In the safety world, many organizations still rely on spreadsheets and binders full of outdated information. Here’s a practical look at what it takes to shift to a preventive EHS program using easily accessible data.
The benefits are huge: transitioning to an EHS culture focused on prevention and mitigation can keep your workers safer and save your organization money on insurance premiums, citations, and fines.
We live in an age of real-time, data-fueled dashboards that help business leaders make forward-looking decisions. And, luckily, there is software specifically designed for EHS that makes transitioning to a preventative program feasible. With all that data available to track, here are three ways to use safety data to get ahead of problems.
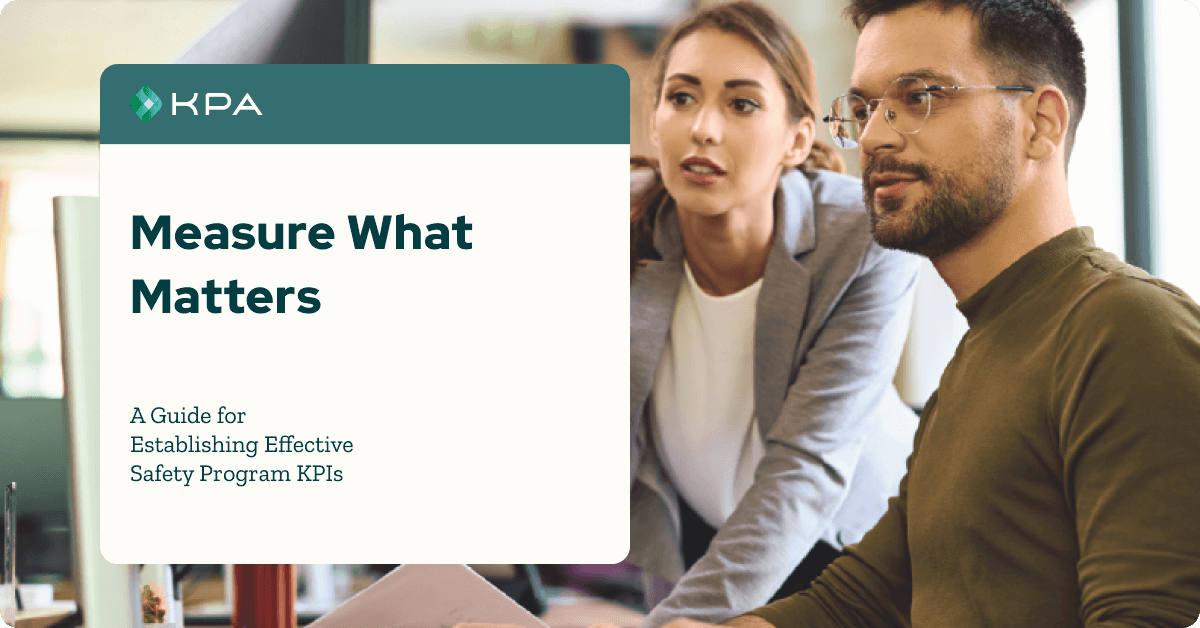
Your guide for establishing effective safety program KPIs. As organizations continually strive to improve their safety standards, the role of Key Performance Indicators (KPIs) in shaping an effective safety program is more crucial than ever.
Data + Culture = A Safer Workplace
Believe it or not, the information you already have about your workplace and employees is the information you need to mitigate future accidents.
There’s a two-pronged secret to putting this information to work:
- Find a system that translates your data into actionable insights
- Cultivate an environment where everyone actively participates in improving health and safety.
By doing those two things, you can prevent incidents and accidents that would otherwise impact employees. This, in turn, can translate to not only happier and healthier workers but also cost savings and less down time—i.e., many of the key ingredients for sustained growth.
KPA Helps Businesses Take a Data-Driven Approach to Safety
KPA simplifies data visualization and reporting, giving users easy access to actionable insights into their EHS program performance. Your data is presented in real-time, so no delay or extra steps are required to access the information. The dashboards are configured based on features tailored to your business’s unique requirements, giving you the power to make informed decisions that impact workplace safety.
Let KPA show you how to take a data-driven approach to safety.
Related Content
Explore more comprehensive articles, specialized guides, and insightful interviews selected, offering fresh insights, data-driven analysis, and expert perspectives.