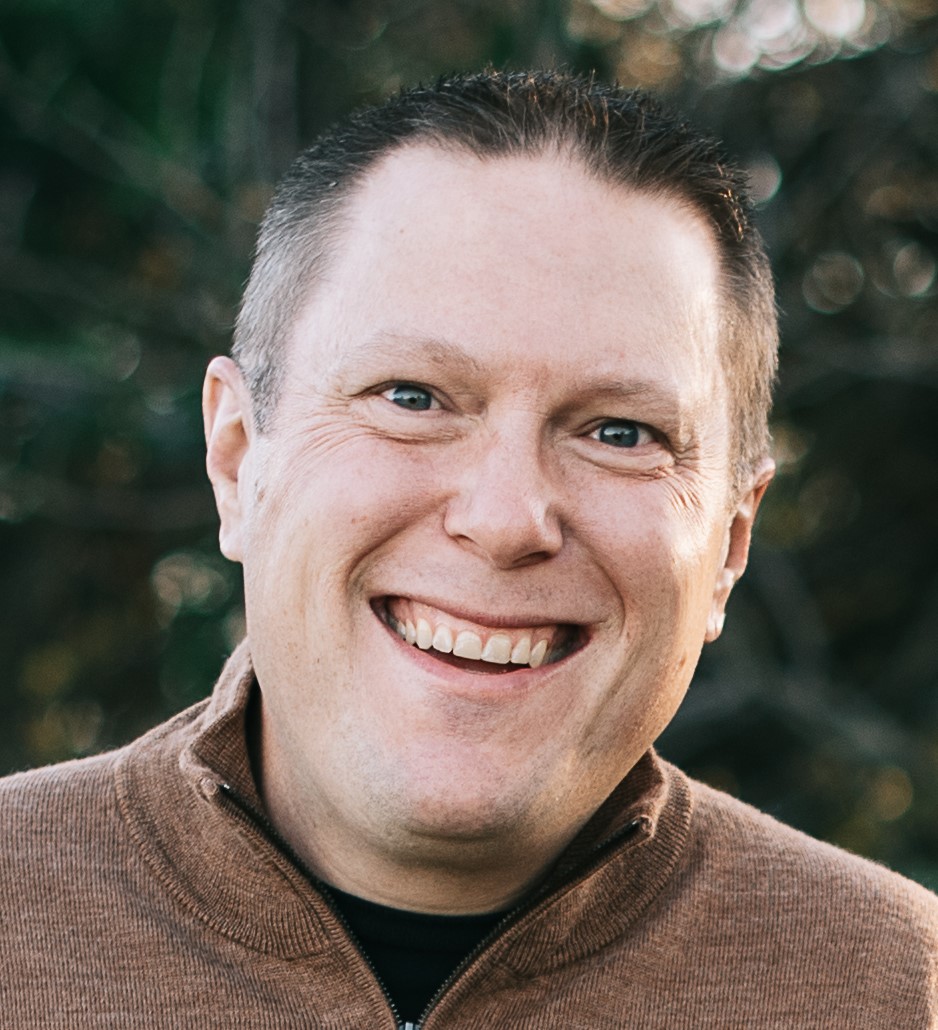
[00:00:00]
On today’s episode, we’re joined by returning guest, Senior Sales Sssociate at KPA, Dale Golgart, to discuss putting down that clipboard and what you gain when you transition from spreadsheets and paper.
Thanks for coming back on the podcast, Dale. We’re so happy to have you.
Oh, you’re welcome, Erin. Great to be with you. Thanks for inviting me back.
[00:00:37]
Let’s dive in. So what are some things people notice when their safety program transitions away from clipboards and spreadsheets?
So I think probably the biggest thing right off the bat is just the amount of time that folks get back in terms of what they can do on a day-to-day basis.
So I can speak to some of my own experience using that. So prior to coming to work with the KPA team a number of years ago, I spent about eight years with an oil and gas company, and for the vast majority of that time I was a safety manager. So I was responsible for being out in the field and leading teams in terms of understanding safe expectations and trying to work towards getting them home safely at the end of the day.
A big part of my role was that I was tasked to go out and conduct field safety observations, inspections, and audits, to document those findings, and to provide reporting to our operations management and our teams in our office so that we could know what our teams were dealing with out in the field.
We were spread out all over the place. We had crews providing services to oil and gas companies, and we might have 10 different crews on 10 different projects spread out all over the place. And there might be four people on a project, or there might be 10 people working on a project with all kinds of equipment and items that I would go out on a regular basis to do field inspections on.
Part of my process at that point, early on anyway, was taking pictures with a digital camera, and jotting down a lot of notes on paper. I would take a notepad with me, and I’m writing out notes of what my findings were of things that I talked to our teams about, or equipment that maybe wasn’t working properly, or that needed to be repaired.
But I’m doing all this manually, so I’m taking photos and jotting down notes on paper while I’m out on location. But then I’d have to go back to my office or come back home, and get my laptop out and spend hours sometimes transcribing that information and putting it all together in a Word document that I could then email out to our operations team. And that was a very time-consuming process because I might spend an hour on location at eight o’clock that morning doing all of these things in person, but then have to come back and spend another hour at my office documenting all this information and then send it out. It might be six o’clock that night before I got that email sent out to folks so they would know exactly what was going on. So it was a very inefficient process that was very time-consuming and also wasn’t very timely.
If I noticed things that needed to be addressed, it might be 8 to 10 hours later before the folks that needed to know about it would have that report in their email. So the beauty came when, as a company, we started to develop a software program to help manage that for us.
One of the safety programs that KPA offers is a platform called KPA EHS, and that software was originally developed in that oil and gas environment. Our vice president of safety had the idea of figuring out a much more efficient and effective way for us to manage and capture the information that we were gathering out in the field. So we were actually the first real customer of this software platform.
So he came to me one day, gave me an iPad, and said, “Hey, I want you to try doing these inspections using this iPad and this mobile app that we’ve developed and see what you think of it.” It was a complete game changer because I could do all of that. I could do that audit and that inspection on that device out in the field, take photos with it, and jot all my notes down on that one device. Then as soon as I left, I could submit that report, and then immediately everyone knew about what was going on. And I was done with that audit, and I could move on to the next one. I didn’t have to come back and spend additional time typing out a report online.
So from that perspective, it just made things so much more efficient. I was able to spend less time in front of my computer and more time out in the field in front of my teams, working with folks one on one, and being able to help with that process. So it was just much more efficient for us to be able to get away from some of that paper documentation to go to this more digital format.
[00:05:08]
That makes so much sense. I do think that you actually touched on a ton of this already, but are there any other comments you want to make about common ways safety teams are using mobile technology?
Yeah, that was probably the biggest game changer for us–the ability to document what we were doing out in the field using a mobile device. So if you can do that and be mobile. . . which, you know, most folks have some kind of a smartphone or mobile device with them most of the time anyway. We were able to go out, capture that information, and put that in the hands of our teams.
Another challenge we faced was just capturing data from the field. As a safety team, we want to know what kinds of things our teams are dealing with on a regular basis. And one of the easiest ways to understand that is for our employees to fill out what we would call our observation cards. So we’re asking them to let us know about any kind of unsafe action or unsafe condition that they’re working in, and also to help recognize other employees for performing things in a safe way.
Again, we were trying to do all that on paper, so we were relying on employees to have those observation cards with them in their vehicle or on their person at all times. Then we relied on them to actually stop and take the time to fill one out, and then they had to remember to get it back to the office and turn it in to somebody. Then that person had to remember to collect all that information, and put it together in some format to email to our corporate office to be looked through and reviewed for trends, data, or information that we’re collecting there. Sometimes that was a very long, tedious process as well.
But once we were able to put that tool in our team’s hands, on their mobile phone–that they have with them all the time anyway–that became much more efficient. So using things like the mobile application for KPA EHS just gives that tool for your teams to engage in your safety program right there on their phone that’s in their pocket all the time.
So, capturing things like observation reports, or field audits and inspections . . . we have a lot of groups that use the software to complete equipment inspections. You can even manage assets and equipment and take and complete training as well. Many of the groups that we work with have employees that are out in the field working on projects on a regular basis and don’t often get a chance to come back to an office or a facility to complete training. So the ability to take training on a mobile device is much more efficient for the employees, and the employees can be engaged and participate in your safety program just by using that mobile device.
[00:07:54]
Can you talk more about how some customers are using mobile devices for training specifically?
Yeah, absolutely. Part of our software gives you the tools and the ability to roll out computer-based training lessons for employees to take, so that you can not only build your own training but can also access a library of prebuilt training content that KPA has created to roll that out for your teams. That can cover a wide range of topics; certainly, there are safety-related topics that OSHA or other federal regulations might require you to take on a regular basis, so those can be built and created in a way for employees to engage in that lesson and take that training right from their mobile device.
It’s also a very interactive platform where there are quizzes and videos, and all kinds of stuff going on to really keep the employees engaged in the training. You know you can roll that kind of stuff out. Companies can create their own in-house training as well, and that’s what a lot of groups do too. They’ll have their own in-house training and development team, and create company-specific training, or maybe it’s something that is specific to a particular operation, or for a particular job task that they have to do on a regular basis. So that training can be created from scratch as well. Again, it gives employees a way to engage in that training right from a mobile device and complete those requirements without always having to come back into the office and spend that time in that area. They can do that when they’re out in the field if they’ve got some downtime or whatever the case is.
[00:09:27]
That’s so great that you can customize it for your specific company.
Yeah, absolutely. You know, some of the training that our team has created within the software, can be customized for your company’s needs. We have a library of just that. It’s fully customizable training of prebuilt lessons that are already created that talk about the topics that need to be done, but then also gives our groups the flexibility to customize those for their specific needs. So if they have certain additional hazards that their teams are facing on a regular basis, based on their job task, they can add in content that’s relevant to that, and make training that’s really for their specific group.
[00:10:06]
Now let’s talk about a specific mobile technology. What is QR scanning and how are people using the technology today?
Yeah, so QR codes you probably see everywhere. There are small, little blocked-out codes that are on packages of products, they’re on websites, and they’re all over the place. The beauty with QR codes is that it’s. . . you know, QR stands for quick response, so the idea there is that someone can use a mobile device, and just scan that QR code, and then that links back to some website. So some groups will use that to link back to a particular part of their KPA EHS software or whatever the case is.
But within our platform, we use QR codes in three different ways. One is every employee profile in our system has an automatic QR code generated. We also use that for our equipment. So if you’re managing assets or equipment in the site, each equipment profile has a unique QR code generated. And then finally, we also use the QR codes within our SDS manager, which allows companies to keep up with and manage safety datasheets that they need to have available for their teams in the field to be able to keep up with those chemicals and materials that they’re involved with.
So the idea with those QR codes is that they can easily be exported out of our software and printed in a way to be attached to something. Whether it’s a QR code for an SDS that gets printed and attached to the container of that material or that chemical, or it’s a code for a piece of equipment that gets printed off on a sticker and attached to that asset somewhere. The idea is that it gives employees quick access to view information about the item that the QR code is attached to. So using our mobile application, they can scan a QR code, and then pull up that profile. Whether it’s an employee and a manager wants to scan a QR code to view that employee’s training history to make sure they’ve completed the training they need to, or make sure they’re qualified to operate a piece of equipment that they’re currently using, or whatever the case is. Or it’s someone that is completing an equipment inspection, and they want to quickly access information and data about that asset that they’re getting ready to do that inspection on.
They can scan that QR code and view that equipment profile. Or with that SDS I mentioned, you can scan that QR code and have quick access to view that full SDS immediately after scanning. That QR code is a really functional piece to be more efficient, to allow users quick access to the information that they’re looking for, and be able to pull that up, right on a mobile device, at any time.
[00:12:47]
Okay, we asked this in our customer community, but I’d like to ask you too, Dale. Do you have any recommendations for our listeners on how to help their company transition away from manual processes and adopt new technology?
Yeah, that’s a good question, and it’s one that I get a lot, because so many groups are doing that right now. They’re seeing the value in moving to a digital platform to help manage their safety program and all the benefits that come with that, but they’re also kind of stuck in this paper, Excel, kind of manual process. The one thing I always talk about is, let’s start small. You know, this could be a very overwhelming process to go from procedures and habits that we’ve developed over a long period of time. To try to take all of that and shove it into a digital platform and start using it all right away can be very overwhelming. So what I always talk about is picking the one or two things that you think you can make the biggest impact on right away, and start with that.
So maybe that is observation reports. Maybe you want to capture information and data from your teams in the field about things that they’re observing and things that they’re dealing with, and that’s a very high priority for you to start to capture some of that. Let’s start with that. Let’s get employees used to filling out those forms, taking that information online, and doing those things through their mobile app. Get them used to that first.
And then start to add in features as we go along. I kind of talk about this crawl-walk-run mentality where let’s not try to run a sprint right outta the gate here. Let’s start small. Let’s go with a couple of things that are priorities for us as a company, get some things rolling there, get some momentum going there. Then as folks start to see how easy it is to use the platform and as a management team sees how that information’s coming in and how we can manage all of that, then maybe we layer in some additional pieces. But when we start to want to go right outta the gate full bore and go with everything immediately, that’s gonna be very overwhelming. So we’ve seen a lot of success with groups just starting small and starting with those things that are priorities for them.
[00:14:56]
That’s great advice. All right, well, thank you so much, Dale, for joining us today. We really appreciate getting to benefit from your expertise.
Absolutely. Well, thank you, Erin. I appreciate it. It was a great chat and I look forward to doing it again.