Safety isn’t just about rules and procedures—it’s about creating an environment where every employee feels personally responsible for maintaining a safe workplace. While many organizations understand this concept, translating it into reality remains one of the industry’s biggest challenges. In fact, increasing safety participation consistently ranks as a top priority for EHS professionals across all industries.
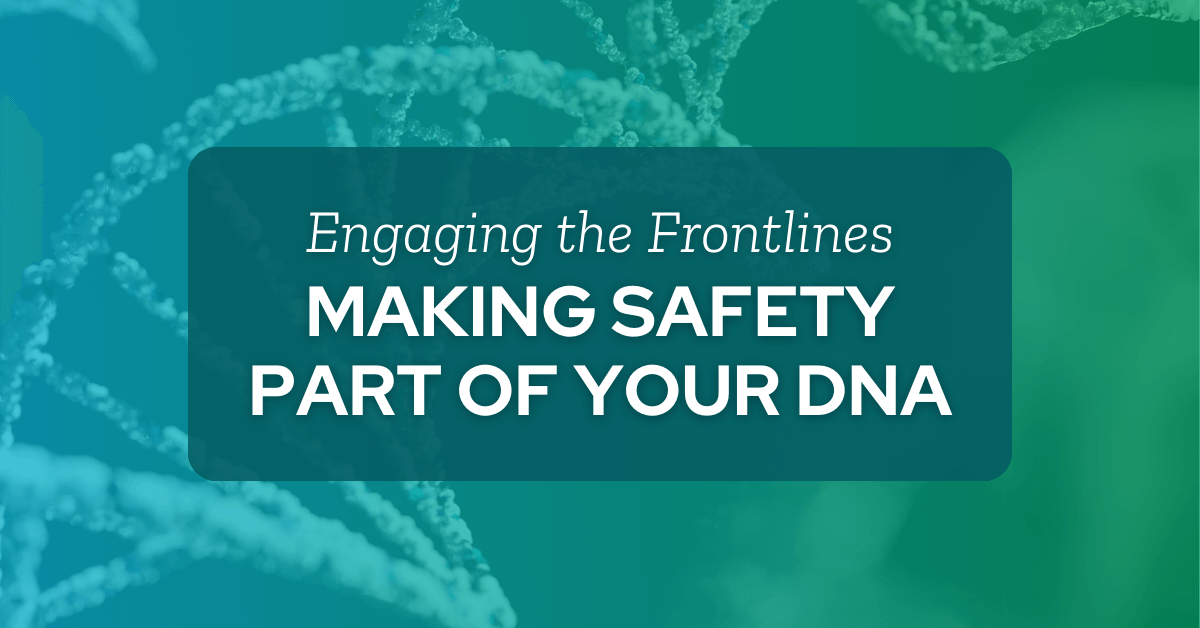
The Leadership Imperative
Building a safety-first culture starts at the top. Without a clear commitment from leadership, even the most well-designed safety initiatives will fall flat. Safety culture must flow from the top floor to the shop floor, from C-suite to craft, creating an environment where everyone understands their role in maintaining workplace safety.
As KPA customer Bill Woods, Director of Safety, Quality, and Regulatory Compliance at American Welding & Gas explains,
“Our company dedicated a full-time resource to lead the efforts of promoting a safety culture throughout the company. This resource reports directly to the company’s CEO, who is very involved and instrumental in allocating proper resources and tools to promote safety culture throughout the whole company.”
Case Study: GE Johnson’s Three-Step Implementation Success
When GE Johnson, a major general contractor, decided to transform their safety culture by adopting KPA Flex, it implemented a comprehensive three-step approach that exemplifies best practices in cultural transformation:
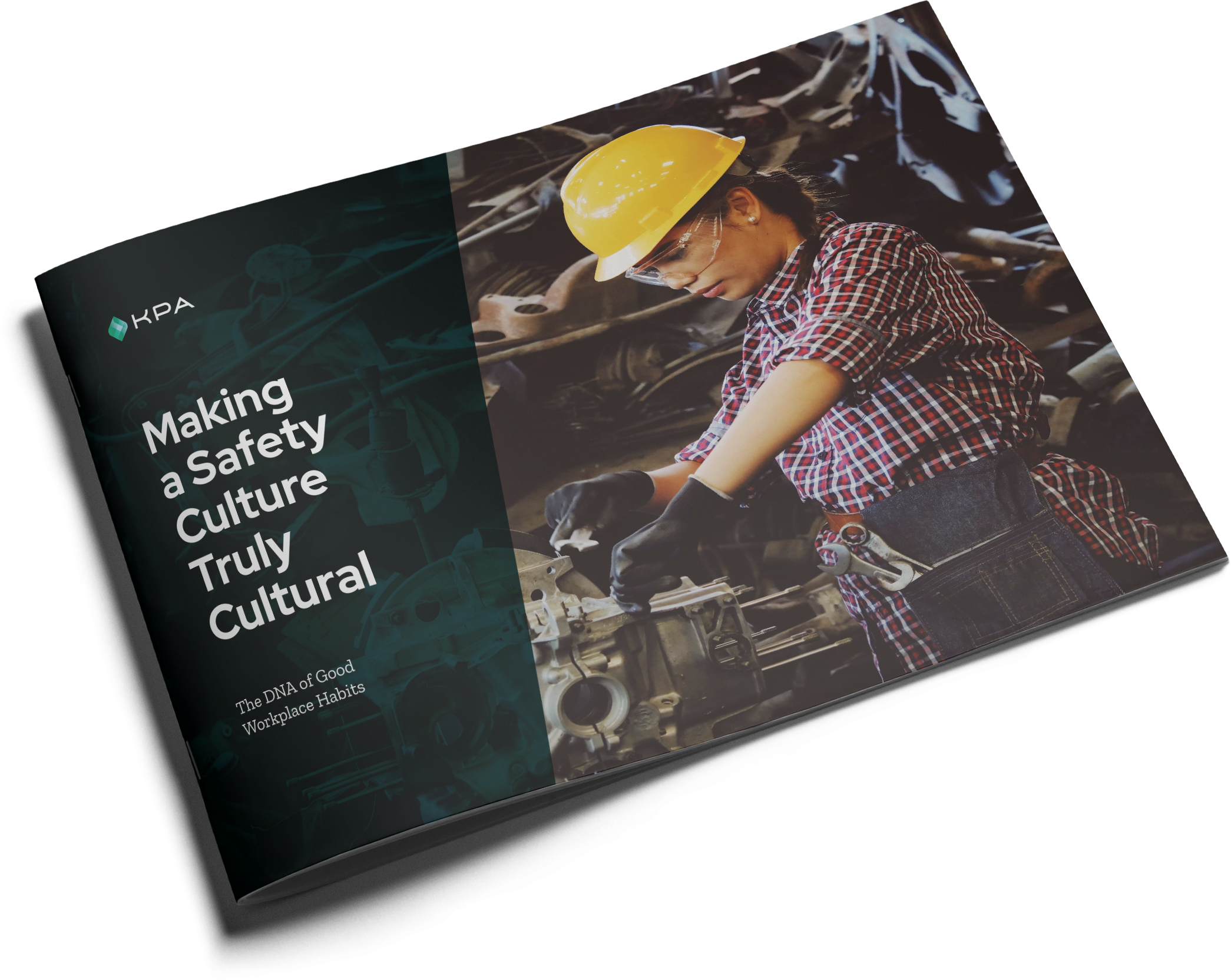
What safety looks like today, where safety needs to change, and how to create a safety culture.
Common Safety Culture Barriers…and Solutions
Creating a safety-first culture requires overcoming several common obstacles that can impede progress. Here are key challenges and strategies to address them:
KPA customer Chris Gafford, EHS Manager at Ring Energy, shares their journey:
“We started the safety culture journey, but it’s a long one. Crawl, walk, run… Most interesting is that the field guys are hungry for more. We recently did a Safety Culture Assessment survey and the overwhelming response was that they are ready to take it to the next level.”
Best Practices for Cultural Transformation
Transforming your organization’s safety culture requires a systematic approach with clear strategies and consistent execution. As one KPA customer and Sr. Safety Specialist explains:
“Putting a focus on Why people should work safe. Put the onus back on them to think about why and who they are working safe for. We utilize a ‘Why I Work Safe’ badge so our employees have a daily reminder as to why they should work safe.”
Consider these essential practices:
As David Finley, KPA customer and HSE Director at Dolese Bros. notes:
“Leadership had to be visibly committed at the very top. Some leaders didn’t stay with the company because they weren’t on board with the changes. We also had to quit being so rigid and have some flexibility in how we got employees actively involved in safety. We started having front-line employees solve safety problems and push their ideas to the entire workforce.”
Judy DeForeest, KPA customer and EHS & Quality Coordinator at LDX Solutions, shares their success story:
“We are constantly visible out in the plant. Our employees see us as a good thing, we are the caring department. Praising people for working safely and finding ways to reward them. It is paying off with our lower mod rates and reduced injuries/prop damages and near misses. It takes a village, and we’re all in this together.”
Safety Leaders, Take Action Now!
Ready to begin your cultural transformation journey? Here are concrete steps you can take to start building a stronger safety culture today:
- Assess current safety culture through surveys and feedback
- Develop a clear vision for safety excellence
- Create a communication strategy
- Implement supporting technology solutions
- Establish measurement systems
- Provide ongoing training and support
- Regularly review and adjust approaches
KPA Helps You Engage Your Frontline Employees
Turn your safety program into a thriving culture of participation. KPA Flex puts powerful safety tools directly in your workers’ hands, transforming manual processes into streamlined workflows that drive real engagement. The result? Better reporting, fewer incidents, and a stronger safety culture—all with less administrative burden.
Learn How Flex Helps Engage the Frontlines
Remember, building a safety-first culture isn’t a destination—it’s a journey of continuous improvement. With the right commitment, tools, and support, every organization can create an environment where safety is truly everyone’s responsibility.
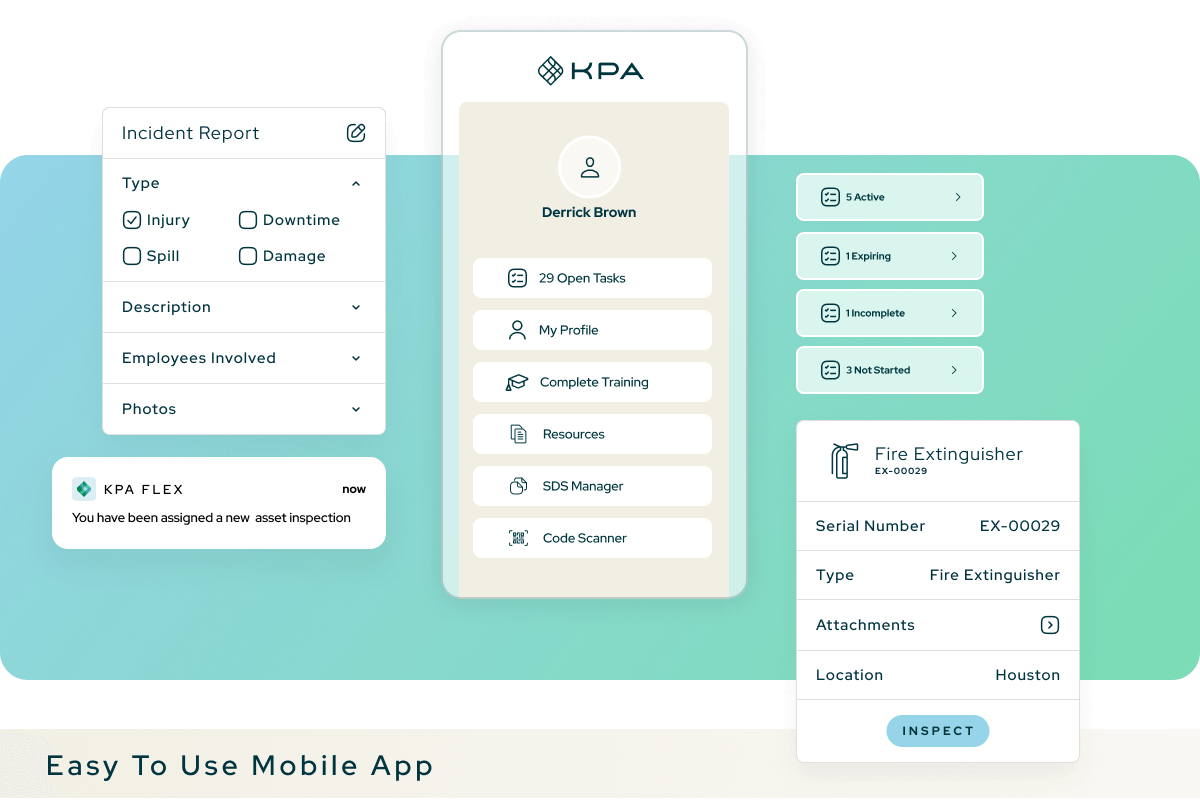
Related Content
Explore more comprehensive articles, specialized guides, and insightful interviews selected, offering fresh insights, data-driven analysis, and expert perspectives.