Think your digital safety program’s a drain on productivity? Think again!
Health and safety programs are often perceived as slowing down processes or disrupting production. How can we flip that perception and demonstrate that safety can actually speed things up?
We all know that time is money. That’s why digitizing safety processes can have a huge impact on productivity. And there are a lot of individual ways that we can measure that:
- Reducing paperwork
- Providing real-time data and reporting
- Supporting a distributed workforce
An EHS software system automates your compliance tracking and reporting, ensuring organizations can adhere to local, state, and federal regulations. And, it reduces the time and effort spent on manual compliance tasks.
Reducing Paperwork
For EHS professionals who have introduced a digitized process, the first ROI they recognize is eliminating manual processes and paper-based recordkeeping with digital solutions.
Think about audits and inspections.
Rather than trying to find a clipboard and the right documents to fill out, writing things down by hand, or entering the data into a spreadsheet, we now have a systemized process and standardized reporting across the workforce.
Not only are we not tracking down paper files, but we also have a digitized review of the collection effort and then summarize standardized information at a higher level within the business. We are just reducing that paper pushing.
Those hard-copy documents often don’t make it to the right hands, and then we can’t identify what data we’re missing or standardize the process. Reducing paperwork and manual processes is one of the biggest impacts of introducing a digitized process.
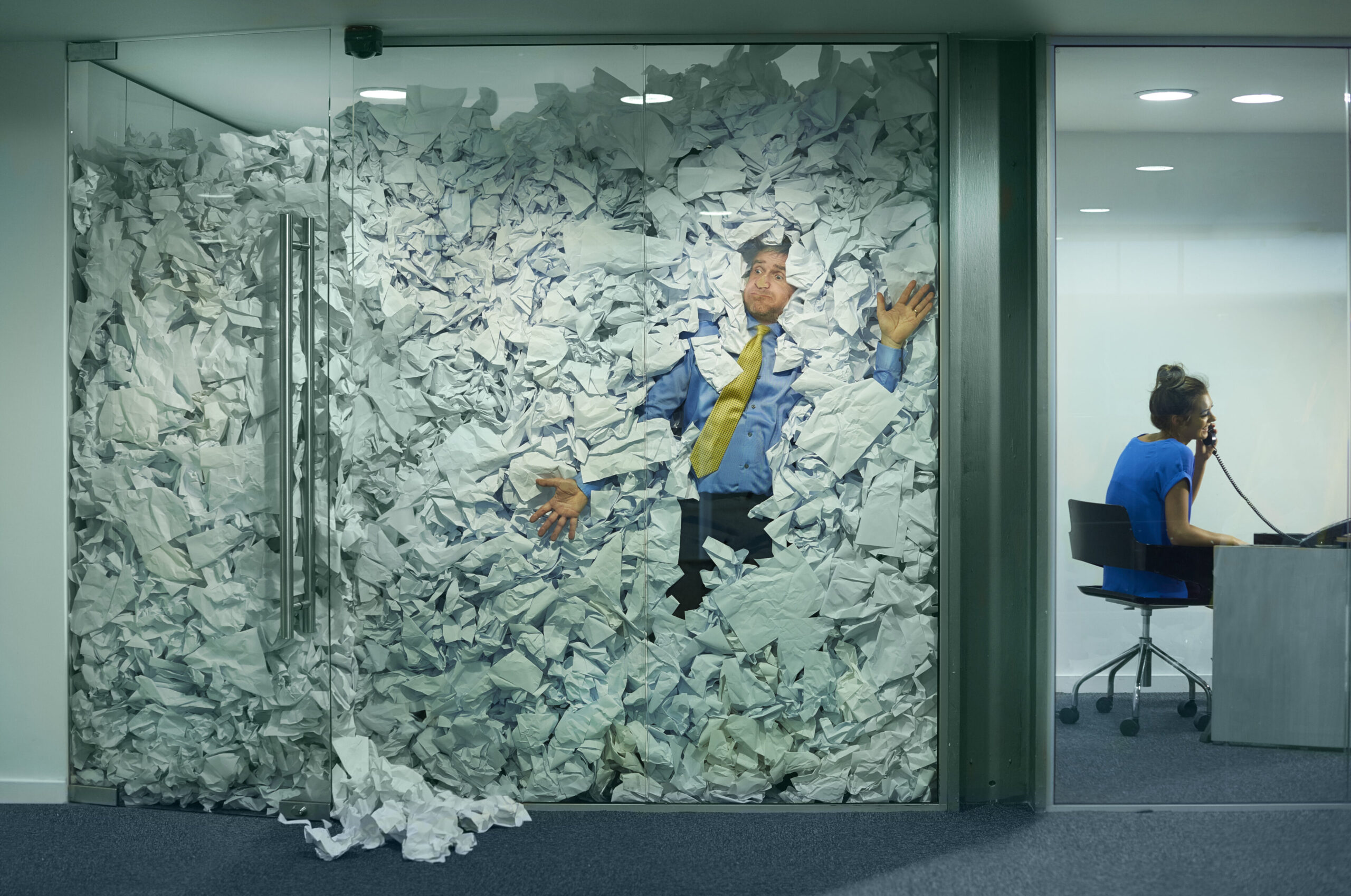
Real-time Data and Reporting
This is where the magic happens. Real-time access to data allows organizations to not spend weeks trying to summarize manual reports but immediately get access and insights into what’s going on in the business. This allows them to make data-driven decisions quickly, identify trends, and take corrective actions.
Supporting a Distributed Workforce
We have a saying we’ve used at KPA for quite some time: Safety doesn’t happen at your desk.
Having a digitized process or an EHS software solution allows employees and teams working in remote areas or at different locations to quickly and easily access any safety data they need and perform necessary tasks.
That might involve looking up a safety data sheet or reporting a workplace incident. I may also need to find a standard policy, program, or job hazard analysis. I have all of that information at my fingertips rather than in dispersed areas within the workplace, trying to track down certain binders or documents or access a corporate SharePoint.
Now, everything is in one place, not to mention training. Online training allows us to educate and ensure that we’re meeting those training compliance requirements and ensuring our workforce is always properly trained. Rather than stopping production, we can do in-person training. We can deliver training quickly, effectively, and more often.
There are many different ways to measure productivity improvement. It comes down to having the right information available to our workforce at the right times. Having a software tool and everything in one place allows for that to happen.
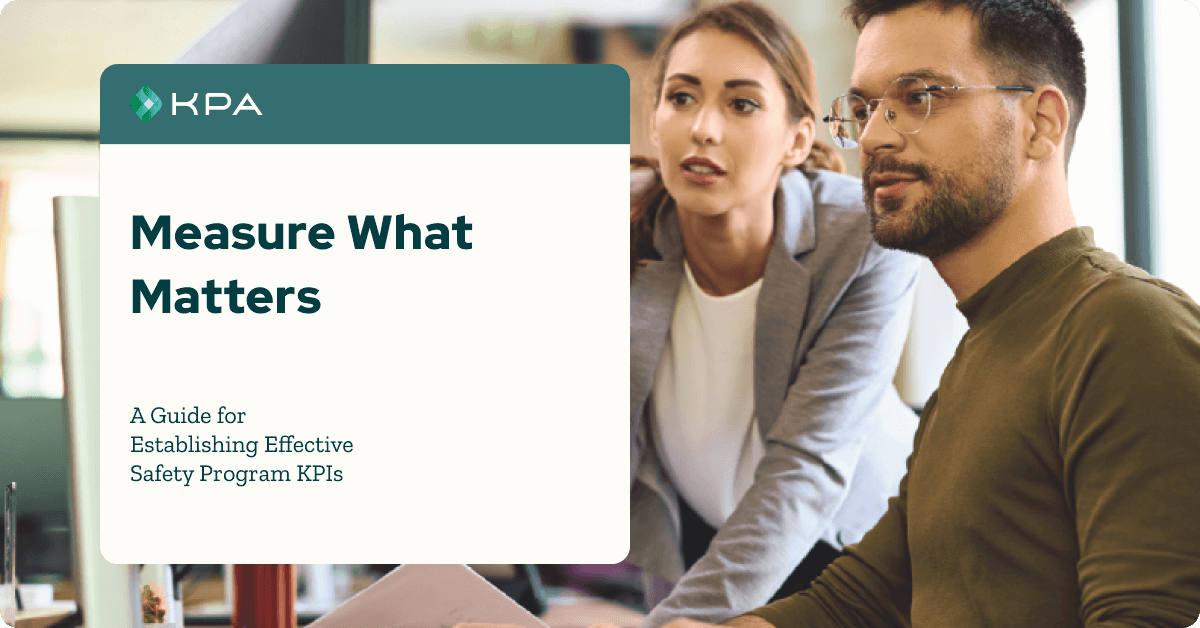
Your guide for establishing effective safety program KPIs. As organizations continually strive to improve their safety standards, the role of Key Performance Indicators (KPIs) in shaping an effective safety program is more crucial than ever.
EHS Software as a Resource Multiplier
If you don’t have a system in place, you’re relying on individual employees, and those individuals need to be in person. Often, an organization might have one safety professional who manages multiple job sites or multiple locations, and they just can’t be everywhere at all times.
Having a technology tool allows them to duplicate their efforts and reach those workforces simultaneously. Thinking again about safety training…if you don’t have a system in place, then it’s your safety officer’s role to be on-site to offer that training, and if they’re doing that in person, they’re stopping production.
They may have missed employees who weren’t there that day, and then the safety person will have to come back. But if we had a tool in place that allows that safety person to customize training and deliver it to the workforce remotely, maybe not stop production, maybe have individuals take their safety training one at a time so work can continue and safety training is still getting done.
That’s one great example. But there are a lot of them.
From doing audits and inspections to getting more of the workforce involved in the safety program rather than making it the sole role of the safety officer. This way, they can spend more time recognizing trends, identifying issues, and taking proactive approaches to reducing workplace incidents and hazards versus paper-pushing and repetitive actions.
Looking for EHS Software that’s easy to use? You’re in the right spot.
KPA offers an EHS software platform tailored to the needs of your business. All-in-one system designed to engage your employees, instill a culture of safety, and enable regulatory compliance.
Related Content
Explore more comprehensive articles, specialized guides, and insightful interviews selected, offering fresh insights, data-driven analysis, and expert perspectives.