Is your company at risk for any of the most common OSHA construction safety violations? Find out if your safety program is doing the job.
$16,131
That’s how much a single manufacturing safety hazard can cost your business in terms of Occupational Health and Safety Administration fines. We’re talking about 5 figures for just one violation of workplace health and safety laws.
The damage to your bottom line doesn’t end there. Once OSHA has discovered a problem, they’ll give you a deadline. If you don’t fix the issue by that deadline, you could face the same penalty every day things go unaddressed, or face multiple penalties if they find the same infraction in multiple instance. Oh, and if OSHA determines that you’ve committed a willful or repeat violation, you could be on the hook for 10 times as much: $161,323.
Ouch. Clearly, OSHA is making sure that construction safety hazards hurt in more ways than one.
By the way, this is only OSHA we’re talking about. Don’t forget about other federal regulators, such as the Environmental Protection Agency, or state plans.
And then there are all the costs beyond penalties. Manufacturers that don’t adequately manage their risks can expect to pay hundreds of thousands—even millions—in indirect expenses such as the following:
- workers’ compensation claims from people who have experienced injuries and illnesses
- lost productivity during and after an incident
- lowered workforce morale due to fear and uncertainty around risk areas
- hours of labor spent identifying and fixing the issue
- expenses of cleaning and replacing equipment and machinery that’s out-of-date, damaged, or broken
- legal and compliance fees
One last, but important point. Good reputations are harder to build than bad ones. And your reputation tends to impact your ability to bring in new clients or your ability to attract and retain good employees.
Are you doing everything you can to avoid these expenses?
Is your construction safety program adequately keeping your workers safe? Don’t wait until someone else—like an OSHA inspector—finds out for you.
The fastest way to measure the strength of your manufacturing safety program is to determine whether you’re at risk for any of the most common OSHA violations.
The Top 5 OSHA Violations in Construction
In 2023, construction companies paid out more than $112 million dollars in penalties for OSHA violations. Here are the 5 most frequently violated OSHA standards in the construction industry:
Check it out:
Read up on all of the top violations in the OSHA Top 10 Resource Hub
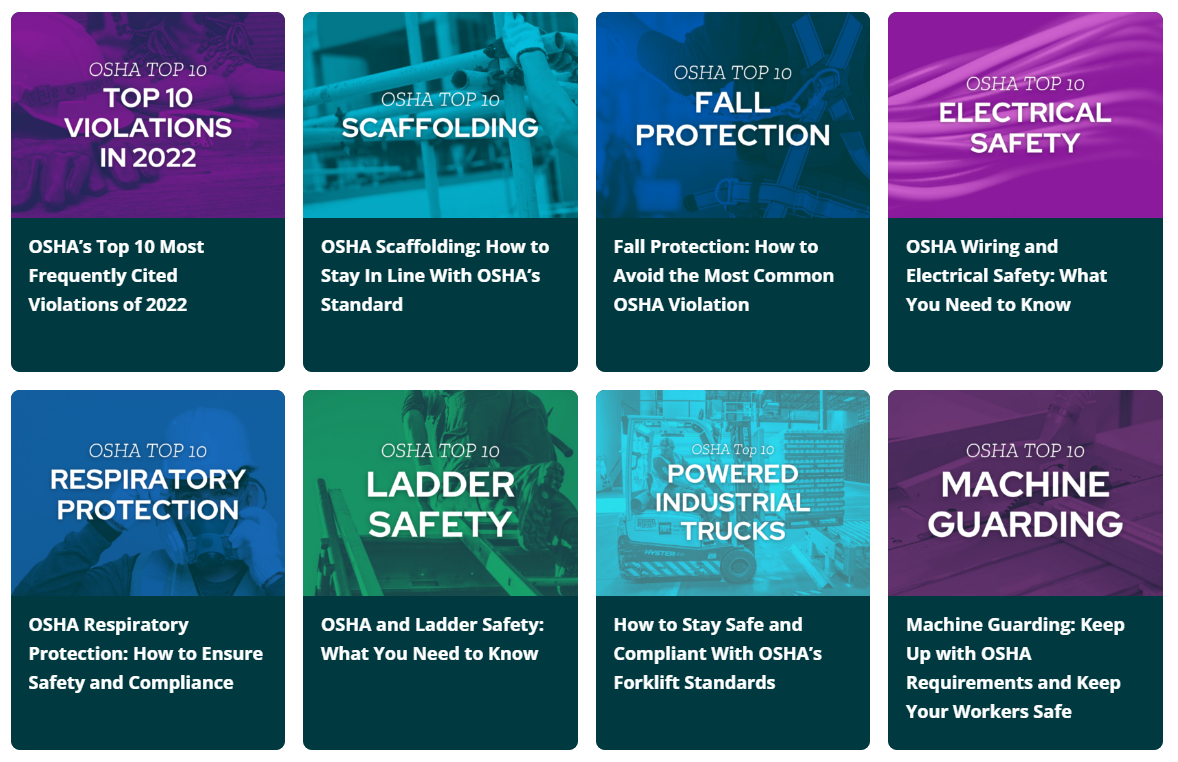
Make sure you’re buttoned up on the most commonly cited construction violations.
In 2020 OSHA issued 6,276 violations, of which 4,871 were cited as serious. The top violations were:
Let’s take a look at the top 5.
Fall Protection & Ladders
1926.501(b)(13)
1926.501(b)(1)
Holding two spots in the top 5, for the 10th year in a row fall protection was the most frequently cited OSHA violation. When workers are performing work at heights of 6 feet or more near openings or edges they must be protected from falling. Edge guarding violations are very common because construction workers are frequently exposed to fall hazards when working on rooftops, openings on sides of buildings, scaffolding, and other heights.
Scaffolding
1926.451(g)(2)
Most scaffolding violations are the result of faulty equipment, dangerous environmental conditions, improper training, or a combination thereof. OSHA specifies that a “competent person” must be on hand to a) determine whether scaffolds are safe to use, b) direct others in erecting and dismantling scaffolds, and c) conduct training and inspections. OSHA’s scaffolding standards lay out safe and proper methods for scaffolding used in construction jobs.
Dive into OSHA’s scaffolding standards.
Fall Hazard Training
1926.503(a)(1)
OSHA expects employers to protect workers from falls, but falls keep happening nonetheless. Organizations just aren’t doing enough to prevent falls, and workers aren’t taking the issue seriously enough. Training is critical to decreasing the number of falls in the construction industry, which is why OSHA leans on this violation a lot.
Learn how to protect your workers from fall hazards.
Eye and Face Protection
1926.102
Of all the body parts that PPE protects, the face and eyes are among the most vulnerable. Many safety incidents involve a workers’ face or eyes getting struck by an object, injured by flying particles, burned by acids or chemicals, or exposed to light radiation. In many of these cases, a worker suffers permanent damage to their vision or even goes blind.
Learn how to keep your employees safe from face and eye injuries.
How to Avoid the Top 5 and Other OSHA Citations
Do any of the regulations on the list apply to your workplace? If they do, make sure you thoroughly review the standards and ensure you are complying with all employer requirements.
Be prepared in case OSHA knocks on your door.
There are several steps your company can take to both avoid OSHA fines and prevent worker injuries, illnesses and deaths. Developing and enforcing a comprehensive safety program is your key to success.
Your safety program should include:
- Written Safety Programs
Develop and maintain written safety programs covering the hazards to which employees may be exposed. OSHA requires written safety programs and looks to see that they’re reviewed and updated annually. Make sure they are available to all employees. - In-depth Safety Training
Both new hire and annual safety training should cover all the risks workers are exposed to on the job site. Staff should be aware of the risks associated with their jobs, especially when working at heights, with hazardous chemicals, or with dangerous machinery. - Periodic Jobsite Inspections
Conduct inspections to identify hazardous conditions at the worksite. Most job sites require frequent monitoring and observations to stay on top of safety issues. Inspections identify hazards and provide opportunities to fix problems before injuries and accidents can occur. - Safe Tools and Equipment
Provide safe tools and equipment and ensure workers inspect them regularly. Many workers rely on their tools and equipment to get their work done safely. Unsafe tools and equipment can mean a higher risk of serious accidents, including losing an eye or a limb. They can also lead to OSHA citations. - Personal Protective Equipment
Provide appropriate personal protective equipment, or PPE, to workers. Companies must pay for and ensure that workers have the necessary PPE, such as fall arrest systems, hard hats, respirators, and hearing protection, to do their jobs safely.
You Don’t Have to Manage Your OSHA Requirements Alone.
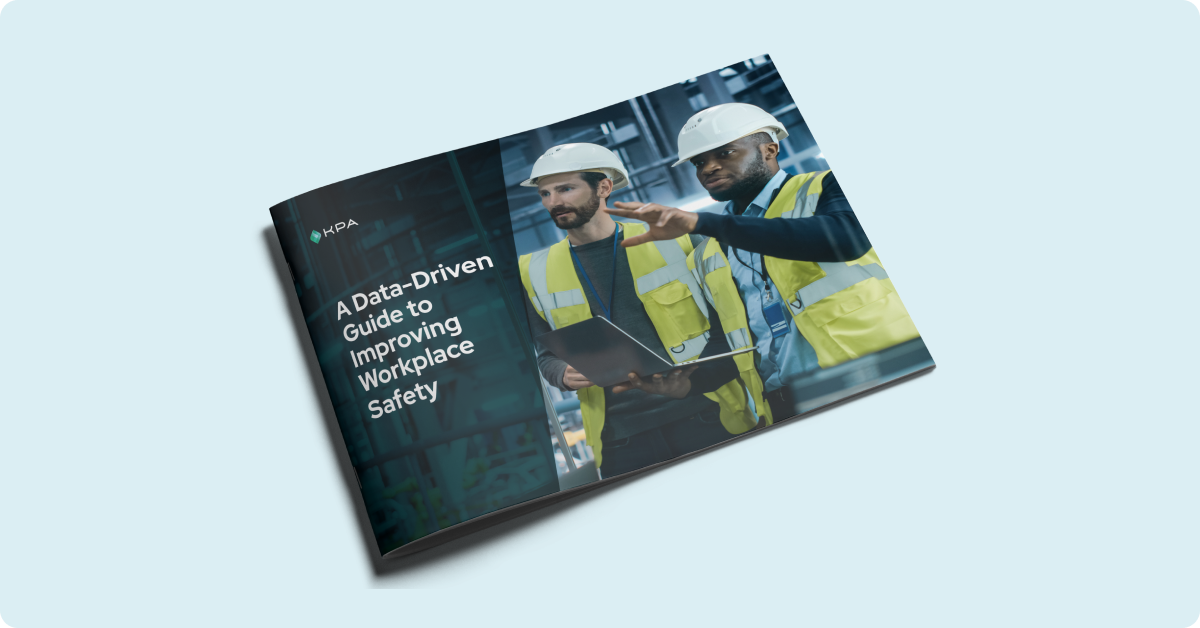
Download this eBook to learn the different types of safety data and best practices for using data and analytics to improve your safety program.
Have questions? Looking for more detailed OSHA compliance guidance? KPA is here to help.
To truly protect your workforce and bottom line, you’ll need in-depth information—and not just about OSHA’s top 5, but every potential hazard that exists in your organization. You’ll also need to conduct a thorough evaluation of your facilities to identify current gaps and risk areas.
KPA’s unique combination of software, training and consulting services can provide the coverage your people and your organization need.