So I was talking to a couple of our environment, health, and safety consultants the other day and I learned a new term: pencil whipping.
If you’re unfamiliar with the term, you might be imagining (as I was) someone literally thwacking another person with a pencil. It’s not as direct as that, but its damage potential is far greater. To pencil whip is to mark a task as complete without actually completing the task.
It means not doing the work but checking the box anyway.
Apparently, pencil whipping is military slang—which has me a little concerned about what’s going on among our armed forces. But anyway…
According to the EHS consultants, pencil whipping is a major problem in the world of workplace safety and compliance. Too often, organizations decide to wrap up safety inspections without taking adequate steps to address problems those inspections have uncovered. It’s also common, they say, for safety managers to try to fill out missing records just because they know consultants are coming to visit. As a result, issues get buried until an accident happens or a regulator such as the Occupational Safety and Health Administration discovers the truth.
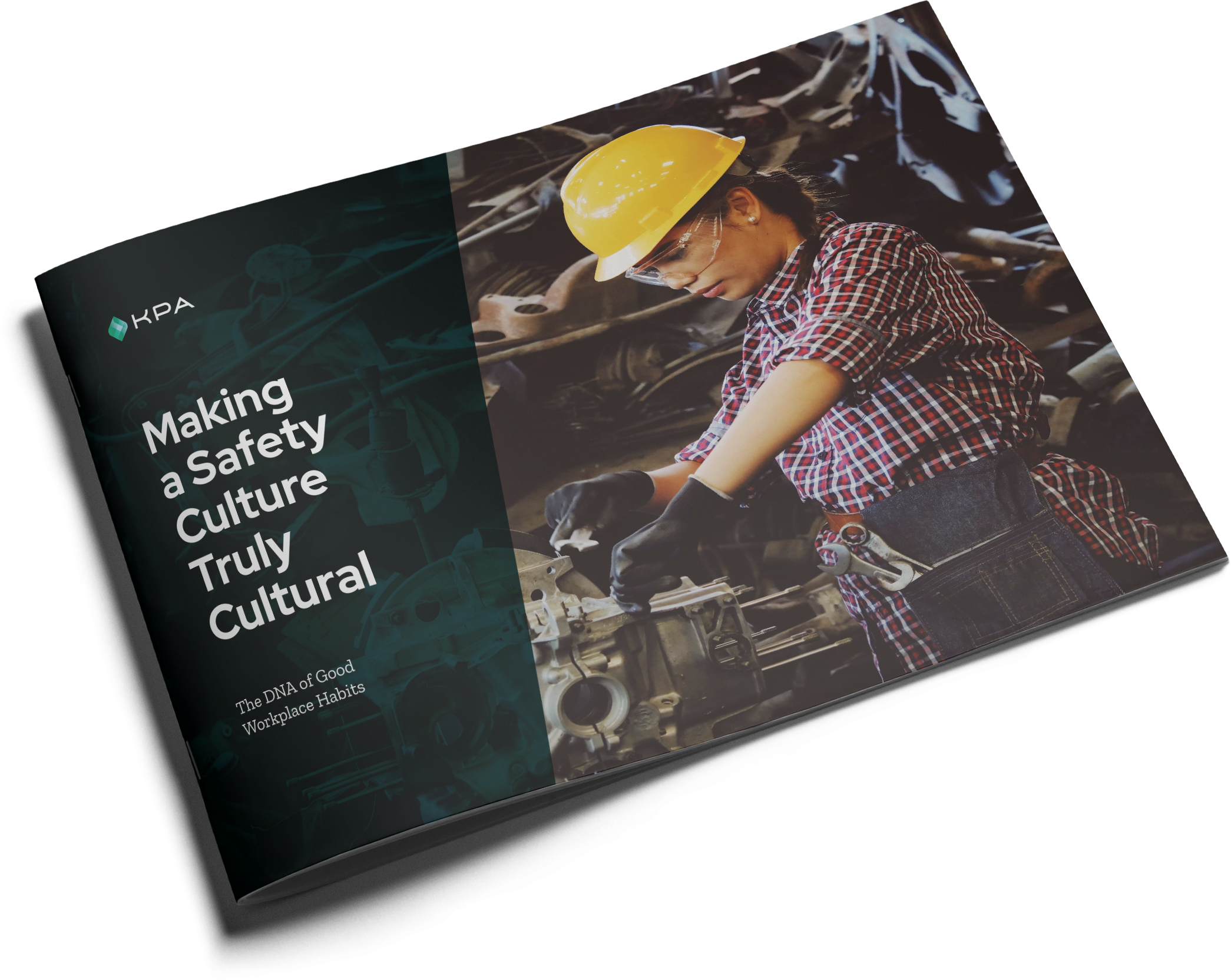
What safety looks like today, where safety needs to change, and how to create a safety culture.
Safety is hard work. And it’s never the only priority.
There’s too much to do and not enough time to do it. It can be tempting to simply check the box and hope for the best.
But there’s a deeper reason behind pencil whipping: lack of buy-in from leadership. If the organization’s decision-makers don’t seem to care about safety, employees may have little incentive to care about it either. As Armin told me:
“If lower-level employees see that management or upper-level management doesn’t care about safety, then they’re not going to put much effort in continuing their previous record or trying to get better. A lot of it comes down to: What does the organization value? If they value safety and training, then they’ll have a strong emphasis on that. If they don’t value it as much, that reflects in their audits and records. You can see that they don’t pay as much attention to it as they could or should have.”
That last point is crucial. EHS professionals can spot pencil whipping immediately. They can tell when safety records don’t accurately reflect reality. And so can OSHA inspectors. According to the consultants, investigators pay attention to everything, and the seemingly tiniest details can lead to violations. For example, if the last 3 months of inspection forms have been filled out in the same handwriting with the same color of ink, that’s a dead giveaway to OSHA that the employer is likely falsifying information.
So, how do you move beyond pencil whipping and meaningless box-checking?
Justin told me that effective training is key:
“The emphasis in training is reiteration. We get in the motion of things, and we start just checking the boxes instead of remembering why safety matters. For example, I’ve seen plenty of fire extinguisher inspection records filled out but then look at the extinguishers themselves and find one that’s not charged completely or not mounted on the wall—it’s just sitting on the ground. We need to reiterate what we’re looking for when we’re doing these inspections to avoid a catastrophic event. We don’t want to be in a situation where we need to put out the fire and the extinguisher’s in bad working order. But safety takes a while to develop as a culture. It’s not going to change overnight, which is why reiteration helps.”
The other essential component is the executive and management involvement mentioned earlier. The people in charge of the organization’s EHS program are responsible for setting the tone and demonstrating the importance of safety at all times. Justin mentioned:
“Leaders will even tell on themselves. I’ve had managers tell me, “I gave my team a heads-up you were coming,” and I’ll see that some inspection tools have been signed off day-of, because they know I’m there. That’s not really the point, is it? The point is that we’re emphasizing safety the entire time that you’re in operation, not just when the KPA guy’s present or the OSHA inspector’s here.”
Fortunately, with better tools and a shift in mindset, it’s easy to turn your organization around.
We have the software, training, and expertise you need to do it. KPA’s EHS consultants will help you lay the foundation for a better safety program and safety culture that lasts—even when we aren’t there.
Stop pencil whipping and start saving lives, time, and money. See how KPA’s on-site and online consulting services will transform your organization.
Related Content
Explore more comprehensive articles, specialized guides, and insightful interviews selected, offering fresh insights, data-driven analysis, and expert perspectives.