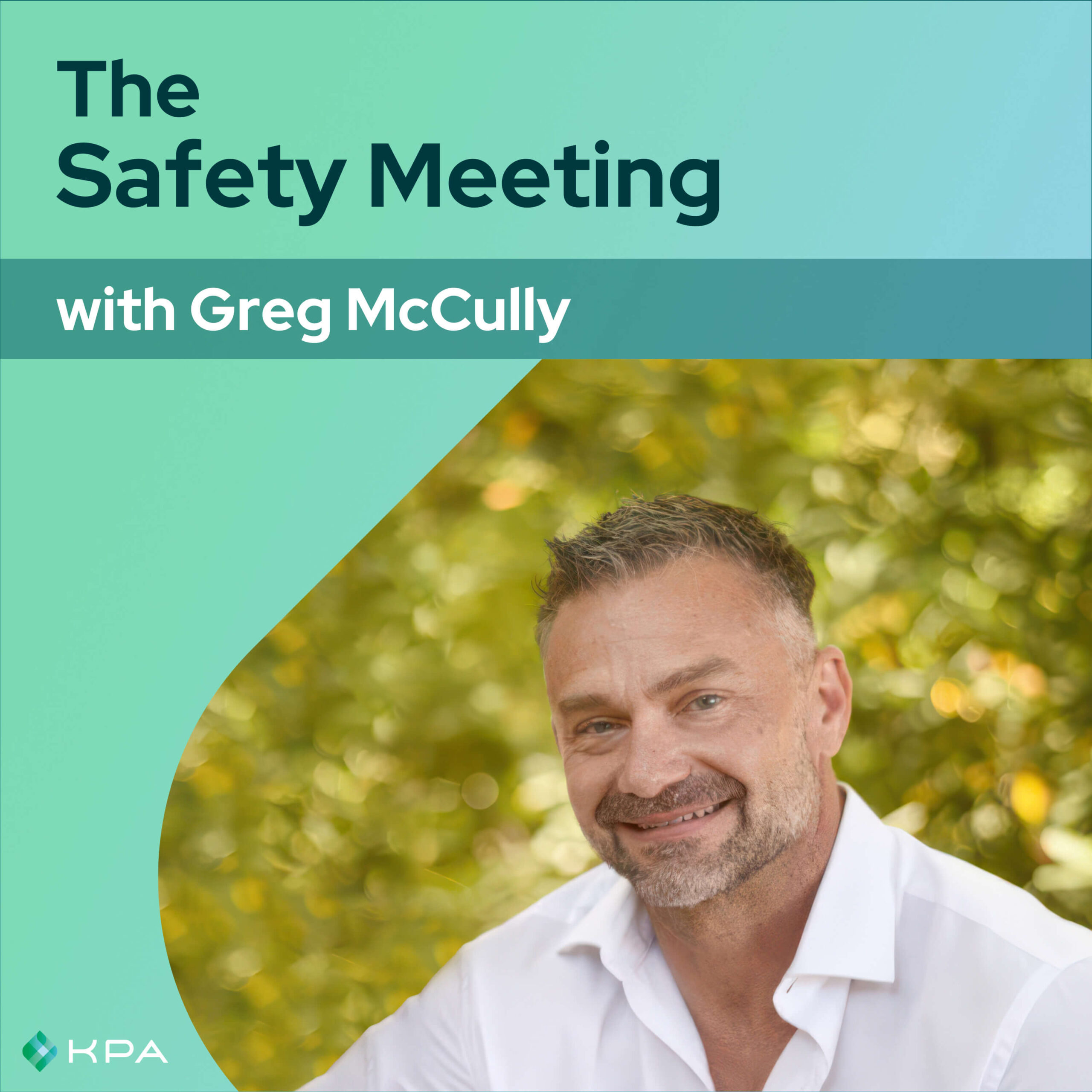
Today, we’re speaking with Greg McCully, a board-certified safety professional with over 20 years of experience. As the founder and managing partner of 2Six Advisors, Greg leads a safety consulting firm that draws on his extensive background in HSE leadership across industries like construction, oil and gas, shipbuilding, and aerospace.
Before 2Six, Greg served as the HSE Director for an ENP company in Western Pennsylvania, helping companies achieve top-tier safety standards.
Thanks for being with us today, Greg.
Thanks for having me. I’m excited to be here.
[00:00:49]
Alright, let’s jump in. I want to start with a more general question here. It may seem reductive, but I think it’s an important place to start when you’re thinking about your safety program: Why do you believe that environmental health and safety or EHS is critical for companies today?
Well, I mean, there are a lot of costs associated with those things for companies, but I feel like the ones that are the most successful with environmental health and safety are the ones that actually do the things they need to do because they care.
I grew up in Western Pennsylvania, doing things outdoors. My kids do things outdoors, too: fishing, hunting, and so on, and we just want to make sure that we’re leaving good places for them to continue to do those things. They need to breathe clean air and have clean water to drink. On the safety side, it’s the same thing.
We have to care about our workforce. The employees are mothers, brothers, sisters, and fathers just trying to go to work every day and earn a living so that they can do the things that they love and support their families.
[00:01:54]
I think this is spot on. Caring for the environment so that future generations can also enjoy clean air, water that they can drink or swim in, and the outdoors, just like we did, makes a lot of sense. And caring for your workers so they can go back to their families safely is absolutely paramount.
So, with this foundation of care in mind, I’m curious: How do you approach identifying and managing the unique risks that different companies face?
Well, there are some consulting companies that have the same approach every time, I think, and we don’t do that.
We get to know our clients. Every client is different, and so are their challenges, what they have accomplished, and what they need to accomplish. And their cultures are different. The culture is probably the most important thing to understand before you start making changes.
So we get in there, get to know our client, and get to know their needs. We always try to understand what changes are needed. That’s sort of the easy part. We go in and do an assessment. There are a lot of people who are good at doing that.
But how do you take those things that need to be done and implement them in the right order? How do you implement them at the right time, when the organization is actually ready for that change?
We usually put together what we call a roadmap. These are the things that need to be done. We risk-rank them to figure out which ones are the highest risk, but we also need to understand the culture of the organization to understand when those things can actually be implemented and be successful. Because if we just throw it all at them at once and say, “This all needs to be done,” people will get overwhelmed, and it’s just not going to be successful.
[00:03:25]
Absolutely. I can see how throwing everything at the wall when it comes to a safety program isn’t going to work. As you said, every company has its own culture and challenges, and you really have to dig into what that company is looking for in terms of enhancing its safety program rather than just trying to do everything all at once.
Speaking of those challenges, I know you’ve worked with many different types of clients, but are there some common health and safety challenges that you’ve seen, kind of across the board, no matter who you’re working with?
Yeah, it’s been pretty consistent, but it’s sort of twofold. So you have organizations that do have a safety person or team of people that are dedicated to the safety department, and the main challenge is they get so inundated in the day-to-day things that they don’t have time, or forget to step back, and just kind of look at the organization as a whole and say:
“What are our challenges? What are things that we need to be looking at for our future? What are the things that we should be doing so that we’re prepared in a year, two years, five years, for either the growth of the organization or just the challenges that we’re currently facing?”
They get pulled into meetings daily. You may be out reviewing an incident, and it’s just those day-to-day things that eat away at your time, and you never really get to step back. It’s kind of being lost in the forest. I used to work in a restaurant, and we called it being in the weeds. You know, you’re in the weeds and really can’t step back and look at that big picture.
So, organizations that have a safety department are the number one thing that we see. And when we come in, we can do one of two things, or maybe both. We’ll come in and help them with that big picture. Say, “Okay, what are you seeing? Let’s look at the information you have and figure out what’s going on in the organization and where you need to be.”
Or sometimes, it’s just taking things off their plate. A company was trying to write a corporate emergency response plan. It took them two and a half years just because they kept getting pulled away from it. Well, if you hand it to us, then it’s done. It’s just done, and that’s nice. I was in the shoes of a corporate safety director, and it’s nice when you can hand something off to someone, and it’s done the way you’d like it to be done, and it’s just off of your plate.
The other challenge we see is the organizations that aren’t quite big enough to have a full-time safety person, and we get a lot of calls, and they say, “Can you write us a safety manual?”
And my first question is, “Why?” Because they think that the safety manual will be the thing that does everything they need to do for safety in their organization.
It’s just more along the lines of they know that they want to do something for their employees. They know they need to do something for their employees; they just don’t know what it is. So, in that case, we will go in, and it’s the same approach: you figure out the organization’s culture and what they actually need, and we only build what they need.
It’s not the same manual we build every time, and I know some organizations do that, but I don’t even like to call them programs. I call them tools. We build tools for them to be successful in what they need to analyze and reduce the risks for their employees.
[00:06:32]
I see. It sounds like whether the company has a dedicated safety professional or not, they can face a wide array of challenges. And for those with a safety professional, the day-to-day can overshadow the big picture. I know many companies are always looking for more resources, time, and people, and it can be tough to keep up with the day-to-day when you’re trying to look at the big picture or vice versa.
I think the day-to-day is probably always going to be more important than stepping back and saying, ” Oh, how can we change?” You’ve got things that you’ve got to take care of, and maybe people who are being injured on the job, that definitely takes precedence.
I know we hear from many of our listeners that one tool that can really help with these challenges is EHS software. Can you discuss some of the key benefits your clients have experienced by incorporating software into their safety protocols?
Yeah, I mean, one we just finished talking about is how everyone has limited time. The software really helps with getting the data that you need easily. It’s all in one place.
You’re eliminating shuffling paper. We see many organizations prior to using the software. They have everything on paper. And then someone has, say, an incident report. So, incident reports all come in on paper. First of all, people who have to complete the incident reports hate completing them on paper because they take a longer time to do.
We’ve seen those paper incident reports lost or finally found when we’re auditing. They’re two years old, and no one has really put eyes on them, so filling them out was worthless at that point. And then when the paper does come in, someone’s taking that and probably typing it into a spreadsheet somewhere, trying to run reports. Maybe if they’re a little proactive, they’re trying to figure out what’s happening.
So it’s just cumbersome, and you end up either with a person who’s really overwhelmed and can’t keep up with it or needing a full-time admin person just to handle that.
I like the software because it puts everything in one place. Especially if you get the right software, which can really do everything for you from an environmental, health, and safety perspective, you can have all of your documents in one place. You have any form that you need, from fire extinguisher inspections to forklift inspections to incident reports, all in the same place.
And for the employees, that’s important because it’s one login. I log into this place and know I can get anything I need. The safety department is telling me that I need to complete a form or my training; it’s all there. One login. I’ve been part of organizations where we have a login for safety data sheets. We have a different login for incident reports. It’s a nightmare, and it becomes almost as bad as the paper just because you have so many logins, and it’s difficult to use.
We have to make it easy for the employees because the easier we make it for them, the more likely they are to complete the documents.
Through KPA, for example, if you do an incident report, I mean, it’s, say, two minutes, but it’s probably less than that. And you have your photos, all of your information. They do it through their app: sent, done, and it’s on to the next person. There’s no lost paper. There are no other problems that we’ve had with not having the software.
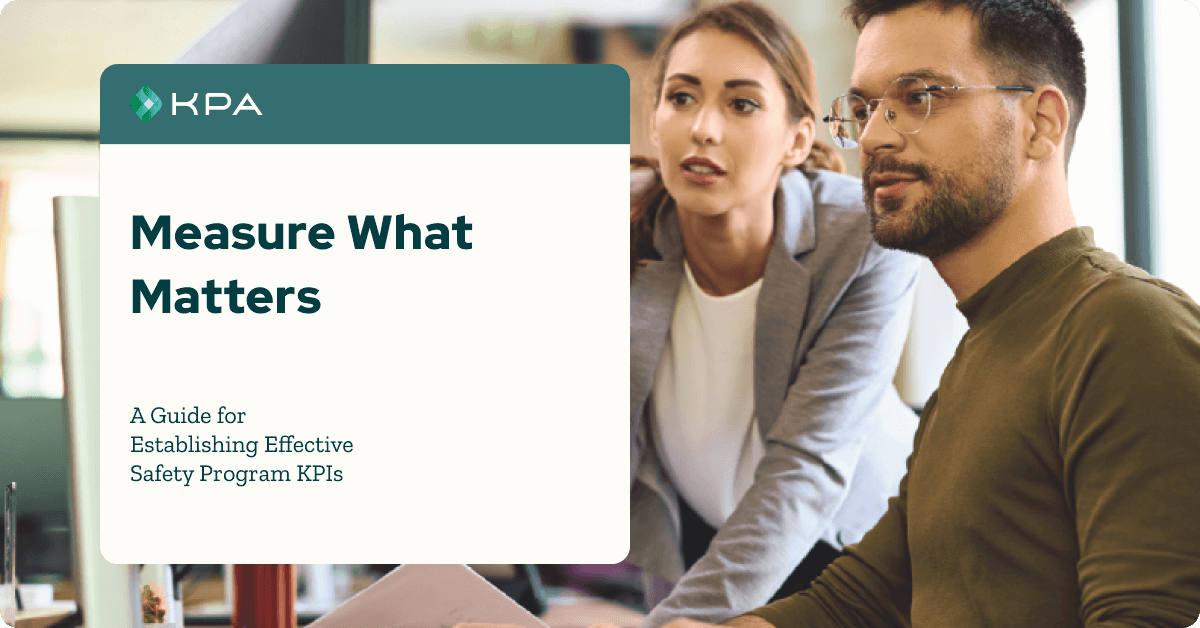
Your guide for establishing effective safety program KPIs. As organizations continually strive to improve their safety standards, the role of Key Performance Indicators (KPIs) in shaping an effective safety program is more crucial than ever.
[00:09:45]
The idea of simplifying processes and centralizing everything sounds like it would make a huge difference, especially when it comes to keeping everyone on the same page. But I know efficiency is really important when it comes to programs like these. How are you measuring that these health and safety programs are truly working well?
I’d like to step back for one second and ensure you’re choosing the right software. We’ve had many clients in the past who tried different software. If you wanted any change at all, you had to send it back to the company, and they had to make a software change that usually resulted in some sort of cost. Then, it returned to the client, and it became cumbersome once again.
So you really want to find software that you can customize yourself, and what a lot of organizations will find then is that it’s almost like Christmas. You’re like, “Well, I can put this in there. I can build this form in there. You mean I can build this form in there?”
So you get the forms you need and a workflow. And I think that’s the important thing because we have paper forms or other types of forms, and they get completed. But there’s no true workflow to say, “This is where it goes next.” You can’t visually see it.
The nice thing about the software is you can visually watch it move and assign it to different people, so the actions are assigned to people. You can track those actions to closure.
So, I think that’s the important foundation for ensuring you have the right software. But the other things are: You can take all of your, any form or checklist or whatever that you already have, and you can put it in this digital form and really watch the workflow, assign actions, and I think that’s one of the things that we, at 2Six, probably help.
If a software company sells its software to an organization, you’re relying on that organization to really understand all of the software’s capabilities and organizational needs. Well, if we’re already in there and we know the culture, the organization, their needs, and the software really well, we go in, and we just build it all out and use experiences from other organizations.
We have one company that we’re using KPA software as their whole maintenance system, and one of the things they really liked about that was that the maintenance department might get a work order that comes in, and it’s an adjustment of a guard, for example. Well, they don’t feel comfortable modifying a guard without the approval of the safety department. So we have a management of change process that’s all built into the KPA workflow that says: this is a management of change that’ll kick it to the safety department. The Safety department has to review and approve the changes to ensure we’re not creating additional hazards. So everyone signs off, and it works. It moves through, and we have a documented digital record.
I think I may have strayed from your topic a bit there, but those are just some things that I wanted to make sure we covered that have been so beneficial with using the software.
[00:12:53]
That’s totally okay. That was a great insight, and I know that including employees in the process makes a lot of sense. They’re on the front lines, after all, so their feedback is critical.
It’s also interesting how you mentioned that incident data can provide those insights, but it isn’t the only indicator of success. But adopting EHS software sounds like it could be a game changer from what you’ve talked about so far. But I know it’s not without its road bumps:
So, what are some of the common challenges that companies face when just starting with EHS software?
I think the common challenge of getting started is that they probably purchase the software for a specific reason, whether it’s the incident reporting or the training element. It’s usually either one or both of those, and that’s what they run with.
The nice thing about training is that you can build a training matrix and assign specific training to specific individuals based on their needs and risks. So, companies will tend to either buy it because of the incident reporting or the training but not really think about all of the other uses.
So we’ve pulled in quality departments and said, “Hey, I’m sure you’re doing a lot of the same thing. You have quality defects that you would track like an incident, and you want to track those to closure. Let’s utilize the same software to do that.”
One of the challenges is that getting everyone involved takes some time and gathering all the information you need to work efficiently.
So that’s a basic challenge you’re going to have with every software, but the other one is, like I said, don’t limit yourself to those things you purchased it for. Start looking around, and every time there’s a form or a workflow, you could probably use KPA to handle that.
[00:14:45]
Absolutely. It’s clear that choosing the right software and really understanding how to leverage its capabilities can be a bit of a hurdle. There seem to be so many different pieces that you have to think about when it comes to making that decision. And I’m sure it can be tough when you’re kind of siloed in your own place, just thinking about what your company does and not necessarily what an EHS software can do to change those things for you. But once it’s dialed in, it seems like the benefits of the software are well worth it.
As we look into the future, safety and health consulting trends constantly evolve. What trends do you see on their horizon, and how are 2Six Advisors preparing to meet those future needs?
One of the things we’re seeing is that smaller organizations are being held to a standard of safety that they may not have previously been exposed to. Just understanding that there is a need for analyzing and mitigating risk in their organization at some level.
In the past, I think many of these small organizations just kind of went to work, did what they did, came home, and hoped people didn’t get hurt. But now, sometimes, they’re getting contracts with bigger companies, and they’re asking them to do different things from a safety perspective. So, we’re seeing more questions from that group of employers.
A lot of times, what they’re doing is they can’t afford to hire a safety person, so they’ll just kind of point to someone that has some background in either. What we see a lot is fire department or emergency services like EMT or something like that. They’ll point to them, or sometimes it’s the HR person, and it’s, “Hey, we need you to manage safety for us,” and then their eyes get really big, and they’re like, “uh, okay, I’m not real sure what that means, but I’ll do my best to do what I can.”
So, we put together a membership where those organizations can sign up for a monthly fee, but they get access to our full team. They can chat and ask us questions so that we can steer them in the right direction.
But the other piece I think is really important is training them on how to be safety professionals. So, “What should I think of in my organization as a safety professional?” I mean, things anyone would think about: well, I want to go out, and if something doesn’t look quite right, then do something about it. And then maybe there’s a guard missing, or we want to make sure that our people are trained, but what does that really mean?
We train every month on those types of topics and also monthly on a topic they can utilize for their employees. So, there are some trainings that every employee in the industry needs.
Like HazCom, we want to ensure that they’re educated on the chemicals in their organization. So, we would do a HazCom training that they can either put up the webinar, and we’ll train them, or they can take the content that we build and train themselves. So, I guess it’s a bit of a safety toolbox for someone who has never managed safety in an organization before.
[00:17:55]
It’s really cool to hear about the proactive steps you’re taking, especially for smaller companies that might not have the resources for a full-time safety officer. Providing them with access to and expertise in this training is a great way to ensure they’re not left behind, especially when it comes, like you said, to those smaller companies and those pillars of the community.
Like you said, firefighting I think, is a great example. I’ve heard many things recently about how firefighting organizations do not have the resources they once did, so it’s cool to hear how you guys are helping to support those smaller companies. Before we wrap up, is there anything else you’d like to share with our listeners?
I think the number one thing is, and it’s kind of my mantra for safety professionals, that the best thing that we can do is listen to the workers. I think we spend a lot of time doing that, whether we’re making changes or providing training or if there’s a change to a rule. We need to go out and talk to the workers.
They’re the experts in what they do daily. Talk to them, have conversations, get to know them, and bring them into the conversation about the SOP that we’re building or making changes to. No one will know it better than they are, so we need to talk to them and say, “If we make this change, is it going to work?”
Because if it’s not going to work, then they’re not going to do it, and we may be creating more of a hazard. So I guess we’re circling right back to caring. The whole reason we do what we do is because we care about the people who are out there doing their tasks every day. So we shouldn’t just tell them what to do; we should involve them in the whole process.
[00:19:26]
I love it. Bringing it back to caring in the first question, and it makes a lot of sense. I mean, it is paramount that we care for our employees and that they go home safe to their families every day. Thanks so much for sharing all of your insights.
It’s clear that the world of EHS can be very complex. But with the right approach and tools, companies can create safer and healthier environments for everyone.
I appreciate it. Thank you.
Related Content
Explore more comprehensive articles, specialized guides, and insightful interviews selected, offering fresh insights, data-driven analysis, and expert perspectives.