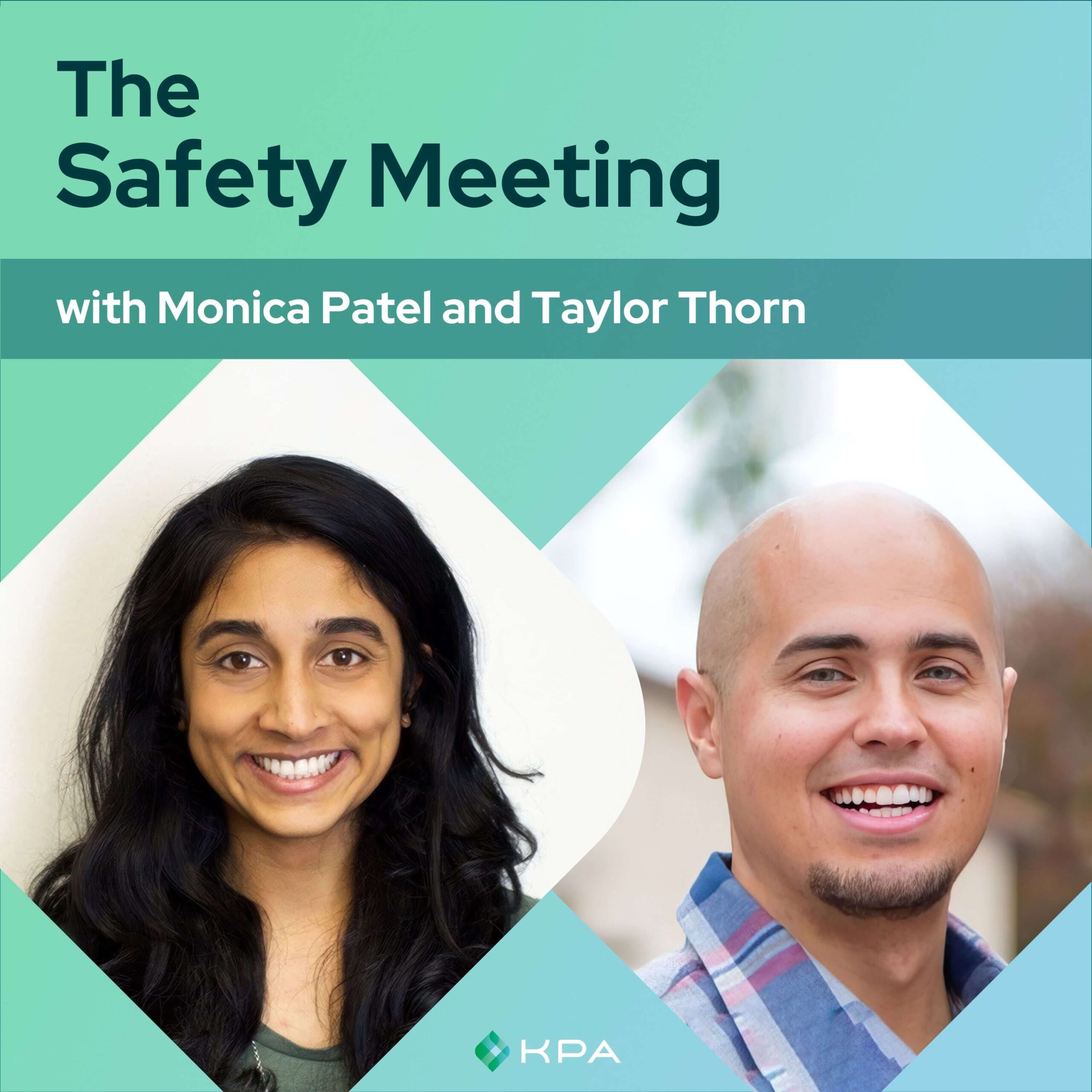
Today we’re speaking with Monica Patel and Taylor Thorn. Monica is the software product manager at KPA, bringing a strong background in engineering and operations and hands-on experience across the energy, technology, and logistics industries. Monica’s expertise lies in leveraging technology to tackle complex safety and compliance challenges, making her a driving force behind KPA Flex. Her passion for enhancing operational efficiency and safety standards is reflected in her commitment to helping businesses integrate innovative solutions into their contractor management practices.
Taylor is the Senior Product Director at KPA and the founder of AnchoRock, a safety and compliance software company tailored to the construction industry.
With over ten years of experience working closely with safety professionals, Taylor has dedicated his career to enhancing contractor management and safety programs. His deep understanding of the complexities of managing contractors and ensuring compliance makes him a key voice in helping companies navigate today’s evolving safety landscape.
Thanks for being with us, guys.
Taylor: Thanks for having us.
[00:01:20]
Absolutely. All right, let’s jump into the questions. So, contractor management is becoming more critical, especially in industries that depend heavily on specialized contractors. Why do you think this shift is happening, and what’s driving the growing adoption of contractor management software?
Taylor: I think that’s a great question and what it really comes down to, at least in my mind, is that more and more hiring clients are relying quite heavily third-party contractors. It’s not necessarily new, but the level at which third-party contractors are being hired is increasing. And when that is happening, we’re seeing a natural increase in potential risk exposure to the hiring client.
So why does the hiring client even go down this path of hiring a contractor? It comes down to at least two things, right? The contractor provides specialized expertise that the hiring client either: can’t perform themselves, or doesn’t want to spend the time to train their staff to learn that specialized skillset.
So clearly the expertise is a big piece of it, but also there’s a economic benefit to the hiring client to hire a third-party contractor. It does ultimately save them a little money. Like I said, they don’t need to learn that trade. They don’t know the trade, so it’s not something they have to invest heavily to become familiar with and experts in that trade.
Hiring a third-party contractor is beneficial to the hiring client. And so we’re seeing more and more of third-party contractors being leveraged by hiring clients in a lot of industries. We’re talking manufacturing, oil and gas, energy, transportation, certainly construction, right?
Construction’s kind of built around this idea of a general contractor and subcontractors, lots of subcontractors. It’s becoming quite the norm. And so with this increase in the hiring of contractors, comes an increase in risk.
And unlike that of their own full-time employees, hiring clients have much less visibility into the contractor’s operations onsite. They have little to maybe no insight into that contractor’s safety practices. That increases the risk exposure to that hiring client.
So with that, this practice of contractor management, prequalification management, and the vetting of third-party contractors has become more and more critical over the years.
And I think technology has certainly helped push this along in terms of the process of contractor management becoming more and more critical for these businesses and their operations. Because tech has changed how they run their businesses and other aspects of the business. And this has just become kind of a glaring hole for some organizations in that, you know, if we’re managing 200, 400, a thousand third-party contractors, there’s go to be a way that tech can help us do that better. Because the methods of storing it in email or trying to track this in Excel aren’t an effective business operation, especially at scale.
And so I think tech has helped push this need for contractor management platforms along. At the end of the day, running their business more seamlessly but also doing it in a way that drastically reduces their risk exposure. I think those two things combined have given this thing a whole push in the back.
[00:04:44]
Yeah, it makes sense that there is a growing reliance on third-party contractors, and like you said, I’m sure there are companies that do have a thousand third-party contractors and how that would bring up some unique challenges when it comes to managing that large body of extra help.
So that actually brings up another question: What are some of the safety challenges that companies face with contractors compared to direct hire employees? How do they differ?
Taylor: What this really comes down to is that the contracting firms the hiring client hires will likely vary drastically from contractor A to contractor B to contractor C.
This variance is a big safety factor in my opinion, because it presents really unique safety challenges. For example, contractors as operating entities themselves, they’re most likely going to have safety standards, safety policies, safety procedures that they’ve set up internally that they use to kind of define: “this is our safety program as a business.” But then when they go on site and work for someone else they may not align with the hiring client’s safety policies, safety programs, safety procedures.
So there’s this lack of alignment, but also contractor A to contractor, B to contractor C, will likely all have different safety programs and practices in place, making it very challenging for the hiring client to align all of that. And so this variance amongst the contractors, I think is a big safety challenge.
Somewhat in line with that would be this idea that hiring third-party contractors brings a risk and a safety challenge as it pertains to training and managing contractor training, and vetting if that training meets the hiring client’s standard. And also determining which contractor employee has specific training to a specific site.
So training management at the contractor level is a pretty clear safety challenge for hiring clients that we talk to, that we work with, that we see in the market. It’s a big challenge, and so figuring out how to get your hands around that and manage that training aspect of your third-party contractors is a concern to many.
I think something else that I kind of mentioned just a second ago, but is probably worth mentioning again, is a lot of industries that are site specific, right? Whether that’s a job site in construction, or a plant or facility in manufacturing, or an oil rig in the oil and gas space. Whatever the case is, site to site, these contractors need to be very familiar with site specific risks.
And when a contractor has that lack of familiarity with the site prior to coming out, obviously they’re not aware of said risks. That’s a safety challenge that needs to be resolved so that when the contractor arrives on site, wherever that site is, that they’re familiar with the risks. They know the risks involved. And all those risks have been mitigated, whether that’s through training or effective communication, whatever case might be. But the risks need to be identified.
But the risks vary from site to site, and we’re talking, at least in construction, could have hundreds, a thousand different sites.
And not that every site will have different risks, but a lot of those sites will have different risks. And so managing that amongst your big pool of contractors, it becomes a pain. And so I bring that up because I do think that’s a big challenge a lot of safety professionals are seeing and feeling right now, in this contractor management space.
[00:08:13]
Sure, and I can see how when you’re coming at this, maybe without tech or trying to solve this problem for the first time, it could seem like selecting and onboarding the right contractors is the most critical point. But I think you brought up a lot of good stuff there about the fact that you could select the right contractors and onboard them the right way, but if you don’t have a way to track what they’re trained on and what is safe for them to do, you’re still in gray area when it comes to putting those people in the right places. Can either of you guys share some practical strategies that companies can use during the selection and onboarding process to ensure that these contractors meet safety and compliance standards, and why that step is so crucial?
Monica: Yeah, great question Kat. So, one of the key things that companies need to focus on is making sure the contractors they bring in are not just qualified, but they’re also fully aligned with safety and compliance standards. It’s not just about checking a box. It’s about making sure that everyone, and this includes full-time employees, but it also includes contractors, understands the specific safety protocols of the site.
The onboarding process is so important because it’s really the first opportunity to make sure that everyone is up to speed. A solid onboarding system also means that you can get contractors working much faster, without cutting any corners in regards to safety, and that becomes so important to avoid accidents down the line.
Our Better Workforce Blog is your Ultimate Guide!
Stay informed with weekly industry updates, expert insights, best practices, and actionable tips to enhance workplace safety and compliance.
[00:09:43]
Exactly. I think as you both know, if companies don’t get that right from the start, it can lead to bigger issues down the line. We already discussed onboarding, but I’m sure you have more tips here. So, what are the most common risks that arise from poor contractor management, and how can companies proactively tackle these challenges before they escalate?
Monica: So when contractor management isn’t up to par, you tend to see issues like safety protocols being overlooked, or even contractors who might not be fully trained on site specific hazards. This creates a real risk for accidents, for non-compliance and even for operational delays. And the best way to tackle that is by being proactive, so having a strong prequalification process in place, so that you can vet contractors properly before they ever step foot onto your site.
And it doesn’t necessarily stop with that initial prequalification. You can do regular check-ins, audits, and real-time tracking of their performance, which can really go a long way in keeping things on track. I actually have an example here from real life.
Back in the day I was an oil and gas field engineer. I did that for many, many years. I specialized in hydraulic fracturing. I was working for a contracting company, so I was an employee of that contracting company. And I was sent to North Dakota in 2011. At that time, a barrel of oil, I think, was a hundred dollars.
And North Dakota was the best place to get that. So my crew and I went up there. We were from California, which meant we knew nothing about the cold. I remember specifically this day, it was negative 18 degrees outside. And we were shut down for something and we didn’t know, or we just didn’t put it together that all of the water in all of the lines needed to keep moving or it was going to freeze.
Frozen water in pipes is extremely dangerous because you end up with something called ice plugs in pressurized systems. And that was exactly what happened. So it caused a huge mess. We ended up having to shut down, bring out a bunch more heaters to make sure that all of the water in the lines could get moving again.
The company we were working for was incredibly mad, because time was money, right? And also it was a really dangerous situation that could have been avoided. So there were the money ramifications of that incident, and then there were the reputation ramifications of that incident.
If we had had rule sets that we had signed off on, or company policy on what to do given specific situations, and cold training right before we stepped foot on that location: it could have been a really different story.
[00:12:34]
Absolutely. I think that’s a great example of how, when bringing in third-party contractors, things can get lost in translation. And you touched on the importance of proactive measures as well, especially in training and ongoing oversight. So I want to dig a little deeper there.
How does training play into effective contractor management? And what can companies do to ensure contractors aren’t just compliant, but also fully integrated into that company’s safety culture?
Taylor: I think there’s no doubt that training is a critical piece in this prequalification process when it comes to third-party contractor management.
Each hiring client knows their sites and their facilities better than any contractor. And the hiring client also knows what type of work is being performed. And with that, we know that specific training needs to be in place. And we know that specific contractor employee training must be held prior to that contractor performing specialized work.
So training of the contractor employee is paramount, and you can look at it in two ways: There’s during the prequalification process, vetting the third-party contractor to ensure that all the training has been met. Maybe that’s through just a quick upload of an Excel file or a training matrix, maybe images of training cards.
That’s certainly one way, and we see a lot of contractors who, that’s a big piece of their requirement management: Please show us proof of training for forklift and mobile elevator, work platforms, whatever it is. That’s common, right? And doing that on the prequalification, on the vetting side prior to that contractor showing up on site.
But I think also the ongoing oversight of this is important, too. And those two certificates I just mentioned, forklift and mobile elevated work platform, typically they expire in a year. And so if the contractor provided proof of training six months ago, but in nine months from now, I don’t have a way to have some oversight there, to automatically see, did new training happen? Did I get a proof of upload for that kind of recurrence or that reissuing of that training?
If I don’t have that oversight, sure I can get it at the front end, but if I am working with that contractor year over year, and I don’t have the continual oversight to see that that training is continuing, I’m at great risk.
So that’s a big piece of it. But I think equally important is this idea of, the contractor coming on site and getting involved with your safety culture, your safety program, your training policies and practices is something that’s really of interest and important to a lot of folks we’re talking to, and a lot of folks who we’re working with.
Getting the contractor employee to something as simple as safety orientation training, right? We use that example a lot when we’re talking to people around contractor management, but it’s important. You can have a site specific, a facility specific, a plant specific, whatever the case is, safety orientation. An orientation that you, the hiring client, were able to curate, put it together, and you make that a requirement that the contractor employees, when they come on site, either they’re going to complete this before they come on site, or they’re going to go off to the side once they arrive, and they’re going to complete this 10, 15, 20 minute orientation training.
We’re seeing that become more and more normalized, and what it does, is not only ensures that those risks and the hazards are being identified and properly communicated to the contractor employee, but it’s getting that contractor employee kind of wrapped into your safety mindset, your safety culture.
“This is what we do. This is normal for us. This is how we operate as a safe organization, and we expect you to follow that as someone who is working on site, on our job, on our project, at our plant.” And so two pieces there, right? The prequalification side, certainly verifying, but then as a contractor employee arrives on site, considering LMS level training for the contractor employee.
We’re seeing that become more and more the norm.
[00:16:39]
That makes a lot of sense. I mean, for a regular employee, you’re making sure that they go through training, so why not make sure that you have some specific training for those contractors that come on site. I think you touched on this a little bit in your response, but I’d like to hear a bit more about how having real-time visibility into contractor compliance and performance can transform the way that companies manage their contractors, and maintain safety standards, and what that can do for an overall safety program?
Monica: Having real-time visibility can be extremely beneficial. So instead of waiting for like a quarterly report, or relying on a past audit, you can see exactly what’s going on with your contractors in the moment. It lets you catch potential issues. That could be something like a lapse in safety certification. It could be somebody falling behind on performance metrics. And it lets you catch those issues before they turn into bigger problems. This can really help stay ahead of something like potential legal or financial risks, and also make sure that operations stay efficient and safe at all times.
[00:17:47]
It sounds like realtime oversight can be a gamechanger, allowing companies to catch those potential issues before they become major problems. Do you have an example of a company that faced significant risks, whether legal, financial, or operational, and how implementing an effective contractor management program helped to mitigate those exposures and prevent a potential setback?
Taylor: Sure. I was speaking to a pretty large electrical contractor the other week. And this scenario is before they started using a platform and a system to manage this. So it’s kind of the “pre” side of it. What can happen if you don’t have a good system in place, but are managing 600 to 800 contractors on a yearly basis.
They had a couple people owning that, trying to manage that, and they were doing it all through sending out a PDF packet, and then waiting for the response, and storing it in shared folders under one drive. And that’s fine. But at 600 to 800, things will slip through the cracks. And that’s the story that I was told.
Ultimately what happened is something did slip through the cracks, right? Of the 600 to 800, there’s probably 20% of them are pretty small operations. But they’re very specialized and they relied heavily on these types of contractors.
So, one of those smaller contractors didn’t submit a document that the hiring client deemed required, but it didn’t get caught. And ultimately, luckily for the hiring client, it was purely a near miss, and they were starting to see some trends out at the jobsite and started to dig a little deeper and caught this before it became a real issue.
But it slipped through the cracks, right?
Monica and I see a lot of contractors who require that their third-party contractors, during that prequalification process, give their OSHA logs, and we see that’s pretty normal. And that was normal for this example as well. But one happened to not submit. It got through the system. It was kind of outta sight, outta mind.
I hate to say it, but it was this whole black hole effect. Kat, you’ve heard me talk about the black hole and it’s hard to keep track of all that data when you’re managing at that level of contractors.
And so that smaller contractor ultimately having some issues on the jobsite caused the hiring client to dig a little deeper. They realized, “oh shoot, we don’t have this on file.” They were reactive at that point, and they got it up to par, but what would’ve happened had there been an incident or an issue or even like damage to a vehicle. With that contractor it could have been a really, really big headache. Not only financially, but could have put the hiring client in jeopardy with the organization they were hired by.
So, a lot of risks there that could have gone the wrong way. Luckily it didn’t. And only a couple near misses and it was able to get rectified. Long story short is that the hiring client now uses software to help manage that process.
And they are doing this in a way that that contractor would’ve never even gotten onsite because they have systems in place now. They have real-time visibility to that data we’re just talking about. And they have someone at the site who’s doing access control, all before any contractor comes onsite. Someone is doing a quick search to ensure that they’re approved, and all those requirements are vetted, and they won’t be approved if they haven’t submitted their OSHA logs. And so that doesn’t happen now, but it had happened in the past because they were handling such a large data set without an effective way to manage it.
Monica: What a great example. I have one as well. I wasn’t directly a part of this example, but I remember it happening in 2018. There was a neighboring oil and gas operating company that was fracking out in Weld County here in Colorado. And one of their pump trucks, on location, caught on fire.
Which is not a common occurrence. But it can happen, right? And there is a protocol for that. So luckily everyone on that location knew exactly what to do. So they do keep little fire extinguishers by each pump truck on location, but a lot of people don’t realize that those aren’t really put there to fight the fire.
They’re really there to get whoever is closest to the fire out of the situation. So, everyone was accounted for on that location. They knew the muster points. All of their contractors knew the protocol. And the worst thing that happened was a few frack pumps caught on fire, right? So there was some financial risk there, but luckily everyone stayed safe.
[00:22:22]
Incredible. Thank you for sharing both of those examples. I think they really highlight the importance of having a solid contractor management system in place. But there’s always a challenge of balancing that safety with efficiency, especially for the routine tasks like the janitorial or the groundskeeping services.
So how can companies keep operations smooth, without letting those safety standards slip?
Monica: Yeah, it’s definitely a balancing act, as you stated, but it totally doesn’t need to be complicated for those more routine tasks like janitorial or, or groundskeeping. Automating compliance checks can really help. And you can still keep things really efficient.
So, clear safety guidelines from the start along with the tools that track ongoing compliance can make sure that even the contractor handling these routine jobs, are always in line with your safety standards. It’s all about setting the right expectations from day one, and using the right systems to make sure that everyone is completely on the same page.
[00:23:24]
Yeah, it’s clear that managing that balance is really an ongoing effort. Something that you’ve got to do day-to-day rather than just set up once and let it run. So now that we’ve tackled what can be done today, I want to look ahead in this space. What trends do you see shaping the future of contractor management? And what should companies be doing to prepare for these evolving challenges?
Taylor: I think there are a few trends that we see likely coming down the pipe in the next few years. One certainly being visitor management, worker management, this idea of who is onsite at any given time. Can I pull a quick report on demand and see, all of the contractors, these are the contractors’ names, but also these are all the contractor employees who checked in onsite. They’ve been here this long. They checked in at this time. They’re going to leave at this time. All the timestamps that go with that. So, visitor management.
Monica and I are hearing from clients, quite frequently is that something that’s desired as a kind of a extension of a lot of what we talked about today, on the prequalification, the vetting side. The contractor shows up on site. There’s certainly a lot of room for growth in visitor or worker management. And on that same thread, in that same vein would be the contractor employee shows up onsite. We’ve done the pre-qual, we’ve done the vetting. We know they’re good to go from that aspect, but can we get that contractor employee involved in our, our being the hiring client’s, onsite safety program?
Maybe we have a specific audit that needs to be performed on a weekly basis. Maybe we want all of our contractor employees submitting our equipment pre-use inspection, our forklift pre-use inspection and the other piece of equipment out at the site. And so getting the contractor employee involved in the day-to-day onsite safety is certainly something that we think will expand in the future, and be something that ultimately hiring clients desire and want.
And then the last piece, you know, I have to say it because I feel like everyone’s talking about this in terms of where things are going with tech in the future, but AI will likely come into play.
The obvious example to Monica and I, because we’ve heard it a million times now, is: Contractor submits a certificate of insurance. That’s almost always one of the most commonly tracked requirements during the prequalification vetting process is that certificate of insurance. Well, those documents are almost always the same, right? The accord document that gets submitted, can we use AI and some machine learning to do document intelligence and scan that document and pick up the coverage amounts and when it was issued and when it expires? And who the insurer is, so on and so forth?
Could that all be collected automatically? Maybe some thresholds are set by the hiring client and it’s automatically approved or denied based on the document intelligence that’s happening in the background.
So, you know, that’s one example, but there’s certainly others in terms of geofencing and wearables on the site and marking areas that are restricted in terms of access. And now your contractor employees aren’t going to walk into an area because they’re going to be notified immediately if they are, because we’ve kind of marked that all out. There’s a lot that can happen in this whole world of artificial intelligence. But I do think it will be something that becomes important to folks who manage contractors in terms of just making their day-to-day more effective and efficient.
[00:26:49]
Amazing. It’s so wild to think about not only how much technology has changed in the past 20 years, but how much, I’m sure now that we have AI, it’s going to be wildly different in just the next five, the next 10 years, to see how that’s going to change. So I know for sure it’s going to reshape the landscape of so many industries when it comes to what you can accomplish.
Alright. Well this has been a great discussion today. I think we’ve touched on the growing importance of contractor management, the unique safety challenges there, the critical role of onboarding, training, and oversight when it comes to keeping contractors aligned with safety standards.
Your insights on real-time visibility, balancing that with safety and efficiency, and the emerging trends that are shaping the future of contract management have been invaluable. So thank you both for sharing your expertise and experiences. It’s clear that proactive management is the key to navigating these challenges. So I appreciate your time and I’m sure we’ll have you both back on soon, and I look forward to continuing the conversation.
Taylor: Thanks for having us.
Related Content
Explore more comprehensive articles, specialized guides, and insightful interviews selected, offering fresh insights, data-driven analysis, and expert perspectives.