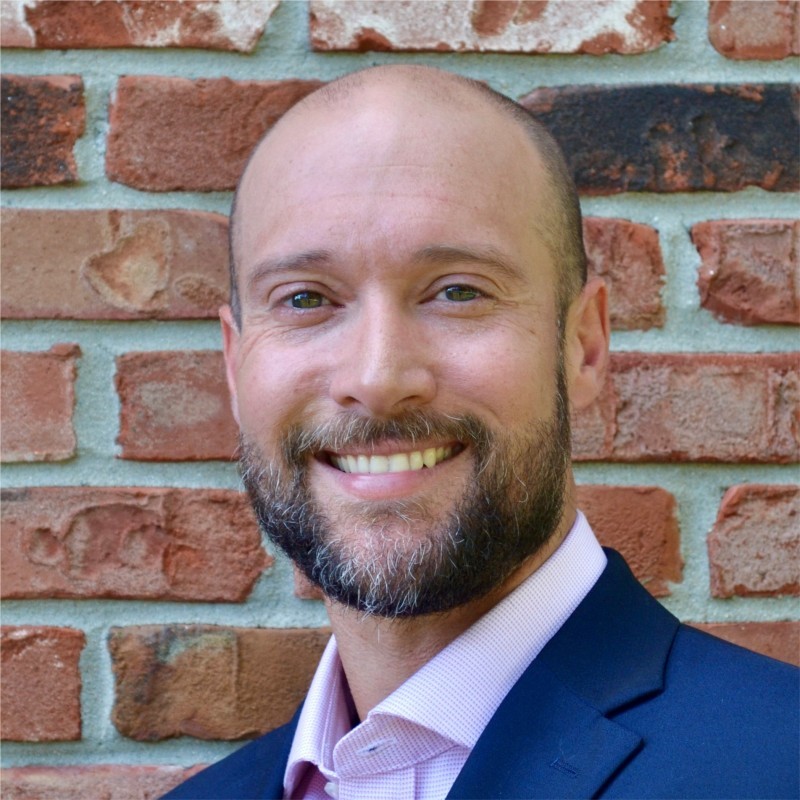
[00:00:17]
Today we’ve brought back KPA’s EHS Regulatory Compliance Manager, Zach Pacillo, for a two-part midyear update on the latest from OSHA and the EPA. In this first installment. We’re covering the most recent updates on rules and regulations from OSHA, and next week we’ll be back with updates from the EPA.
Zach, it’s really great to have you back with us on the show. Thanks for being here.
Thank you for having me. Lots to talk about today.
[00:00:48]
Okay, then, let’s dive in. When you joined us in January, we talked about likely areas of focus for OSHA in 2023, including the final rule on the HazCom Standard and other rules and regulations undergoing updates. Have things played out as you expected?
Well, it’s been slow-moving on the safety front. Lots of movement on the environmental front, but we’re gonna start off with the safety front and the Occupational Safety and Health Administration (OSHA). So the government just released its Spring 2023 agenda, which is basically going over all the different stages of where these regulations are at and their rulings.
You have the pre-role phase, you have the proposed rule phase, and they have the final rule phase. And the final rule phase means that, hey, it’s final. We’re gonna put this in the code of federal regulations. We’re done with accepting comments. We’ve created the actual regulation itself. It’s getting ready to be printed.
[00:01:44] Now, a couple of different items have hit the final rule stage. The first one is about injury illness record keeping, so our OSHA 300 form. So OSHA 300 is every year a business has to take account of all the injuries and illnesses that have occurred in the past calendar year, and then take that data and enter them into a specific log, the OSHA 300 form.
That data goes into an OSHA 300, a summary as well too. And there were certain industries that had to report their findings electronically to the government’s web portal for tracking this data. And so that included industries in highly hazardous categories. If you were over a hundred employees, that came with the stipulation as well too. So any industry where you had a hundred or more employees in a high-hazard industry, you had to submit your data electronically. If you had more than 250 employees, it didn’t matter what type of industry you were in, you had to submit your information electronically.
The new final rule to update is that they took away the 250-plus employee stipulation. So now if you’re in an industry where you have more than 250 employees, you are no longer required to submit your information electronically unless you are in one of those high-hazard categories and have over 100 employees.
And so those industries have to report the data from the 300A, the 300, and the 301. And we need to make sure that no matter what industry you’re in if you have 10 or more employees, you still have to track this data unless you’re on an exemption list. And they do have a printed exemption list out there for industries, but you need to maintain that information for five years. So that’s one of the current updates.
[00:03:32] Another final rule, as you alluded to, was the HazCom Standard. So hazard communication. We’re talking about chemicals and safety in the workplace with chemicals. When it comes to the hazard communication standard, we’re talking about Safety Data Sheets. We’re talking chemical labeling pictograms, where we have to label our chemicals with symbols so that all employees can understand what the hazards are of those chemicals.
Back in 2011, The United States adopted a new stipulation into HazCom Standard called the Global Harmonization System (GHS), and that’s where we got on board with the rest of the world with what type of symbols are being used to identify chemicals. And then with Safety Data Sheets, they all needed to look uniform for international shipping purposes.
The United States adopted that version, which I believe was version 7 of the Hazard Communication, standard GHS rules. Since then, the rest of the world has been continually updating those GHS rules, and I think we’re on version 17 now. And so, the United States is trying to catch up by amending the HazCom Standard to adopt the new version of those rules.
So what does that mean? What really has changed? They’ve added a couple of new classes of combustible liquids. Also, when it comes to labeling for really small containers under the previous HazCom Standard you had to put on there the pictogram warnings about the chemical ingredients and manufacturers’ information.
If you have a little vial that’s only about five milliliters container, how can you fit all that onto the container? So the new update specifies that you don’t have to put all that on those individual containers. It would just go on the bulk packaging on the outside and then reference points on the inside as well too.
[00:05:24] Another final rule is the COVID-19 exposure and healthcare. So it is in the final rule stage at this point. So COVID-19, whatever your opinions are about Covid at this point, it was a pandemic. We all had to react to it. It was a dangerous situation for a time. I feel like the world has gotten a little bit out ahead of it, but we are still dealing with several cases of that on a day-to-day basis, especially in the healthcare industry.
Now the federal government tried to put in place a COVID-19 exposure for all industries in the United States. That did not pass. The Supreme Court did find that to be unconstitutional. However, with COVID-19 exposure in the healthcare industry, obviously the exposure there is going to be a little bit more elevated. Therefore they did make that final rule go through. So if you are in the healthcare industry, I’m sure it’s probably already been addressed, but you need to have exposure plans. We’re talking about still providing face masks to employees, and who must be trained on all personal protective equipment (PPE).
And then also when it comes to respiratory protection, we’re going with N-95 respirators, which are kinda like those surgical types of masks. Then they still need to be fit-tested for those. So we’re not completely out of the clear of COVID-19 yet.
There is also still a National Emphasis Program that is still in effect with the Occupational Safety and Health Administration. That was set to expire in July of last year, I believe. However, they extended it, and they never put an expiration date on that. They said that this National Emphasis Program will continue until determined to be otherwise expired. So they never put an actual official date on that. So the National Emphasis Program is still going on.
So if there are exposures going on in the workplace, those still need to be addressed from a safety standpoint or else it could bring out an OSHA type of investigation to ensure that employees are being protected in case there is a hazard identified.
There are states that are still dealing with that. California, in fact, passed a COVID-19 exposure law last year, and then they made some updates to that this year. It’s no longer an emergency standard. Now it’s an official standard. Therefore, if you have outbreaks, you have to make sure that you’re responding to those in a timely manner, possibly reporting those depending on how large the outbreak is to the state government as well.
[00:07:45]
Wow, that’s a lot going on for the first half of the year.
Yeah, and those are just the final rules. We have yet to even get to the proposed or pre-rules. So the thing about the federal government is they do move with slow on some of these items. However, once they do take effect, there is a lot that industries need to pay attention to, to ensure that they’re complying with everything in place and have a plan for all those different types of burdens.
[00:08:11]
So quick question on that. You had mentioned that these are the final rules, so that means that these things really shouldn’t be a surprise because they’ve been in the works for a while. Meaning industries, companies have had a chance to prepare for the rollout of these, is that right?
Correct. Yes. So the federal government puts out its regulatory agenda in the fall and the spring of every year. And the spring one just was released maybe about a month ago. And so that’s where you can follow along with regulations. Also, at regulations.gov. And then, of course, keeping up with KPA newsletters and content as well too.
But as these rules go down the pipeline, the one that moved the fastest was anything to do with COVID-19 because it was an emergency phase, like the HazCom Standard, the injury and illness recordkeeping final rules, those have taken years to get into place and there are some that are still on that list, that have been on the list in the pre-roll phase, and that are maybe another five to 10 years before they actually become final rules.
[00:09:18]
Wow. With that kind of timeline and that many things going on, I imagine that’s why it’s helpful to have a partner like KPA to stay on top of all of it.
Exactly. Yeah. So newsletter information, we send out client alerts. If we see a regulatory change that does come about where it lists out what the regulation is, what you need to do as a client, and what resources are available to you that KPA has provided to make sure that you’re complying with any type of rule change.
[00:09:51]
That’s awesome. I know that there were still a lot more updates to cover. Where should we pick up from here?
There is a procedural change that I believe we need to talk about, and that’s not really a new regulation, it’s just how OSHA officers can go about enforcing items out there. It’s called the instance-by-instance procedural change. And so in the past, typically, a compliance officer, if they’re on-site doing an investigation at a facility, and I’ll use an example here.
Let’s say that they walk by and they see a spray bottle that’s unlabeled, that’s a violation of the Hazard Communication Standard. So they’re probably gonna issue a citation for that. Let’s say they see another bottle, and another bottle, and another bottle. We’ve got five bottles that are unlabeled, all right in a row.
Normally they’re gonna group all five of those bottles together, and they’re gonna issue one citation for the facility not doing labeling as they should be on those containers. In the instance-by-instance rule change, now the area director has the authority to now make those individual citations for every single bottle that was found to be unlabeled out there.
Now, typically, they’re only gonna do this if you are a habitual offender of violating OSHA regulations. There are a couple of industries I’ve known in the past that have several issues with their stock blocking exit doors. That’s been in public information out there. I’m sure you could probably figure it out through Google searches.
And they’ve been hit several times with large penalties. We’re talking seven-figure penalties at this point, and they’re still not getting it. And therefore, now, with this instance-by-instance rule change for every location that they go into, it could be a repeat violation. And then we’re gonna hit you for every exit door that you blocked in every one of your stores.
And so that cost could get really elevated and be very expensive for somebody to try to mitigate. So mainly, it was created for the people that, hey, you’re not getting it. Therefore we’re gonna fine you till you’re outta business. Or you do get it. One of the two.
[00:12:04]
A little more teeth in the enforcement, then.
Exactly. A couple of other proposed rulemakings. I thought this one was a little bit interesting. It’s on the docket, but there’s not an official rule for what this is gonna be called, but it’s requiring additional personal protective equipment (PPE) in the construction industry. And it means providing PPE which fits all employees.
And when I read into that, what we’re talking about is women, so PPE that will fit women in the construction industry. A lot of times, employers will buy maybe gloves in a size medium or large because that’s the typical size for men, and they avoid the smalls or the extra smalls on the hand size or something like that.
And so, being unable to provide PPE that fits any type of body type that’s out there could be a violation in the future. So making sure that personal protective equipment fits all employees, especially in the construction industry, is now on the proposed rule of making as well.
Another one that’s probably going to take years to actually get into a final rule stage is updating the emergency response standard, and this one’s gonna sweep across all industries. I’m not really going into this one too much because I think it’s, as I said, it’s gonna be years, but really it’s talking about responders in a company and what type of regulations they should put around protecting those responders that have to, let’s say in a manufacturing factory, if you have somebody that has to go and respond to a fire, there might be some additional required PPE that they would need to wear that wasn’t necessarily put into the emergency response regulations years ago when they were actually created. Where now, OSHA wants to be a little bit more specific.
[00:13:55]
Is there a particular reason that you think this one has a few more years in the process?
Because everybody’s going to put their input on it, and it’s going to require lots of different comment reviews where the public can put in their comments, and it’s gonna meet a lot of different, probably legal, pushback because each industry is different, but a lot of them don’t want additional regulatory burden that they have to go out and purchase additional equipment.
They feel that they’re fine on their own. But one place that OSHA doesn’t really talk about emergency action plans like they don’t do anything specific when it talks about responding to a natural disaster. It doesn’t really have specifics, and therefore responding to inclement weather, a tornado versus an earthquake, it’s just basically general terms. And I think we need to update that to have a bit more specifics on what we do in those situations.
And the same thing with workplace violence. We’re seeing more and more different active shooter situations and it does address some workplace violence in the regulations, but not specific when it’s just somebody’s coming in with a gun.
It’s an emergency. How are you supposed to respond to that? We have emergency action plans that say to evacuate in most cases. Should we evacuate in a situation like that? And the regulations don’t really dictate what should be done there.
[00:15:16]
Gotcha. So a lot of scenarios to cover, and because it’s cutting across all industries, like you said, I imagine, just a lot more voices in the mix.
Exactly. Yeah. A lot more voices, a lot more probably attorneys representing those companies challenging different things as well too.
All of which extends the timeline, I’m sure.
Yeah. Yeah. And one more thing on the OSHA side. They are seeking out additional input from industries on leading indicators and how businesses have successfully implemented them. So leading indicators are when you are taking. preventative strategies to ensure incidents aren’t happening at your facility.
So there are leading indicators and there are lagging indicators, and what’s in the middle is an employee injury. So if you’re doing your investigation after the employee injury, what caused it? How are we gonna train? How are we gonna react to that? That’s a lagging indicator, meaning the injuries already happened.
Leading indicators mean that, okay, let’s do hazard identification walkthroughs. Let’s take a look at everything. Let’s do employee training in all of these areas. Let’s make sure our audits or checklists are taking a look at all of this information. And so leading indicators, OSHA has put out a guidebook on that in the past, and now they’re looking, I believe, to update that guidance book on additional leading indicators. They’ll have actual case studies from different companies on what’s been successful for them. That way, other industries can take a look at that and maybe use some of those ideas to influence their own safety programs.
[00:16:54] But this kind of flows right into ESG. And so ESG, we’re talking environmental social governance, and it’s a popular buzz term that’s out there. A lot of companies are getting into their ESG philosophies and ensuring that they are trying to take their safety programs beyond compliance. Beyond just the regulations. And so, how can they do that? Looking at leading indicators is a big part of that, establishing preventative hazard identification systems through audits and third-party audits.
Using resources of a company like KPA to come in and help identify hazards using technology through mobile applications to make that data more efficient. And right there in the palm of your hand. So we can take a look at that data and see, okay, we can set a leading indicator goal to get, our training numbers up in two categories, let’s say could be fire prevention and hazard communication.
We’re gonna get our training numbers up on that in the next three months, and here’s how we’re gonna do that. KPA can work with companies on that. We have the data and the tools to actually track some of those goals to make sure that you’re actually reaching the goals, and then you can tout that on your public-facing websites for your ESG benefits.
[00:18:11]
Nice. So really being more proactive than reactive.
Of course. Yes.
[00:18:16]
And you had said OSHA is soliciting input at this point.
Yeah. Yeah, they are right now. They have advisory panels that are out there. If you go to osha.gov and go into the newsroom, you’ll be able to see some of the news items out there where they have requested some of that information.
[00:18:34]
Awesome. All right, so we’ve covered quite a bit, but we still need to talk about OSHA’s heat illness rule and how that’s developing.
Yeah, so it’s still in the pre-rule phase and they are still trying to get more information about how to actually write the standard. I had thought that maybe they might push this regulation along a little bit sooner to try to get ahead of it, especially this summer, but it seems like it’s one’s gonna be dragged out for quite a while.
So like I said, it’s in the pre-rule phase. This is where they go on and they accept public comments. Then they have to talk about small businesses and how they can adopt these regulations. Or if anything should be different for them, then they have to create resources to try to make sure that people understand how to comply with this as well too.
For example, OSHA measures heat illness based on an instrument called the wet global thermometer. I don’t know of any industry except for a few that have access to that. You know, trying to make sure resources are available as far as how to comply with any of the standards they put forth must go into those proposed rules, then that gets looked at by several different judicial views and then it finally goes into a final rule.
But the heat is here every summer, and I feel like it’s here to stay. In fact, as of this recording, a few days ago, the World Health Organization released information that it was the hottest day ever recorded. July 3rd, 2023. We had temperatures in China that were above 95 degrees. In North Africa, I think they set a record at 122 degrees Fahrenheit, which I’ve never experienced anything like that myself. But this is all due to climate change, carbon dioxide, and greenhouse gas emissions going into the environment and, unfortunately, harming some of our ozone layer. And so now we’re experiencing a lot of that warming going on.
Now, some states have adopted some new heat illness prevention standards. California was the first. They have an outdoor heat illness prevention plan. The state of Washington they’re looking to have one going to affect July 17th, 2023. And so a lot of times, the federal government will take a look at some of those plans and think, what should we take from these plans? What’s working for them to make it into our federal program? So, for instance, California they are also on the verge of adopting an indoor heat illness prevention standard. And so now I saw that the federal government has not just labeled this as heat illness prevention.
Now it’s outdoor and indoor heat illness prevention. So, for instance, in California, if you are working indoors and the temps in that particular area are going to be above 87 degrees, you have to enact your heat illness prevention policies. Or if you are in that area and it’s above 82 degrees and your job requires you to wear restricting personal protective equipment, then heat illness prevention policies will have to be enacted on those days as well too.
So constant monitoring of areas. We’re also seeing some states that are opposing regulatory burden, which I think is going to really stall this out. For instance, in Texas, the state government wants to eliminate the regulatory burden on businesses, and so they just introduced a new act where they can repeal safety regulations that have been put in place by different towns, cities, and ordinances.
It’s called the Texas Regulatory Consistency Act. And for instance, Dallas and Houston had ordinances that would require water and shade breaks for local workers. The Texas State Government, according to this act, repealed those ordinances because they feel like it was a regulatory burden. Now, that has yet to really go into effect.
The act has passed, but they haven’t really repealed anything just yet. But on June 16th, there was a news article where heat stroke was diagnosed as the cause of death for a construction worker in Texas in Houston. And the state government is trying to repeal some of these ordinances that are out there and protecting people, I think we’re moving in the wrong direction with that.
I understand their thoughts on the regulatory burden, but at the same point, there are some regulations out there that are protecting workers from these hazards out there that are gonna get their employees killed.
[00:23:06]
And during one of the hottest summers on record in Texas too.
Yeah. Yeah. So unfortunately, I think this one, the heat illness prevention standard, I think it’s gonna be delayed a few years. I could be wrong, they could get moving on it, but I just think it’s a large sweeping regulation. It affects all industries, and like we said, it’s gonna meet bureaucratic opposition, there’s gonna be lengthy judicial reviews. And they don’t have the funding, unfortunately, and the resources to really fight back on a lot of that.
[00:23:38]
And if this were to go through, it would supersede things like individual states rolling back protections because it would be mandated at the federal level. Is that correct?
That would be correct. Yes. So if it becomes a federal regulation, all states are required to adopt that into their Department of Labor plans if they have one. Not all states have a Department of Labor plan. They can adopt a safety plan. Some states have not chosen to do that, but then they’re subject to federal enforcement and regulations. So whatever OSHA adopts, all states must adopt it. And if they don’t have a state safety plan, then the federal regulations is what they have adopted at that point.
Another thing is the temperature is probably gonna be another item that really pushes back when it comes to legal challenges. OSHA is probably gonna put a temperature out there such as 87 degrees Fahrenheit, on those days, you must enact your heat policies. I could see attorneys being like okay, what does a shade break mean? If you say we have to take shade breaks on 87-degree days, does that mean that we have to be completely covered in an area with mechanical fans, or does standing under an umbrella count as a shade break for 15 minutes?
[00:24:54]
Gotcha. So definitely a lot with this heat illness rule to keep an eye on.
Correct.
This has been the first of a two-part episode with KPA’s EHS Regulatory Compliance Manager, Zach Pacillo. Be sure to check out part two, where Zach shares recent updates from the EPA.