In the world of workforce safety and compliance, there are effective programs and then there are spreadsheets.
If you keep up with the KPA blog regularly, you already know how we feel about spreadsheets around here. But in case you’re new or haven’t gotten the message yet, I’ll say it loud and clear:
Spreadsheets stink.
Spreadsheets don’t improve safety. They don’t reduce workplace accident rates. They certainly don’t keep people out of trouble with the Occupational Health and Safety Administration. And yet many organizations—too many—still use them to manage and track the bulk of their environment, health, and safety data.
In our recent State of the Industry: EHS Program Trends report, we found that spreadsheet-reliant organizations tend to fall short in multiple ways. Compared to industry averages, they put their employees at greater risk, are less profitable, and face higher expenses—from workers’ compensation costs to legal fees—in the wake of an EHS incident.
What’s wrong with spreadsheets, exactly? Let’s dig in and find out.
Why Spreadsheets Are No Longer Sufficient for Managing Safety
Once upon a time, spreadsheets were cutting-edge technology. They simplified data storage and analysis, making it easier for non-mathematicians to perform advanced number-crunching, generate charts, and find patterns in large amounts of information.
That was decades ago. In the years since the advent of spreadsheets, organizational information has grown exponentially in size and complexity. We now live in an era of big data—an era spreadsheets weren’t built for. It isn’t enough to capture a few data points and store them in a folder on an individual’s computer. There’s simply too much information out there, and it’s unfolding and evolving too quickly. No single person or spreadsheet can monitor and make sense of it all.
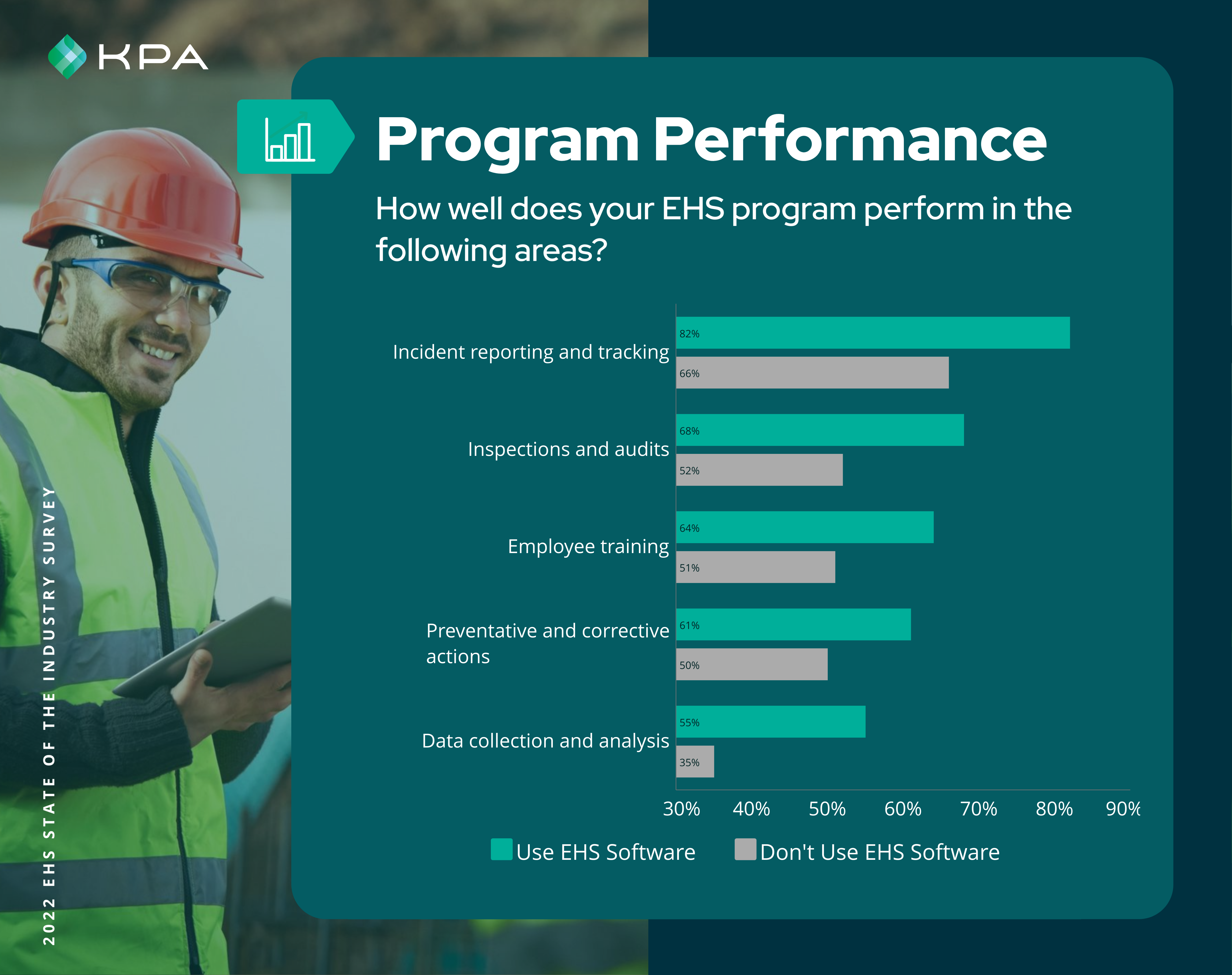
4 Reasons EHS Software Is More Effective than Spreadsheets
To overcome information overload, organizations need to find newer, better tools. They need to use EHS software.
EHS software is more than a means to collect and scrutinize data by hand. It provides a holistic view of the workforce and automates data analysis, giving organizations the power to identify actionable, up-to-date safety and compliance information in seconds.
This tends to improve organizational safety and performance, for several reasons:
1. It’s faster.
Instead of spending hours typing in numbers, selecting cells, and applying formulas, safety professionals can generate reports in just a few clicks. And instead of searching through files and binders for the information they need, workers can pull up safety forms and resources instantaneously. This can save lives. In the aftermath of a workplace incident, every second counts.
2. It’s more accurate and efficient.
Not only is automated EHS software faster than spreadsheets, but it also minimizes human error. This is essential for reliably reducing incidents and reporting verifiable safety and compliance information.
3. Anyone can use it.
Software is more intuitive than spreadsheets, thereby eliminating bottlenecks. There’s no need to rely on a single individual to manage the entire safety program.
4. Anyone can understand it.
EHS software makes it easy for safety professionals to communicate the value and importance of their programs to others in the organization, from frontline employees to executive leadership. When people understand why safety matters, they prioritize it and take it more seriously in their work.
Key Capabilities to Look For in EHS Software
It’s important to note that some EHS software solutions are better than others. If you’re unfamiliar with the market and unsure of what kind of technology to invest in, here are a few key features and capabilities to look for.
- Mobile reporting and inspections:
Accidents don’t happen at desks. EHS software needs to be available and fully functional on mobile devices. When there’s an incident, an employee should be able to pull their phone out and log the details immediately. Similarly, safety managers need to be able to do inspections on the fly. If someone is walking around a facility and sees something that needs to be addressed, they should be able to document it with photos and/or videos. - Corrective and preventive actions:
After capturing data, the software should make it easy for safety managers to assign corrective and preventive actions to employees, and then track employees’ progress so no issues fall through the cracks. - Training:
Good EHS software is supported by high-quality training content. Any solution you use needs to facilitate employee training—online and offline—with a comprehensive library of safety and compliance education. The more dynamic and interactive this training, the better. - Program monitoring:
Ultimately, good EHS software demonstrates its own effectiveness. It helps safety managers prove ROI and show organizational leadership that KPIs are improving. The clarity and quality of the data are what matter here.
Some software solutions have better capabilities in some of these areas than others, but spreadsheets, of course, do none of the above.
Want help making a smart decision? Grab a copy of the EHS Software Buyer’s Guide.
KPA EHS – The Backbone of Your Safety Program
KPA EHS helps you develop a comprehensive EHS program that harnesses technology, best practices, and the concerted efforts of your workforce to maintain a safe and productive workplace.
Introducing an EHS software platform tailored to the needs of your business. Manage your safety program in an all-in-one system designed to engage your employees, instill a culture of safety, and enable regulatory compliance.