OSHA Eye and Face Protection/PPE: What It Is
OSHA definition:
“Thousands of people are blinded each year from work-related eye injuries that could have been prevented with the proper selection and use of eye and face protection.
OSHA requires employers to ensure the safety of all employees in the work environment. Eye and face protection must be provided whenever necessary to protect against chemical, environmental, radiological, or mechanical irritants and hazards.
Personal protective equipment, commonly referred to as ‘PPE,’ is equipment worn to minimize exposure to hazards that cause serious workplace injuries and illnesses. These injuries and illnesses may result from contact with chemical, radiological, physical, electrical, mechanical, or other workplace hazards.” (Sources: 1, 2)
Simple definition:
Personal protective equipment (“PPE” for short) is exactly what it sounds like: equipment people wear on their bodies to protect themselves. OSHA requires workers to wear PPE whenever they could become injured or sick by not wearing it.
Why OSHA Eye and Face Protection Violations and Other PPE Issues Happen
Inadequate eye and face protection is one of the most common OSHA violations. Other PPE issues are less frequent, but still happen hundreds of times every year.
Why do so many eye and face protection violations occur? The simple explanation is that the eyes and face are often under-protected and overexposed.
Workers and their employers frequently underestimate the risk of eye and face injuries. Employees may neglect to wear eye and face protection or remove their PPE before it is safe to do so. Common complaints are that the PPE doesn’t fit comfortably, is too hot, or makes the wearer look unattractive. For goggles and safety glasses in particular, a major problem is the equipment fogging up, causing the wearer to periodically remove it and clean off moisture.
One of the leading reasons for PPE violations is inaccessibility—the right equipment isn’t readily available when people need it. It may be stacked high on a shelf in a closet, buried deep in a box, or seemingly unavailable. Rather than go through the trouble of retrieving the correct equipment, workers decide to do the work unprotected.
Sometimes, violations occur because the employer has failed to provide the necessary PPE. Perhaps the employer didn’t conduct a thorough hazard assessment or consider every danger in the workplace. Maybe the PPE available isn’t designed for the job it’s being used for. Or maybe the employer mistakenly believes that workers are responsible for supplying their own PPE.
Now and then, violations occur because PPE hasn’t been stored or maintained properly. Poor storage and maintenance can cause equipment to degrade and become damaged, losing its effectiveness.
Finally, as with virtually all OSHA violations, inadequate training is a significant cause of PPE violations. Workers need to know when and how to use PPE; how to put it on, adjust it, and take it off; and how to properly test, store, maintain, and dispose of the equipment.
Check it out:
Read up on all of the top violations in the OSHA Top 10 Resource Hub
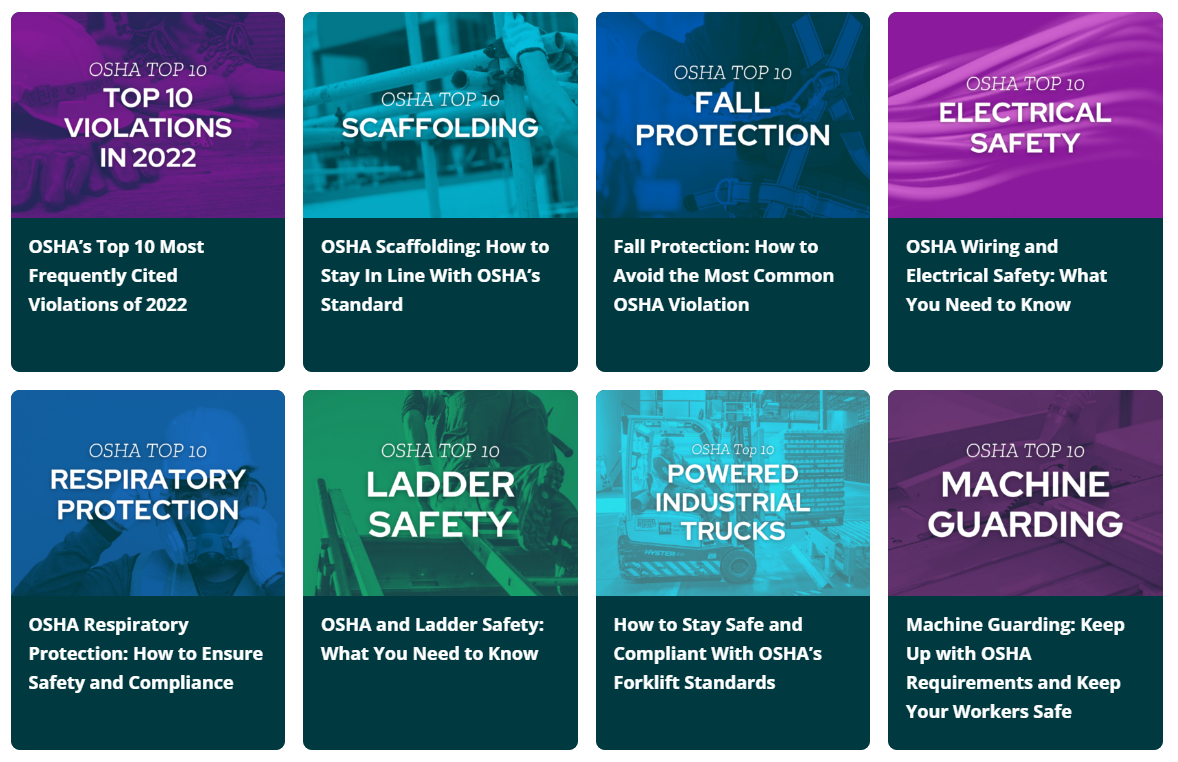
There are many different kinds of PPE, with each piece designed for a specific job or working condition. Common examples of PPE include…
- hard hats
- safety glasses
- goggles
- face shields
- gloves
- steel-toe boots
- respirators
- earplugs
- vests
- coveralls
- hazmat suits and other full body suits
PPE needs to fit comfortably and properly, or else it may not work as intended. It must be regularly inspected and maintained, and replaced when no longer functional. Employers must supply and pay for all PPE necessary to keep their employees safe.
Of all the body parts that PPE protects, the face and eyes are among the most vulnerable. Many safety incidents involve a workers’ face or eyes getting struck by an object, injured by flying particles, burned by acids or chemicals, or exposed to light radiation. In many of these cases, a worker suffers permanent damage to their vision or even goes blind.
What You Stand to Lose When PPE Violations Happen
Direct costs: OSHA penalties can exceed $15,000 per violation—and as much per day for every day the issue hasn’t been fixed by OSHA’s deadline. The fine for a willful or repeated violation can be 10 times as much.
- workers’ compensation claims from workers injured by improperly locked machinery
- lost productivity during and after an incident
- costs of replacing any equipment damaged by improper lockout/tagout procedures
- legal and compliance fees
- decreased morale
- negative publicity and reputational damage
Signs You’re at Risk of a PPE Violation
How to Avoid a PPE Violation: Your Prevention Checklist
You Don’t Have to Manage Your OSHA Requirements Alone
Have questions? Looking for more detailed OSHA compliance guidance?
KPA is here to help.
To truly protect your workforce and bottom line, you’ll need in-depth information—and not just about OSHA’s top 10, but every potential hazard that exists in your organization. You’ll also need to conduct a thorough evaluation of your facilities to identify current gaps and risk areas.
KPA’s unique combination of software, training, and consulting services can provide the coverage your people and your organization need. For more information and guidance about preventing a hazard communication violation, please contact us.