We all know how important it is to keep our workers safe. However, many companies develop their safety programs based on assumptions made by leadership rather than the realities facing their front-line workers.
Here’s where the golden opportunity lies. We can level up our safety game by tuning into what our employees out in the field are saying. Let’s take a look at five realities front-line workers experience that hold true no matter where you look.
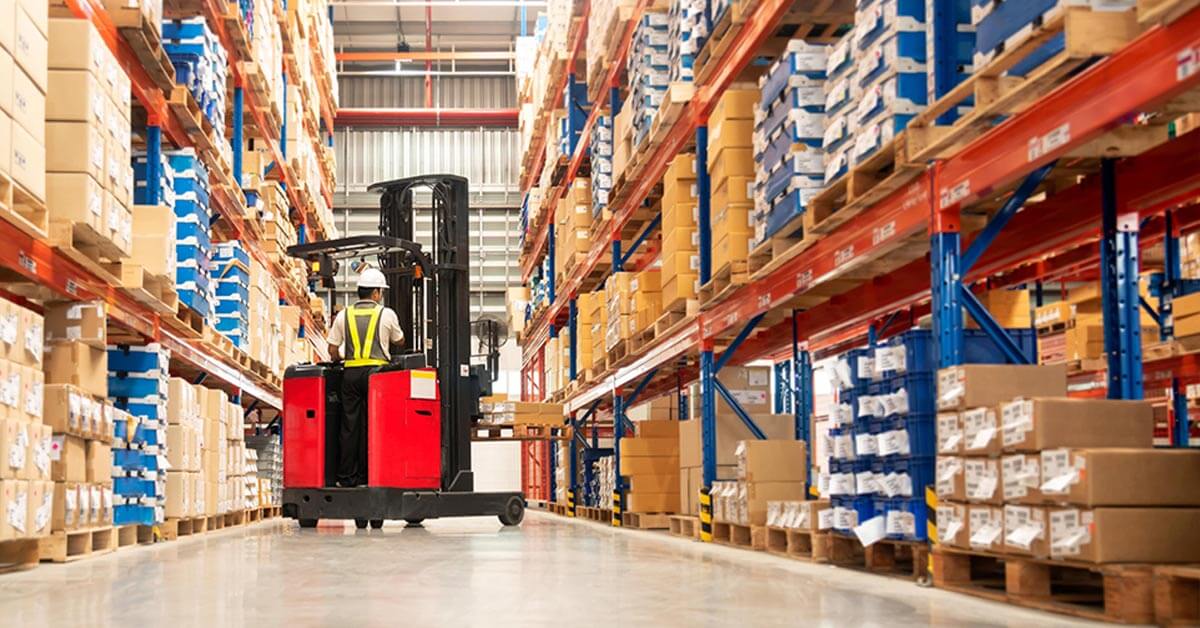
Front-line Workers See the Good, the Bad, and the Ugly
Much like a reality television show, there is no hiding the truth when real life plays out. The front-line worker sees it all, whether positive or negative, safe or unsafe.
Leadership must know what their front-line workers know. Leadership isn’t required to make every decision, but the decisions made should make a difference. Decisions should be made with the best information available, and the best candidates with the best suggestions come from the front line.
Front-line Workers Know the Shortfalls
The front line knows the shortfalls better than anyone. Whether it be a lack of resources, insufficient materials, or improper tools, the spotlight on shortfalls is very well known by the front line. When shortfalls are present, corners get cut.
If left ignored, shortfalls create inefficiencies, cost money, and put workers in an unsafe position… as they perform tasks in a “last resort” mentality. Knowing the shortfalls and applying the necessary fixes will strengthen safety, quality, and operational efficiency.
Front-line Workers Recognize Quality
Mentoring and training are important programs but don’t discount the observations of new workers. Experience should be an advantage, but even new workers can tell the difference between high and poor quality. Workers recognize things uniquely and can provide personal perspective when things aren’t right.
A strong reporting culture can elevate personal safety, but also strengthen the quality of work being performed. When audits, job planning checklists, and post-job reports are part of a program, workers will elevate their own performance knowing it will be documented.
Front-line Workers Have “Oh, $#!+” Moments
Situations occur every day that may not be actual incidents but are seen as significant to the worker experiencing the event. Near misses and close calls are events that directly affect the worker and get their heart racing.
These near-miss events are the best “free, damage-less” lesson we can learn. It is critical that they be reported and learned from. Even if the significance is only in the worker’s mind, being fully aware when they happen and providing quick feedback is vital for a strong, safe working environment.
Front-line Workers Need Feedback
Front-line workers need feedback, whether appreciation, correction, direction, or simple discussion. Coaching makes a difference, and leadership must know how, what, and when to coach.
Understanding that workers need feedback, it becomes important that feedback be timely. If a significant near miss is not responded to quickly, the worker will lose confidence in any perception of safety culture. No response can translate into no one caring, it isn’t important, or no one is listening. Remember, crickets damage culture…. so be responsive and timely in providing feedback.
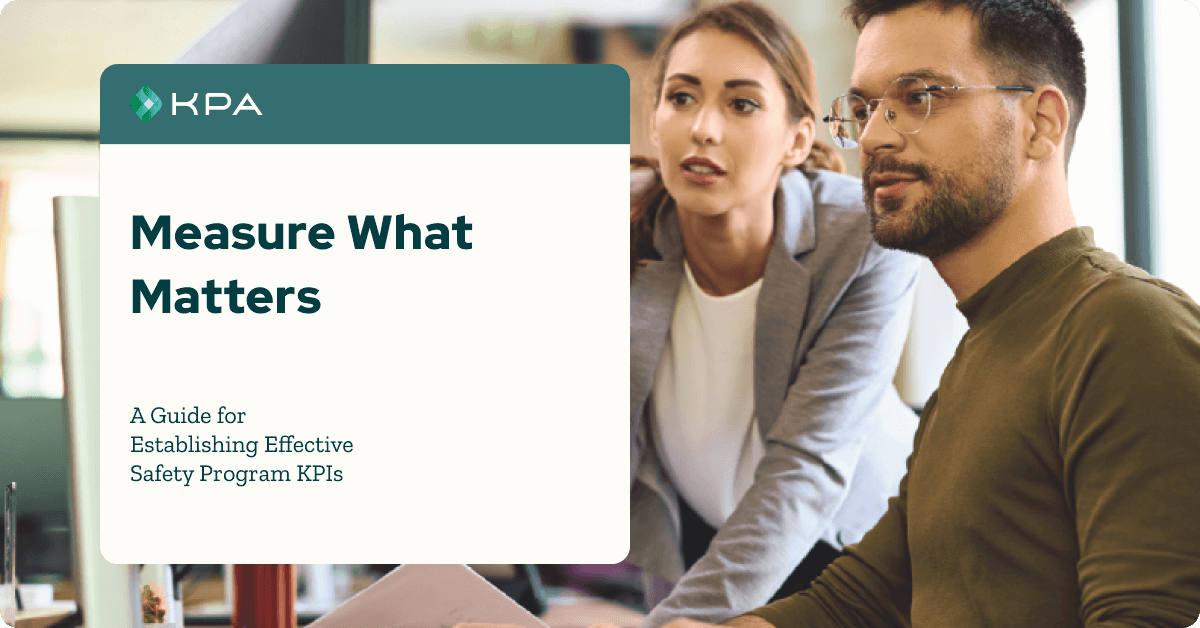
Your guide for establishing effective safety program KPIs. As organizations continually strive to improve their safety standards, the role of Key Performance Indicators (KPIs) in shaping an effective safety program is more crucial than ever.
Five Tips For Gathering Front-Line Information
Consider these tips when creating a pathway to collect front-line information. Use the information to make the best decisions for growth and change within your organization….
- Chuck the paper – forget trying to keep up with written, paper-based reports. Tracking becomes tough, inconsistent, and delayed.
- Make it simple – get more participation, and take less time for your workers to be involved. Simplicity will push participation.
- Involve everyone – whether a seasoned veteran or a new hire, every worker can provide information and perspective.
- Receive immediate notifications – be aware now. Set up alerts when reports are submitted from the field to your email or device in real time. This allows for immediate awareness of conditions.
- Respond to a response – when information is received, respond. It could range from a needed correction, a thank you for reporting, or an opportunity for immediate clarification and training.
Monitoring your safety program is easier with solid EHS software in your team’s hands.
KPA simplifies data visualization and reporting, giving users easy access to actionable insights into their EHS program performance. Your data is presented in real-time, so no delay or extra steps are required to access the information. The dashboards are configured based on features tailored to your business’s unique requirements, giving you the power to make informed decisions that impact workplace safety.
Let KPA show you how to take a data-driven approach to safety.
Related Content
Explore more comprehensive articles, specialized guides, and insightful interviews selected, offering fresh insights, data-driven analysis, and expert perspectives.