When it comes to Environmental Health and Safety (EHS) compliance, identifying issues is only half the battle. The real challenge—and opportunity—lies in effectively tracking these issues to resolution and using that data to prevent future problems. As someone who’s worked with countless dealerships to improve their safety programs, I’ve seen firsthand how proper issue tracking can transform a struggling safety program into a proactive, efficient operation.
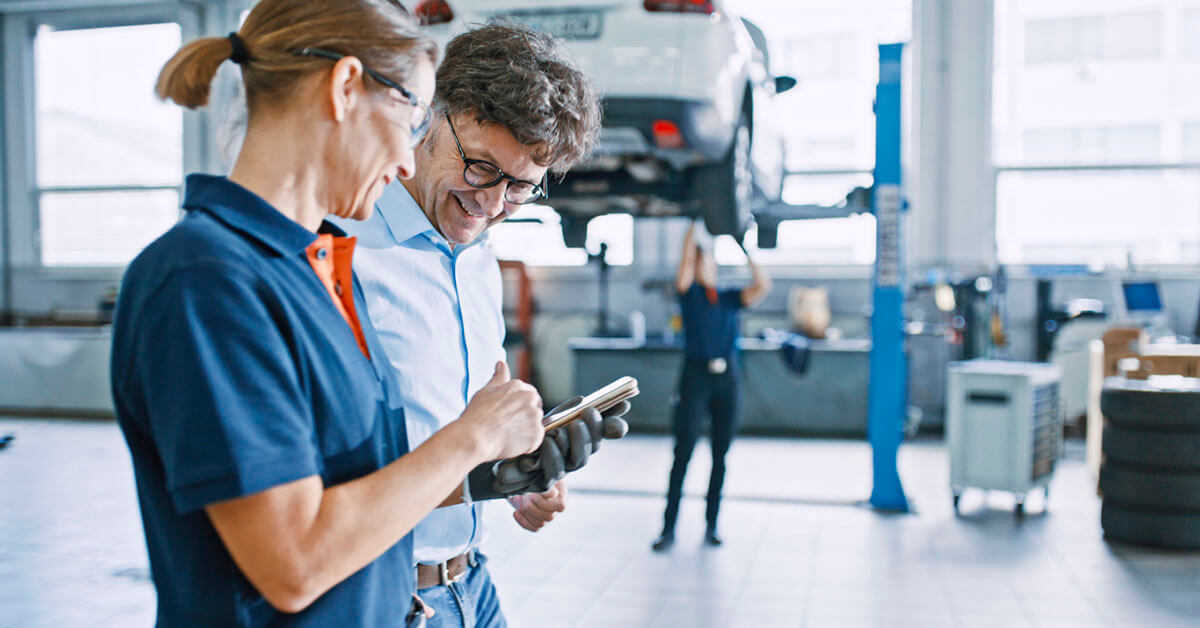
Periodic Assessments
Issue tracking begins with periodically conducting internal assessments of your facility and operations. A periodic schedule could mean that an internal inspection happens on a cadence which could be:
- Daily
- Weekly
- Monthly
- Quarterly
An assessment should identify any hazards in the workplace that are likely to cause an injury or illness. The assessment should also capture identified errors in a process or procedure. Capturing photo evidence will provide great detail as to the actual condition of the hazard and its location. When conducting the assessment, the inspector should capture the following in relation to an identified hazard:
- Title for the hazard: Electrical cord tripping hazards
- Department: Service Department
- Location: Service Bay 12
- Priority: High Priority
- Comments: Three loose cords were observed on the floor as trip hazards
- Photos: Photo of the observed hazard
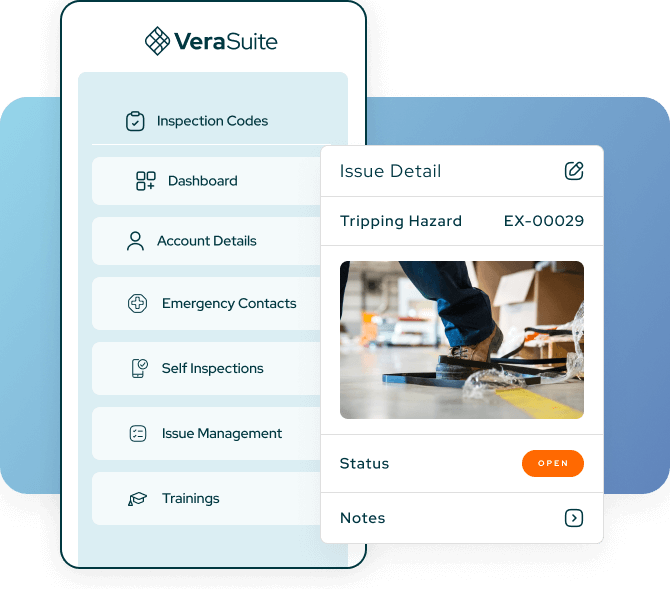
The direct and indirect costs of a workplace injury or illness can have a significant impact on a dealer's bottom line. Download this guide and save your dealership millions.
The Foundation of Effective Issue Tracking
Issue tracking is more than maintaining a list of problems—it’s about creating accountability and ensuring nothing falls through the cracks. A robust issue-tracking system serves as the backbone of your EHS program by providing a mechanism for properly completing, verifying, and closing out identified areas for improvement.
The key is having a closed-loop system for your assessments. This isn’t about trust—it’s about taking the guesswork out of compliance. When everyone knows their responsibilities and has a clear path to completion, safety becomes a natural part of daily operations rather than an afterthought.
Beyond Paper: The Power of Digital Tracking
I frequently hear from dealerships that their current system is “very pen and paper.” While this might seem sufficient at first, it creates significant challenges:
- Trend identification becomes nearly impossible
- Multiple inspectors might miss recurring issues
- Papers pile up on the safety manager’s desk
- Data analysis becomes time-consuming and impractical
- Departmental patterns get overlooked
Consider this common scenario: Department B has ongoing issues with daisy-chained extension cords—a fire code violation. Each inspection noting this issue with a paper-based system becomes just another sheet in a stack. Multiple inspectors might document the same problem without realizing it’s a persistent trend.
Leveraging Software for Better Results
A digital issue tracking platform transforms how you manage safety concerns. Instead of wrestling with paper records, you can:
- Track issues from identification to resolution
- Easily analyze trends and patterns
- Generate reports on top concerns
- Monitor completion rates
- Identify systemic problems
This capability to analyze data leads to powerful insights. You might discover that most of your issues relate to hazard communication—perhaps container labeling is consistently missing, or employees are choosing incorrect PPE. These insights allow you to develop targeted emphasis programs that address root causes rather than just symptoms.
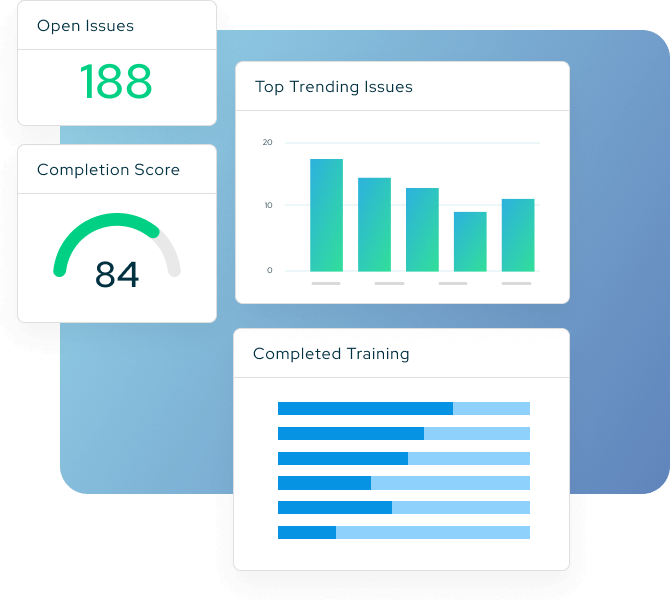
From Insights to Action
The true value of effective issue tracking comes from how you use the data. When you can quickly identify your top 10 issues and understand their relationships, you can:
- Create focused training programs
- Develop specific safety protocols
- Allocate resources more effectively
- Measure improvement over time
- Demonstrate program success to management
Making It Work for Your Dealership
Effective issue tracking is crucial whether you’re just starting to formalize your safety program or looking to improve an existing one. Here’s what to focus on:
- Implement a system that works for your size and needs
- Ensure all stakeholders understand their roles
- Make data entry and tracking as simple as possible
- Regularly review and analyze the data
- Use insights to guide program improvements
Remember, the goal isn’t just to track issues—it’s to create a safer workplace through systematic improvement. When you can show clear trends and demonstrate how addressing them improves safety outcomes, you build support for your EHS program at all levels of the organization.
Transform Your Safety Program Through Systematic Issue Tracking
Effective issue tracking transforms safety from a reactive necessity to a proactive tool for improvement. It provides the data you need to make informed decisions, the accountability to ensure problems get resolved, and the insights to prevent future issues. In today’s complex regulatory environment, this systematic approach isn’t just helpful—it’s essential for maintaining compliance and protecting your people and business.
Complete Dealership Compliance from KPA
Keep your dealership safe from environmental factors that impact your workers’ and customers’ safety. KPA helps auto dealers maintain cultures of safety, streamline operations, and manage risk through a robust set of tools that includes a combination of consulting, training, and regulatory content.
Next Week, Let’s Look at Safety Committee Meetings
Join us as we break down the essential steps every dealership must take to build and maintain a successful safety program. If you haven’t already, subscribe to our blog for weekly installments of the 10 steps to complete compliance.
Follow a 10-step journey to compliance.
Move your mouse over each step to learn more about each step.
Related Content
Explore more comprehensive articles, specialized guides, and insightful interviews selected, offering fresh insights, data-driven analysis, and expert perspectives.