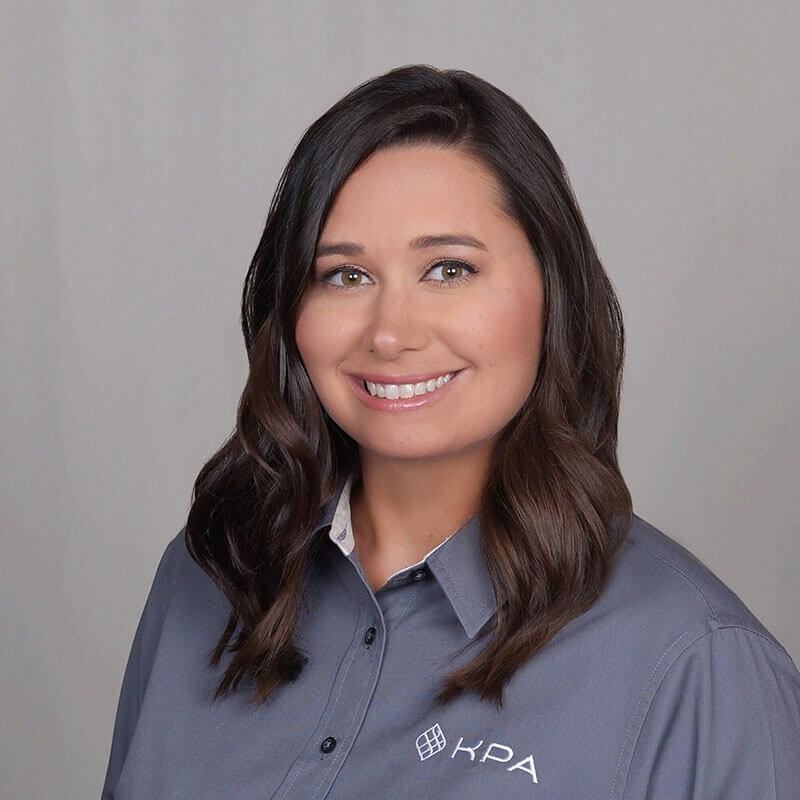
Today we’re thrilled to welcome Amanda Rawls, director of EHS Field Services at KPA. Amanda is a seasoned safety professional with over 20 years of experience in the automotive industry as an expert in general industry OSHA compliance. She’s partnered with major national automotive groups like Group One and the Hendrick Automotive Group.
Each year, Amanda oversees OSHA recordkeeping and reports for over 1200 clients, ensuring that they meet critical deadlines and stay on top of their compliance responsibilities. With her extensive knowledge and hands-on experience, Amanda joins us to share invaluable insights on OSHA reporting and how to navigate the complexities of year-end compliance.
Thanks for being with us, Amanda. Let’s jump in: Can you give us an overview of what OSHA recordkeeping reporting and year-end reporting typically entail for companies?
Sure thing. So OSHA recordkeeping reporting refers to the basic requirements for employers to report work-related injuries and illnesses to OSHA every year, which primarily involves recording injury details on the OSHA 300 log, summarizing that data on the 300E form and then posting that summary form at the workplace each year by February 1st. Everything I just said does apply to most industries, but there is an additional requirement for certain high-risk industries or just employers with a large workforce who will need to electronically submit this data to OSHA through the injury tracking application (or ITA), depending on their specific criteria.
And I should preface the rest of our conversation by saying that there is absolutely no way that we can cover every exemption and funky scenario when it comes to OSHA record-keeping. Otherwise, we’d be talking all day. How and where employees get hurt onsite can get complicated, and how those quirky scenarios apply to the OSHA paperwork is just not always easy to interpret. So I’m going to do my best to summarize in some generalities.
So I’ll start by saying this. You definitely need to know when the OSHA recordkeeping applies to your facility, and you also just need to know how to fill out those OSHA forms accurately. There is a right way to do it and a wrong way, and it’s not terribly hard, but sometimes it takes a little bit of practice and working through the paperwork to get it figured out.
The good news is that there are tons of free resources and guidance documents available to help you fill out those OSHA forms correctly. Hmm. So just don’t count on ignorance as an acceptable answer for not doing it right. There’s so much available that OSHA is expecting you to know how to do it.
Our Better Workforce Blog is your Ultimate Guide!
Stay informed with weekly industry updates, expert insights, best practices, and actionable tips to enhance workplace safety and compliance.
[00:02:53]
Fantastic. Yeah, I can see how diving into the intricacies of everything isn’t really possible because of the breadth and scope of what OSHA covers and what different businesses are doing day to day. So it makes sense that you have to speak in generalities, but I think it’s really important to touch on the fact that even though there are a lot of complicated bits and pieces, there are so many resources out there that you should know how to do it and you should have tools that help you to get these things done properly and submitted on time.
You mentioned that everyone has to do this. Can we discuss who exactly has to keep up with OSHA record-keeping and who is exempt?
Yes. So there are really two things to consider for those applications. The first one is that if your company has always had 10 or fewer employees during the last calendar year, you do not need to keep OSHA injury and illness records unless OSHA or the Bureau of Labor Statistics has informed you in writing that you do have to do that.
The second part to consider is that there is a list of partially exempt industries. There are more than 80 industry codes listed in that exemption list, so we’re not going to talk about all of them. But I’ll just give a few examples. If you’re a gas station, a florist, an office supply store, a doctor’s office, a restaurant, or even just another motor vehicle dealer (like an RV dealership), then these paperwork requirements do not apply to you.
[00:04:20]
Okay, interesting. So, there are some nuances in who’s actually doing this reporting. I know that it’s the company’s job to make sure that you know what you’re doing here, but can we talk about why year-end reporting is such a critical time for safety professionals?
Yes. This is the time of year that, as a safety professional, you actually get a chance to look back at your safety program. Most businesses are going to measure their success year-to-year. So in the safety world, that’s usually the January to December timeframe. Safety professionals use statistics like the “Total Recordable Incident Rate” or the “Dart Rate” (Days Away, Restricted, Transferred).
Both statistics are typically measured at the end of the year because they use a formula that requires you to know the total hours that were worked by employees throughout the year. Once you calculate these rates, you can compare them to previous years and see if improvements have been made. If you have had fewer injuries, then you’ve likely improved your “Experience Modification Rate,” which could also improve your workers’ compensation premium the next year.
You can also compare that rate against the industry standard based on all the statistics that I just mentioned. So again, just with those comparisons, you get a chance to reflect: Are you doing better or worse than your peers? If you’re going to go against that industry standard or just against yourselves, and you know how you did the previous year, it definitely gives you something to think about.
Safety professionals should start analyzing these rates right now and just at the beginning of next year because it’s important to know if your safety program needs to pivot.
Was your program more successful this year than last year? If so, what works? And if not, what failed?
Injury rates are a lagging indicator because the bad thing has already happened. So, the very important part about any of this analysis is trying to do our best to change that going forward, especially if you were on a downtrend. All of these statistics just give you some cold, non-biased insight into the trends that occurred at your workplace.
It just gives you time to think, how serious were the injuries? Were these injuries from the same departments? Is there an age group or a time of day that has some commonality? There’s just so much to glean collectively by looking back at what happened, and just doing these forms gives you an opportunity to reflect while you are filling them out.
So yeah, this is a regulatory requirement for many of those businesses to look back and share the results of their safety programs with employees. But by requiring these businesses to do that, OSHA is also offering an opportunity to recognize what went wrong, and hopefully, it can be corrected in the future.
[00:07:03]
Yeah. Being able to look back at your year and see what went wrong or what went right in the safety program is valuable, even if it wasn’t required for OSHA. And I know that everyone who’s listening to this podcast really cares about the safety of their team and wants to make sure that everyone goes home at the end of the day.
I think it’s also important to touch on that insurance piece because if you review things, see what went wrong, and think, “Hmm, maybe there’s a way that we can improve things, ” mention that better insurance premiums could be a good way to get higher-ups on board.
So absolutely, yes. Talking dollars, talking numbers, that’s always important to the conversation, so just having those statistics to help with your feeling about how your safety program went is just incredibly important. You can’t make change without showing some of that data to the others around you. It helps get them on the same page about what you’ve been experiencing.
[00:07:59]
Yes, and from the year-end episodes we’ve had, I know that we’ve touched on that topic a lot, so it’s good to hear that reinforced for year-end reporting.
So, thinking about that, looking back at the year, and preparing for the year ahead, have there been any recent changes or updates to OSHA regulations that listeners should be aware of as they prepare these year-end reports?
There have, actually. OSHA announced a new rule in 2023, which went into effect in January of this year. So next year marks just the second time that certain employers need to submit injury and illness information to OSHA electronically.
So if your establishment has 250 or more employees, you’ve always had to report that injury data to OSHA. However, starting in 2024, employers with 100 or more employees in designated high-hazard industries also have to report injury data. So that’s the piece that changed, employers must use the OSHA’s injury tracking application. It’s just an OSHA website to submit that information. OSHA will use that data to analyze injuries, illnesses, and hazardous conditions and make that information available to the public.
If you do qualify for that, you must report that injury data by the federal deadline, which is March 2nd, 2025, next year.
[00:09:14]
Wow. Okay. So coming up really fast, right? It sounds like there’s not a ton of time to prepare if this is the first time you’re hearing about it, so definitely good to jump on that. Glad we’re getting this episode out three months in advance of that deadline.
So, based on your field experience—I know you’ve had a lot of hands-on-the-ground time with many of these companies—can you talk about some of the common challenges that companies face with OSHA reporting or year-end reporting in general?
Yeah, and it’s the one that you just mentioned, and that’s time. So people wait to do the paperwork, and if you wait and then you figure out that you don’t know how to do the paperwork, you’re going to start to hit the panic button at that point. So talking about this now and absorbing what your role is going to be, that’s important to know before we get closer to that deadline.
The other problem is that everyone’s waiting for someone else onsite to do the paperwork. OSHA paperwork isn’t included in many job descriptions, so people make assumptions that this is on someone else’s plate to take care of, even though it’s a regulatory requirement.
So just don’t make that assumption. Ask the question, who is doing it? Get the name. Once you know that it’s John, Mary, Susan, or whoever, you can actually follow up with that person to ensure that they know the expectations and that they are also aware of that federal deadline.
And just one more challenge is just knowing what kind of injury qualifies to be reported on the OSHA 300 Log. What qualifies as more than first aid? That’s the definition that is sometimes tricky to interpret. So if you haven’t been keeping up with your OSHA 300 Log throughout the year and you’re trying to look back to get it all filled out at once, again, if someone’s unfamiliar with how to do this and what qualifies that a 300 Log is the starting piece of documentation.
You really have to get that right. We want to make sure that everyone is giving themselves and the others around them enough time to ensure that we can do it correctly.
[00:11:13]
It sounds like that can be really complicated, depending on how you manage your safety program throughout the year.
Like you said, going back and trying to fill out something that happened in January and kind of remembering everything that goes into it or finding all the paperwork that was involved could be very complicated. So I think it makes sense that if you can jump on this earlier rather than later, you’ll be able to get things done in a timely manner and probably in a more organized manner.
Yes. And that’s the key. You can’t do it on your own, especially if you’re new to it. So if you need to ask for help or clarification, keep in mind not only your timeframe but also the others around you that you may need to rely on to just get this thing filled out.
[00:11:58]
Right. That makes sense. I’m sure with all the changing regulations year-to-year, sometimes it can be hard to keep it all together, but that’s why there are people like you who are helping these businesses get this stuff together and know what they’re doing.
So knowing that things can change year-to-year, are there any emerging trends or patterns that you’ve noticed this year that stand out compared to previous years in terms of what OSHA or other regulatory bodies are cracking down on?
Yeah, I’d say that one is maybe a little bit more prevalent this year and that’s heat illness. It’s getting hotter every year, so more employees are experiencing the symptoms of heat illness more often. There’s also a national emphasis program regarding heat illness with OSHA.
So if you’ve had an employee that has been hospitalized or lost consciousness at work due to the heat, or just because of their physical activity performed in the heat, then those types of incidents do belong on that OSHA 300 Log. So I know some people just think, “Oh, it’s hot outside.” And that’s something that maybe they’ve lived with, especially just your region and the country. But just having a realization that hospitalizations, even though it’s due to heat, still count, and that it’s just newer for employees to grasp nowadays just because the heat is a bit more prevalent every year going forward than it probably has in the past.
So we’ve just seen that type of injury logged more frequently on the 300 Log, and sometimes people forget to log those types of injuries.
[00:13:29]
I see how that could be overlooked. As you said, with living in a certain area like the south or other places that get really hot during the summer, you’re like, “Ah, this is just what it is.” So it’s good to remember that that is something that does need to be tracked and is an important factor. Have you seen companies that are successfully using that reporting data? Maybe, you know, taking that information, like, “Oh look, heat illness is spiking,” to improve their workforce safety practices?
Yeah, the good news is basically everyone is.
If you could track it, you could measure it. All these data points that I’ve mentioned are going to show a trend. Injuries cost companies a lot of money, so an easy way to save money is to have fewer accidents.
The only way to stop a problem is to first identify it so that you can think about the solution more thoughtfully. Again, just having the excuse of meeting this requirement to fill out the forms does give yourself and those people in those departments an opportunity to look back and see if we can make changes.
[00:14:32]
Absolutely. Thinking about that and thinking about making changes, I think it’d also be interesting to look at the other side of this. So conversely, have you encountered cases where poor reporting has led to issues? And if there’s ever an opportunity where you can learn from other people’s mistakes, what lessons can our listeners take from these situations?
I have. Everyone gets so concerned with the federal deadline at the beginning of every year, right? But we don’t really think about the paperwork that lingers afterward. And I’ve done all this, but what do I do with the paperwork? That paperwork should exist for the next five years, and OSHA can ask for it at any point.
So my example is of people forgetting about this paperwork. I do have just one bad news example, and that was this year, back in the summertime, way past that federal deadline, we had a dealership replace their HR manager, as we know is sometimes going to happen. This same dealership also got an OSHA inspection because of a hospitalization, which meant that OSHA was going to investigate. The first thing that they requested was five years of OSHA logs.
That’s just a very common request from OSHA as part of an investigation. The new HR manager had no idea where the previous paper copies of those 300 Logs were kept. They didn’t have access to the previous HR manager’s digital files. So, since she didn’t even know where that was, she was unfamiliar with this process.
She also had no idea how to fill out the paperwork. Knowing that she needed to do it from scratch, she had to learn really quickly to complete not only that year’s 300 Log but also to go back and look at entry information for the previous four years. So, if you’re learning all this on the fly, that’s hard to do in a day.
It actually took a couple of days for this manager to figure out and get that paperwork sent over to OSHA, which was too long. Typically, you’ve got about four hours to respond and give them the requested paperwork. So a couple of days is too much for their threshold. So, in the end, this dealership was fined; their citation amount was $1,400 for just failing to provide those documents within the requested timeframe.
So I want people to realize that, yes, there’s a lot to glean here. We know that we’re doing this because of the regulatory requirement, but it’s not just to meet the deadline and post the information. It also needs to be available for OSHA during these tougher times when they could be doing an investigation onsite.
[00:17:00]
Yeah, that’s powerful. Thinking about bringing in a new person and not having all of that information ready for them in a way that’s easy to digest and easy to find, I just can’t even imagine what a nightmare that feels like. I know that being in the shoes of that new HR person would be like, “Oh no, we’re getting an OSHA fine because I couldn’t find the paperwork.” I mean, obviously not her fault, right?
It wasn’t her fault, not necessarily. Probably no one told her when they hired her, “Hey, you’re also in charge of the OSHA paperwork.” But yeah, in the end, she was the person identified to make that thing happen. And so you need to be ready for it.
That’s why it can’t just rest in one person’s purview. Everyone needs to be aware of where this paperwork is and what it means. That way, if this scenario ever happens in the future, we don’t have to rely on the knowledge of one person on one computer.
[00:17:51]
Yes. That’s super important to have that access everywhere, easy to find, in a way that’s easy to adjust for anyone who comes in to look at this.
I think this next question kind of really ties into that paperwork loss. So, what happens after that paperwork is filled out and posted? Managers have spent a lot of time and energy putting this paperwork together, and now we know we don’t want to forget about it. So what happens next?
Yeah, well. As we just talked about, OSHA requires keeping the 300 Log, the 300A form, and any related incident reports for the last five years. So, just don’t think that all your time was wasted after that 300A form was posted between February 1st and April 30th.
This is also available in case employees would like to review the history of injuries that have happened on site. That information is going to be available to them. And just like I mentioned, this is one of the first pieces of paperwork that OSHA’s going to request if there is an OSHA investigation. The reason is that these forms are the fastest way for OSHA to get to know your safety program at FOIAs onsite. It’s going to provide them some valuable insight into the number and the severity of injuries that have occurred in the past.
[00:19:00]
Yeah, that makes a lot of sense. I know we talked a lot about keeping that and making sure that it’s available, so I think that’s a huge piece of advice that you’ve given people: make sure that they keep this stuff in a place where they can find it.
So, as everyone wraps up the year, what’s your biggest piece of advice for safety managers who are preparing these year-end reports?
I’m going to double down on what I’ve been telling you already, and that’s just do not wait to do this, a signed 300A form is due to be posted from February 1st until April 30th. So if you wait until the last few days of January, you’re really doing yourself a disservice. If you’ve kept up with that 300 Log and you’re pretty familiar with doing this paperwork already, sure, you can probably wait until those final couple days of January to get this all together.
But if you’re new to this process or have a senior manager who’s not always around, you’ll need their signature before this can be posted. So again, being conscious of other people’s timetables is very helpful.
So do not wait. If you’re learning through the process, just know that it’s going to take some time to learn that process, and that deadline doesn’t change.
[00:20:06]
Right. And I know we’ve talked a lot today about how this can be an opportunity not just for you to get everything into OSHA and learn the process of what year-end reporting looks like but actually use it as an opportunity to learn about your safety process for the next year. Can we talk more about how companies can use this reporting process, not just for compliance but as a tool to drive meaningful safety improvements in their program in the new year?
Yeah, as I said at the beginning of our conversation, these are lagging indicators, and lagging indicators are everything. They are the evidence that you need to pivot, jumpstart, or even celebrate your safety program.
If you need a reason to ask an owner or a senior management team for an investment in your safety program, there is no better way to make that case than by displaying injury trends. So, reviewing the injuries annually can just make the best case for the return on investment when it comes to safety.
[00:21:04]
Especially if you break out those insurance numbers.
Exactly. If you can improve that, it will cost a huge amount for most locations. So, making a minute change in that Experience Modification Rate could significantly save you dollars in the upcoming year.
[00:21:18]
Absolutely. You’ve done an incredible job of summarizing the basics of year-end reporting and how people can use this information to improve their programs. Your best advice is “Don’t wait,” and people should jump on this as soon as they can.
Is there anything else you want to share with our listeners before we wrap up today?
I just want to reinforce that this can be a learning experience. Again, we’ve got the requirement to do it, but I think being a little bit more thoughtful about what the results have shown is really a jumping-off point for the rest of the year and will give you a better direction for how you’d like to take your safety program in the months coming up.
[00:21:54]
Well, thank you so much, Amanda. It has been a pleasure speaking with you today. I’m so glad we were able to get some clarity on your end reporting, and we really appreciate your insight from the ground level. So thanks again.
Absolutely. Yeah, thank you for your time as well, and to all of our listeners out there learning a little bit more, really appreciate it.
Related Content
Explore more comprehensive articles, specialized guides, and insightful interviews selected, offering fresh insights, data-driven analysis, and expert perspectives.