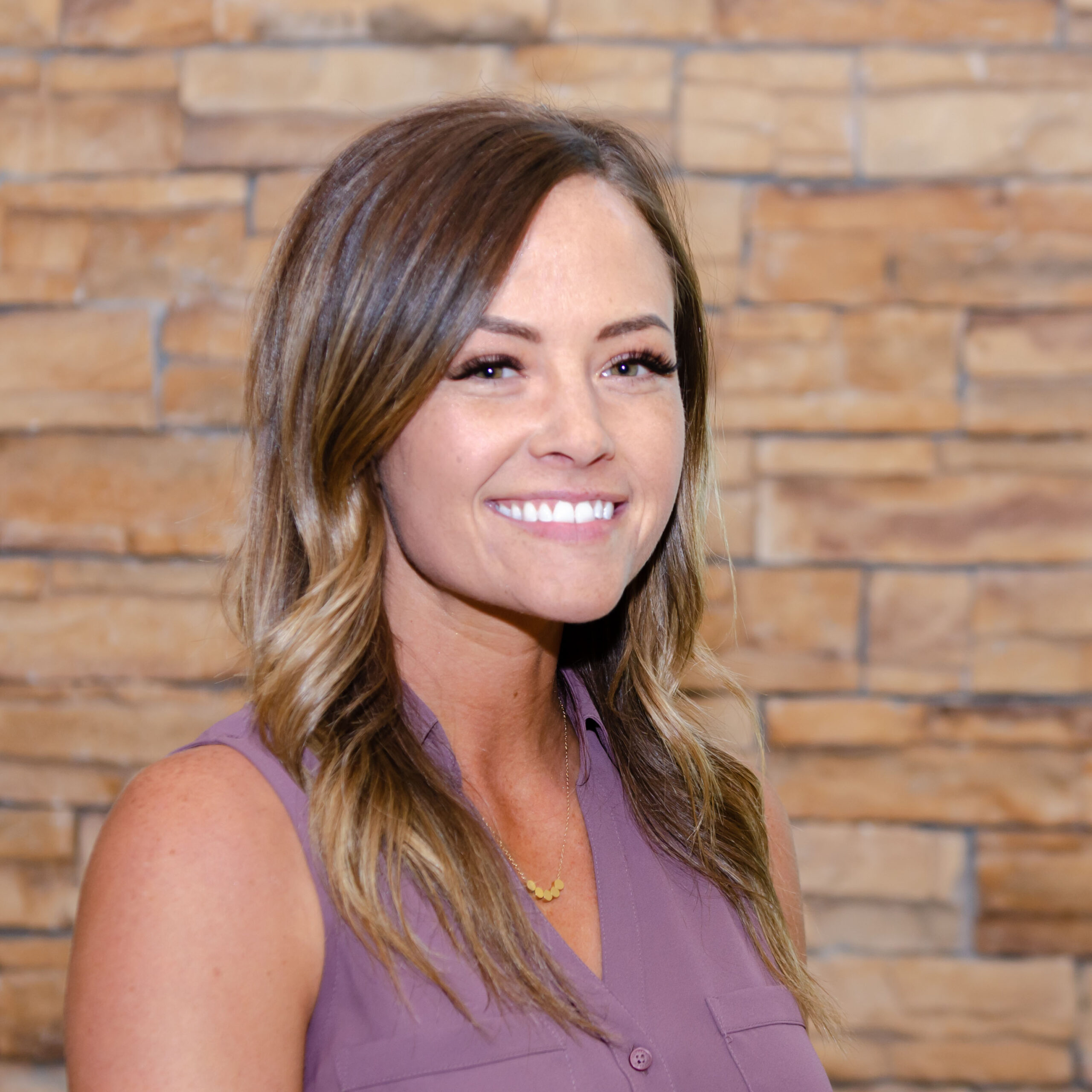
[00:00:32]
Okay, so let’s start with the basics. Will you explain for our listeners what we mean when we say data and analytics tools?
Jade:
In general, when we think of data and analytics, we’re referring to a process of analysis. One that’s going to uncover some insights and trends in order to help a business draw some conclusions and enable better decision-making.
So when we think about data and analytic tools as it relates to EHS, these can be some really powerful resources that can help businesses learn more about their company safety and environmental performance, and then use that information to make necessary improvements. But it all is going to start with the, you know, the data that you’re putting in.
So data inputs, such as incidents that occur within an organization, inspection, findings, observations, et cetera. And then you can start to look at trends and patterns that are going to uncover areas of opportunity that help an organization mitigate risk.
[00:01:38]
So it sounds like before you can get to the analytics side of things, step zero in the process is making sure that you are inputting the correct data when it needs to be input, kind of that garbage in garbage out philosophy of making sure you have all the right stuff in your system ahead of time, so that when you process the analytics, they’re telling you the truth of your situation, does that sound right?
Jade:
Exactly. You gotta walk before you run. So, start with good data. So you get good data out.
[00:02:06]
So how did data and analytics tools play a role in the overall management of workplace safety procedures? What do the safety managers stand to gain by using these tools on a regular basis?
Jade:
So, this is going to help uncover trends, but data analytic tools really help businesses go beyond what I would consider just basic compliance, you know, checking a box to say, you know, we’ve done our inspections, we’ve recorded our incidents.
You know, what, what are those basic things? And instead implement an effective program where performance is constantly measured. So a basic compliance program is often referred to just kind of in the EHS industry as being a reactive program, because it involves just a direct response to something only after that event has taken place.
Data and analytic tools are going to allow organizations to not only migrate from what we call historically reactive to a proactive safety program, which proactive could mean, for example, instead of the checking the box and saying we’ve done the inspection. Throughout the process, we’re identifying areas of risk through observation reporting or implementing processes and procedures that, again, mitigate that risk. But data analytic tools help us go one step further from proactive to what is often referred to in the industry as predictive.
And a predictive EHS program recognizes trends through behavior, using key data points that we call leading indicators. And these leading indicators help us pinpoint areas of concern in order to guide those that are responsible to where they should be focusing their safety efforts.
[00:03:54]
What’s the other side of the coin, the lagging indicators. We’ve got the predictive side, then how are we also using data to look back and evaluate the past?
Jade:
So, we talked a little bit about leading indicators and those leading indicators are really your crystal balls.
So we can have a forward-looking view at the road ahead. So if you think about safety, as you know, you’re being in a- we’re in a car, are we looking in the rearview mirror or are we looking in through the windshield and your, your leading indicators are your windshield. Your lagging indicators are where you’ve been, and these are important measurements as well.
So it’s really important for an organization to measure EHS performance through these lagging indicators because it is the undeniable truth. However, unlike our leading indicators, there’s nothing we can do to change these outcomes. You know, it’s what’s already happened. And so lagging indicators are just by definition, they’re final when you’re reviewing them. So, what can we do with this data? Lagging indicators are often the key measurement is just measured by the incidents that are occurring. So it could be workplace injury and illnesses. It could be property or asset damage. It could be environmental exposures, spills, things like that. And while we can’t prevent the incident that’s already occurred we can learn a lot from this information. We can investigate these events. We can do root cause analysis. We can identify corrective and preventative actions that allow us to make changes in the organization now so that we can mitigate this risk in the future.
So thinking about kind of jumping back to the leading indicator side of things, if for lagging indicators, a key metric is something like a root cause analysis. What are the key predictive indicators that we’re looking at for the future?
Jade:
So, some good examples of some key predictive indicators would be measuring data such as safety observations.
So you know, nothing’s occurred necessarily, but we’ve identified, you know, there’s a wet floor in a high traffic walkway and you observe somebody kind of walking around it. But that’s- we’re observing something, a hazard in the workplace that could potentially lead to a particular incident.
And we’re capturing that data- a safety professional that is looking across the business, multiple business units, departments, locations, they’re able to more easily identify, okay, where are we having a frequency of these safety observations that are being reported? Where are we having higher severity? So then we can focus our safety efforts and pinpoint problem areas before something occurs.
Safety observations are one example of that, reporting near misses, is an example of a leading indicator, training compliance reports, all of these are good examples of leading indicators that provide key insights to exposure.
[00:07:07]
So then taking those analytic tools and looking at the past, looking at the future, how does this play into the process of OSHA reporting?
Jade:
One of the key data points used to capture, evaluate our lagging indicators are the incidents or the events that happen within your organization. Now, not every one of these incidents is going to be classified as an OSHA recordable incident. Those are just going to be our injuries and illnesses and those have a certain severity. But if you’re already using data and analytic tools to capture this information upfront, it’s gonna make it so much easier for you to complete that regulatory compliance report, like an OSHA300 and an OSHA301, because the information is readily available. So, you know, at the end of the year, you’re not scrambling to pull together this information and pull different spreadsheets in or, or capture the- you know, go back in time and try to remember what has occurred in order to get those reports completed.
Everything is already available to you. You can either generate the report automatically, as a lot of tools have an integrated solution to build your OSHA logs or export the data and load it to the OSHA federal website.
[00:08:28]
It sounds like it takes a lot of the stress out of the reporting season because you already know the information is in there. It’s easy to access, easy to report.
Jade: Absolutely.
[00:08:37]
So in what ways can a safety manager use data and analytic tools to improve their training programs?
Jade:
Training completion and participation can be a really excellent metric to track as a leading indicator. As we kind of mentioned before, we know in the safety industry that an employee that’s properly trained is happier, healthier, and presents a lower risk to themselves and others.
So data and analytics can, can help a safety professional identify areas of concern in the instances where training. Overdue. So overdue training is an indicator that training has not been done. Those refreshers are really important to keep those key safety concerns front of mind, and how to properly address them or measure where comprehension is low.
Maybe we’re looking at training scores and we can pinpoint a particular training topic, or maybe an area of our business, the scoring a little bit lower on a particular topic that would allow a safety manager to focus on specific program improvements. So it could be that we, you know, need to reboot our training resources for this particular topic.
It’s an important topic like lockout/tagout, and maybe we need to make it more relevant to our business and our equipment, and our processes. Or just, you know, something else that we need to look at. But it gives those key insights to making sure that your workforce is properly trained. They’re comprehending the information that’s being presented to them. And in turn they’re a lower risk for the business.
[00:10:18]
And what I’m hearing here is that it can really help with prioritization, right? Like it’s one thing to say, I’m going to improve my safety training program this year. And it’s another to know exactly where those improvements need to be made, where those pain points can be pointed out.
Jade: Exactly.
So if safety leaders walk away from this conversation, remembering just one thing, what would you want it to be?
Jade:
That’s a great question. I think I’ve used a lot of the same terminology throughout the questions here, but I would just want to remind safety leaders that safety traditionally has looked at just one metric and that one metric has been injuries.
And we’ve used that one metric to answer the question, “is it safe?” Is our business safe for our employees? Our entire goal is to send our workforce home in the same, or even better state than they arrived at work that day. So unfortunately, this metric is a one dimensional measurement.
If no workers are getting hurt. Does it simply imply that everything is safe, that our businesses are safe, that we don’t have hazards in the workplace that we’re not aware of? Perhaps yes and perhaps no. But when we start to analyze our organization below the surface, by looking at those, again, buzzword, leading indicators, we can truly understand where our employees are. And beyond our employees, our consumers and our community are exposed and become more predictive in our activities. We become more intentional with our processes to actually reduce and even eliminate risk wherever possible.
Sounds like a win-win scenario for everyone involved.
Jade: Absolutely.
Well, thank you so much, Jade. I really appreciate you talking to us today about this. I know that I’m not the only one who has learned a lot from this conversation.
Jade: Perfect. Well, thank you.