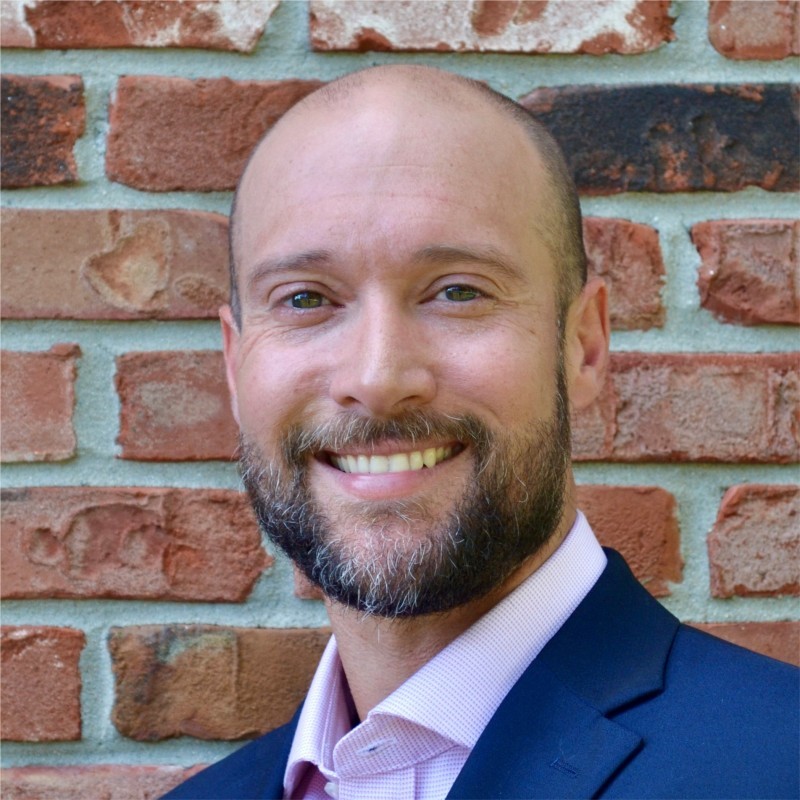
Today, we’re back with Zach Pucillo for his look into 2025. If you’re an avid listener of The Safety Meeting, you know that Zach is KPA’s own EHS Regulatory Compliance Manager, a certified safety professional, and a certified hazardous materials manager, recognized in 2022 by the Alliance of Hazardous Materials Professionals as Hazardous Materials Professional of the Year, and accepted into the 2022 Class of Rising Stars by the National Safety Council.
Thanks for being with us today, Zach. As we look forward to 2025, what are some of the major trends and updates that you think will be shaping workplace safety and compliance?
Well, I think we’ve got a major shift about to happen. We have a new administration going into the White House, and with a new administration comes new department heads and new selections. This administration, the Trump administration, is known for deregulation. We’re going to see some changes, and there’s going to be some rollback of some regulations.
We’re going to see some items out there that were in the pre-rule phase and the proposed rule phase change before they get to that final stage. Once again, they’re looking out for big business, probably moving forward and then over the next four years.
A couple of things that kind of go along with that would be, for example, the Chevron deference that was actually overruled earlier this year.
Our Better Workforce Blog is your Ultimate Guide!
Stay informed with weekly industry updates, expert insights, best practices, and actionable tips to enhance workplace safety and compliance.
Many people are probably asking, what’s this Chevron deference all about? Well, it’s actually the Loper Bright ruling. There was a court case where the judge pretty much overturned the Chevron deference that was being utilized to interpret a regulation. The Chevron deference basically treated regulatory authorities such as the EPA and OSHA as subject matter experts. And when they came out with a regulation, they were the subject matter experts who would interpret that regulation as well.
As you go through that whole regulation and companies trying to comply with it, there are going to be little nuances here and there with different industries, such as how we comply with the regulation in this situation. And so with the Chevron deference. The judge in that court case would turn to the regulatory authority, such as the EPA, and say, okay, subject matter expert, you wrote this standard, how is this supposed to be interpreted? Well, since that’s been overruled, it’s going to actually be the interpretation of the judge on how that standard should be interpreted in each one of those cases.
So it kind of removes some of the authority that OSHA or the EPA had in levying some of their standards as far as how they apply to certain businesses that are out there, with that deference being overturned.
There could be a lot of different changes, especially with items coming up, such as the heat illness regulation that’s going to be coming out. It’s in the proposed stage right now, but with little nuances from construction industries that have issues with how the rule was written. Once it hits a final stage, we could see OSHA getting sued over that. Then, it’s up to a judge, not the OSHA subject matter experts. It’s up to the judge to actually interpret the standard themselves and make a ruling on it.
We also saw that the fall regulatory agenda was recently released. The White House will release a regulatory agenda in the spring and also in the fall. So we keep an eye on that to see, okay, what’s coming down the pipeline as far as federal rulemaking goes.
Under the Biden administration, we saw that in our pre-rule update, “process safety management” was the only thing added to that list.
Process safety management is the prevention of chemical accidents for chemical manufacturers. So, as a chemical manufacturer is actually putting all their ingredients together and sending the chemical to the process to make a refined product, they have to go through process safety management to ensure all the employees and the whole chemical process is completely safe, as it’s moving through that route.
So, pre-rules, we don’t know exactly what’s going into those as of yet, we just know that they’re taking a look at it.
Now, under the proposed rule stage, not a whole lot has been moved there. Usually, we have a good update on that, but the “emergency response initiative” was moved into a proposed rule stage, and the “heat rule” was moved into a proposed rule stage.
So, an emergency response initiative is where, if you have an organization that has a rescue team or an emergency response team that you have organized, or emergency responders from the federal government or state local governments, they may have to abide by these standards as well.
And so they’re taking a look at personal protective equipment, ensuring that the right personal protective equipment is in place for those teams, making sure that they have the right processes and procedures and training to actually respond to an emergency.
The other big rule in the proposed rule stage is the heat rule. And so that’s going to go sweeping across the entire country if this actually does get passed. It’s to try to prevent heat-related illnesses and injuries from happening to employees all across the country. So, no matter if you’re in the northern part of the country where you don’t have to deal with heat as much, you still would have to comply with this. You do have the summertime as well, too. But you know, Southern California, Texas, Florida. They would have to comply with this rule.
So it has different trigger points: 80 degrees Fahrenheit means you have to actually put your heat policy in place for that day, and that’s measured by a heat index, not just the overall temperature. So it might be 79 out; however, if you add the heat index to that, you might be over 80 degrees. And then at 90 degrees, that triggers the “high heat advisory” as well. And there are a few other items that go on top of it.
Complying with the rule is not that difficult. I mean, most likely, we’re already doing this: providing water, shade, rest breaks, and training employees on heat-related illnesses so that they can take care of themselves if they see any symptoms.
OSHA is now making that a standard. If your organization does not apply these things, you could be cited for not following the heat rules.
Some companies find it a little bit of a burden because they constantly monitor areas and because it’s not only outdoors. It’s easy to monitor the heat index outdoors. We all get the weather report, you know. Put in your zip code, and you can see what the heat index is going to be for that area.
But this is also indoor heat. So if you have a manufacturing facility and large machinery that gives off a lot of radiant heat, like a boiler room, or in a foundry, or your employees are wearing personal protective equipment where it’s a little bit restricting and you don’t have a lot of ventilation going on, you actually have to monitor for that and make sure that you’re adapting those policies for those indoor areas where it could apply.
You have to monitor indoors for the heating index as well, and that’s going to be a little bit of a burden on some organizations because they could be at that threshold mark. So it’s like, do we always comply with it or do we only apply, comply with it on certain days when the outdoor temperature really heats it up in this area?
There are a couple of ways to monitor it. If you can get a heat index using some kind of measuring device, that’s a possibility. However, you can’t really go off of the outdoor heat index unless you want to just comply on any one of those days for anywhere in the inside organization. Also, there’s a measuring device called a wet bulb globe thermometer, and that’s the one that OSHA references within the proposed rule.
So now we have another burden of organizations having to buy that type of temperature recording equipment, which measures radiant heat, heat index, and dry heat as well.
So, there are a couple of rules that are in the final stage as well.
In fact, personal protective equipment in construction has just become a final rule from OSHA. That is regarding the fit of personal protective equipment. So, if you’re an organization that has to provide personal protective equipment to mitigate hazards for your employees, that’s great. And per the standard, you have to supply that to your employees mostly at no cost to them. There are a few exceptions, but you have to ensure that the PPE actually, you have enough variety out there so that people have a good fit for that personal protective equipment.
You can’t just buy size large gloves, vests, and other types of clothing and expect it to be one-size-fits-all for everybody, right?
We’re all different shapes and sizes out there, and therefore, we have to ensure that we have a good variety so that the PPE does not become a hazard in itself.
So it’s kind of common sense, but now it’s just an actual standard for construction.
The other one that I’m taking a look at is the powered industrial trucks. It’s really a design update. I’m taking a look at older powered industrial trucks, mainly forklifts, and making sure that they have cages on them.
They have some more regulations spelled out for operator platforms or order pickers that we’re commonly seeing, like warehousing and all that. And then also a little bit more in the standard about lifting personnel: When you have the proper attachments or if you’re on one of those operator platforms or pickers, there are some actual weight restrictions going into the requirements now; the device already had a weight restriction; it’s just going into the standard, making sure that you’re not overloading that equipment.
OSHA is also looking into collecting information to see if they need to update, how you go about maintaining it, evaluating the equipment, and then training for operators as well. It’s been a long time since they looked at these standards and adopted some of the nuances of newer equipment that’s out there, especially as the world changes with technology and all that. OSHA’s trying to catch up with a lot of that stuff and put it actually under the standards.
[00:09:52]
I’m sure it can be tough being a body like OSHA that has so many things that it needs to touch to make sure that you’re staying up to date in every single area, especially as tech has accelerated at a rapid-fire pace in the last decade. I’m sure it’s tough to see all those pieces, knowing that it’s a lot to keep in mind. And speaking of these specific regulatory bodies, why don’t we narrow it down a little bit? So, when it comes to organizations like OSHA, EPA, the DOT, etc., who do you think will have the biggest influence in 2025? And what should safety professionals be keeping on their radar?
How about none of the above? Is that an option because I’m going to go with that actually. With the new administration, I see, like I said, deregulation happening.
The heat rule will probably be number one. I’m really unsure if that’s really going to actually come out and be a federal rule.
The most impact will be at the state level. Because of the administration that’s going in, federal regulation is probably going to take a back seat, but the states will still have the authority to move forward. They can still make additional regulations as much as they want to.
The two states I would keep my attention on, especially from the safety side of things, are California and Washington. They have always been leaders on the West Coast when it comes to employee safety and protecting the employees within the industry.
They typically lead the way. I think Washington originally had a heat rule that came out first. They both have them now.
California also adopted a workplace violence standard earlier this year.
That was a little bit of a burden to get on board with; however, I think a lot of companies have gotten on board with it, and they see some of its benefits as well. New York just adopted a workplace violence standard, too.
So we’re going to see the states actually trying to make their own standards as they see fit since the federal government is more than likely not going to try to overregulate anything, at least during the next four years.
And then there’s actually a department that the Trump administration is creating. Let’s wait and see how all of this evolves, but there’s a new Department of Government Efficiency that’s going to be headed up by Elon Musk and Vivek Ramaswamy. And so they’re going to be taking a look at government structure, all the different agencies that are out there, the budgets, and whether we are spending wisely. Are we overburdened with regulation? Are we overburdened by the number of inspectors out there from some agencies such as OSHA or the EPA?
We could see some department budget changes and cuts. I even saw a bill introduced in the Senate that would eliminate OSHA altogether! However, I don’t think that’s ever going to make it very far in terms of votes or anything like that.
However, that’s what I’m seeing with this Congress that’s going into place. There is a lot of deregulation out there and a lot of government step-back. So we’ll see how that rolls out over the next four years.
[00:13:09]
Since we’ve discussed the state’s influence, maybe we should discuss these specific industries a little bit. Are there any industries, like automotive, construction, manufacturing, and maybe oil and gas, where you’re seeing anything stand out in terms of challenges for the year ahead?
I can definitely see it with construction. We’re going to see additional regulations for the construction industry, such as the personal protective equipment that just rolled out.
Also, when it comes to the heat regulation, if it does pass, which we do have some states that have already passed, that’s not going to go away. Whatever happens to the federal side of things, if your state has already passed it—and I think there are five states out there, maybe six at this point—that have already passed the heat regulation within the state, that’s not going to go away.
Automotive is another one to take a look at as well. Especially with the EV market really continuing to grow, we’re seeing advances in electric vehicle technology. In fact, there’s a regulation out there called the Tailpipe Emissions Rule. We’ll see what happens to that one, but California is definitely moving forward with that, no matter what the federal government does.
The idea is to have almost all automakers be completely electric by the year 2035 or something similar. It may not be one hundred percent, but EV technology is continuing to grow.
And lithium-ion batteries do pose a little bit of a threat. We’ve seen where it’s almost like a spontaneous combustion, what they call a thermal runaway. So, if the battery is exposed to too much pressure and too much heat, there’s a possibility that those cells can actually overheat, producing a fire. And then you have a thermal runaway where you have a cell catching fire, cell after cell after cell. And that could emit some toxic vapors, too.
We’ve seen fires with lithium-ion batteries in some of the laptops and smaller objects out there. But think about a car with a huge battery. Think about a semi-truck with a huge battery in there. And so imagine that catching fire; that’s difficult to put out.
And then one final industry: warehousing. Online shopping continues to grow, and a lot of this is being done by shipping things to warehouses. Therefore, we’re having a lot of automation going on in warehouses with order pickers and robotics. We can see a lot of regulations coming into play for robotic maintenance management in these warehouses.
[00:15:37]
Yes, that makes sense. I feel like I’ve seen a lot about how warehouses are changing. I saw something back in the 2000s of an Amazon warehouse that looked like a human could walk through it. But now there are so many spots where you literally cannot walk through as a human because that’s robot territory.
With all these changes and shifts related to things like EVs or robotics, I think it’s interesting to look at the emerging tech front. As we hear about these tech advancements in compliance, are there other trends in safety tech that we should be paying attention to?
Oh, for sure. Tech is always growing, and it’s always going to evolve. We’re seeing software really grow in this industry, too.
It used to be, how do you keep track of all your training, your incident rates, and all of the things that you need to stay organized as a safety professional? It was pretty much done back in the day with binders. Then, it turned into Excel. It was the spreadsheet phenomenon.
That was the easiest way to keep track because you could really customize it to your needs. Now, software has caught up to that game in specific industries, especially in the safety industry. The software understands incident rates and TRIR, and it can help manage that for you.
There’s a lot of customization with software that’s happening as well. You can spend a ton of time trying to manage a spreadsheet. However, why do that? That is coming to an end. Now, you have intuitive practices out there within an industry where you could customize the software to be your learning management system.
You could set up your own forms to ensure that you are identifying the correct hazards. Then, set up workflows so that when incidents happen, immediate notifications are sent to the correct people.
Then, they can go through an incident investigation the proper way, as opposed to trying to fumble it through themselves. Instead of like playing a cop in a scene trying to do detective work, now you have automatic step-by-step guidance on what you need to do and what data you need to collect.
So software is great. It is making our lives a whole lot easier, but there are also some things that we have to be aware of as AI enters the market. AI can be a great thing. It can make our lives easier, but we can’t rely 100% on it. We’ve got to fact-check. And you know you’re not going to ever have something specific that is spit out of AI. So if you go into one of these softwares that’s AI and type in: “I need a forklift program,” it’ll write you a forklift program, but more than likely, it’s not going to write you a site-specific one.
Because it doesn’t know your site, it doesn’t know the hazards. You may have several different ramps that the forklifts have to go up and down. You may have an overhead sprinkler system that we have to be very cautious of when lifting objects so we don’t hit them.
There are a lot of different things that AI is not going to see. But it’s starting to catch up in the industry. And we can make use of it. I’ve been to a couple of different industry shows where I’ve seen camera systems that can recognize employees’ unsafe behaviors. And so if that’s spotted, it’ll actually send out an alert to the safety team. And then it’s a stop work authority, and we’re going to take a look with that employee: “Oh, this behavior right here, you took off your personal protective equipment at a time when you really shouldn’t have been taking that off, you know? You went 30 minutes without wearing your safety glasses. No, that’s unacceptable in this industry. We wear safety glasses all the time.”
So these things can be caught now by some of the technology.
QR codes. I wish we had QR codes way back in the day. I think they’re great for quick information for employees. Maybe you take a QR code sticker and put it on the back of a clipboard, or I’ve even seen some sites put the QR code sticker on the hard hat itself. You can pull out the iPad, pull out the phone, scan the QR code, and all of a sudden, we’re filling out an incident report.
Once that’s done, it immediately goes through to correct people. We’re getting much more efficient at getting the information back and forth.
One more thing I’ll also include in there, and I thought this was a hoax at first when I first read it in a report, but it actually is legit, is that OSHA is actually testing out smart glasses for inspectors.
These are smart glasses that can start recording when you focus on an object or snap a picture. OSHA is testing them out, and who knows, we might see OSHA really step up its game.
I can see it: When a compliance officer goes in to inspect an area, they’re usually there to inspect a specific spot, incident, or complaint. But if they’re walking around and looking at everything, now when they go back to the office, they have a pretty good representation of everything they’ve seen instead of just a few things they snapped pictures of.
So, it could really help out in an inspection to investigate not only what they were there to see but maybe also other things that they can note.
[00:21:05]
That was absolutely my first thought, too, thinking, oh, a person maybe wouldn’t notice something, whereas the glasses are going to pick up on it. That’s very interesting. I mean, I think it’s been clear for a long time that technology is really reshaping the field of safety.
I think companies still need to address some challenges. Can we discuss what’s tripping them up the most when it comes to adapting to regulatory changes and how they can get ahead of those issues?
Professionals still have to make sure that they’re staying informed. A lot of times, you’ll have an EHS professional or safety manager, and they have multiple sites across the United States and trying to get the information to those sites, trying to get information back, trying to make sure that you have a consistent process throughout all of those is a very difficult challenge.
It’s probably easy to do that at your own site, where you have eyes on it every single day, but maybe there’s a site four states away, and you only get out there maybe four or five times a year. How do you get that messaging out and keep it consistent?
Software is a great way to do that because with software you can actually get the messaging back and forth. Everybody’s a part of the same training program, all from one central database hub. If you don’t have something like that, how do you maintain consistency? That’s a tough challenge that’s out there.
Staying informed, too. Especially if you’re across the United States. Keeping up to date with the state regulations. Not an easy thing to do. I mean, there are 50 different states out there. Not every one of them has a Department of Safety or Department of Labor. But those that do are going to come up with new regulations. How do you keep up with those for only that particular state?
Another challenge is making sure the employees understand the information you’re giving them. Let’s face it, safety is not the most exciting thing in the world to teach.
But it definitely comes into play when there’s a consequence, you know? You never want to be reactive to it. We don’t want to ever be like, “Ah, see, if I just would’ve put my safety glasses on, you know, 10 seconds earlier, I wouldn’t have had this injury or issue happen.”
How do we get that idea in front of the employees so that they understand to do those things before an incident happens?
That’s always going to be a challenge, but I think there are ways to go about it. I think that putting employees in the scenario as much as you can is important. I mean, don’t subject them to hazards, of course. But do drills to see how they react and respond, and are they doing the right thing? Did they actually listen to the training?
[00:23:56]
Absolutely. You’ve already been doing this, but let’s give our listeners some more actionable advice. If a safety manager is listening to this podcast and wants to get ahead start on 2025, what are the three things they can do right now to stay ahead?
Get organized. That’s number one.
You need to make sure that your whole process, your whole system is organized. Like I said earlier, if you’re still operating in spreadsheets, you’re spending a ton of time just trying to keep the spreadsheets accurate. I’m no spreadsheets guru, some of those formulas can really get complicated out there. And you could easily end up with data that’s flawed because of a bad formula or something out there. Take a look at software to help keep you organized.
Another one is to get with your new employees before they’re actually thrown on the production floor. There’s a trend out there where we’re trying to hire as many folks as we can continuously, and sometimes it’s like, “Okay, we got to take who we can get and let’s just put them out there, and you know, throw them to the wolves.”
And that’s where employees get hurt. We don’t want employees going onto the shop floor or plant floor without any safety knowledge or training. I think we are missing the safety component when it comes to new hire training.
Are we getting the actual safety training done before they hit the shop floor, before they actually see those hazards out there, before they hop on that forklift or are told to do so?
I would also recommend having a mentorship program in place for a new safety manager. We can train as much as we can, but we’re usually a small team of less than four people. In an organization, the safety department is usually not that big.
So, your best trainers are going to be the people who have already been in place, the people who have been there for a while, your veterans in the organization. Use them as mentors.
With a mentorship program, you’re doing a couple of things. One, you’re making sure that the employee adapts to the culture of that work site. Two, you’re giving a veteran an opportunity to see if they excel at being a mentor. If they do, then you probably have a great leader on hand here.
[00:26:12]
Absolutely. And that sounds like a great way to keep people involved, too, because if they know that they have an opportunity to mentor and maybe get that promotion like you were talking about, it’s a lot easier for them to want to be involved in that safety aspect and keep the rest of the team safe.
Those are great tips for staying ahead. Let’s talk about how companies can use the data you talked about earlier a little more effectively. It seems like more companies are relying on data and reporting to improve safety. So, how can they use that data to do more than just check a compliance box?
Nobody should just check a compliance box. If you’re doing that, you’re not really in the safety field. That’s not the goal of being in the safety field. The goal is the employee’s safety, right? The goal is to make sure everybody’s going home safe at the end of the day.
So, use your data to take a look at areas of focus: where can we train? Where can we improve within the safety systems that we have?
You know, we may be deficient in one department, but we may excel in a different department. We may be on the decline when it comes to certain training, such as injury prevention, but we’re doing great with our forklift training. So use that data, use the audits that you have, use the training scores that you have, and use all that data to make sure that you are driving your complete safety programs and environmental programs. Make them site-specific and focus on your areas of improvement.
[00:27:51]
Absolutely. That makes a ton of sense. I can see how leveraging that data can truly transform a safety program. So, let’s end with a look ahead at what excites you most about 2025. Can you tell us what you are most looking forward to in terms of the future of workplace safety and compliance as we step into 2025?
We’re seeing a bit of a shift when it comes to that term of compliance. It’s not going to just be compliance anymore because we are going to see potential deregulation when it comes to the federal side of things. It’s going to put the spotlight on and showcase those out there in the safety industry who are there for the benefit of the employee, not just to check a box to be compliant. And that excites me.
I can’t stand it when I hear from an organization that says, “Yeah, just make me compliant.” You know, I’m a consultant, so I go out and see them. We’ll arrive on-site, and they’ll say, “Just make us compliant. We’ve already got a business to handle on the other side of things. You just make us compliant, and we’ll be good.”
No. That’s not how you should actually operate. Because when you do that, you’re still going to be missing the mark as far as hazards go. You’re still going to be subjecting employees to potential injuries in the workplace. It’s more of a shift in focus towards not just compliance but going above and beyond compliance to lower the costs of those claims to make sure that you have a moral conscience on hand for your employees. You don’t want to see them hurt.
You want to make sure that you’re attracting the right people, too. You know, the younger generation is looking at that. They want to make sure they’re working for a safe organization. And I like the fact that we’re starting to see companies take initiatives of their own as well so that they’re not waiting for tragedies to happen.
Like First Aid and CPR training, organizations are really starting to put in AEDs at all locations, not just because it’s a requirement. There’s not actually a requirement out there that states anywhere from OSHA that you have to have an AED in place. But we’re seeing a lot of organizations put it in place because they don’t want something to happen to their employees or their customers that could be a tragedy to their organization.
In addition, they’re training their people in first aid response to ensure that they’re morally doing the right thing, not just because a regulation told them to.
[00:30:09]
Absolutely. And, you know, that’s a great note to end on as we look ahead to 2025. You’ve done a great job laying out what companies should look for in terms of regulatory changes, what may be coming from the regulatory bodies, and/or if they’re moving away from some regulations and also that emphasis on how the state regulations may jump in, and how technology is going to continue to shape the field and the safety space.
Zach, always great to talk to you. Thanks so much for your insights. We’re excited to see what happens in 2025, and we’ll talk to you again in June.
Thank you very much, and everybody, have a safe 2025.
Related Content
Explore more comprehensive articles, specialized guides, and insightful interviews selected, offering fresh insights, data-driven analysis, and expert perspectives.