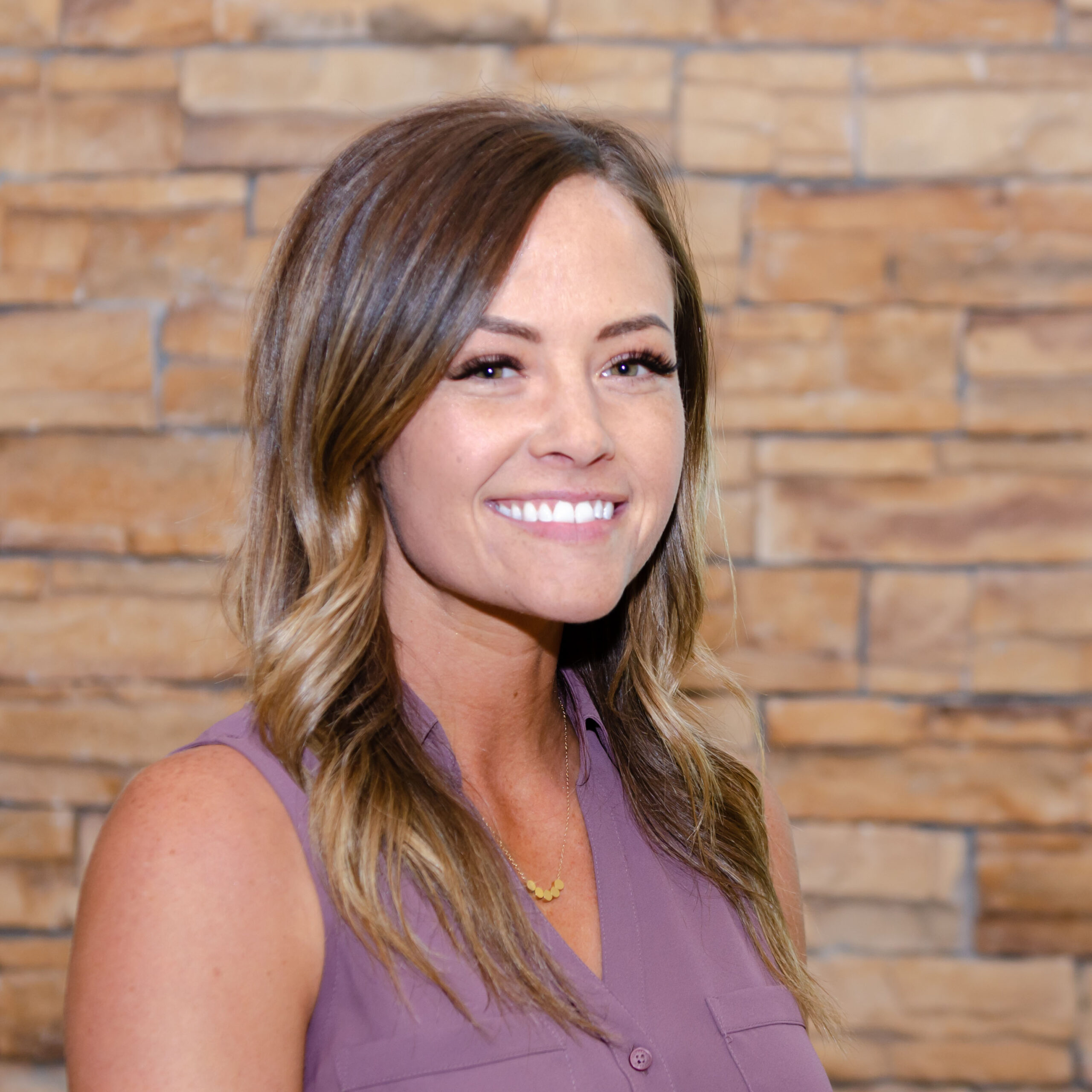
[00:00:29]
This week, I’m excited to welcome back to the podcast Jade Brainer KPI’s, Director of Product, Jade. So I haven’t mentioned this to you before, but our last conversation about data and analytics has been our most listened-to episode.
Oh yeah?
I’m glad that we can get together again to talk numbers. Thanks for joining us.
Of course. Glad to be here.
[00:00:52]
I asked Jade to join us today to discuss the results of this year’s EHS state of the market survey, where we surveyed safety leaders on the trends that they’re seeing in EHS programs. So I’m excited to get your take on the results.
So we started off the survey by asking people where within their EHS programs were the key areas they were gonna focus on in the next 12 months. What did you find interesting about how people answered?
Yeah, so honestly, not a lot of surprises. I guess the top results demonstrated that organizations over the next year, um, the key areas that they’re gonna focus on – and this is across all industries and company sizes – are reducing incidents, implementing effective training, regulatory compliance, and increasing participation in the program. So not a lot of surprises there, especially since reducing incidents is at the top of the list of 58% who reported that their organization is gonna give extreme focus to that initiative in the next 12 months.
So I think every year we do this, reducing incidence is at the top of the list. But what was a little more surprising was to see effective training and increasing participation of some of the other options that didn’t make it into this kind of top four, like enhancing reporting and analytics and automating processes.
So, to me, that suggests that in general, things are shifting to a more proactive approach to incident management. So having effective training or lack of participation in the safety program, reporting workplace hazards, and reporting near misses, those are leading indicators of safety program performance.
While focusing on incidents is always important, the methods that we go about reducing those incidents can make or break a company’s success.
[00:02:59]
Yeah, I thought it was really interesting to see how part of, uh, it was an even split between people-focused and process-focused results as far as their priorities. So it’s nice to see that it’s not tilted completely one way or the other.
Yeah, absolutely.
[00:03:16]
Next, we ask safety leaders what challenges they were facing in meeting their EHS focused goals. Did you see any surprises?
Yeah, so I think the responses were 63% reported that employee engagement and culture is the biggest challenge to meeting EHS focus initiatives.
Um, and then second to that, the workforce shortage pulls in at 49% with the, you know, third runner up is, uh, leadership commitment at 40%. So leaving the lowest challenges, which was a surprise. The lowest challenges being lack of budget and lack of tools or resources. So to me, these responses are indicative honestly of what we have going on in our world today with our labor shortage issues coming out of the pandemic.
And most of these industries are struggling to overcome that – oil and gas, manufacturers, construction – many are finding themselves in situations where they’re required to do more with less simply because finding and retaining talent is much more difficult in today’s climate than maybe in years past.
So when you combine, you know, a forced lean operation, with an increased regulatory environment, sometimes that can negatively impact the safety program performance. So participating in safety activities such as, you know, taking training or reporting workplace hazards, or, you know, performing audits and inspections.
Those things are seen as not contributing towards production, not contributing towards the widget that they’re selling, you know, and, and, and what, what their day to day job is. And so therefore it becomes a lower priority, something that gets deprioritized, especially if leadership is not on board.
Enforcing participation – that can become a problem. But in a time like this, it’s crucially important to ensure that you have the right tools and resources in place so that safety doesn’t become a burden. Have tools that are, that are easy, that are quick, that are practical for the environment the workers are in.
So, you know, if I’m, I’m out on the, on a job site, you know, not having to go to a laptop or pull out a piece of paper, have something that is, that is quick and easy and practical for my day-to-day process that is crucial to increase the likelihood of getting employee engagement and adoption and leadership involvement in the overall safety program.
So not a lot of surprises there. And I think it, it kind of mirrors what, what we’re seeing today with, with the labor shortages.
[00:06:04]
How do you crack the code of increasing participation, which is what people are focusing on with not enough people to actually get everybody’s work done? That’s, if they can figure that out, they’re golden.
So I thought it was interesting how people answered the question about mobile access. What does that tell you about the future of incorporating technology into safety programs?
Well, the trend is obviously growing, so mobile access and safety and training information. We asked that same question last year, and the rates have increased from 38% in 2021 to 46% in 2022 of organizations that allow their team members to access safety training and, and other resources and tools from a mobile device. So again, going back to our last question, it is crucial if you’re gonna focus on employee engagement and participation, that you have the right tools available to the people that are, that are practical for their day to day life and, um, that you know, their regular job.
So the more participation you have, the more people that you have reporting information of what’s actually going on in the workplace. The more data you have, the more accurately you can evaluate and even predict the effectiveness of your safety program and pinpoint areas of concern.
[00:07:35]
So the question that we asked about confidence in safety leaders’ EHS programs, that one always brings up some interesting insights. What stands out to you from these responses?
So it was good to see that in most organizations, the report showed two-thirds of the respondents, 67%, you know, across all industries and company sizes.
They indicate that their EHS program is strong, and that’s whether they’re using EHS software to manage that program today or not. But what stood out most to me are the other areas. So based on the data reported, I could actually state that those that don’t use EHS software are less confident that, number one, they cover all areas of risk within their business and compliance issues.
And they’ve stated that they cannot accurately anticipate scale or plan for critical issues. And you know, the flip side of that, the EHS software user respondents more often than not, describe that they, they can do those things, so they, they, they feel more confident that they have uncovered or that they’re aware of all areas of risk and compliance issues, and they have tools in place to, anticipate and, and sort of predict critical issues before they occur.
So what that tells me, in summary, is that a safety program without software, which is a manual process. You’re using Excel spreadsheets; you’re using hard copy documents. Clipboard style is a reactive program, so there’s less certainty about what the overall risks and issues are, and those that do come up are handled after the fact.
So it’s, it’s a reactive program kind of the whack-a-mole approach to, to safety, if you will. I mean, maybe we’re responsive, we’re, we’re on top of things, but we only focus on what actually occurs rather than those preventative measures being taken.
[00:09:43]
I like that. The whack-a-mole approach to safety. We’re gonna use that at some point.
Following up on that last question, and this is my last question for you, Jade. What can safety leaders do to increase confidence in their program? Get away from whacking those moles.
Have good data. Data speaks for itself. It allows organizations to establish baselines, and benchmarks, set goals, and just keep moving forward.
And the more complete your data is, the more accurately you’re gonna be able to depict the state of the safety program and focus your safety efforts more effectively. But having good data largely depends on where you’re getting that data from. So where are those inputs coming from? And if you aren’t capturing enough data and only evaluating a portion of it, for instance, if you’re just looking at OSHA recordable incidents, then you’re not looking at the complete picture.
So for those organizations that want to increase their confidence and, and go to their leadership teams and have a, a report of here’s how we’re doing from a safety perspective. Here’s where we need to go and here’s how we need to get there. I would encourage them to focus on their input processes.
Ask themselves the questions, you know, how, how are we capturing things like incidents, near misses, safety observations, et cetera? And is that process working? Are we getting enough data and what do we need to change to get a more complete view? So if you can incorporate processes like we talked about, things that are practical, that work for your business. There’s no one size fits all.
Every organization is a little bit different. So evaluate what process works for you, for your business to get good data in. And the more good data you have, the clearer, more accurate view you’ll have of your safety program and be able to identify, you know, here’s how we’re performing today. Here are some areas that we need to focus on.
So you can improve that safety program and, and have confidence that you’re doing the right things and you have awareness and communication of where you need to be.
[00:12:10]
Always brilliant, Jade. Thank you so much, Jade. I always appreciate you talking numbers with us and it’s always great to get your insight.
Thank you, Toby. Great report.