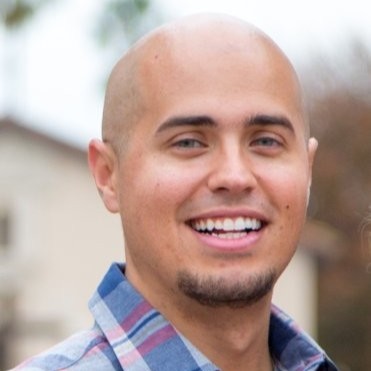
[00:00:33]
Great. Well, let’s jump in. In the fast-paced world of construction, we both know that safety is paramount. How have you seen the landscape of construction safety evolve over the years and what role does technology, especially safety software play in this evolution?
I think technology has played an extremely large role in the evolution of construction safety. What might be the best place for us to start to break this down this evolution and we look at it in a few different phases. So we’ll start with kind of what I’ve called, and this is Taylor’s version of this and this is my take on it, but we’ll start with this phase zero. This is the traditional pen and paper contractors operating in this realm. They’re printing PDFs to be filled out at the job site. They have physical job site binders that have hundreds and hundreds of pages of printed material. Back in the office, they might have file folders with printed OSHA 10 cards, OSHA 30 cards, and so it’s very, very heavy. It’s pen and paper focused. It’s forms in the field on those pens and paper and it’s slow. And so this is kind of the phase zero, very traditional approach to it. Less and less, to be 100% honest, contractors operating in this phase, but they still exist.
And then on the other end of the spectrum, we’ll call it phase two, and yes, I know I skipped phase one. I’m going to come back to that after phase two. But phase two is the opposite end. And this is your full-blown digital safety program operating 100% digitally. We’re using software to leverage the program. We have our field using mobile devices to access that software. They’re completing forms in the field. They’re doing all of their safety processes, so their toolbox talks or JHAs or pre-test plans, their inspections, maybe even things like a hot work permit or a confined space permit. The field, your foreman, your superintendent, we often call these field leads, they’re doing all of that through a mobile app.
And when they’re completing these processes, it’s syncing up to the cloud, it hits a database, and then typically the safety team, who is usually in the office, is seeing all of this data come in. And so this is the phase two. This is full-blown digital safety management, kind of the world that KPA Flex lives in and plays in. There are contractors that certainly do this and do this very well. Usually, it’s your more sophisticated contractors, but there are a lot of smaller shops that realize this is where the world’s going. And so they’re jumping in on this.
And then there’s that phase in the middle, the phase ones, and this is where I see a majority of contractors today, is kind of this hybrid approach. Some of the processes are still pen and paper, maybe we’re tracking our training on an Excel spreadsheet. Not pen and paper, but not fully connected digital where we have our employees down the left column, we have columns across the top of all the different certs and we’re plugging in dates of when things expire. It’s closer to digital, but it’s still not kind of a fully connected solution. People can’t have access to that in the field usually. Oftentimes it’s not updated in real time.
And so this phase one might have a few digital things here and there. Maybe they’re using an inspecting tool just for inspections, but they go out there and they do their job site inspection on this inspecting tool. But then other processes, like their pretest plan, are still done on paper. And so this hybrid approach, I think is where a lot of contractors are operating right now. So not fully digital, but kind of one foot in the water as they say, and they’re primed to make that jump into that phase two.
Another item worth noting on this evolution is that technology itself has become normalized, to be honest on the job site. Yes, of course, there’s your safety software, but before some of this safety software existed, some of the first technology and construction out at the job site was really around the idea of managing plans and specs and doing markups and annotations more on the project management side of things. But that was widely adopted and that led to timekeeping being digital out at the job site and then estimating and then of course safety. And so this idea of not having a digital safety program has almost become a hindrance for some contractors to get work.
Those who have a digital safety program almost use it like a resume builder. And when they’re out there pitching themselves and bidding on a job and trying to impress the hiring contractor, the general contractor, subcontractor A, all pen and paper, subcontractor B, digital safety software to manage or safety program, that general contractor’s going to look at those two and make a decision most likely based on these performance metrics. And safety is a big one. Having a digital safety program likely will help subcontractor B get that job. And so technology has gotten to this point where it’s helping companies win business by having this technology in place.
[00:05:28]
It sounds like tech has really revolutionized many facets of the construction industry, and I’m sure that you know that having easy access to data is crucial for an effective safety management program. Can you share some insights into why having readily available safety data is so important, and particularly in the construction sector, how it contributes to a safer working environment?
Sure, absolutely. Time and time again, I’m often asked what’s the number one reason a contractor should start using a safety management platform to manage their safety program? And to be honest, my answer is usually the same. It’s this idea of this black hole effect, right? A black hole effect takes place when a contractor has so many things going on in terms of safety that they can’t find anything and they don’t know where anything is. And it’s all just kind of going into this black hole.
And so, say, in your 20-person electrical shop, you might have five foremen, and those five foremen might need to do three tasks weekly. They need to do a toolbox talk, they need to do a weekly job site inspection, and they need to do a weekly vehicle inspection. So three processes, five foremen, okay, 15 records. That’s easy enough to track down. If I’m the, well, a 20-man shop probably doesn’t have a safety manager, so they might have a PM who’s managing safety, maybe the owner or the CEO is overseeing safety. But you get my point, there are 15 things that need to be tracked down, that is doable in theory.
But the second that five foremen goes up to 24 foremen, 50 foremen, 100 foremen, we are talking hundreds or thousands of records a week that need to be documented that are maybe getting documented, but I actually have no visibility to it. So it’s out of sight, out of mind. As a safety professional, and I’m not doing this maliciously, this is just kind of the nature of the beast as they say where things are getting submitted, but I have no idea where that is. Is it in Taylor’s truck at the job site? Is it at Jim’s house because he left it there? Where is all this stuff that we say we’re doing as a safety program? Where is it and where does it live and how do I have access to it?
And so this kind of black hole, out of sight, out of mind is a real problem for a lot of contractors. We’ve seen a couple of times where we had a large electrical shop, like 400, or 500 foremen that were supposed to be doing weekly tailgate meetings and weekly pre-task plans. We’re talking 1,000 records a week. It is nearly impossible to manage that on pen and paper, even with a staff of 10 safety professionals trying to manually track down who has done what, gather things back via email, scan, and deliver to the office, it’s nearly impossible to manage that at that level.
And so that’s where we see the need for a system to manage and store this critical safety data is huge. And so I think that’s really what is pushing a lot of contractors to go this way is that they’re being asked to do so many different things as it pertains to safety. Maybe it’s being asked by the GC, maybe OSHA’s requiring it, but whatever the case might be, there’s so much going on there that they need a system of record to maintain all of this data so that when the time comes, they can produce it and access it when they need it.
[00:08:46]
Talking about the phase one companies being the majority of what you’re seeing out there, this could be a really painful process for a lot of these companies where they’re using that pen and paper or have some digital, some pen and paper. It’s got to be tough. And I know that you know that transitioning into safety software can really be a game changer for these companies. What challenges do construction professionals face when they’re adopting new technologies and how can organizations overcome these hurdles to ensure that they have a seamless integration of safety software into their workflows?
One of the biggest hurdles in my opinion is getting that field-level buy-in. Oftentimes, not all the time, but oftentimes the field workers, the contractor, are very, very powerful in terms of the decision-making process. They are the ones essentially doing the work that runs the business and a lot of them know that. And so anytime we get some objection out in the field, the key is going to be to show how this safety software that we are transitioning to, that we are planning on implementing, is going to benefit them. And a key one is to focus on speed and efficiency. The field staff are tremendously overburdened with deadlines and timelines, and they have a job to run.
Yes, safety is an important part of that job, but they’re day-to-day, they’re not trained safety professionals per se. They are electricians, they are plumbers, whatever the case might be. And that’s what they want to do and they know they need to do, at a very high level. And, yes, they need to do these safety processes, but if I could be presented with a tool that allows me to do safety, not only better but faster, saving a few minutes a day, albeit it might seem small to a lot of people, is big for these guys in the field. And it allows them to focus on what they do best and what their day-to-day job really is. And so the idea of efficiency and speed as the value proposition of deploying safety software could be a good way to increase that field buy-in.
I think something else to look at in terms of the transition to a safety program could be this idea of integration and automation. Can we connect our safety software to our ERP or can we connect our safety software to our HR software and pull and push data back and forth so that these multiple tools don’t need to be double admined? We’re reducing rework, we’re saving time, we’re increasing efficiency. That’s the name of the game here. And integration and automation is a great way to do that. A classic example is single sign-on. A lot of companies are using SSO now for their email and the different kinds of business platforms that they use. Could the safety software that we’re deploying also leverage that same SSO so that our field staff don’t need to worry about one more password and it feels seamless and it’s more effective? And typically that will lead to greater buy-in.
I think one last point on this idea of overcoming some obstacles in terms of deploying safety software, this is becoming less and less, but we still hear it every once in a while, considering hardware and the devices in the field. That is going to be a big piece, if not the most important piece to a contractor who’s deploying a digital safety program, we need tech in the field so that our field staff can perform these functions through this new software. And so make sure that’s in place so that doesn’t become an obstacle. I do think that piece, especially in this day and age with how much tech is out in the job site is becoming less and less, but we still hear that objection every once in a while as, “Oh, I need to figure out how to get 50 tablets.” So put a plan in place to get those devices in place prior to deploying said software.
[00:12:33]
I think those were some really great insights on understanding the return on investment of this software in more tangible ways because I think that that’s important for the safety managers to hear and of course all the people that are out in the field to kind of understand what it’s going to mean for their day. And it’s really essential to making a big move like this. And with construction sites being such dynamic environments, communication is key. How can this safety software enhance communication among these construction professionals, ensuring that everyone stays informed and engaged in maintaining a safe workplace?
This is really what these safety platforms at their core are supposed to do and they were designed to do. And so this idea of instant access to critical safety data is important to every safety program, and it’s certainly an important part of a digital safety program. The grand idea is that all field personnel are aligned with safety staff and back office staff. To make that happen, you have to have a safety platform in place that allows those two organizations, the back office and the field staff to be connected. And ultimately that will help with better communication, better education of the workforce, and ultimately mitigating a lot of risk.
And so the construction environment is ever-changing and field staff are always needing up-to-date information. I’m the foreman, I’m going from Project A to Project B. Project A, might’ve had a specific site safety plan, but Project B has a different site safety plan and that is provisioned through the safety software and I know where to go to get it. I click on a few buttons and boom, there it is. I have what I need. Instant access to the data at the tip of my fingers is the name of the game. And so safety software provide that instant access to that critical data that the field staff needs to not only do their jobs well but to keep themselves plus their crew, the labor that they oversee, to keep all of those entities safe.
And so leveraging safety software becomes important for that. And I think a classic example is this idea of a JHA or pre-task plan. Yes, you could do that on paper, but something that safety software might do that you can’t do physically on paper in terms of this JHA and pre-task plan is this idea of a procedure set library. I’ve talked to a lot of contractors about this idea, so I’ll paint the picture here. I’m the foreman in the field. I am leading today’s pre-task plan. We’re going to talk about the three tasks that we’re performing today. What are the hazards associated with that task and how do I control said hazards? Well, if you’re doing it on paper, typically what will happen is task one, installing conduit, the potential hazard, pinch points, how to mitigate, wear gloves. And so the foreman’s filling that out, talking to the team about it, but filling it out on paper what he or she knows about the task and what he or she knows about what are the potential hazards and controls.
What a safety software could do that couldn’t be done in that paper version that I just explained, we could set up a procedure set library. The safety team goes through and says, these are the 100 common tasks that we’re going to do as an electrical outfit, for example. And if it’s installing conduit, it’s running cord in the wall, whatever it is, they detail these 100 tasks and then they’re going to go through and detail out all of the hazards associated with those tasks and how do we mitigate or control those hazards. So now we’ve created this library of data, it’s all within the platform. And so now the foreman, this is the new version now, we’re using the safety software, opens up the app, opens up that pre-task plan and starts picking from the common tasks. Once they pick the three common tasks, the hazards and controls that were pre-populated by the safety team are displayed on the screen there. And now the foreman’s no longer guessing what the hazards and control might be. They’re seeing what the safety team says these hazards and controls are.
And so then the foreman reads that information with the team. Everyone is on board with the communication of the plan. Everyone is educated and we’ve documented this process. And so that’s two, the same process, pen and paper. Without that digital with that procedure set library, it’s very different in terms of the content and the education being delivered to the team. And so I think that’s where you can see how communication becomes key in these things and how safety software really allows these contractors to do this at a different level.
[00:17:04]
And I think that’s truly the best outcome that you can hope for is that they’ll be able to operate at this higher level and keep their staff and people safe.
And I think while you’ve done a great job of explaining this so far, for those construction professionals listening who are still hesitant to embrace safety software, what success stories or tangible benefits have you witnessed that can demonstrate the positive impact of implementing these tools on both safety culture and the overall efficiency of these construction projects?
Absolutely. I’ll give two examples here. The first one will be shorter than the second one, but the first one we saw a few months back, an electrical contractor out here in Southern California needed to put a couple of people down into a trench. That’s typically a very high-risk area anytime someone’s going into a trenching situation. And so certain people need to be trained before they go into the trench and the foreman is looking to send two people down and has 10 people as part of the crew. Well, three of the 10 are saying they’re trained. So then I have those three, and I’m hoping that all three of them are actually trained. That’s the situation without safety software.
The situation that actually occurred was the foreman before he sent anyone into that trench, looked up all three of those people through his app on his device and instantly verified that only two of the three had up-to-date trenching and excavation training. And the third one was expired. Had that situation not played out the way it did with instant access to that certification and training data for those three people, there’s a chance that the foreman sends that third into the trench that had expired training on trenching. And so those kinds of situations where you don’t have that instant access to data or you have old data that hasn’t been updated because you’re not using a safety software, those instances are avoided and potential risk, like very, very serious risk is mitigated. And so that’s one example.
And then the second success story we actually just heard a couple of weeks ago, and we got involved because we wanted to help out this contractor with the situation. But essentially what happened was OSHA gave this electrical contractor a heads-up, “Hey, we’re coming to this job site next week. You have five days, we’ll be on site. Please have the following information.” And they needed six months’ worth of job hazard analysis, six months’ worth of tailgate meetings, and six months’ worth of job site inspections. “Make sure you have that all ready for us.” I mean six months of data on this job, and it was a big job, they had a couple of foremen out there, ended up being almost 1,000 records, individual records of those three different processes that I mentioned, that OSHA was essentially giving five days’ notice that we want proof of all of those and have it ready for us when we get to the job site.
And this contractor, it’s amazing to actually see it play out, in a matter of a few hours, this contractor pulls all of these reports focused on the job site, sets a date range report over the last six months, then focuses on each specific form. Here are our tailgate meetings. Okay, there’s 300 of them. Here are our JHAs. Okay, there are 600 of those. Here are our inspections. Okay, there’s 200 of those. And they extracted all of that data. They had it both digitally. They went as far as exporting it into a giant PDF and OSHA showed up and they were, to say the least, impressed. And it all went over very smoothly. And it not only presents well, but it says to OSHA, we are serious about this and we have a system in place to make sure not only that we’re keeping all these records because clearly, they did that very well, but that also shows that we are doing this and we’re doing this very actively in an attempt to keep our workforce safe.
[00:20:48]
I think the fact that OSHA was impressed at the level of record keeping says a lot about those companies you mentioned in the first question about phase one, that they are encountering so many of these companies that can’t pull this data together or don’t have it in a format that’s going to be easily accessible and easy for OSHA to parse through. So I think that in itself says a lot about what a safety software can do for a construction company. Those were some incredible stories. Before we close out, do you have anything else you’d like to share with the listeners?
Sure. A lot of people ask, “Why should we do this? Why should we go down this path of deploying safety software?” Yes, of course, you’re going to save time. You’re going to save money. So that’s the business side of it, but you’re also going to have great recordkeeping. I just told the story about a prime example of that. And so your OSHA compliance from a recordkeeping standpoint will certainly be bolstered. But the third, and this might sound a little cliche, but this is why at least I do what I do and what a lot of people here at KPA, why we do what we do, and certainly why safety professionals and contractors do what they do is to ensure that employees go home to their loved ones at the end of each and every day. And having safety software that allows you to manage safety better and do safety better will ultimately lead to that.
[00:22:08]
Fantastic. Taylor, this has been a great conversation about the ways that safety software can revolutionize what people are doing at the job sites when it comes to construction. Great examples of how you can be ready for those OSHA visits and what it’s going to mean for those people in the field when they’re saving that time in their day, and they don’t have to guess when it comes to the safety of their crew. Thank you so much for being with us. This has been incredibly insightful. We were so happy to have you.
Thanks for having me.