The construction industry is one of the most hazardous in the US. According to the National Safety Council (NSC), the construction industry experienced the largest number of preventable fatal injuries in 2020. There were 957 fatalities and 250,000 medically consulted injuries in the construction industry in 2020. Investing in safety can prevent accidents and fatalities and save companies money in the long run.
Think of safety incidents like an iceberg. There’s the costs you see and the costs you don’t. Accidents have a significant impact on construction projects, and can result in expenses that can quickly add up to thousands of dollars.
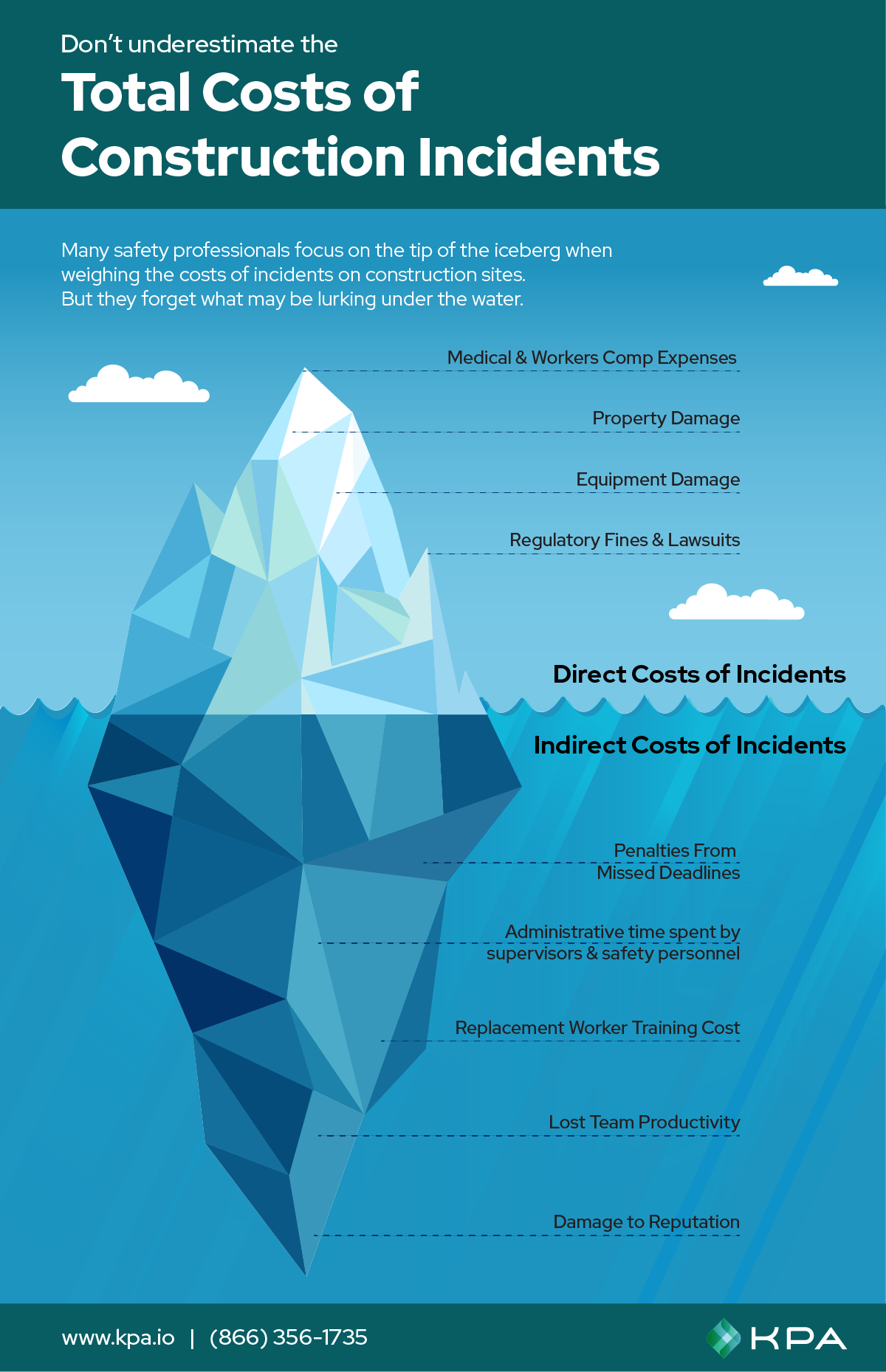
The tip of the iceberg, or direct costs of a construction incident can include things like:
- Medical bills,
- Damage to materials, equipment, or property,
- Litigation, and
- Regulatory fines
But, looking below the surface, construction accidents can also lead to indirect costs, like
- Hiring replacement workers,
- Penalties for missed deadlines, and
- Costs from implementing corrective measures.
In high-risk industries like construction, indirect costs can be much higher, sometimes several times higher than direct costs.
Calculating the Costs of Construction Injuries
For construction companies, the average cost of one lost-time injury on a job site is $35,000, though many injuries cost much more due to litigation, medical expenses and compensation, according to the Workplace Safety and Insurance Board. Further, 6-9% of construction project costs are workplace injury related, leading to long-term increases in insurance costs and shrunken profit margins. A severe or deadly accident can mean the end of a project or company.
According to the Occupational Safety and Health Administration (OSHA), US companies pay over $1 billion per week in workers’ compensation for disabling and non-fatal injuries. Preventing these accidents means protecting the lives of workers, while offering major savings for their employers. It is estimated that the full impact of workplace injuries and fatalities cost companies approximately $151 billion per year.
The human impact of accidents is even more significant and important than financial losses. In 2020, the US Bureau of Labor Statistics (BLS) reported 2.7 million work injuries and illnesses, and 4,764 workplace fatalities. One fifth of those fatalities occurred in the construction industry.
Investing in Construction Safety
On many construction projects, safety is often viewed as a necessary expense, something that must be included in the project but is often a waste of money and time.
Studies have shown that the cost of doing nothing is much higher than the cost of prevention. According to one study, when companies invest just 2.5% of project costs into safety training and procedures, accident rates decrease and profits increase by 4-7% per project.
When comparing accident and injury prevention costs with accident costs, doing nothing is far more expensive. A NSC survey showed that every dollar invested in prevention saves $2 in accident consequences. The NSC also estimates that each prevented injury or illness saves the employer $37,000, and each prevented fatality saves $1,390,000. And multiple studies have come to the same conclusion: doing nothing about construction accidents is 200% to 300% more expensive than investing in prevention measures.
When an accident does happen, the consequences can be far more expensive than the money and time spent to prevent them.
5 Keys to a Solid Construction Safety Program
1. Develop a written safety program.
To make it stick, talk frequently with employees about the importance of safety. Hold employees accountable for breaking the rules through progressive disciplinary steps, and reward them for following procedures. Make managers responsible for their teams’ group safety records.
2. Complete a hazard analysis for every job activity.
Preplanning will save you lots of headaches. Analyze each specific activity for each job. What are the hazards, how can you mitigate them and which equipment will you need? Create an equipment list for that activity. Train everyone who will be on that jobsite.
3. Use toolbox talks as safety training opportunities.
It’s a best practice to use toolbox talks as a platform to complement your existing safety training program. Use the job hazard analysis as the basis for your content, and you’ll achieve three objectives at once: reinforce previous training, meet the requirements of CFR § 1926.21(b)(2)—Safety training and education and reduce injuries on the jobsite.
4. Train new hires before day one on the job.
Make it specific to their type of contracting work. Electricians should have different training for scaffolding work than a plumber, for example. Construction firms have specific challenges when it comes to new-hire training. Your company might have to address double the number of subjects as an auto dealer, for example. Even the most minimal orientation training can take half a day or longer. But since most construction worker injuries occur in the first year of employment, the investment in more comprehensive onboarding training is a no-brainer.
5. Provide proper training for your “competent persons.”
OSHA requires a competent person to be on-site, which is someone who:
- Is capable of identifying existing and predictable hazards in the surroundings; or
- Working conditions that are unsanitary, hazardous or dangerous to employees; and
- Is authorized to take prompt corrective measures to eliminate them.
KPA Can Help You Sell Safety to Your CFO
Looking for hard evidence of the business value of EHS software? Want an industry pro on your side as you make your case? KPA has the data, case studies, and expertise you need to speak fluent CFO. Ask us how we can help.