified” lift inspector inspect all vehicle lifts at least annually. The inspector should be Automotive Lift Institute (ALI) certified as independently verified through the ALI Lift Inspector Certification Program. There is even a tool that will verify inspectors within a several-mile radius of your location.
The Inspector should tag every lift for easy verification of annual certification and give you a comprehensive inspection report. Each lift should have a completed report, and any repairs should be made immediately to keep the lifts compliant.
Keep in mind that an invoice for lift repairs is not considered adequate documentation of a thorough inspection.
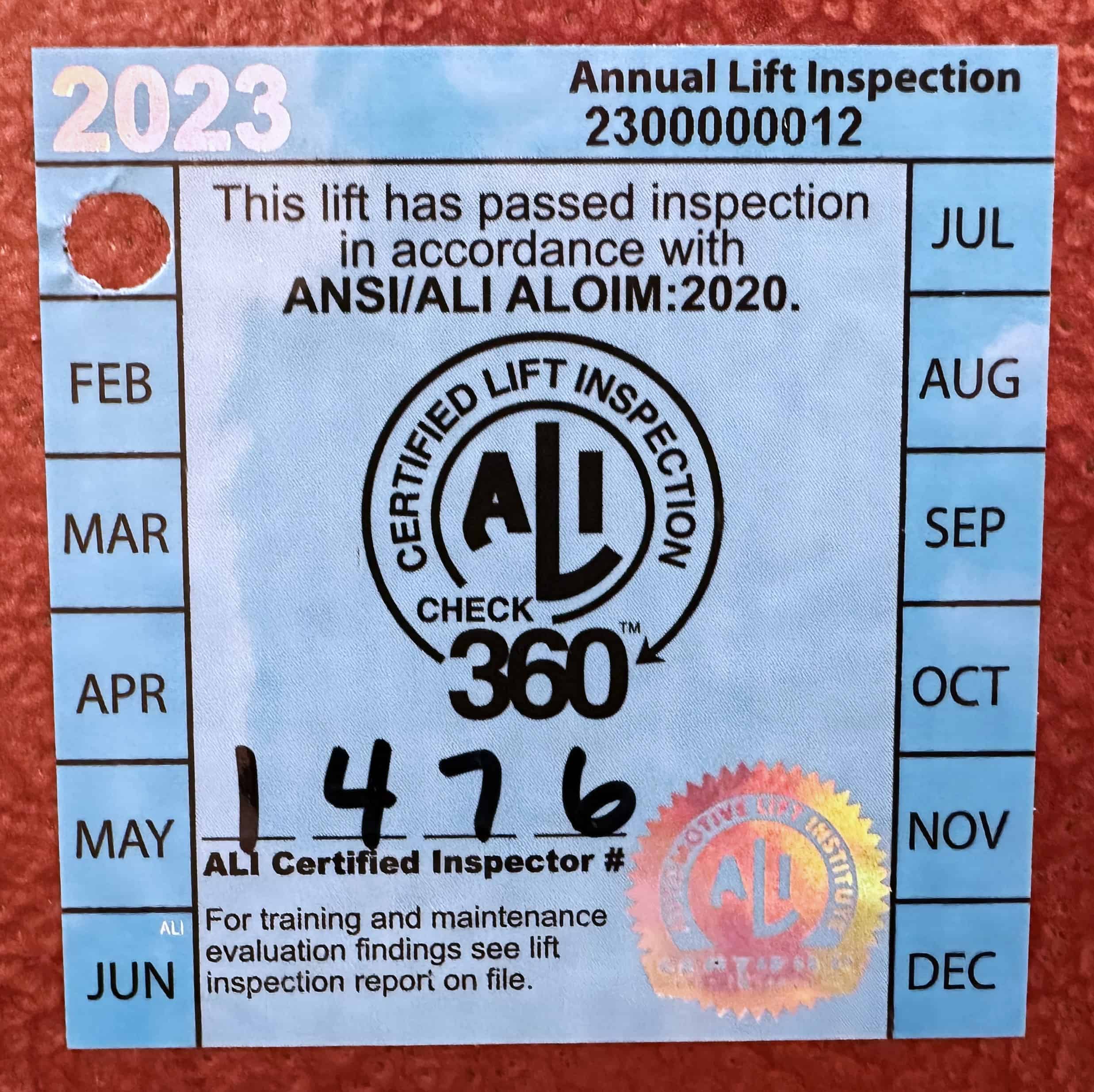
Daily Auto Lift Inspections
That missing cotter pin our consultants often find? It would have been discovered if the technician had inspected their lift before use that day.
Daily Inspections should be completed by the technician using the lift to verify it is in good working order before using it. This doesn’t have to be documented, as it is a quick visual check, but it is an essential piece of lift safety compliance.
If the lift operator has any concerns about the functionality of the lift and any part of the lift is not operating correctly, they should discontinue using the lift and report the issue(s) directly to a supervisor. Lifts not functioning correctly should be taken out of service until able to be repaired.
It is the technician’s responsibility to check their lift daily before use.
Your daily inspections should verify:
- Operating procedures and safety tips/warning labels are attached and readable.
- Rated load capacity is readable
- Operation Controls are working properly
- Structural components or other components (hoses, wire ropes, etc.) are not worn/deformed. Lift contact points are not worn
- Lift locks are operating
- Hoist fastening devices are all present
- No hydraulic or pneumatic leaks are detected
- No sudden noises or erratic movements are detectable during the operation
- No cracks or loose concrete are observed around the anchors
Lift Safety Training
The consequences of unsafe lift operations can be extensive; property damage, employee injury, and even fatality. These accidents, however, can be prevented with safe lifting procedures. Those safe lifting procedures must be communicated to the technicians through proper training.
As with any training, Lift Safety Training must be documented and should be completed before beginning work with an automotive lift. Regulators haven’t established a cadence for this training, but we recommend annual training. Completing this annually stresses the importance of this information to the technician and keeps lift safety at the forefront of your overall safety culture.
Your technicians should understand how to lift any vehicle without causing injury or damage. So important training topics include:
- How to spot a vehicle
- How to lift a vehicle
- How to prepare the service bay
- How to maintain load stability
- How to lower the lift
- Basic lift maintenance
There are a few ways to accomplish this training:
- Become a certified lift inspector and teach your staff,
- Have the lift inspector train your staff
- Use the training program built by the Automotive Lift Institute and available through KPA.
We recommend the ALI Training – it’s thorough, complete, and available anytime you hire a new technician.
Lift manuals and lifting point guides should also be readily available to your technicians. Safety signs and lift safety tip cards are good reminders for your team to stay vigilant while operating this equipment.
After all, we want everyone to go home safely after work.
Auto lifts are one of a multitude of hazards lurking in your dealership.
That’s why dealerships around the country rely on KPA tools, training, and consulting expertise to minimize risk and maximize business performance. Let us show you how we can help.