Unless you’re a safety professional, you’ve probably never given the words “safety inspection” and “safety audit” a second thought. And even if you are a safety professional, you may not have considered that there’s a difference between the two. After all, many people use the terms interchangeably or lump them ambiguously together.
However, if you want to keep your people safe (which you definitely do), you need to know what these terms mean and how they differ from each other. An inspection is not the same thing as an audit—and confusing the two could get you in trouble. Here’s what you need to know.
Safety audits and safety inspections are similar in that both involve an examination of an organization’s EHS program. That said, an audit is distinct from an inspection in 2 fundamental ways:
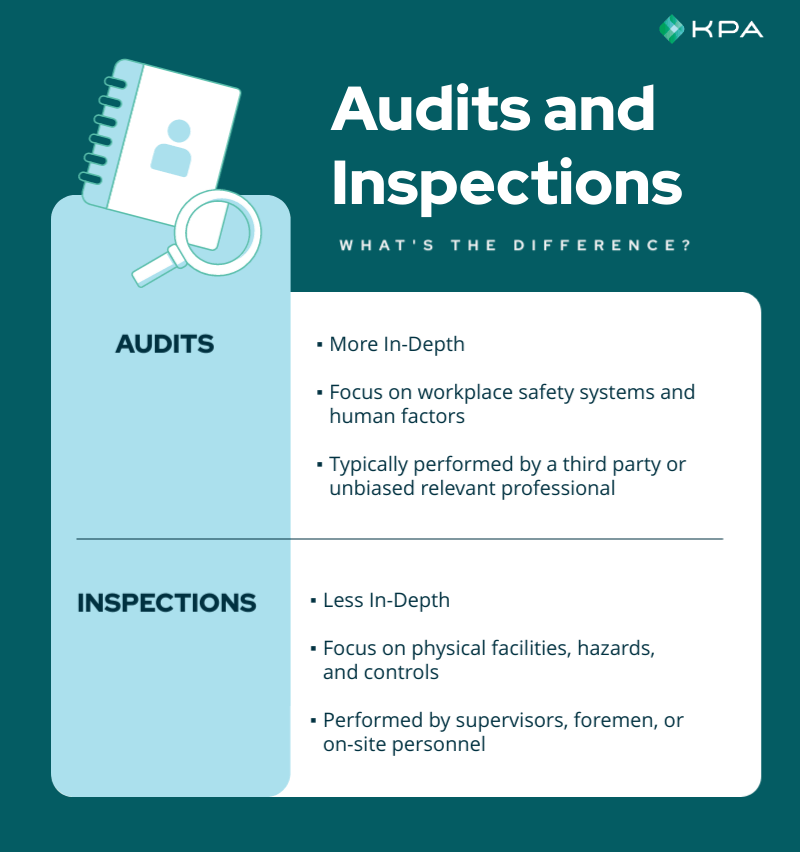
1. Safety audits are more in-depth than safety inspections.
Inspections tend to focus on physical facilities, hazards, and controls. An inspection may center on questions such as the following:
- Are all chemical containers labeled?
- Are there any boxes blocking exit routes?
- Is machinery well-maintained and properly guarded?
- Are workers performing their duties safely and wearing all necessary personal protective equipment?
An audit addresses the same kinds of concerns, but also goes beyond immediate hazards to examine behind-the-scenes workplace safety systems and additional human factors:
- What do the organization’s safe workplace policies look like?
- Are people adhering to policies?
- Is the safety program focused on the right goals?
- What kind of training is provided to employees? Is the training comprehensive and up-to-date?
- Is there any health and safety software in place? Is it the best possible software?
- What data points are being collected?
- Are there any short- or long-term legal risks the organization should be aware of?
- Is leadership truly on board with the program?
- Is the organization investing enough money in safety and using the budget effectively?
- How could the safety program become more efficient?
Essentially, a safety audit determines the extent to which an organization has developed a safety culture—the invisible force that unites people around taking care of themselves and each other.
2. Safety audits and safety inspections are typically performed by different people.
Managers, supervisors, foremen, and other on-site personnel are usually the ones who conduct safety inspections. By contrast, a safety audit is a job for an external, third-party professional.
Note that OSHA allows organizations to perform “self-audits,” which “must be conducted by or supervised by a competent person who is capable of identifying the relevant workplace hazards.” As the agency recognizes, not every organization can afford to hire an auditor, nor does every organization have a person with “engineering, scientific, industrial hygiene, or other relevant professional accreditation” on staff. However, whenever possible, an audit should be conducted by an independent professional.
As discussed above, internal employees and stakeholders lack the objective perspective—and often, the training—to perform audits themselves. They may not know what to look out for, or might see only what they want to see.
Moreover, the time and expense involved in an internally-managed audit frequently exceed the costs of hiring a third-party auditor. Keep in mind that every hour an employee spends on the audit is an hour that could have been spent on work.
Organizations that conduct self-audits without the aid of a third party may also expose themselves to legal liability. In an article in Modern Contractor Solutions, labor attorney Michael Rubin writes:
“As a preliminary matter, if you do decide to perform a self-audit, you should be prepared to implement any required changes to eliminate and/or mitigate any discovered hazards. If you fail to do so, and OSHA later shows up, you could receive a ‘willful’ violation for allowing a known hazard to exist at your workplace. In certain cases, you might even expose yourself to criminal penalties.”
An independent, third-party auditor will not only ensure your audit catches every problem, but that your organization immediately implements the necessary corrective and preventive measures.
Find and Address Issues Before They Lead to Injuries or Worse
Use KPA audit and inspection tools to uncover issues and address them with corrective and preventive actions before an incident occurs. Tailor your EHS inspections to address the areas of risk specific to your facilities.